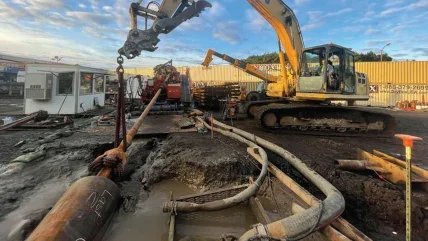
There are easier places to build than along the wild and rugged Oregon coastline. But the high wave energy of the Pacific Ocean offers an ideal testing environment for wave energy devices and explains why the region was chosen as the location for the PacWave South project.
Once completed, PacWave South will become the first pre-permitted, full-scale test facility for wave energy devices in the US.
Jacobs partnered with the HDD Company in support of Oregon State University (OSU) developing the project, which will provide a platform for up to 20 different Wave Energy Converters to be tested in real-world conditions in the open sea.
The powerful ocean off the coast of Oregon offers an ideal testing environment for these prototypes, allowing for comprehensive testing across a wide range of conditions.
This phase of the project comprised of four offshore steel conduits, each extending up to 36.5m (120ft) beneath the seafloor and reaching a mile offshore.
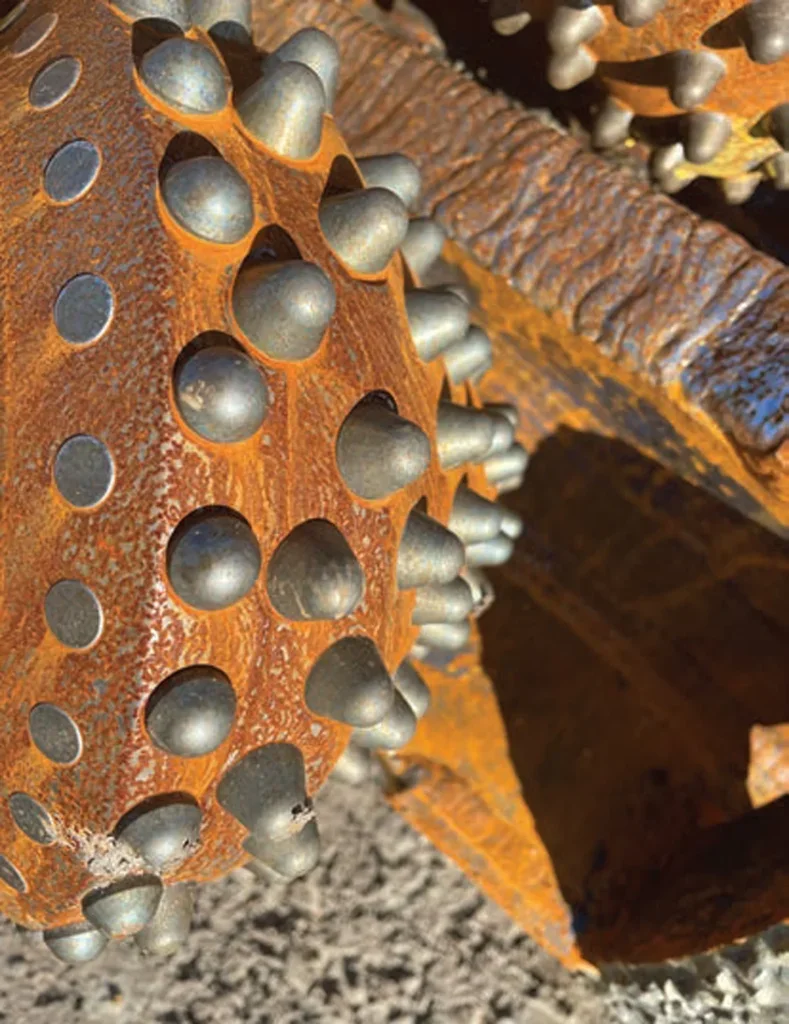
The offshore conduits run into an underground vault facilitating the transition to onshore infrastructure – bundle of five conduits made of high-density polyethylene (HDPE). From the vault, the five conduits extend half a mile to PacWave’s Utility Connection and Monitoring Facility, where the results of the offshore testing will be analysed.
