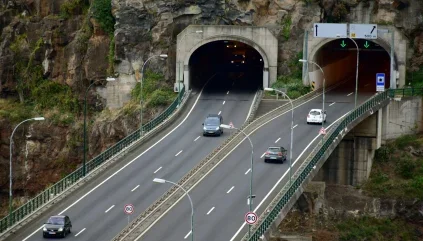
The discussion on the design of rubber sealing systems to keep out water from immersed tube tunnels – long tubes that can be assembled from steel or concrete sections, laid across the beds of rivers, estuaries or sea lanes – was presented by Nicas van den Brink, a design engineer with Trelleborg Ridderkerk BV.
Based in The Netherlands, he holds a master’s degree in industrial engineering from Technical University Delft and has worked in various fields of engineering. In civil engineering, his design work has included use of rubber to keep immersed tube tunnels watertight.
When the talk took place, in June 2020, the world was still getting to grips with the disruptive lockdowns brought in response to the covid pandemic. The talk was arranged to be shared online through a joint collaboration of the young member groups of the British Tunnelling Society (BTS – BTSYM) and the Tunnelling Association of India (TAI – TAIym).
The YM groups accelerated the take up of online media to share information, including through live online broadcasts via the BTS YouTube Channel, including this talk.
In his talk to the joint meeting of BTSYM/TAIym, van den Brink introduced Trelleborg’s activities within the sector, presented a brief history and working principle of immersed tube tunnelling, and then discussed rubber material properties and seal design. He has revisited the points of his talk for this article for T&T and also added some update points.
INTRODUCTION
The Trelleborg group is a large company that is a world leader in engineered polymer solutions, said van den Brink. The company was founded in 1905.
employs about 24,000 people globally and has about 120 manufacturing facilities. His business unit mostly serves the oil & gas and infrastructure & construction sectors, respectively, and is the Trelleborg Marine & Infrastructure Unit, containing his firm Trelleborg Ridderkerk BV, located at the edge of Rotterdam.
Trelleborg Ridderkerk BV manufactures engineered products for immersed tube tunnels, underground construction, energy, dredging, water management, and dealing with noise and vibration. In additional to tunnels, projects have included providing bearings for bridges and a storm surge barrier.
The company has supplied seals for immersed tube tunnels across the world – the major markets using the tunnel technology being Asia, the US and Europe, the latter of which has the largest concentration of such project for the company.
Key immersed tube tunnel projects he worked on include: the large Dalian Bay link and Shenzhong link projects, both in China; the Guldborgsund tunnel refurbishment, in Denmark; the Khor al Zubair tunnel in Iraq; and MOSE flood protection project in Venice, Italy.
HISTORY
Immersed tube tunnels are one technological solution for transport across waterways. The first concept for an immersed tube tunnel started in the early 19th Century when, in 1810, Charles Wyatt wanted to build a series of brickwork capsules to be lowered to the bed of the Thames and joined together.
The brick cylinders would have domed ends, acting as temporary bulkheads and would eventually be removed and the brickwork shells of the joined-up capsules would form an interconnected tunnel below the waterway. However, the project did not get built.
Toward the end of the century came physical proof that the concept really worked and this happened in the US, on the Boston sewer tunnel, in 1893, said van den Brink. “However, there was still not a tunnel that could be used for human transportation,” he added.
Such an immersed tube transport tunnel came almost in 1910, again in the US, with a rail tunnel at the Detroit River, in Detroit, Michigan, formed of twin parallel steel tubes.
Further immersed tube tunnels were developed across the world, including in the mid-1960s for Rotterdam metro, in Trelleborg Ridderkerk BV’s home town. The project was also the first time the company supplied rubber waterproof seals to such a tunnel.
Much later, during renovation of the tunnel, Trelleborg received some samples of the sealant back from the tunnel owner which, van den Brink said, gave valuation information on the long performance of the product in the environment, which is crucial information as immersed tunnels are generally built to last for 120 years.
