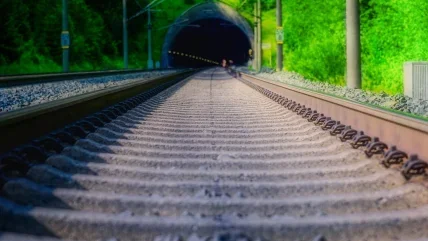
The world may be struggling under the adversity and tragedy of the Covid-19 pandemic but the British Tunnelling Society (BTS) is doing its best to maintain a programme of lectures and meetings on a virtual platform. Its meeting on 18 June shows how well these efforts are being supported by the wider tunnelling industry: more than 2,600 people viewed the BTS YouTube channel showing of a talk that evening given by Peter Harris – Director of Civil Engineering at COWI UK – and over 60% of those came from outside the UK.
Harris is clearly an expert in his field of UK railway tunnels and provided a very informative lecture on the construction of the tunnels in the great railway age of the 19th century. So extensive was his talk it is impossible to give credit to all the detail it contained and this report will only cover some of the highlights.
Harris split his talk into five distinct elements:
- The tunnel alignment survey
- The construction of shafts
- The work away from the shafts to form the tunnel
- The portal structures
- Details surrounding the development of tunnels.
Tunnel Alignment Survey
Tunnels were aligned often by constructing a sighting tower at the highest point on the tunnel alignment and sighting from one portal site to the other using a transit theodolite. Intermediate shafts could then be aligned using the theodolite. Such sighting towers would often be constructed in masonry and then enveloped by a timber windbreak structure. Masonry sighting towers remain around the countryside.
Shaft Construction
Early tunnels were built from portal to portal but as speed of construction became increasingly important shafts were used along the tunnel to provide ventilation and speed-up the programme. Once sunk, shafts could be used to work faces, splitting the tunnel into a greater number of working faces rather than the two usually seen in an end-to-end construction.
Shaft winding equipment always centred on winders and kibbles. In the early days the winder was a horse powered gin, before the move to steam driven beam engines and steam-driven cranes.
Shafts were typically 9 to 10ft (2.7–3m) in diameter and brick lined. An important feature of early tunnel construction was that the method of work always involved two separate teams of workers: the mining team would open the ground and excavate, and the bricklaying team would line the tunnel with brickwork before the excavation could recommence.
The initial section of the shaft would be excavated at ground level; a top timber frame laid at ground level and a lower timber frame pocketed into the ground and hung from the top frame using cast iron rods. This lower frame would then act as a sole plate for the brickwork to be built up from. The excavation was then continued from frame to frame, each downward advance lined with brickwork before excavation started on the next advance.
At a point just above the tunnel crown, a large bottom timber frame would be pocketed into the ground to support the shaft brickwork above and the lower section of the shaft mined to tunnel invert using timber square work.
A heading would then be mined out along the tunnel alignment to connect together all the intermediate shafts and the two tunnel entrances.
Tunnel Construction
Once the shafts had been sunk, it was possible to align the tunnel to be constructed by wire drops to tunnel invert level. Two plumb bobs were suspended from wires falling all the way to the shaft bottom and there damped in barrels of oil or sludge. The wires could then be used as a transfer of sight from top to bottom.
The tunnel cross-section was always set out from a series of circular curves: the miners and bricklayers would work on a series of radial offsets to set out either the alignment of the excavation or the brickwork.
Tunnel construction would proceed out from a break-out chamber adjacent to each shaft and the tunnel worked in a series of lengths from the shaft.
Each length would vary from between 8ft and 15ft (2.4 – 4.6m) depending upon ground conditions. In so-called ‘heavy ground’ – a term used for weak and water-bearing ground – the length of advance would be shorter. The roof of the excavation was supported by 12 –18in (300-450mm) round tree-trunks; the crown bars that would be dragged forward for each length. Mining teams excavated the tunnel length by length, with each finished length handed over to the bricklayers for lining. Typically, each length would take four to five days of construction. By working from a number of different faces in the tunnel, miners and bricklayers could be continuously employed on its construction.
Typically, each length would take four to five days of construction – mining and bricklaying – and the tunnel would be advanced length by length. Gangs were employed on a subcontract lump basis, with each gang being managed by a ‘butty man’, somewhat similar to being ‘on the lump’ in the mid-20th century.
