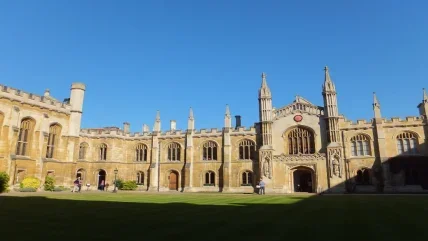
An overview of the pros and cons of the techniques Artificial Ground Freezing (AGF) was presented at the 10th International Symposium on Geotechnical Aspects of Underground Construction in Soft Ground, held in Cambridge, UK, in June this year.
AGF was not among the total of 14 papers submitted and accepted for the symposium’s session on ground improvement. However, Italian geotechnical consultant Vittorio Manassero, of Underground Consulting S.a.s, in acting as General Reporter to the session and also an expert in the area, gave a presentation on AGF to the gathering.
The symposium was organised by the Geotechnical Research Group of the University of Cambridge, under the auspices of the International Society for Soil Mechanics and Geotechnical Engineering’s (ISSMGE) Technical Committee TC204. It had been delayed and rescheduled by the covid pandemic. T&T attended the symposium and presentations on ground improvement, including the overview of AGF.
INTRODUCTION
With the topic of AGF not dealt with in the submitted papers to the symposium, Manassero presented a briefing on the technological process of using artificial freezing to control groundwater, the peculiarities of the method, its critical issues, and the advantages and disadvantages of its application compared to other methods of ground improvement.
Manassero said that, in general, AGF is a construction method of freezing groundwater in desired bulk shapes of soil for temporary ground improvement. He said it is possible to create frozen ground bodies of appropriate shape, thickness and mechanical characteristics to act as temporary soil support and, or, for waterproofing.
“Frozen ground behaves like a conglomerate where the binder function is accomplished by the frozen water – the ice – filling the soil voids,” he said.
Manassero added that the frozen body of ground “is impermeable and its mechanical characteristics are remarkably improved” compared to the ground in its natural state prior to a construction project. Further, he said the technology is applicable to any type of ground, provided there is a sufficient amount of water, or moisture, to be frozen.
EXTRACTING HEAT FROM SOIL
The primary scope of AGF is to extract heat from the water-bearing soil until its temperature drops below the freezing point of the groundwater system. This is the freezing phase of the operation and is achieved by installing a pipework arrangement that permits circulation of a cold medium to extract the heat from within the volume of ground to be frozen, said Manassero.
The system of freeze-pipes is installed with suitable spacing intervals around the perimeter of the body of soil that is to be improved by temporary freezing. During this phase, the circulation of the coolant fluid results in columns of frozen soil gradually starting to form around the freeze-pipes and gradually spread farther out.
The columns of frozen soil grow as the freezing process continues and they eventually merge into a continuous body that is “a resistant and impermeable retaining structure.”
The full frozen body will contain the intended excavation zone, such as for a tunnel. The zone to be excavated is unfrozen but encased by the surrounding impermeable shell of the ice body. Farther out, beyond the pipes, the frozen body will extend far enough to have effectively established as sufficient retained ground as required.
The required temperature of the frozen block is maintained during the entire excavation phase until after the permanent structures are built. The temperature is maintained by adjusting the flux of heat extraction from the soil. This is called the maintain phase.
FREEZE-LANCES
The pipes of the soil cooling system are called freezelances. A freeze-lance is made of two concentric pipes that are inserted into drilled boreholes, located specifically according to a design plan to achieve optimum freezing of a large block of wet soil.
The concentric pipe arrangement allows for coolant medium to be pumped in and to flow back out. The result of the fluid circulation is to extract heat from the local wet soil and cause the groundwater nearby to lower in temperature, gradually to progressively freeze farther away from the pipe.
The concentric pipe has an outer pipe with a closed end and inner pipe with an open end, stopping just short of the length of the outer pipe. Manassero said that, generally, the coolant fluid is pumped along the inner pipe to emerge at the open end and, stopped by the outer pipe, to flow back out, conveyed along the annulus between the concentric pipes.