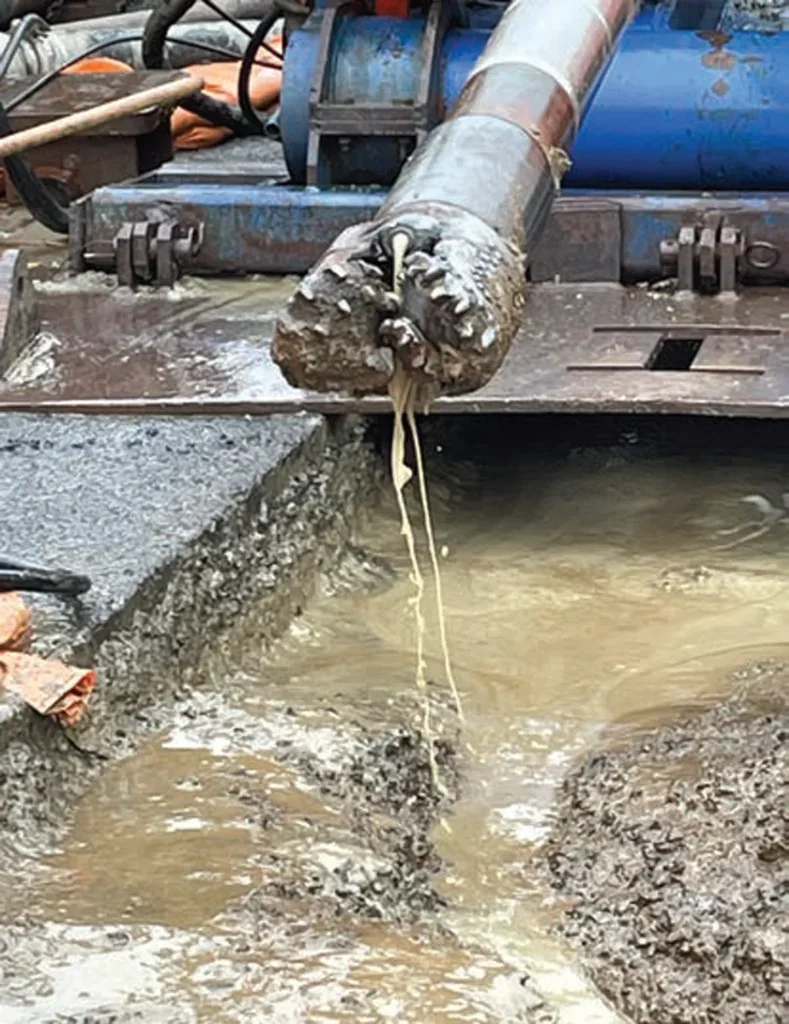
PROTECTING SENSITIVE WETLANDS
After an extensive public consultation process that spanned several years, Newport in Oregon was selected as the location of the offshore testing site, and Seal Rock selected as the landing site. One of the major factors in the offshore site selection was the need to ensure that construction would not interfere with commercial fishing activities.
For the landing site in Seal Rock, the parking lot of Driftwood Beach State Park was used to minimise additional disturbance of the environment and surrounding sensitive wetlands by providing an already developed location to stage the construction.
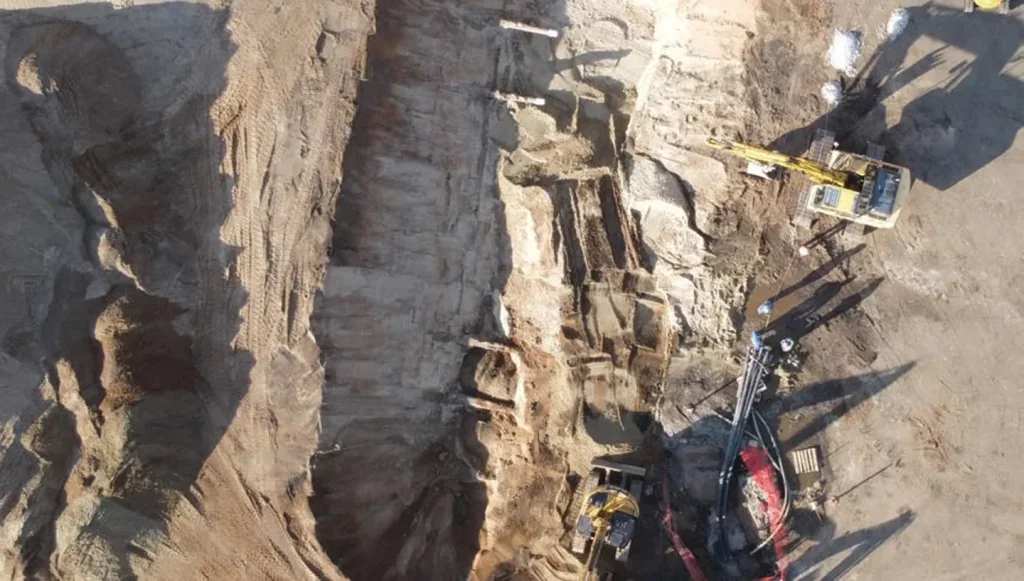
To ensure that the wetlands were preserved, the team utilised horizontal direct drilling (HDD) to bore beneath the zone. Instead of the traditional method of digging a trench and backfilling, a half-mile long HDD bores connecting the two sites were drilled up to 40ft below ground.
