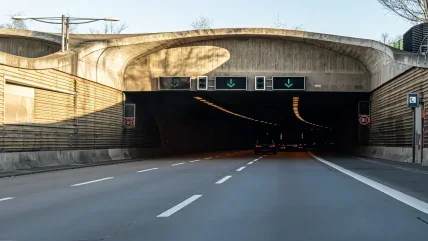
Accessing underground works, especially on urban tunnel projects, is always a challenge when seeking options to overcome the vertical distance from the surface in ways that are logistically and economically efficient but most of all reliably safe. Ladder scaffolding, crane lowered hoists, and manrider cages have been used on different projects, depending on many factors.
In 2019, on the metro tunnel works in Paris, France, XL Industries brought into service its XE5 small footprint mechanised access lift – able to be used, and extended, while shaft sinking was underway. The shafts would be excavated deeper in steps and then the suspended and wall-tied support mast for the XE5 would be extended down in 1.5m steps – each section being added from inside the cabin itself to be inserted and bolted into place without other intervention.
Mechanised access to the shaft base is therefore available from the start, and goes deeper with the same system from the start of the excavation.
Manufacturer XL Industries, based in France and with a UK operation, XL Industries UK, says its XE5 system exceeds the construction hoist standards (BS 12159), especially due to the innovative extension and landing.
While XL notes that XE5 has been seen as a niche product it says the suspended vertical access system offers a “massive health and safety” benefit by enabling continuous access to the bottom of a shaft while being attached to the top. The mechanised system also has a small footprint onsite for the cabin – a 1.5m x 1.5m cabin that can be adjusted from within, onsite, at any time out to 2.5m x 1.5m to take more load or passengers, says the company.
Once at shaft bottom, the system can be parked – it doesn’t need to return to the top over have other equipment help it do so. That helpfully influences site support needs and logistics in comparison to, say, crane-lowered hoists or cages that would need to lift up again after transport to the bottom, or at least for the crane to be freed for other work before returning.
In terms of scaffold ladders, XE5 has the advantage of being slimmer and able to be used from the outset. And, fewer return trips are needed, compared to the cranelifted systems.
And, says XL, a permanent operator is not needed for the system.
With over 150 projects completed across the world, from Europe to Australia, for many types of deep access needs including tunnels and deep basements, the XE5 is also being used in the UK on the London Power Tunnels, Phase 2 (LPT-2) project. The Hochtief Murphy Joint Venture (HMJV) has two XE5 hoists on its works.
Lee Aspden, HMJV’s TBM project/construction tunnel manager, said: “XL Industries have provided an excellent service to Kings Avenue over the past two years. When called upon, XL have quickly made themselves available to resolve any issues albeit very few issues occurred.
“Safety performance of the hoist has also been well managed with regular servicing and when required changes have been made at the request of the site team with minimal disruption to operations on site.
“The use of the hoist over traditional methods like manriders on cranes for access in and out of the shaft has also proved beneficial to the production of the operations underground, providing easy access in and out of the shaft on a regular basis.”
XL says the contractor usage of the system is showing an average of 32 round trips in a day since 2021 with the max of 92 and minimum of two (New Year holiday).
XL says the XE5 hoist comes pre-assembled and can be installed on its supporting frame and commissioned in three days. It can be cantilevered at the top of the shaft to suit the project needs and specifications, and then the extension of the support frame follows the works programme. Maintenance is planned every 26 hours of hoist running, which is 700 round trips on a 40m deep typical installation, says XL.
With the XE5 able to be raised and lowered to accommodate the build process of the shaft, and do so independent of a crane, once the shaft is complete there is no need to remove the whole hoist – it can remain for permanent access solution, says XL. Or be removed – as easily as it went in.
HMJV’s Aspden says: “The new system offered for a top down installation looks to be very valuable for future work relating to shaft construction as this would also minimise lost time with use of manriders or installation of ladder access.”