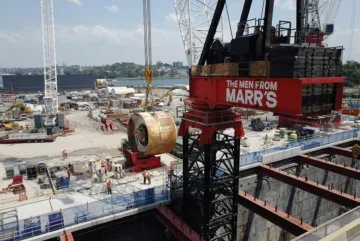
Metro projects present a unique set of challenges for project owners, their construction partners and engineering teams. By design, metro stations are located in heavily populated urban areas. High traffic density, congested sites with limited space for construction works, and demanding construction schedules are par for the course.
Since 2016 Marr has been working with Sydney Metro and their constructors to develop a new approach to cranage that is helping to take the complexity out of large-scale transport infrastructure projects.
Similar projects around the world have adopted the cut-and-cover box method, where crawler cranes are nearly always the immediate consideration, but our approach has consistently demonstrated that strategically installing the right cranes can change the way an entire project is constructed, principally because of the ability to lift bigger pieces and remove the requirement for costly, challenging and time-consuming groundworks.
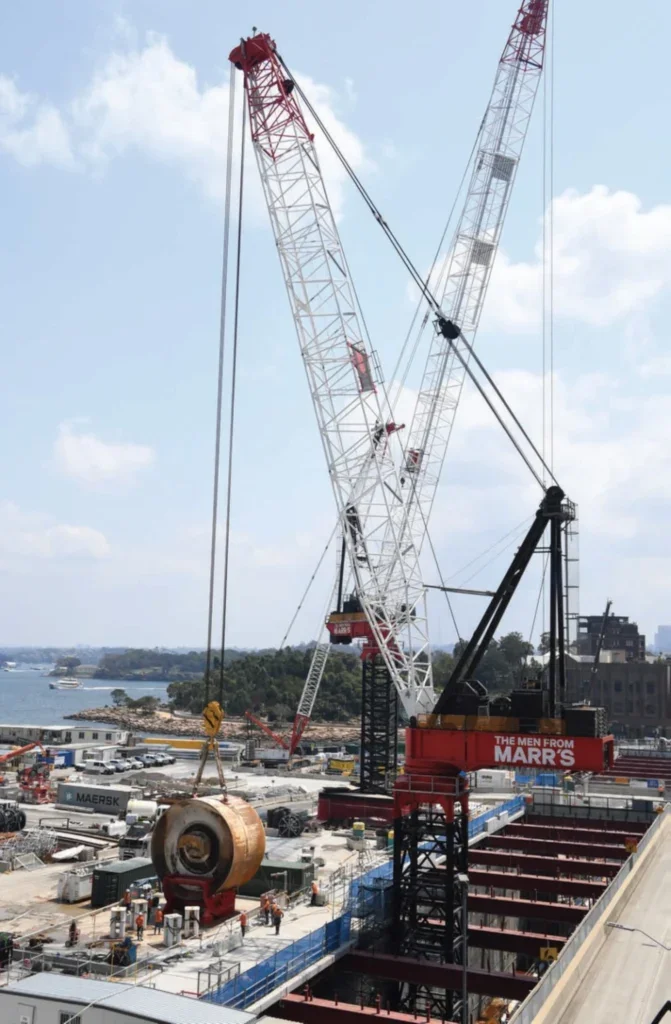
From our initial engagement on the construction of Sydney Metro’s Castle Hill station, we’ve subsequently been engaged to deliver bespoke cranage solutions across 14 stations.
By adopting lessons from other projects and sectors and working collaboratively with our clients, we’ve developed cranage solutions that have enabled the delivery of safer, faster and lower cost projects – all with the goal of simplifying construction.
EARLY ENGAGEMENT IS KEY
Key to the successes we have achieved for our clients on these projects has been the willingness of project teams to engage us early in the planning stages – and to think differently about how cranage solutions can be procured and delivered.
The traditional approach to construction views cranage through the lens of achieving the crane budget, which is a small package in relative terms on most projects. This approach only considers cranage once design and procurement are established, which limits the opportunity to develop innovative solutions to address project challenges.