IMMERSED TUBE TUNNELLING – PRINCIPLES
In essence, the immersed tube tunnel is built as a long assembly of watertight elements placed underwater on a prepared bed.
The basic principle of building an immersed tube tunnel is to construct the long elements offsite, such as at a drydock that is close to the project site or farther away, or somewhere else, said van den Brink. Sometimes, and rarely, the tunnel elements can be made on part of the alignment of the project route itself.
While the overall immersed tube tunnel is made by longitudinally connecting a series of long elements, such as concrete elements 100m-200m long, those elements themselves are usually made as a sandwich of shorter lengths – segments of the same cross-section, are joined together and have a waterstop rubber seal cast-in to help support watertightness and flexibility of the element when they are joined, or bonded, together. Flexibility of the tunnel element is needed during transportation at sea and during the tunnel’s lifetime when slow progressive ground movements induce forces onto the element. The segments are manufactured, or cast, individually, at the onshore facility.
Once the segments are together as a long element, bulkheads are installed at the ends of the assembly to make the structure watertight in preparation for flotation and being taken offshore. At the end, compression seals are also placed around the perimeter of the cross section at one end. The rubber seals fixed to the protruding edges of the element, just beyond the bulkheads, using steel end-frames and clamping systems.
The compression seals are called gina seal types and these are the primary seals of the immersion joint between connected long elements placed on the bed of a waterway.
To get there, the elements are floated out of their docks with pontoons and transported from sheltered waters, each to be sailed, slowly, to its nominated position along the alignment of the tunnel at the project site.
On site, each long element is submerged in turn such that, one by one, they add to the total length of immersed tube tunnel being progressively built on the bed of the waterway channel. The bed is prepared for the tunnel by dredging a specially shaped trench.
Each newly arrived element is carefully placed on the floor of the trench, on sand, immediately next to the previously placed element in the sequence. The next, vital step of the tunnel construction process is to use jacks to slowly pull the new section to be sealed against the elements already in place.
Along the edges of their cross sections, as noted, the long elements have initial gina compression seals. As the jacks pull the elements together, the gap closes between them and the rubber seal is spread more against their adjoining surfaces, so making their joint watertight.
The gina compression seals are already fitted on the end of the element already in place on the bed of the waterway. The sequence of fitting compression seals to an end of a long element is worked out onshore, during the fabrication steps. Each new element that is lowered into place, therefore, has ends with and without the fitted compressions seals.
Once the newly joined elements have been jacked together and compressed the rubber seal a few centimetres giving initial compression, their edges, by protruding beyond the bulkheads, will have created a space full of sea or river water. The space is dewatered which creates a hydrostatic pressure differential between this space and acting waterpressure outside the tunnel element. This pressure differential subsequently pushes the elements closer together, the gina seal is compressed to its nominal position to create a watertight connection and the adjacent bulkheads are removed. The far bulkhead at the end of the newly placed element remains in position, awaiting the next element to be lowered into place.
Meanwhile, within the open up space in the connected elements there are further seals to be installed, positioned immediately to the inside of the primary rubber seals. These extra seals are omega seals – a secondary seal immersion joint, said van den Brink. They are clamped into position, masking off the primary seals.
Eventually, with all elements in place across the bed of the waterway, the immersed tube tunnel has been constructed and with bulkheads removed it has a fully open throughway that is watertight.
Where the immersed tube tunnel ends and is connected to onshore tunnels, built by cut and cover construction, the watertight seals are called terminal joints. Those relatively short cut and cover tunnels lead up to open ramps and then to the surface.
Upon completion of the installation, the trench and immersed tube tunnel are backfilled and any armour protection needed placed on top.
The design life of the tunnel system is usually about 120 years. The performance of the rubber seals is key to the watertightness and success of such tunnel projects.
But why build one?
The question arises why build an immersed tube tunnel when there are many options in civil engineering to construct fixed crossings of waterways, noted van den Brink. There are multiple reasons physical and environmental/geological reasons why the option may be preferred in some cases, apart from the matter of the economics of the alternatives.
