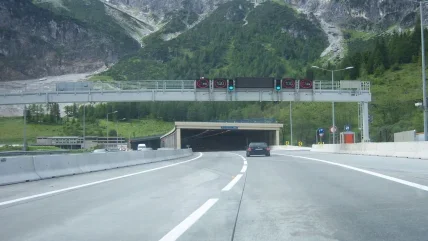
INTRODUCTION
Tunnel fires are a horror scenario, not only since the accidents in the Mont Blanc and Tauern tunnels in 1999, which claimed many lives.
When it comes to detecting and locating the source of a fire in a tunnel, every second counts. Special fibre optic cables, in combination with powerful measurement and evaluation technology, make it possible to reliably meet this requirement.
Federal Highway 49 – tunnels at Treysa/Frankenhain
After the shell of the approximately 900m-long tunnel of the federal highway 49 between Treysa and Frankenhain in northern Hesse, in central Germany, was completed in Fall 2015, the technical expansion of the two tunnel tubes began. The general contractor for the technical equipment of the tunnel was the plant engineering company SPIE OSMO GmbH, from Georgsmarienhütte. Germany. Its approximately 330 employees are active in numerous business fields, from electrical systems to control, mechanical and plant engineering to information and communications technology as well as traffic engineering. The traffic engineering unit, with its 50 or so specialists, was also responsible for the fire alarm system in the tunnel.
In over 100 projects over more than two decades, the company has been responsible for the technical equipment of numerous tunnel structures, mostly on behalf of the public sector.
“Especially in the field of fire detection equipment, we are observing a continuously increasing demand for fibre optic systems. Not least for this reason, we were looking for an additional, reliable supplier,” explains Jens Grewe, project manager for traffic technology at SPIE OSMO.
This supplier would not only provide suitable hardware for the Hessian road tunnel project, but it also had to have experience with the design and data connection to the fire alarm control panel.
The choice fell on Yokogawa Deutschland GmbH from Ratingen and its DTSX1 fibre optic temperature measurement system. The system is already being used successfully worldwide to monitor conveyor belts, pipelines, subway lines and chemical production plants. Compared with conventional temperature sensors, such systems have various advantages: they are easy to install, durable, require little maintenance and therefore offer an advantageous price/performance ratio.
Certified safety
The DTSX1 fibre optic fire and heat detector was certified in 2020 by VdS Schadenverhütung GmbH as the German approval body in accordance with European Standard EN 54-22, fire protection classes A1N, A2N, BN and CN. It applies to resettable linear heat detectors consisting of a sensor element with fibre optic cable and designed for fire detection and fire alarm systems in building construction and civil engineering.
The sensor cables comply with CPR (Construction Products Regulation) class B2ca -s1a, d0, a1 in accordance with the Construction Products Regulation or EU Regulation 305/2011. This describes the properties of the flame-retardant cable in the event of fire as lowsmoke, non-burning dripping and releasing only small amounts of acid.
In addition, the public client of the Hessian road tunnel project requires VdS certification for each hardware component as well as its complete documentation. Only then are all formal requirements for use fulfilled.
Yokogawa supplied a total of four DTSX1 signalling units, the fibre optic cables for the sensor and interconnecting lines, as well as installation components and uninterruptible power supplies for up to 72 hours.
Thus, a redundant hybrid detection system was set up for each of the two tunnel tubes, consisting of one two-channel and one single-channel measuring circuit. The dual-channel system offers the advantage of being able to continue monitoring the entire tunnel length even in the event of damage to the sensor cable in the tunnel, since the laser pulses are sent through the fibre optic cable alternately in opposite directions. However, this requires a slightly longer measuring time relative to the single-channel setup.
MOUNTING AND COMMISSIONING
The sensor cables, which are only about four millimetres in diameter, each contain two optical fibres for the two independent measuring circuits. These are surrounded by a stainless steel protective tube, a stainless steel strain relief and finally a flame-retardant, corrosion-resistant outer sheath.
The cables were installed in the federal highway 49 road tunnel in the second half of 2020. For the installation, plastic and stainless steel clamps centred a few inches below the tunnel ceiling were used. Connecting cables, back to the DTSX1 signalling units, run in empty conduits in the area of the emergency walkways.