The method poses challenges. To drill a bore of such length, drilling fluid had to be pumped into the bore under pressure to clear the cuttings. However, if the pressure levels were too high, the fluid would be forced to the surface, potentially harming surrounding flora and fauna.
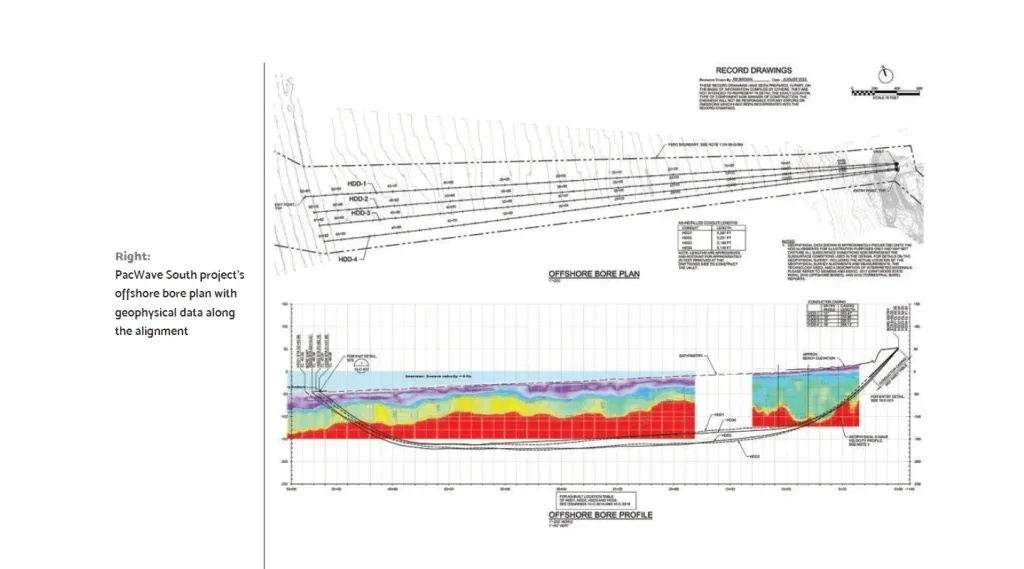
To mitigate this risk, the project team deployed an intersect bore technique, drilling from both ends and meeting in the middle. This approach reduced the amount of pressure needed to remove the cuttings and ensured that the sensitive wetland environment was protected.
By employing hydrofracture calculations provided by Jacobs, The HDD Company maintained allowable annular pressures in the bore.
This involved adjusting pump pressures and refining the drilling fluids recipe to ensure the pressures remained within a designated pressure envelope. Think of this envelope as a ‘speed limit’ for the bore, which is informed by real-time data from subsurface tooling. The HDD Company were able to adjust in real time based on the actual field conditions.
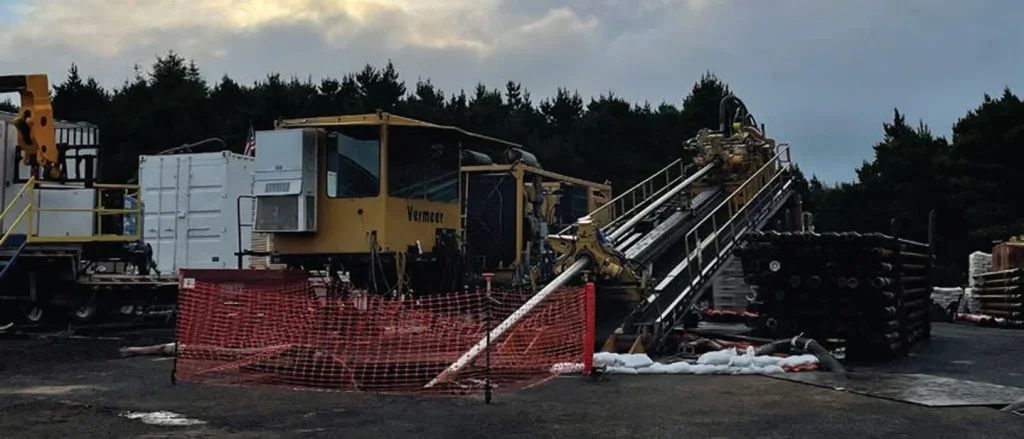
NAVIGATING THE OREGON COAST
Oregon’s coastal geology created a second major challenge. The project team was tasked with positioning the conduit exit points beyond the surf zone, where they could be used to route the cables to the offshore test site.