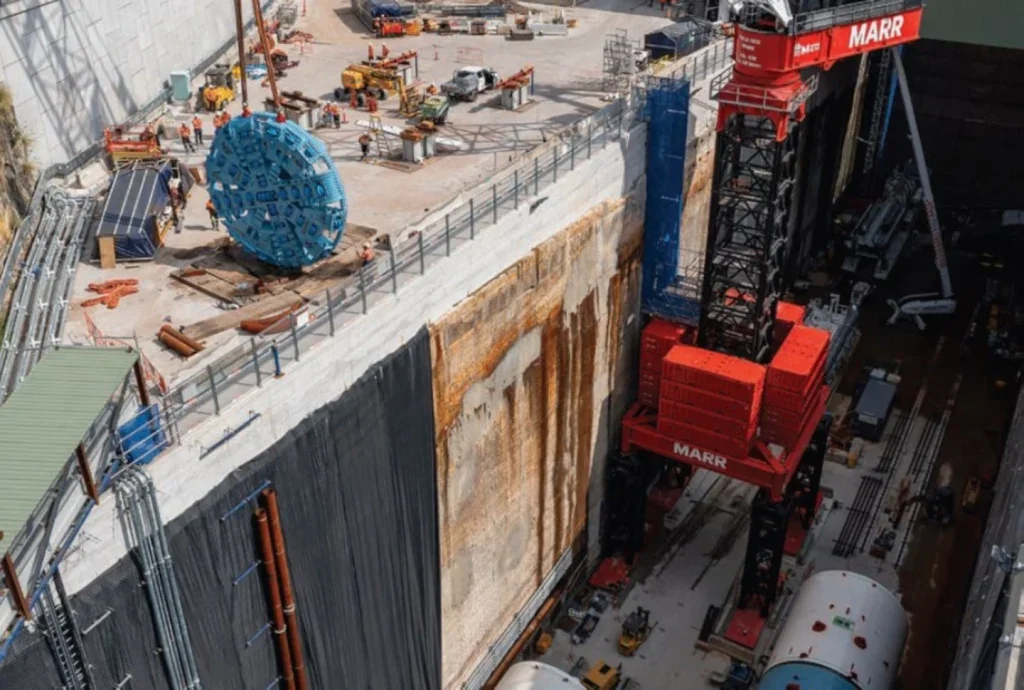
The early engagement approach to crane selection offers the possibility to change the way a project is delivered, with fewer engineering, procurement and construction activities.
It always comes back to the fact that cranage doesn’t need to be as hard or complex as it often becomes. It’s about getting the right solution for the project and the challenges that come with it, but there is often too much focus on the crane instead of how it is working for the project. Importantly, the cranage solution should serve the project, not be ‘star of the show’.
OUT-OF-THE-BOX SOLUTIONS
Our first involvement with Sydney Metro was working with the Northwest Rapid Transit (NRT) Consortium on construction of the Castle Hill station.
NRT was initially considering a cranage solution using crawler cranes travelling along the edge of a 200m x 30m cut-and-cover station box to cover the required lifts. However, as is the case with many metro projects, the site was congested and landlocked between two existing roads. The traditional approach would have placed a large surge load against the station box walls, with the consequence of having to excavate around the box and fill in with groundworks to specific bearing pressures.
Off the back of working on Australia’s largest resources project at the time – the Gorgon LNG Project, where we introduced large capacity tower cranes to address the challenges of working in a congested area with limited space for crawler cranes – we looked at NRT’s challenges from a different perspective.
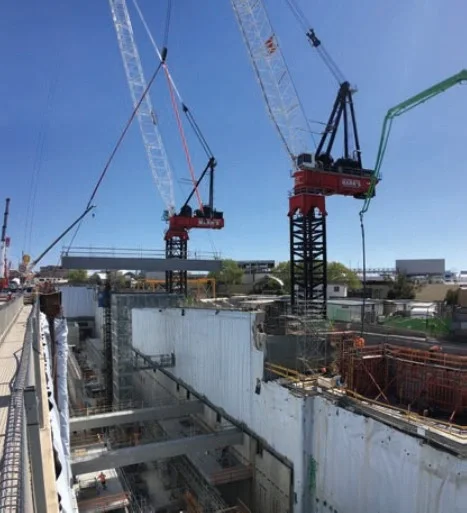
Understanding the benefits of combining fewer cranes with greater efficiency, Marr’s solution of using two heavy lift luffing tower cranes, sitting alongside the station box, provided lifting capacity across the entire site and changed the way the whole project was constructed.
Our approach – using fewer cranes with greater capacity and reach to deliver less complex, more efficient, and safer ways of constructing – also became a new blueprint for other metro station builds on Sydney Metro.
ADAPTABLE AND FLEXIBLE SOLUTIONS
Working collaboratively with our clients to deliver the best outcome for their preferred construction methodology, we’ve adapted our approach to suit the specific constraints of each project – changing where we locate the cranes from outside the station box to inside, on the side, or on gantry systems halfway between the tunnel boring machine (TBM) tunnel exit and entry points.
After working with John Holland and CPB Contractors as part of the Metro Trains Sydney Consortium, the John Holland CPB Ghella (JHCPBG) Joint Venture engaged Marr during the tender process to develop a cranage solution for Sydney Metro’s Barangaroo station.
JHCPBG wanted a solution to allow heavy precast concrete elements to be installed, reducing the construction programme. It also had to address the challenges of working on a restricted harbour-front site adjacent to another development, with limited real estate for access and the movement of equipment around the site.
The other significant challenge was how to retrieve TBM sections weighing up to 255 tonnes midway through the construction programme.