FREEZING METHODS FOR CONSTRUCTION
There are three types of AGF available: 1) Indirect or Brine Method; 2) Direct or Liquid Nitrogen (LN) Method; and, a combination of the first two methods.
Indirect or Brine Method
The Indirect or Brine Method is a closed-circuit process that requires the use of an industrial refrigeration plant to cool the brine, which is usually calcium chloride (CaCl2) solution, said Manassero. Premixed coolant fluids are also available on the market and may be used as an alternative to brine, he added.
The refrigeration plant cools the brine down to -28°C to -35°C, typically. The brine is pumped into the freezelance pipework system that has been installed into the ground.
The brine is warmer on its return from the freezelances as it carries heat from the ground. The warmer fluid returns via an insulated surface manifold system. It is then re-cooled in the refrigeration plant and recirculated back to the pipework in the closed-circuit process.
Manassero notes that the Indirect or Brine Method relies on two points: the pumped circulation of large
Direct or Liquid Nitrogen (LN) Method
The Direct or Liquid Nitrogen (LN) Method is an open circuit process. The coolant medium is liquefied nitrogen at -196°C, the cryogenic medium manufactured offsite and delivered to be stored in vacuum-sealed storage tanks.
The method does not involve use of a refrigeration plant but pumps the LN via an insulated manifold system directly into the freeze-pipes. Passing through the freeze-pipes, the LN extracts heat from the ground and evaporates. The resultant gas is allowed to exhaust into the atmosphere, typically at a temperature ranging from -100°C to -60°C.
Manassero noted the points that Direct or LN Method rely on are: very high temperature differential between delivery and return; relatively low flow rates of coolant fluid; and, on the thermal energy provided by the evaporation of LN – about 60% of the total energy produced, he added.
He added that the Direct or LN Method is quicker than brine in achieving the desired frozen body of soil, is also more effective in possible adverse hydrogeological conditions, and it attains a higher strength on the frozen ground. However, the Direct or LN Method is generally more expensive than the Indirect or Brine Method.
Combined Method
A third construction method for AGF exists, consisting of a combination of the two methods described, said Manassero.
He said that the Direct or LN Method could be used in the freezing phase to rapidly build up the frozen body of soil, and then the Indirect or Brine Method can be used to the keep the soil temperature as desired during the maintain phase.
But, he added that the LN Method could be alternated with the Brine Method within the same ground freezing project.
Or, it may be that the LN Method is adopted for use in localised areas where the build-up of the frozen body using the Brine Method is likely to prove unsuccessful. Manassero said the LN Method is more powerful and less sensitive to possible adverse hydrogeological conditions.
APPLICATIONS AND CHOICE OF FREEZING METHOD
In underground construction, typical applications for AGF are for shafts and tunnelling below the water table. Manassero added that additional, minor, applications may also include underpinning, gap freezing, preservation of permafrost, temporarily frozen roadways, and more.
Still more applications may include local needs on larger tunnelling projects, such as for cross passages to join TBM-bored parallel main tunnels, or taking a section of metro tunnel below a river, or shallow underpasses to rail or highways. And more.
With respect to shafts, Manassero said that when freeze-pipes can reach an impenetrable cut-off stratum then only a circle of freeze-pipes enclosing the shaft layout area is usually required.
However, where no such stratum exists, at least at reasonable depth, then a bottom plug – in principle installed by a non AGF system – is required to help seal off the construction zone by working with the frozen surrounding wall of soil. Manassero said that using AGF to establish a frozen bottom plug would require installing freeze-pipes that would interfere with the subsequent excavation of the shaft. The approach would also lead to anticipate switch off and premature thawing, he said.
In tunnelling, for shallow tunnels the AGF system can be established from the surface where there is sufficient free space along the entire length of the tunnel and there are no obstacles created by buried structures, utilities or other obstructions over the distance. The possible use of an impermeable cut-off stratum for the AGF solution could see the freeze-pipes installed vertically or inclined, he added.