As noted, traditional trenching methods were ruled out due to their potentially destructive impact on the marine environment and disturbance to the beach and this led the team to consider the HDD approach.
However, Oregon’s coastal area presents notable challenges for HDD drilling, with several projects in the state being abandoned over the years due to specific geological features. These challenges include marine sedimentary rock formations, which pose difficulties due to their swelling nature, as well as characterised by reactive and bentonitic properties. Additionally, the presence of basalt formations significantly impacts the drilling rate of penetration, adding another layer of complexity to construction.
To overcome this challenge, it was crucial to understand the composition of the ocean bed and the material that the project team would drill through.
In an ideal scenario, a drill rig would be used to collect samples of the soil and rock below the seafloor during the project’s design, requiring the installation of a platform in the surf zone. This approach was not feasible due to permitting, as well as the cost and schedule delays required to mobilise the specialised equipment required, which would have taken years to plan and execute.
Instead, the team conducted a thorough analysis of the local geology, studied similar projects in the area, and utilised geophysical data collected on land and from boats. Though this did not provide physical samples to review and test, this effort gave the team an understanding of the seabed composition, revealing the presence of two key substances – basalt and mudstone.
Mudstone can be particularly challenging to drill through. Some mudstones react with fresh water to swell and can close in on the drill bit, locking it in place.
Additionally, mudstone’s fine particle size can mimic the behaviour of traditional drilling fluid, creating a thick, unworkable substance.
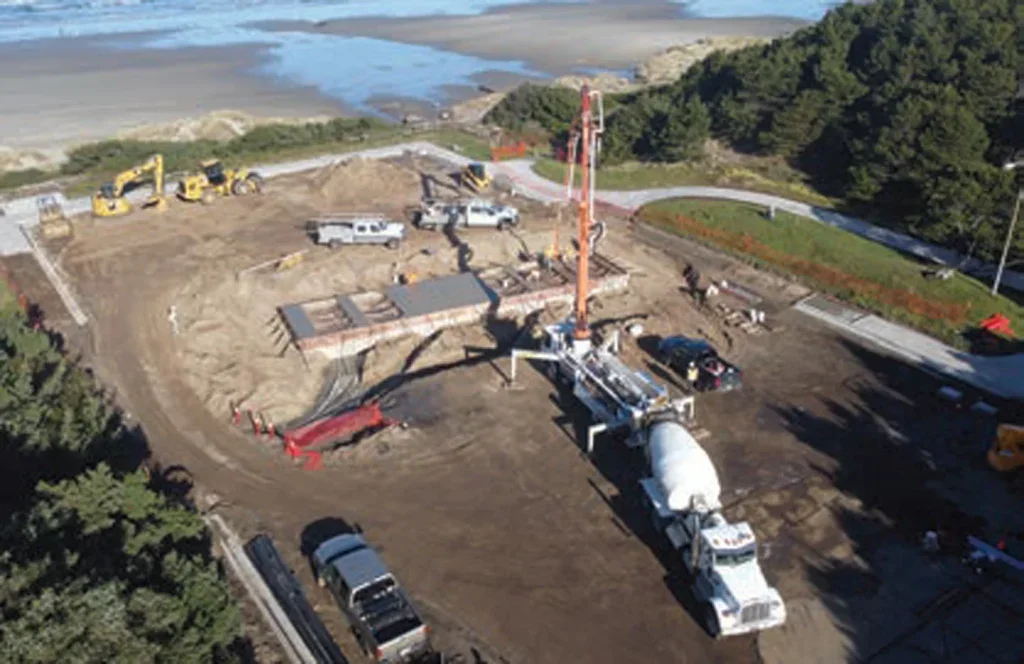
To address challenges associated with the drill locking, the project team lab tested the mudstone’s composition from samples taken in onshore explorations. This enabled the team to formulate a specific type of fluid that reduced the risk of the drill bit getting stuck.
The drilling fluid was engineered with dual objectives in mind. Firstly, it aimed to minimise the ‘stickiness’ of the clay and alleviate some of its reactive characteristics. However, many additives that address these issues often diminish the suspension properties within the drilling fluid, thereby hindering its ability to effectively transport solids and cuttings from the bore.
To address this, additional adjustments were made to the formula to uphold adequate suspension capabilities without compromising the primary purpose of the fluid.
The potential presence of basalt also required careful preparation, with the studies indicating that the team could encounter basalt in dikes and sills 9.1m (30ft) or more in thickness. Basalt can affect the rate of drilling, as well as have strong magnetic signatures, potentially disrupting the drill’s magnetic steering and sending drilling activity off course.