He said immersed tube tunnels are: suitable for short crossings; suitable for shallow crossings in soft soils; flexible in shape and dimension – so can economically accommodate multiple lanes and transport modes; they offer land reclamation opportunities, such as artificial land or islands in the surrounding area.
In terms of distance required for alternative projects to fit into the landscape, bored tunnels usually require longer distance overall and bridges even more, he said. The immersed tubes can be economically advantageous, therefore, in urbanised areas with water bodies to be crossed that have softer than usual soil.
Trends
What can be said over the years of development and construction of immersed tube tunnels?
A lot of trends are being recognised, said van den Brink.
The early immersed tube tunnels were across shorter waterways than today and so had fewer elements. The waterways were also shallower than those achievable later. So, a trend over the decades is for immersed tube tunnels able to be built longer and be comprised of more elements as sitting in slightly deeper water.
The Oresund immersed tube tunnel, linking Denmark and Sweden, was constructed in the late 1990s and it has 20 x 175m-long concrete elements, each 8.5m x 42m (H x W) in section. The tunnel was constructed in water of 22m depth.
By 2010, the Busan Geoje Tunnel, in South Korea, was constructed with 18 x 180m-long elements, each with 9.75m x 26.5m cross sections. The depth of water for the project is about 48m.
More recently, the Hong Kong-Zhuhai-Macau Bridge (HZMB) fixed link includes a 6.7km long immersed tube tunnel. The tunnel is formed of 33 elements and, uncommonly, involves pre-stressing the segments together in each.
In 2020, the Shenzhong tunnel, in China, was completed with 32 x 180m-long elements, each 10m by 50m in section. It was constructed in water of 36m depth.
But, since the talk was given to BTSYM/TAIym, by far the longest immersed tube tunnel in the world has got construction underway in earnest – the 17.6km-long Fehmarn road and rail project, linking Denmark and Germany (see box panel). Trelleborg is suppling seals.
In the talk, van den Brink said that, then, the total number of new immersed tube tunnels across the world grew steadily, exhibiting linear growth since the early 1960s to the late 2010s, increasing from about 20 to 150 projects about 2015.
There are different types of construction material used for the tunnels – steel (single shell, double shell, sandwich composite) and concrete (monolithic, segmental).
The monolithic concrete type has been dominant since the mid-1960s and entails more than 50% of all immersed tube tunnels, though is used mostly in Europe and some parts of Asia, depending on requirements and also the national infrastructure, such as use of concrete pours or steelwork in numerous shipyards, respectively. Monolithic concrete is much cheaper to construct that steel type for immersed tube tunnels, in general, added van den Brink.
Segmental concrete type started use in the 1970s and the numbers have fairly steadily grown, and steel sandwich composite is a more recent addition since the turn of the century. Use of steel, though, has barely increased since the early 1980s.
Geographically, the countries that have built most immersed tube tunnels include The Netherlands, US, Japan, China (including Hong Kong), Germany, France, the UK, Denmark and Sweden. The is a major expansion in use of these types of tunnels in Asia, especially China, he added.
RUBBER MATERIAL PROPERTIES
For the design of immersed tube tunnel projects, there are a lot of different environmental factors that can have dynamic and other influences on the joint design – such as forces and movements of different scale and period due to factors like seismic events, temperature change in the materials, any differential settlement under the loading of the waterway bed, and water pressure fluctuations as levels change with tides.
And, of course, there is the matter of age of the system and longer-term scale of the factors mentioned. All together, these cause various movements that require the design of the immersed tube tunnel to include a range of different tolerances at the joints, which must remain watertight. The movements can be accommodated by flexible materials, such as engineered rubber, said van den Brink.
Engineered rubber
The general ingredients in rubber are elastomer (40%), carbon black (40%), plasticiser (13%), anti-oxidants (2%), process aids (3%), sulphur (1%) and accelerators (1%).
Rubber is a unique compound that is an amorphous polymer in a vulcanised state – the molecules are interconnected. Through manufacture, then, when you see a seal it is one very large molecule with side chains.