The angles of installation of freeze-pipes shift to horizontal, or almost so, where surface access is not feasible or the tunnel alignment is too deep underground for freezing of the construction zone to be undertaken practically and economically. In these deeper projects, the arrays of freeze-pipes are installed into boreholes drilled at almost flat angles.
Should AGF be required to help excavate between two tunnels, such as cross passages for twin road or rail tunnels, or other large voids, then drilling accuracy needs to be accounted for and, for distances of more than approximately 40m there may need to be directional drilling employed, said Manassero.
For such longer linking tunnels, or indeed for deeper main tunnels requiring extended use of AGF, an approach can be to undertake staged installation of freeze-pipes and associated ground freezing work.
The stages would be achieved by a ‘multiple horizon’ approach in which the freeze-pipes are not installed horizontally but in a more pronounced sub-horizontal fashion to establish fan-shaped arrays. The angles keep the prior pipes clear of the drill zones for the next stage of freeze-pipes to be installed.
However, care must be taken to ensure, at the end of each stage of AGF, there is adequate bulkhead and such can be established by various means and access, such as adjacent tunnels and voids, and choosing ground freezing or other methods.
Overall, it is clear that it is vitally important to ensure the ongoing integrity of the frozen body of soil and continuity between the areas from which it is formed, enabling the encapsulated space to remain stable and impermeable to permit safe working. Manassero, therefore, emphasised that highly accurate surveys of the actual arrangement of the network of freeze-pipes be undertaken, and a 3D as-built model constructed, so to identify potential zones of weaker ground freezing and any need for extra freeze-pipes to be installed. A check survey should follow to ensure the close of any gaps or “oversized windows” into the frozen block.
With a variety of factors to consider depending on the tunnelling project, Manassero further said the choice of ground freezing method to employ depends on assessment of a number of design, construction and financial factors, including:
- ground and groundwater condition
- speed of the groundwater seepage
- required design strength and stiffness of the frozen Ground
- planning
- duration of the maintain phase
- logistics
- safety
- costs
- and more
He added that from a design perspective, although geotechnical design is the main aspect of AGF it should be accompanied by a thermal analysis. The analysis would establish the temperature distribution, elapsed freezing time and thermal energy required to perform the work. There should also be a technological design.
Further, he said that the mechanical properties of the frozen ground depend on the nature of the soil (grain size, density, porosity, etc), its degree of saturation, temperature and time. While lower temperature brings higher mechanical properties, the longer the load time for the frozen body the more the risk of lessening the mechanical properties because of creep of the ice.
In terms of the perspective on construction needs, the AGF method needs highly capable engineering ability and a very skilled and experienced geotechnical contractor. In that regard, close regard to quality control and monitoring are vital factors to achieving a successful ground freezing job, he added.
MONITORING
Manassero stressed the importance of monitoring as a “crucial aspect” of safe use of AGF technology – monitoring of the soil temperature, the coolant fluid temperature, groundwater pressures and any displacements. He added that such monitoring should be performed by an automatic system for the reading, acquisition and recording of data, all of which should be shared in real-time with all key parties via a webplatform.
Soil Temperature Monitoring
A specific temperature monitoring network should be designed and installed in the soil near the freeze-pipes so to be within and around the volume of wet soil to be frozen.
The measurements should be undertaken using instrumentation fitted inside permanent casing pipe, placed in the purpose-drilled boreholes.
The boreholes should be surveyed too, which is important for the temperature data to be related to the freeze-pipe positions and so inform an accurate model of how the freezing operation is performing. This will also help ensure the integrity and continuity of the frozen body.
The instrumentation should be offsite assemblies of ‘temperature chains’, comprising gauges spaced at regular intervals, typically within 1m-3m, the gaps selected in relation to the overall length. The chains would be fitted to data loggers.