The signalling units were to be installed in the operations building at the south portal of the tunnel. The specifications included an initially inconspicuous additional requirement: The DTSX1 signalling units were not to be mounted in a housing on a wall as supplied, but were to be housed in two 19-inch control cabinets.
What at first seems trivial has some consequences, as Carsten Schwarma, project manager at Yokogawa, explains: “The installation of the electronics in the control cabinet was in itself possible without any problems. However, we had to make sure that this would not affect the certification of the system, and we also had to clarify with our Japanese parent company that the customer’s warranty claims would remain fully intact.”
This required some teleconferencing and correspondence, but was ultimately accomplished to the satisfaction of all involved.
“In addition, Yokogawa assisted SPIE OSMO and the tunnel’s operating company with on-site installation and commissioning, and training of operating personnel,” adds Schwarma.
THE ‘ACID TEST’ – FIRE TEST IN THE TUNNEL
In order to be able to guarantee smooth functioning of the sensors and the entire detection chain in the event of an emergency, a one-day test was carried out in May 2022 under realistic conditions in the tunnel which was almost ready for operation.
Only after this fire test did the final acceptance take place.
In both tubes, experts simulated a car fire with fire and smoke in accordance with a standardised test setup. In this way, it was demonstrated that, once broken out, a fire with a 5MW fire load – corresponding to about 20l of burning gasoline on an area of four square meters – would be detected by the fire detection system and localised to within 50m within 18 pre-defined zones.
In accordance with fire protection class A1N, fire detection takes place either when a temperature threshold of 60°C is exceeded at the sensor cable – even briefly, if necessary – or when the temperature rises by more than 25K over 100s. The sensor cable is then connected to the fire alarm system.
A measuring cycle with two independent measurements takes less than ten seconds. This information must then be passed on to the fire alarm control panel via a relay circuit and processed there – within 60s, according to the safety specification. Powerful fans then start up to transport smoke and heat as efficiently as possible to the outside, depending on the location of the source of the fire.
In the event of a fire, the emergency services are notified and the entire tunnel is closed to traffic. Loudspeaker announcements in the tunnel and outside provide instructions on what to do in such a case.
A TECHNOLOGY WITH POTENTIAL
Grewe, from SPIE OSMO, summarises his experience from the project: “The detection system has fitted seamlessly into the safety infrastructure and has proven to be efficient and reliable in the fire test.
“In addition to the quality of the technical components, Yokogawa’s expertise also contributed to this – from planning to commissioning.”
Yokogawa’s Schwarma commented: “Our fibre optic temperature measurement systems are very versatile and are constantly opening up further areas of application.
“The fire alarm system in the Frankenhain tunnel was a premiere for us in this application environment and an exciting challenge for that reason alone. It became apparent that the requirements and project handling in the construction industry are in part quite different from what we are familiar with from the process industry.”
Grewe adds: “But there were no obstacles that couldn’t be cleared up quickly after a clarifying discussion.”
For future projects, which are already on the horizon, he would particularly like to see a standard 19-inch built-in version of the DTSX1.
LASER-SUPPORTED MEASUREMENT OF TEMPERATURE PROFILES
The DTSX1 signalling unit continuously generates laser pulses which are coupled into the temperature sensor as excitation signals.
The relevant measurement signal is the light backscattered from the fibre cladding, which is fed back to the signalling unit via modes of the optical fibre. The modes act as individual light paths in this process.
The detector unit analyses a part of the low-intensity scattered light, namely the frequency-shifted, longer-wavelength Stokes and shorter-wavelength anti-Stokes signals. These arise as a result of the Raman effect, i.e., the interaction of the laser light with the lattice vibrations of the glass fibre molecules.
The temperature at any given location on the optical fibre is a result of the intensity ratio of anti-Stokes and Stokes scattered light and the travel time of the light to the measurement location and back to the detector.
Up to 32,000 temperature measurement points are possible per fibre, with a fibre length that can be up to 16km for the DTSX1,” adds Ralf Cymontkowski, DTSX account manager at Yokogawa.