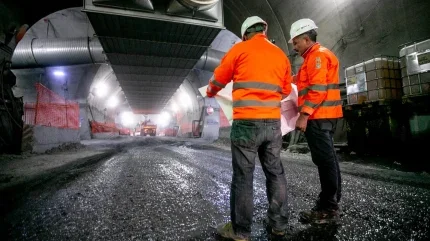
The history of Salini-Impregilo dates back 110 years, when in 1906, in Milan and in Piacenza, two men: Vincenzo Lodigiani and Umberto Girola established their companies, constructing their first projects locally in their respective home towns. In 1936 Pietro Salini established his construction company, Salini Costruttori.
Salini Impregilo Group was born on 1 January 2014 as the result of the merger by incorporation of Salini into Impregilo.
The companies joined to consolidate their experience and create a player with technical and financial capacity and industry knowledge.
Today Salini Impregilo is an industrial group specialising in the construction of complex projects, operating in more than 50 countries with 35,000 employees, a turnover of around EUR 4.7bn (USD 5.08bn) and an order book of more than EUR 33bn (USD 35.65bn). Salini Impregilo is a global player in the construction sector and the leading global infrastructure company in the water segment.
Last year the company presented its 2016-2019 business plan in London, announcing key targets. Pietro Salini said: “The Group’s new 2016-2019 Industrial Plan aims to strengthen Salini Impregilo’s role as market leader in large, complex infrastructure, confirming its leadership in the water segment and continuing to develop its presence in transportation, in particular metros, railways and roads. The Plan is focused on generating free cash flow. The expected growth, guaranteed by an order book that covers nearly 70 per cent of total revenues.”
Regarding tunnelling works, Nicola Antonio, a civil engineer who has been working at Salini-Impregilo’s Underground Works department since 1996, says: “Over the years we have executed every kind of tunnel, worked in difficult situations. We are able to operate in the middle of nowhere in the Icelandic tundra or in an ancient and crowded city centre as in Copenhagen.
“Mostly our experience has been with TBM, but we have also worked with drill and blast, for example on a highway project in Slovakia and for part of the high speed rail tunnel between Milan and Genoa.
“We don’t usually provide the design for our tunnelling works, our normal involvement is to coordinate and supervise the design of our consultants.
“The tunnelling sector is really important for the company, covering some 40 per cent of 2015 turnover,” Nicola says. “For example most of our hydroelectric projects always include tunnels or underground works.”
Past Projects
“The first modern TBM project for us was the rail tunnel for the Passante line in Milan in the early ‘90s, where we were [an early adopter outside Japan for the use of EPB machines with foam] and [also for] plastic dowels and guiding rods to connect the segmental lining,” Nicola explains. “The TBM was 8.03m diameter and bored a 4km-long tunnel through alluvial sand and gravel. After that we have utilized more than 60 TBMs for a length exceeding 500km.”
Other relevant jobs include: the Yellow River Diversion Project (Wanjiazhai) in China, which required the excavation of a 90km-long hydraulic tunnel with four double shield TBMs with diameter of 4.8m through limestone and sandstone; the West Side CSO Tunnel in Portland, Oregon, using a hydro shield TBM for the first time in the US.
“We utilised two 4.9m-diameter machines in gravel and cobbles below the Willamette River, with a constant water pressure around 4 bar,” Nicola says.
“I’d also like to mention the Gotthard Tunnel for the excavation of the Bodio and Faido lots for a total length of about 60km with two main beam machines of 9.3m diameter, mainly in metamorphic rocks with cover exceeding 2,000m; Copenhagen Cityringen and Doha Metro Red Line North were two metro projects in dense urban areas, with four EPB TBMs in each project, both projects in water bearing soft sedimentary rocks.
A recent project is the Lake Mead Intake No. 3 in Las Vegas, Nevada, completed in 2014, where Salini- Impregilo used a 7.2m-diameter hybrid TBM (slurry/open).
“On that occasion we moved a step forward in the limits of the tunnelling industry, reaching the outstanding operating pressure of 16 bar for a long portion of the drive below the Lake Mead in metamorphic rock. This pressure was never experienced before in the world.”
Tunnelling Trends
Mechanized excavation has seen impressive improvements including flexibility.
“In the recent past, the TBM could be used only if the geological conditions were supposed to be homogeneous all along the drive. All the miners with grey hair like me have spent a lot of time and efforts to pass through faults or other critical situations that, today, with modern hybrid or Variable Density machines, are not even detected.
“Other substantial improvements have been reached in the technology of the ground conditioning, of the backfill grouting and of all the aspects of the segmental lining. The tunnelling technology is constantly progressing and tomorrow we will be in position to perform tunnels that can not even be imagined today.”