Coolant Fluid Monitoring
To monitor the cooling fluid, temperature gauges are installed at selected points of the freezing system, notably at the outlet and inlet of the refrigeration plants and in/out points of every freeze-pipe – or series of pipes, should they be arranged so.
Depending on the flow rate of the coolant fluid, the data from the gauges help to estimate temperature differences and establish the quantity of heat extracted from the soil by the arrays of freeze-pipes.
Water Pressure Monitoring
Monitoring water pressure within the closed and impermeable body of soil created by AGF is extremely important and is usually done by using one or more open pipe piezometers, installed in the core yet to be excavated. Each piezometer is fitted with a valve and pressure gauge.
The monitoring will show a rapid rise in water pressure when the body of wet soil eventually achieves its complete closure. It can also help to detect overpressures upon structures at the boundary of the frozen body of soil, which can be relieved by turning the piezometer valve to permit some drainage.
The valve drainage function can also be called upon to drain the unfrozen core prior to commencement of excavation.
Displacement Monitoring
When artificially freezing the ground, frost heave or horizontal displacement or frost pressure can be expected, said Manassero. The phenomenon is complex as ice has larger unit volume than water, thereby expanding the frozen soil compared to its unfrozen state, but both drainage and suction complicate the outcome – drainage in coarse soils away from the freezing zone; suction in fine soils bringing in extra water into the freezing zone. It can also be made worse should the soil heave be restrained by a building or other structure.
The risk of frost heave/horizontal displacements can be reduced by properly controlling the freezing process both during build-up and maintaining the frozen body of soil, said Manassero.
Then, after the freezing period, the thawing of the frozen soil may entail its weakening compared to its prior state, before the construction project. Deformation caused by thawing implies downward displacement, or settlement. The phenomenon has different possible components: volume reduction due to phase change; self-weight of the soil; de-structuration of the soil while it is being frozen; and more, said Manassero.
Manassero said compensation grouting can help counter the thaw-induced settlement.
SELECTION OF AGF – CRITICAL ISSUES
A few critical issues are important to be aware of when selecting the method of AGF for a construction project: groundwater seepage velocity hindering the formation of the frozen body of soil; and, holes or “windows” of weakness in the frozen body.
One of the most critical issues for the frozen soil build-up is the possible excessive speed of groundwater seepage, said Manassero. This arises should chilled water seep away from the intended freezing zone only to be replaced by relatively warmer water. The result is a risk of the frozen body not forming or it takes much more time and thermal energy to do so.
In general, he said, groundwater seepage velocities of up to 2m/day at brine temperatures and 20m/day at LN temperatures, respectively, are not significant enough to jeopardise the build-up of the frozen body.
Manassero added that interventions to accommodate greater velocities and so reduce the risk to frozen body build-up include: pre-grouting to reduce permeability; installing more freeze-pipes with either extra in the row at closer spacing or by installing further rows; chilling the cooling fluid to even lower temperatures; or, when Indirect or Brine Method is being performed during construction to switch to the Direct or LN Method.
The risk of a hole in the frozen body when an impermeable, sealed ice chamber is required below the water table is another critical issue, added Manassero. The risk is that the discontinuity lets seepage occur and the hole to widen, further risking the frozen body. Surveys and monitoring are therefore vital, in addition to experience and skilled designers and contractors.
In terms of pros and cons of AGF versus other methods of ground improvement, Manassero notes that no other method is so well monitored or as impermeable as AGF, and that the mechanical characteristics are better. But AGF has a higher anticipated cost. However, the gap in costs with other methods can end up smaller when extra rounds of grouting or jet grouting are called for on some projects. The statement that AGF costs more than any other soil improvement methods may be misleading due to its safe result, and both the anticipated time and cost generally are not supposed to increase during the construction works.
Additionally, and all that said, “finally we cannot overlook” that AGF sometimes is the only technical solution to pursue for solving particular technical and complex problems on a project, added Manassero.
ISSMGE’s proceedings from the symposium are due to be published soon as a 2nd edition, with eds Elshafie, Viggiani and Mair. From Routledge.