Before manufacture into seals, the rubber usually arrives at the factory in stacked layers resting on transport pallets.
Rubber has a greater temperature range for engineering uses, due to the vulcanisation, compared to crystalline polymers (such as HDPE, PE and PP) and amorphous plastics (PVC, PS and LDPE) which soften at higher temperatures.
But, at the same time, rubber is a difficult material with some other characteristics that need to be taken into account when designing for watertight sealing purposes, said van den Brink.
Rubber is a non visco-elastic material, which means it is unpredictable in that its stretch-strain pattern are not set and so do not obey Hooke’s Law. Instead, the stress -strain patterns form a hysteresis loop – “energy is being dissipated within the material,” he said.
Further the ‘compression set’ of the material also has an effect, meaning, he said, if there is dynamic compression of the material the rubber does not resume all of its prior spatial dimensions. “This means the material behaves differently to what was originally anticipated,’ he added.
Additionally, there is also matter of relaxation of the material – when you have an initial compression of a seal the stress will lower over its lifetime.
Overall, though, rubber is a durable and reliable building and engineering material that can make the immersed tube tunnel “watertight for a very long time,” he said.
SEAL DESIGN
While the long elements of the immersed tube contain a number of joints within them, as noted those are waterstop (for segments joints) and gina and omega (for element joints) rubber seals.
Gina seal
As with the trends in immersed tube projects getting bigger, with larger cross sections and placed in deeper water, so too have the gina rubber seals got larger, said van den Brink.
The gina seal is designed for large hydrostatic pressures and large movement in xyz direction. It contains multiple types of rubber compounds, specially engineered to fit depths and relative stiffness for different local compression needs. It has low relaxation properties and low aging behaviour over the design lifetime to ensure minimum loss of reaction force over time. Trelleborg has more than 60 years of experience producing these types of seals.
The seals have to withstand up to 150 000kN of compression forces and be able to deal with movements, such as up to 100mm in transverse direction and +/- 60mm axial. The deepest immersed tubes are in range 20m-45m but the rubber seals are tested up to 9 bar. The design lifetime expectancy is 120 years.
Omega seal
These seals also started small and developed in size over the years, said van den Brink.
As secondary and final rubber seals for the immersion joint between long elements, the omega seals are connected to the adjacent elements. “They function as a membrane, basically, and cover up the joints,” he added.
They come in different types – standard omega, reversed, seismic, and both standard and large M-seal closure joints.
Again, they are designed to accommodate large axial movements and settlements. They have a strong and durable inlay materials for load distribution within the product, leaving the rubber layers to provide watertightness only. The product has been tested to 20 bar and higher.
Often the fixing bolts are pre-installed in the elements, leaving only the clamping of the omega seal to be done and deciding the force to be applied in doing so when tightening the bolts. After the initial fix, most of the time further tightening is required within 10-14 days as relaxation of the material is taken into account.
The omega seals also have design lifetime expectancy of 120 years.
Omega seal – Closure Joint
The omega closure joint is a special type of rubber seal that is not commonly seen. Such closure joints have to extend up to 1800mm to deal with tolerances, where the final gaps need to be accommodated and yet sealed as the last, usually shorter, element is placed on an immersed tube tunnel project.
Waterstop seals
These are cast-in to the structure during early manufacture, enabling them to be watertight seals of adjoining segments.
They are static tested up to 9 bar with a 90mm gap. Also tested dynamically at pressure over narrower gaps.
Where cast in concrete, the quality of the mix design and pour are vital. But should there be voids or hairline cracks in the concrete then resin injection can be used.
Given the long lifetime of the tunnel and considering how to handle the possibility of more cracks during the long period, Trelleborg is working to develop more injection possibilities, such as: fewer injection locations to save time and cost; and, flexible rather than static injection hoses.
FEHMARN IMMERSED TUBE TUNNEL
Fehmarn project is the world’s longest immersed tube tunnel and it is under construction with a dedicated giant precasting factory for its concrete elements.
