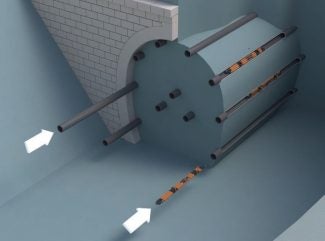
As many within the tunnelling world are now aware, with its automated underground construction concept, hyperTunnel is proposing a drastic change to the way in which the ground is entered and treated for construction, monitoring and repair. It presents a genuine alternative to well-trodden techniques such as tunnel boring or drill and blast, and is aimed to also make underground construction fundamentally more cost effective, more sustainable and safer.
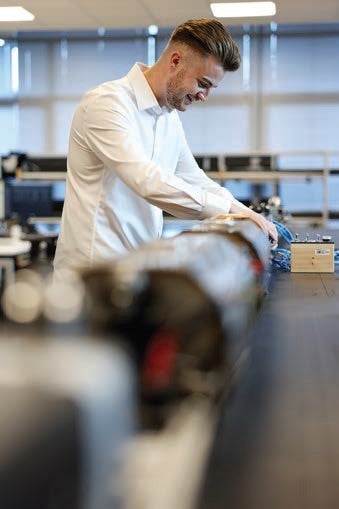
Harnessing the power of an information-rich Digital Twin, the hyperTunnel concept uses an innovative approach comprising ‘swarm robotics’, moving through multiple access adits pipes to perform additive manufacturing techniques. In addition to those cutting edge technologies, the system will also utilise Artificial Intelligence (AI) and Machine Learning (ML) with the Digital Twin.
The ‘swarm robotics’ approach allows for a ‘work everywhere at the same time’ construction philosophy – many, many multiple work faces in contrast to techniques that can see slow progress with working at one or a few small areas.
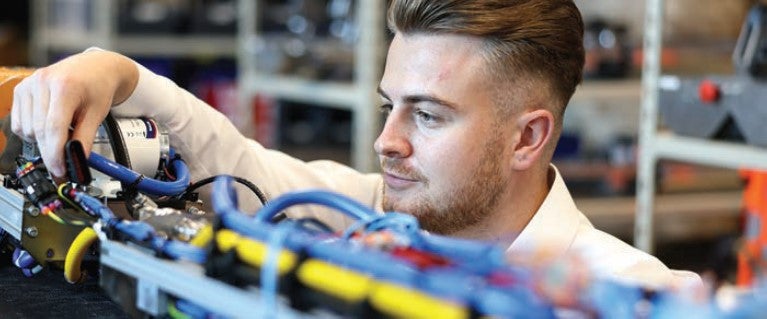
The first step of the process involves installing a simple grid of HDPE pipes in the ground. The grid provides access along the entire length of the structure for the swarm of hundreds or thousands of semiautonomous robots. The pipes forming the grid are specially, geometrically located adits, in effect.
The robots move throughout the grid and facilitate an additive manufacturing process to build the required structure within the ground – somewhat akin to 3D-printing, while using the geology as support in the additive build process. This is very much like 3D-printing an item in a tray of powdered raw material.
The first level of the technology, called hyperDeploy, is to improve upon the immediate local geology. The next level of technology is hyperCast, which is to replace the geology with new material and create precise structural lining; it is due for release in 2025.
Through the construction activities, the many processes and activities that will be underway concurrently will be managed and monitored by the AI and ML-integrated Digital Twin.
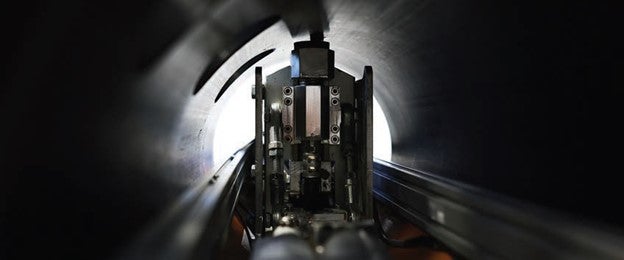
During the first half of 2024, the ‘robots in the ground’ are expected to be seen in operational environments.
ARRIVING AT PRE-PRODUCTION TESTING
With much R&D required, hyperTunnel has been putting the products through a rigorous testing programme to achieve Technical Readiness Level 8.
The work takes place at indoor and outdoor test centres, with the bulk of pre-production testing occurring in an indoor lab at its Basingstoke headquarters. There, test cycles are continuously performed, running an initial fleet of 50 robots through a 12m representative grid on a 24/7 basis.