Salini-Impregilo is working all around the world and about 85 per cent of its turnover is made abroad, so the company is used to following all the markets. “Today I think that the best performing countries are US and Australia, where we are concentrating most of our efforts,” Nicola says.
Forrestfield-Airport Link
The Forrestfield-Airport Link (FAL) is an upcoming project in Perth, expected to start in mid-2017 and last until 2020. The EUR 791.7M (USD 854M) rail link will connect with the existing Midland line near Bayswater Station and will run to Forrestfield through underground tunnels, to ensure minimal impact on the existing land and road network.
The project aims to increase public transport options for the eastern suburbs and foothills area and to improve access between the city and Perth Airport.
Early in 2016, the Western Australian Government awarded the major contract for the Forrestfield-Airport Link project to Salini-Impregilo (80 per cent) and NRW (20 per cent), an Australian company specialising in the civil, mining and construction industries.
“I don’t know exactly how we beat our competitors; however, this kind of work is quite familiar for us,” Nicola says.
“Of course every project is different from another but we have already managed several TBMs with environmental or traffic constraints. We experienced that in San Francisco, Copenhagen, Milan and so on”.
Awarded by the Public Transport Authority of Western Australia, the contract includes the design, construction and maintenance for 10 years of the Forrestfield-Airport Link, which will connect the eastern suburbs of the city with an existing suburban rail network as well as the airport. Its total length will be 8.5km, 8km of which will be underground. Salini-Impregilo and its joint-venture partner will bore twin tunnels for virtually the entire length of the line and build three stations.
Parking spaces and new and expanded bus feeder services will also be built.
The designing of Forrestfield in Perth is carried out by a group of designers, composed of GHD (leader), Geodata and Coffey.
Preliminary works are underway at the Forrestfield end of the rail line, with relocation of key utilities complete and work set to start on the construction of the ‘dive structure’ or entry points to the rail tunnels at the time of the interview.
Rail Route
After evaluating route options between Bayswater and Perth Airport to accommodate existing road layouts and future upgrades, it was decided that the rail route would be through mainly underground tunnels. They would run from Bayswater Station on the Midland Line along Tonkin Highway and Brearley Avenue into the Perth Airport Estate and on to Forrestfield.
This route is expected to travel through the Midland Line rail reserve, Tonkin Highway road reserve, Brearley Avenue road reserve, Perth Airport Estate and the Public Transport Authority rail reserve in Forrestfield. As the line will be located almost entirely underground, the impact on surrounding communities will be minimal, both during construction and once the line is operational.
The depth of the tunnels as they run under the Swan River will be 24m.
Bayswater Junction is the tunnel portal for the trains, and sits in the road reserve near Tonkin Highway. This will provide the entry for trains to the tunnels, starting their underground journey to Forrestfield.
In Belmont station rail tracks will be fully underground, running inside the tunnels. Some features include a bus, a train interchange and a car park with 500 to 1,000 bays.
There will also be a completely underground station to serve Perth Airport, which is undergoing a major redevelopment.
This Airport Central station is expected to assist the increased demand in both air passengers and staff working at this major aviation hub.
Located at east of the Perth Airport, the railway station is adjacent to Dundas road at south of Maida Vale road.
Forrestfield Station aims to deliver a significant public transport boost to Perth’s growing eastern and southeastern suburbs. Forrestfield station will also provide a bus feeder network, parking for almost 2,500 cars, and serve future residential and business developments.
Passengers will enter Forrestfield station at an elevated arrival area with a clear view down to the 150m-long island platform below. Access to the platform will be via a SmartRider fare gate, with escalators, lifts and stairs taking passengers to the lower level to take the train.
We studied several working phases to never stop the traffic of the train on the existing line,” says Nicola. “So we have to build a temporary line on one side and then restart the existing line”.
Mechanised Tunnelling
Two TBMs have been supplied by Herrenknecht to excavate the 7m-diameter twin bored tunnels. TBM components were manufactured in various places around the world before an in-depth nine-month assembly and testing program was conducted in China.
Once testing was completed, they were disassembled and shipped to Fremantle Port, in Western Australia.
When the TBMs arrive onsite in Forrestfield, they will be lowered into a dive structure to begin their two-year excavation journey towards Bayswater. During the 8km journey, the TBMs will excavate under Perth Airport and the Swan River, reaching up to 30m depth below the surface.
The two TBMs will be staggered two months apart to help ensure ground stability. The first TBM will start in July and will finish tunnelling approximately April 2019. The second will start in September and finish tunnelling approximately June 2019.