At 17.6km long, the tunnel is being developed by Femern A/S and is designed to be large enough for bi-directional, separate road and rail traffic to pass between Denmark and Germany, and Scandinavian and European transport networks.
The tunnel will include 79 ‘standard’ elements, each 217m-long and 8.9m x 42.2m (H x W). These are enormous lengths compared to those built before.
The standard elements are formed from nine segments, each 24m long and large cast concrete structures in their own right. In addition, and unlike other immersed tube projects, Fehmarn is so long it needs to have 10 ‘special’ elements, sized slightly bigger to house equipment to operate and maintain the world beating length of tunnel. The specials are to be positioned at 1.8km intervals along the tunnel alignment.
Trelleborg is contracted to design and supply various sealing systems for the project. The seal design is not only limited to the immersion and segmental joints but also involves the sealing of the modular bulkhead panels that will be integrated within the project and seal design for the sliding drydock gate.
In order to bridge supply contingency, Trelleborg designated a third production location in Singapore, alongside with current production location in Qingdao, China. The scope is of the project is enormous which makes it the largest project to date for Trelleborg Ridderkerk B.V its design engineer Nicas van den Brink tells T&T.
QUESTIONS AND ANSWERS
Following the lecture, Nicas van den Brink and colleague
Joel van Stee, also a design engineer with Trelleborg, took questions from online attendees to the live event. Below is a report on the Q&A session, edited and abbreviated for clarity and space.
Q: How do the rubber seals deal with fire?
A: The seals are hidden, such as the omega seal placed in an indent in the structure or place a waterstop. Fire retardant plates cover them.
Q: How do you test vulcanised joints for integrity, especially if they are vulcanised on site?
A: The vulcanisation process has protocols to follow that require knowledgeable and experienced workers performing the works, including any on site. Further tests can also be done, such as for secondary sealing solutions with omega seals which, for example can be opened up and pressure applied between them and the gina seal to see how the welds are performing. So, it is a combination of steps – working principle, experience and validation.
Q: How do the seals deal with possible slight misalignment of elements during construction?
A: If a gina gasket is already installed for example, and where there may be a misalignment with pre-installed anchors, for example, sometimes you have to install the omega seal slightly offset from your nominal position to make sure it fits. These kinds of offsets are already allowed for in the omega seal design.
Q: How does the sealing system withstand corrosive environments, such as seawater?
A: The gina and omega seals need to be held in place with the use of steel, such as clamps. These types of materials can corrode over a certain length of time so need to look at choice of types of steel to minimise that problem, increase their thickness, take these types of corrosions into account as part of the design or take anti corrosive measures such as coatings and application of anodes. Rubber can handle the saline environments very well. Although if the environment has problems like hydrocarbons in the vicinity then polymer can be changed in the rubber product, such as a change from a natural rubber, which may then affect some mechanical properties that need to be allowed for by other means. Or a solution may be to have a combination of different rubbers as best.
Q: How is the rehabilitation of a rubber seal carried out at joints?
A: What can be done depends on whether it is for a primary or secondary seal. The risk of leakage must be minimised. If the gina seal needs repaired then you can vulcanise the rubber on site. Or you can add another, omega rubber seal over it, and in that case you need to make chemical anchors in the structure, unconnected to the original reinforcement. After chemical anchoring, the omega can be clamped into place. There is no standard way. It’s a challenge. A good inspection system is needed to know the root cause of any problems, such as whether the seal is leaking or there are cracks in the concrete, and then you can make a bespoke solution.
Q: What are mitigating measures if seals fail?
A: It is not that every leakage or failure is catastrophic, and there are also pumps in place in tunnels. Usually there are two seals in place, so if one fails you have another. But good design and regular inspection are key to help prevent these types of things from happening. For example, an omega seal in constructed with woven fabric inside so that if it fails it’d usually be a local failure that can be repaired. The degree of leakage is also a factor to consider in the degrees of what may be considered failure. Usually there are protocols in place, a fail tree with steps to be taken should different things happen. But often the bigger problems can be not those that are sudden but gradual and so an inspection system is really important.