To ensure that basalt-related magnetic structures did not pose a risk to the project, the team deployed a gyroscope. Gyro steering does not rely on the earth’s magnetic field, but utilises accelerometers, which allow the drill’s position to be calculated as it is advanced.
The steering method also eliminates the need for deploying a coil wire grid into the ocean, which would be required to maintain drill alignment without a gyroscope and would pose significant challenges along the volatile Oregon coastline. Securing and maintaining a coil wire grid in such conditions would be inherently difficult. Moreover, it would entail further encroachment into the marine environment, thereby undermining the low impact benefits that HDD methodology offers.
With gyro steering, the team were able to successfully guide the offshore bores to within 40ft of their planned exit, around a mile from the drill rig.
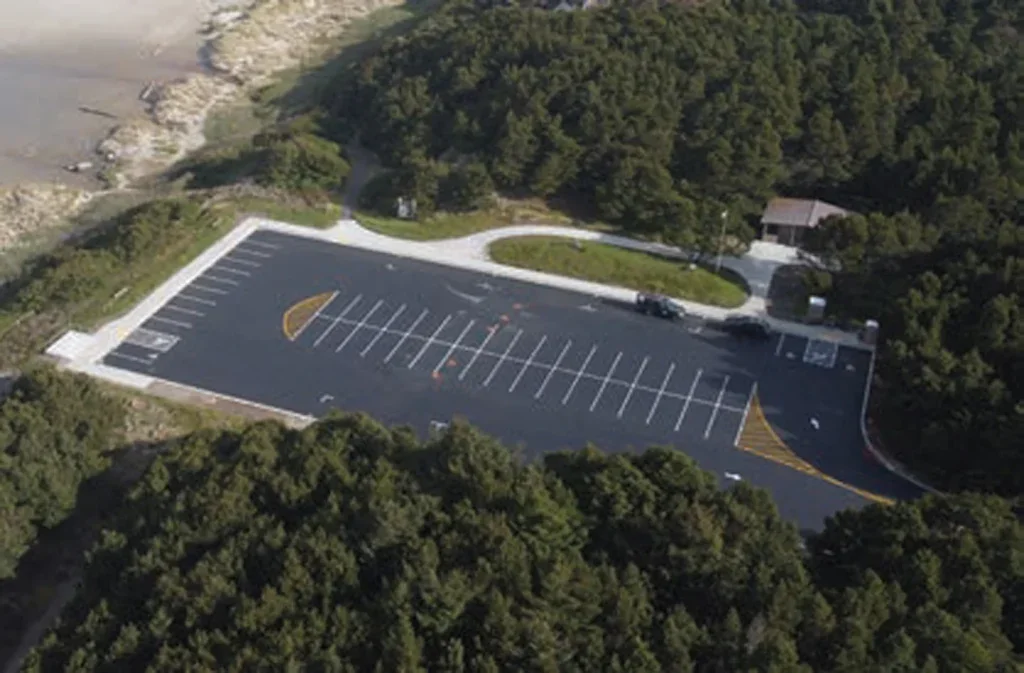
A FIGHT AGAINST TIME
Time constraints added another layer of complexity to the project. The federal permitting for the project took almost a decade to issue the relevant construction permits due to the unique nature of the project.
Under normal circumstances, the design phase of such a project could have taken at least a year. However, to help meet the operational goals of the project, an abbreviated design schedule was developed that allowed the team to complete the design in just five months.
Instead of adhering to pre-determined design milestone phases at 30%, 60%, 90% and 100%, the project team of Jacobs, OSU and The HDD Company worked continuously and collaboratively, solving problems as they arose.
The state park also granted OSU permission to be onsite for only one year, limiting the time for construction.
The HDD Company was able meet this aggressive time limit for HDD construction through the strategic utilisation of two rigs simultaneously, an uncommon approach given the large size of the drill rigs required for HDD bores of this size and length. By carefully timing the HDD punchouts into the ocean to be concurrent, the project minimised the need for multiple construction dives per punchout, a crucial adaptation considering the unpredictable nature of weather windows in the area.
Additionally, all custom equipment, including pipe tong equipment, was engineered for maximum mobility, enabling rapid movement between HDD bores.
The PacWave South project is a testament to the power of innovation, collaboration, and determination.
The team was able to successfully navigate a multitude of challenges, delivering the project on schedule and within budget.
On completion, the PacWave project will mark a significant milestone for wave energy generation in the US.
Our hope is that this project can help unlock new forms of clean energy, contribute to energy transition and, ultimately, the journey to net-zero.