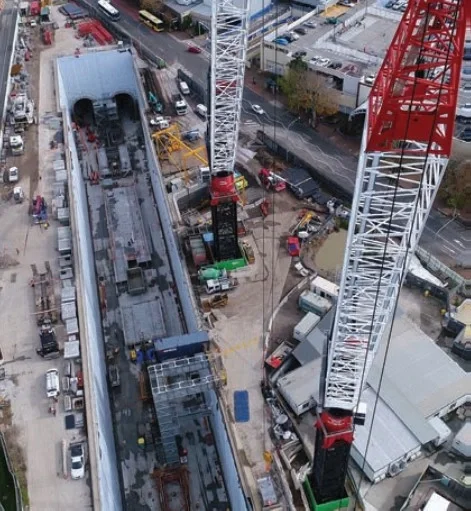
JHCPBG had proposed using a crawler crane to remove the TBMs, but the need for additional groundworks on an already congested site, with limited areas for laydown and access limitations due to night lifts to facilitate road closures (another common constraint on metro projects), made it an inefficient option.
The solution we developed – using an M2480D and M1280D heavy lift luffing tower crane sitting on purposedesigned foundations in and outside the station boxes – provided lifting capacity across the project (including the TBM components); it took up less than 90 per cent of valuable space than the other, initially proposed method. It also provided the option to build with precast beams, allowing for increased modularisation and fewer lifts.
A SIMPLER APPROACH TO TBM ACTIVITIES
The traditional approach to installing and removing TBMs places large crawler cranes outside the station box.
This tends to be a very complex lifting operation, involving a number of logistical and safety challenges, particularly when working in high density urban environments like metro projects.
Putting a large crawler crane alongside temporary structures imposes a significant surcharge on those temporary structures to perform a specific lifting activity. This then requires building even more temporary works to support the existing station box or using the temporary works to support and strengthen the box. That’s complex and expensive.
The other problem with using a large crawler crane is that it takes up valuable space in what are already heavily congested sites for TBMs to be removed, disassembled and loaded out. This brings another set of challenges because it requires working around other crane activity, transport movements and interfaces with other workers, which then becomes a risk in terms of safety and schedule.
The TBM solution developed for Barangaroo station was a world first. We’ve since supported Sydney Metro and their construction partners with a simpler, safer approach to 12 planned TBM activities across the project.
Leveraging the benefits of our M2480D – which, with a maximum lifting capacity of 330 tonnes, is the world’s largest capacity luffing tower crane – our solution allows us to manage the lifting operations without impacting the existing temporary works. The net result is less congested, less complex and much safer worksites.
BESPOKE SOLUTIONS FOR UNIQUE CHALLENGES
Another example of how adaptable our solutions are is the one developed for Sydney Metro’s The Bays station. The site was so congested that there was no room available for delivery of the TBM due to the surcharge on the load of the station box wall.
Working with the John Holland CPB Contractors Ghella Joint Venture, we built an M2480D on a portal frame over the top of the TBM, allowing the machine to drive under the crane to begin its tunnelling work. It was a simple solution, allowing the contractor to build the TBM in the station box without the crane adversely impacting the project or the programme.
Another benefit of considering cranage at the front end of a project is that it can be built into the design. Station construction requires large precast elements, so it’s about considering how to maximise the weight of those components to enable fewer, heavier lifts.
Designers can also take the capacity of the crane and apply it to other parts of the project – even down to how reinforcing steel is unloaded. Instead of the traditional method of lifting piece by piece, it’s possible to lift the entire trailer load with a heavy lift crane and place it close to the work front, where it can be distributed faster and easier.
All those little productivity gains add up when it comes to securing the construction programme.
And, with a global shortage of skilled labour, it’s also about how we can take some of that pressure off a project by applying the right cranage solution with heavy lift, high volume construction machines that can deliver real productivity gains.
ADAPTING TO OTHER SECTORS
The future of urban transportation lies in major tunnel works beneath the surface and cities around the world are continuing to invest in underground transportation infrastructure.
Delivering these mega projects in a cost-effective, safe way with as little disruption as possible to the communities they serve is a constant challenge that requires innovative thinking across every part of the build process.
The solutions developed across Sydney Metro can be adapted to the design and construction of similar largescale rail and metro projects.
The advantages of this new approach are not limited to metro projects alone. We have already seen how learnings from Sydney Metro can easily be transferred to other sectors, such as some of the large industrial projects we are currently working on in the UK.
Innovation is never a one-way street. It requires constant learning, knowledge transfer and collaborative thinking. One of the benefits of exporting our technology into markets like the UK is that we have been able to learn from our clients and embrace different approaches in areas where the UK is more advanced than Australia.
Ultimately, the willingness to collaborate on the basis of ‘cranes as a forethought, not an afterthought’ can have a significant impact on ambitious projects. The key is getting the right solution for the challenge – and that will always be one that serves the project, not the crane.