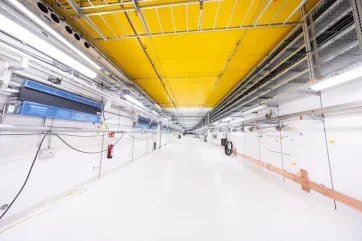
Construction of the northern section of Germany’s FAIR particle accelerator, which includes a 1.1km tunnel, is nearly complete.
Porr, which is responsible for the build, has installed more than 340,000m3 of reinforced concrete and 40,000 tons of reinforcing steel. The final concrete component – a small external staircase – was cast in February.
The FAIR (Facility for Antiproton and Ion Research) particle accelerator is being built at the GSI Helmholtz Centre for Heavy Ion Research in Darmstadt. The facility accelerates particles to near the speed of light.
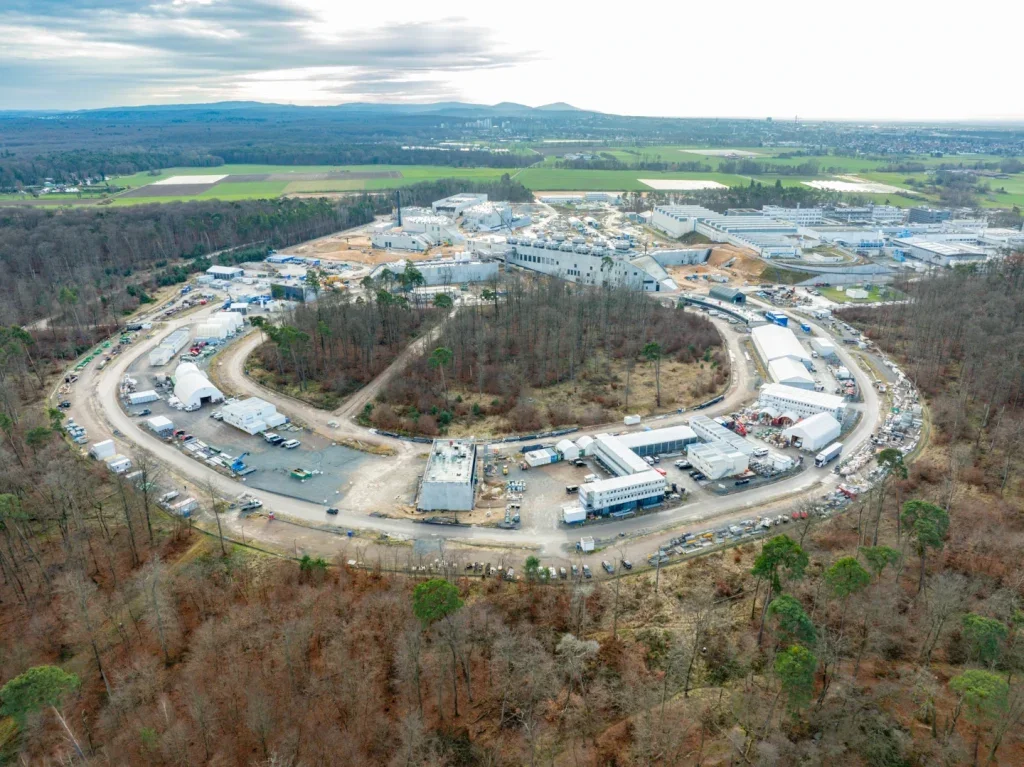
The central structure of the entire facility, including the northern section, is the 1.1km-long, up to 40m-wide tunnel for the SIS100 ring accelerator. It is complemented by structurally interconnected underground and above-ground facility components such as accelerator and experimental structures, operational and utility structures, as well as transfer lines and storage rings.
Porr built the circular accelerator tunnel as well as nine above-ground and underground buildings for experiments, operational and utility facilities in the northern construction area.
Porr says the challenge was not only the logistics of the large amount of earth – the large number of pipes required for the supply and disposal of the particle accelerator also presented new challenges for pipeline construction.
The planning of the pipe network followed the “form follows beam” principle to ensure a compact system. Only necessary components were installed in the tunnel, while the ventilation lines and cable conduits were laid outside in the sand bed.
The high level of complexity arose from the 3D geometry and the number of pipes that had to be measured, welded, and installed. A 3D model was used as the basis for the installation.
Numerous lines were run up to 13m high and embedded in compacted layers. For ventilation, 4,400m of HDPE spiral-wound pipe and 3,000m of heat-resistant carbon steel pipe were installed, along with 100,000m of cable conduits. Furthermore, approximately 2,500 electrical conduits were connected to ensure watertight pressure resistance, and expansion joints enabled vertical displacement.
Porr says the construction materials also required innovation. The three-cell tunnel was built using open-cut reinforced concrete construction – a frame structure with massive components. This includes the 6.35m-thick slab with a 29m span, which was constructed using formwork on a supporting scaffold.
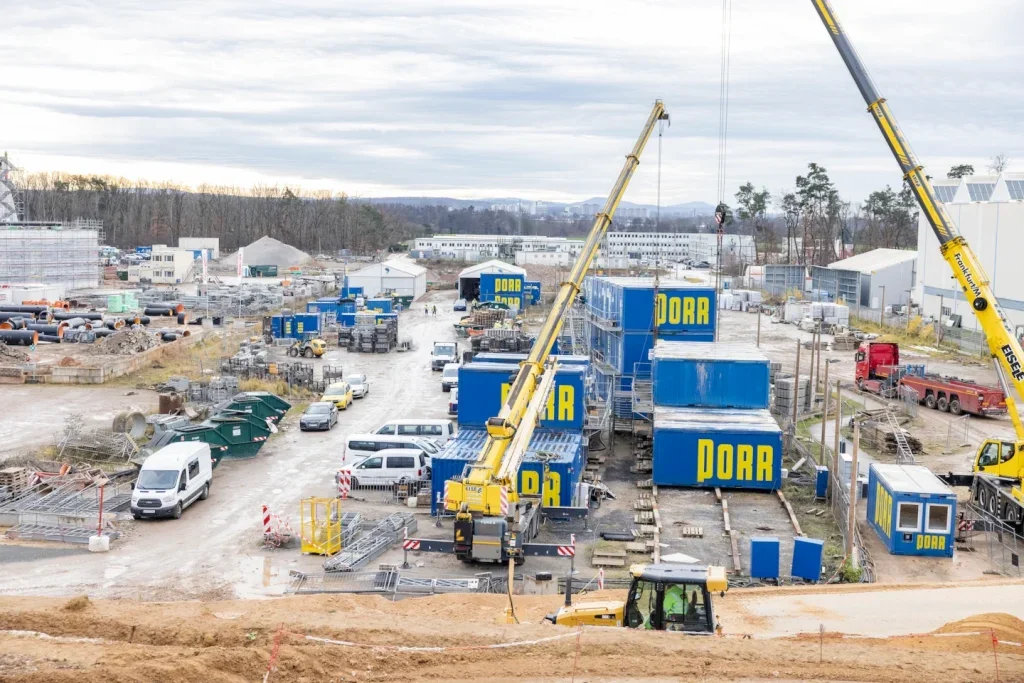
“What’s special about this structure is that it is 18m underground and will later be completely covered,” says Porr.
A major challenge was the wall axis on which the slab rests, with a reinforcement ratio of up to 750kg per cubic meter of concrete. For this, Porr used a self-compacting concrete developed specifically for the project in collaboration with a concrete manufacturer.