Each TBM is 130m in length, weighs 600t and will be operated by a team of 15 people. The driving force pushing the TBM forward is up to 5,000t. The TBMs will be Mixshields, set up for variable ground conditions.
“Our client has conducted a geological investigation and after the results, the Technical Specification of the Contract required a machine capable to operate both in EPB and slurry,” Nicola says.
“On this basis we selected to mobilise two Variable Density TBMs and we expect to use the TBM in a slurry mode in all the area under the airport. So it will be the 75 per cent of the drive and then, we have to decide according to the geological conditions if we have to operate in EPB mode or we can continue with the slurry mode.
“It is a quite long tunnel spanning more than 7km through alluvial plain and reaching some remarkable depths between 7m and 25m. We have to cross most of the geological formations from clay to sand to weak rock – there is a long portion in rock. At the end there is an intersection with an estuary, which represents the most critical point. On the other hand we have to cross below the airport strip and the station of the international airport boring through sandstone.”
Regarding the possibility to meet any geological faults, Nicola says, they expect running sand, classic clay and weak rock. “We are not concerned about that because we don’t have serious geological issues and faults.”
“We have some intervention for ground improvement at the break-in and break-out of the station,” said Nicola. “We need to cross two stations, and to improve the ground where we have cross-passages.
“The TBM must have the capability to grout outside because we can’t have access from the surface in the airport. We can’t make any intervention from the surface. That was an agreement between our client and the airport authority as required in the tender.
“We usually use permeation grouting or jet grouting. If necessary, we are able to use compensation grouting or other special intervention, but there is no need to use any special ground stabilisations at the moment.”
Nicola mentions the need to monitor all the drive both from the surface and from underground. “Under the airport the ground movement is almost 0 because we have quite tight tolerance under the settlements,” Nicola says.
“Anyway this is not very big tunnel – more than three diameters of cover – so we will take care but we are not afraid of this limit.”
Lining
The segmental lining will be the same all along the tunnel, for a total of 60,000 precast concrete segments, which will be cast in a factory a few kilometres away from the portal. The precast plant utilises a carousel system with nine sets of moulds, supplied by Euroform. The ring is made of five segments plus one key and the length of segments is 1,600mm.
The concrete of the segments will be class f’c = 60 MPa, reinforced with 40 kg/m3 of steel fibres and a frame of steel bars.
Logistics
The main station will be exactly in the square of the airport station.
“We have performed a management plan for the construction of the station in order to reduce the impact on the usual activities of the airport and to comply with all the restrictions specified by the contract,” Nicola says.
“The problem may be the truck, which has to remove the material and bring the segments. This can be concentrated in certain hours; it depends on the future measures.”
Excavated soil will be pumped out as slurry to the Forrestfield site where it will be treated for reuse and or disposal. It has been expected to excavate 800,000cu.m of spoil, which could be reused by the airport for embankments and roadworks.
Tunnelling Benefits
The aim of this project is to improve public transport options to and from the eastern suburbs in addition to reducing the strain on current transport infrastructure due to passenger growth.
The Forrestfield-Airport Link has also been designed for easing road congestion:
- To create additional rail capacity on the Midland Line in the inner suburbs of Perth, where demand is expected to exceed current supply in the near future.
- It can also provide a 20-minute rail journey from Forrestfield to the city, which currently takes 45 minutes by car in peak hour.
- To halve the current 70-minute travel time in peak hour from Kalamunda to the city by providing improved bus feeder networks to Forrestfield Station.
By 2021 the Forrestfield-Airport Link is expected to generate 20,000 passenger trips on the suburban rail network every day, increasing to 29,000 daily by 2031.
Transport minister Bill Marmion says, “putting most of the line (8km) in twin bored tunnels will reduce impacts to the community and the environment.
“Placing the rail line underground has several benefits: it minimises disruption to the community during construction; it is the least intrusive solution in terms of visual amenity; there will be a limited impact during construction and operation to the environment.
“The depth of the tunnels varies depending on the location. The deepest point is under the Swan River at around 26m and the average depth under the airport aprons and runways is 15m.
Construction of the tunnels will not impact the river because the bored tunnelling process will not disturb the bed of the river or alter flows within it.”
The Public Transport Authority of Western Australia will continue to consult with the Swan River Trust and will manage any potential impacts from non-tunnelled sections under the Swan and Canning River Management Act 2006.
“Typically the commencement date of twin tunnels is staggered to simplify the commencement process, prevent the movement of one machine affecting the other and so that any lessons learnt from the initial tunnelling can be applied to the second machine,” adds Marmion.