Bricklaying would be worked across from the invert to the skewbacks (at each bottom corner) made out of purpose-shaped brickwork. The sidewalls were laid in free air and only the rood and crown laid on centring.
Portal Construction
Once the tunnel bore was complete, work would turn to finish the portal structures. Tunnel portal design varied in terms of the overall concept and effectiveness. Often, for reasons of economy, shallow swept-back, wing walls were used but these did little to brace the portal. Such flat-face portals are prone to cracking and parting from the tunnel lining.
Brunel adopted a more structurally competent portal design for his tunnels, providing curved sidewalls so that the portal could act as an arch.
An interesting feature of those tunnel portals designed by Brunel is that he often placed a 36ft-long (11m) bell mouth at the entrance and exit. Even in the days of 55mph train speeds, designers were concerned about the effect the air pressure wave would have on passengers as the train entered the confined space of the tunnel. The bell mouth was designed to dissipate the effect of those pressure waves. We now see a similar need for porous portals in the design of High Speed Two (HS2) but for speeds which are considerably higher.
Details
One very interesting element of Harris’s talk was seeing the way in which shafts were finished at their intersection with the tunnel crown. It was common practice at that location to place a cast-iron curb or shaft eye. The audience was left wondering how the great pioneers of railway tunnel construction ever managed to install the cast-iron curbs in those positions.
To view the presentation in total visit the BTS You Tube Channel at: http://tiny.cc/944osz.
Questions and Answers
The following questions were asked by the audience and answered by Peter Harris.
How was the void filled between the excavated ground and the extrados of the brickwork?
The sidewalls of the tunnel were generally vertical and required very little fill. However, the real problem was in the roof with significant overbreak, often evident above the brick arch. Drawings consistently show the overbreak filled with mortar. In many cases, these tunnel voids were certainly not filled with mortar. At Standedge [through the Pennine hills] specifically, the drawings show voids filled with mortar but later site investigation showed voids to be filled with loose rubble.
How was ground movement controlled above the tunnel construction?
Fundamentally, there was no system of controlling ground movement. For example, at the Macclesfield Tunnels which were constructed in sand with shallow cover, it is possible to discern the line of the tunnel on the surface marked by a 150mm-deep linear depression along the tunnel alignment. There were of course no sophisticated means of ground settlement control available to builders at that time.
Why were brick piers used to fill the over break above the brick tunnel arch?
Simply because it was easier to build piers than filling with rubble and the piers were considered sufficient at the time.
Is Network Rail still working on tunnel management strategies?
All tunnels on the railway have a tunnel management strategy and these are updated periodically.
What progress is being made on the programme of finding hidden shafts?
Most hidden shafts have now been located and Network Rail is working out what to do with them. This is very much an ongoing process.
Why were circular brick drains adopted on southern railways and not elsewhere?
There is no known reason – just different railway companies and different engineers.
Was lime mortar used in brickwork during the early years?
Yes, it would have been used in the early days but had the disadvantage of low strength. Occasionally, one sees in drawings the requirement for the use of cement mortar and even occasionally a requirement for Roman Cement. Brunel used Roman Cement in his Thames Tunnel to provide a rapid hardening mortar due to high water ingress.
How was the presence of groundwater dealt with?
In soft ground, miners often referred to water-bearing ground as ‘heavy ground’, requiring heavier timbers as the lengths advanced. The English Method of constructing a heading between shafts at the low level provided a drain. In cases of greater water ingress, additional shafts were constructed just to pump through; such extensive pumping temporary works can be seen at Kilsby Tunnel, Northamptonshire, and described in the TA Walker Severn Tunnel book. Shafts and additional works were often added on an ad hoc basis.
How are these tunnels now maintained?
Maintenance is very variable and tunnel specific. Tunnel maintenance programmes are based on inspection reports. Some now require extensive relining, with the trend moving to more and more repair. With more and more trains using the tunnels, the time to carry out the repairs is very limited.
What is the speaker’s favourite tunnel and why?
Standedge – having spent the past 24 years of my career there, supervising various works and innumerable nightshifts in the tunnel, and sleeping in my car at Marsden Station either side of the shift. Between the North and Central Tunnels at Standedge there is a chamber called ‘the cathedral’ which is supported by cast iron ribs. It is an amazing structure. I would have liked to have been married in that ‘cathedral’.