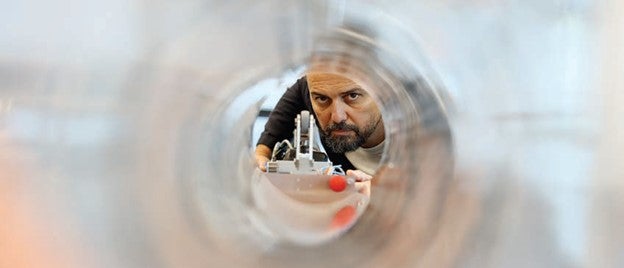
The robotic hardware is of modular design, comprising separate elements coupled together. Robots consist of an intelligent tractor that acts as the drive unit and master to other two modules: a payload, which contains the specific toolset; and, a bogey, which provides the robot with power and is easily swapped out when it needs charging.
The focus is to keep the robots – ‘bots’ – simple with very low bills in material costs. Individual members of the swarm must be expendable in the approach that is always looking to mimic nature. The economy comes from the swarm effect.
An individual robot task might be: digital surveying where the tool – for example, a ground penetrating radar (GPR) unit – moves through the grid to provide geological scan data to the Digital Twin; or the installion of special skin fittings (hyperBits) in the wall of the HDPE pipe for controlled access into the geology; or to deploy chemistry through a hyperBit. The list of tools to be utilised is growing.
hyperTunnel’s lab set up allows the engineering team to perform dress rehearsals for each real-world contract scenario. Fitted with exact payloads and according to contract parameters, the robots act as if they are on a client job. The test team can measure their positioning to fractions of a millimetre and gather data to determine whether any errors are caused by software or hardware issues.
Testing to this level of accuracy and realism is paramount. By proving delivery performance against forecast contract time, customer confidence can be gained before real construction takes place.
To get to the pre-production testing stage, it has been important to develop a deep understanding of both product and system performance and limitations. To achieve this, a blend of simulation, conventional physical testing, and accelerated lifecycle testing has been adopted.
FROM PROTOTYPE FLEET TO OPERATIONAL
An interesting feature of hyperTunnel’s testing strategy is the production of a fleet of 50 robots. This is rapid prototyping with a difference. Traditionally, prototypes are usually a one-off production at a higher cost that engineers aim to reduce later. Due to the ‘swarm’ nature of the hyperTunnel method, though, many robots must be available at an early stage to accelerate swarmbased development and testing.
Progressing to swarm behaviour testing with multiple variables as soon as possible, speeds up the process and allows for gathering more test data. The functionality of components can be tested as intended to work and also with the hardware there can be early involvement of electrical and control engineers.
Managing multiple lower cost units with off-theshelf components – able to be reused or upgraded instead of using one very costly test unit that would be eventually discarded – is more cost effective. Instead of engineering costs ‘out’ of the robots, as is commonly the development route taken, the hyperTunnel test method with swarms instead determines various paths for engineering ‘in’ product upgrades. The upgrade paths have transitioned the robots from prototype to operational products.
hyperTunnel is not only building the bots but also the operating system, the network that will allow the bots to communicate, and the distribution network all over the world.
In parallel with fleet testing, hyperTunnel has already developed a second generation of each robot.
The initial tethered system of the first generation, using cables to supply power, communications, and chemistry, is now battery-powered and wireless in the second generation.
Accelerated life testing is proving the bots’ robustness, reliability, and capabilities. For example, testing of a robot, called hyperRam, simulates the forces required for the installation of hyperBits through the HDPE pipes into the ground. The tool can push with a force of 2300 kgf (22.5kN) and in a max load test completed over 3000 cycles (equivalent to 10,000 live cycles) and displayed only minor wear. The hyperDAR surveying bot is now achieving a positioning accuracy of 0.5mm within the pipe, which is more than sufficient.
NEXT STEP: COMMERCIALISATION
There is backing for the hyperTunnel system from many big construction industry players and investors. Funding from various sources has reached £18.5 million so far.
In mid-2022, for example, the European Innovation Council (EIC), under its EIC Accelerator scheme, gave a €1.88 million grant to complete the development of the swarm robotics underground construction platform for testing to Technology Readiness Level 8. The grant enabled the company to ramp up activity and reach the pre-production testing phase, as outlined above.
The core route-to-market for the hyperTunnel system was launched in late 2022 as exclusive distributor licensing agreements (EDAs) for certain applications, sectors and territories. The EDAs would provide construction contractors with opportunity to differentiate their offerings to those licence parameters. Companies partnering with hyperTunnel during the R&D phase have early mover advantage and privileged access to technological developments.
In October 2023, the first EDA was signed with AmcoGiffen under a licence to apply the hyperTunnel technologies and systems in the UK rail sector for crucial activities, including enhancements, repair, rehabilitation and monitoring of underground spaces. The applications can also include stabilisation and water management for slopes and track bed infrastructure.
One of the next steps in the technology development toward commercialisation is taking place at the UK’s Global Centre of Rail Excellence (GCRE), located in south Wales. This year, hyperTunnel is to use its system on a demonstration project to construct a fullscale sized underpass. The UK government is funding standout railway innovations to be tested at GCRE and hyperTunnel is one of a number of technologies to be trialled this year.