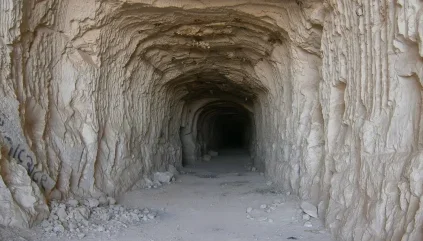
Tunnelling is an inherently dangerous undertaking. Human beings go deep underground, into narrow and confined spaces amid dust and damp where the geology and structure of the ground is never fully certain; they face the possibility of collapse, of fire, of flooding, of damage to their bodies from breathing compressed air; and, if a life threatening event does occur, the only way out may be several kilometres behind them.
That those dangers now result in remarkably few accidents or fatalities is the result of skill, expertise and care among engineers, tunnelling companies and miners themselves. It is also due in no small part to the efforts of men like Dr Donald Lamont, MBE, who has devoted much of his career to making tunnelling safer. In 2009 he was awarded the James Clark medal, the recognition by the profession of his efforts. The citation reads “For his long-standing service and dedication to tunnelling, the ITA, and the BTS.”
A Scotsman, he was born and brought up on the north-east coast between Aberdeen and Inverness; as with very many members of the profession he got into tunnelling by accident. There was no family history of engineering: “My father was a bank manager, my mother a teacher. I went to Aberdeen University to read civil engineering, then joined the Glasgow-based engineering consultants Babtie Shaw and Morton. Bridges and dams were some of their specialities. They were working on a big regional drainage scheme in south west Scotland and as part of it they appointed me Resident Engineer on a pumping station contract. The night before I went to take up the job the Regional Council cancelled the project.
“But three gravity sewer contracts were already underway; one of them had a 6-foot-diameter hand shield which had hit a very large boulder and was knocked offline. It was underneath a main road just to make things easier. I was sent up to oversee the recovery and reinstatement of the shield and so on.
“I was there for a while and then became Resident Engineer on another of the gravity sewer contracts. My predecessor there had virtually completed the job before going off to the Middle East; all that remained was a 50-metre gap across the car park of a retail warehouse. The warehouse was denying the local Council access to the land, even to tunnel underneath it, and the Council went to court. The court threw out the Council’s application and refused permission to go under the car park.
“So we had to go round it: we had to tunnel under a four-track railway embankment, then 50 metres down the other side and back under the railway to complete the sewer. And we had to grout because we were close to a river, we had to use compressed air because of the river, all these sorts of things just for that last 50 metres. And we completed the job.
“And, at the end of that project, I saw an advertisement for the Health and Safety Executive (HSE). It asked for people with experience of tunnelling, compressed air, excavations, earthworks, and piling, and I had done all of these, many of them around that car-park. So I duly applied.
“I had been with Babtie for twelve years and I felt it would be good to move elsewhere. And I’d had the odd visit on site from the Factory Inspectorate so I knew a little bit about the HSE. I went for the interview and got a letter back saying don’t call us and we won’t call you.
“Nine months later I was sent out to Nigeria for three postings over six months to do some work with Babtie. The night before I came home finally, I phoned my wife and she said, ‘Guess what, Health and Safety have actually just sent you an offer.’ This was the 1980s, there was a big cut back in civil engineering just then, jobs were definitely scarce and HSE and the civil service would be different and I hoped challenging. So that’s how I got into HSE.
“And, because I had some tunnelling experience and some compressed air experience, after a couple of years I was asked to take over as the national specialist in that work. For a period, I also had responsibility for HSE’s inland/inshore diving activity, which later proved useful in my work on hyperbaric tunnelling.”
It wasn’t quite going from poacher to gamekeeper, but was it a major change in outlook?
“Not at all, because all I was doing was enforcing a different form of specification. As a Resident Engineer you have a specification which is the contract you have to adhere to. As an HSE inspector you have a specification which is actually called the ‘Health and Safety at Work Act and various sets of Regulations’, and you have to adhere to that. It was the same sort of job, just in a slightly different framework. What I did miss was not being involved in one contract and actually being able to say ‘I helped to build this’, but otherwise I didn’t find a big change at all.
“It was still telling people how things should be done, but it was not confrontational. Things have changed greatly, and for the better, in tunnelling health and safety but it has been evolution, not revolution. The tunnelling industry realised it was the way to go, the right thing to do.
“In those days there was only a small number of tunnelling companies in the north-west of England so I used to find that we dealt with the same companies on a regular basis. You went to one contract and told them how they should be doing things, and on the next contract you found they were trying to do it and you explained how they should be doing it better, and on the third contract they had taken it on board and were doing it. There was willingness, there was cultural learning from previous experience, and they had got it right.
“So it was a cooperative effort. You worked with them and they were happy to take the advice and to learn from it and move forward.
“There is a public perception that tunnelling costs lives. A reporter rang me one day and said: ‘I understand that there is one fatality for every mile of tunnel dug, or for every kilometre. Can you tell me which it is, one per mile or one per kilometre?’ I told her that actually we hadn’t had any fatalities at all in the last couple of years. She put the phone down because there wasn’t a story in it from her perspective.
“People ask how many fatalities a year there are. What they should ask is how many years it has been between fatalities.
These days the number of fatalities in tunnelling, and the number of serious injuries, are actually very few and far between. The main concerns these days should be on health.
“Noise in tunnel construction is damaging to the body, and so is dust, particularly dust from spraying concrete and waterproof membrane and things like that. That’s where we need to improve. Hyperbaric tunnelling is another issue.” Here he is perhaps one of the better known specialists worldwide. “Tunnelling under low pressure and intermediate pressure is reasonably well understood, but high pressure tunnelling is still very much new technology. And the need for it is increasing. Tunnels are getting deeper. The shallow underground space is being largely used up. In places like Singapore with very extensive underground railway and utility systems, gradually new tunnels are having to go deeper and deeper to get a clear horizon. The same is true of Hong Kong, of London… As space is used up, people have to go deeper so the pressure is higher.
“The other contributing factor is that there is more demand for crossings under estuaries. There, tunnels have advantages over bridges. Bridge crossings have to allow for shipping and for the weather. With a tunnel you are out of the way of both. For things like the Lower Thames crossing that logic has obviously struck home. Hong Kong and Bangladesh have similar examples.
“So there is demand for road tunnels under water features and estuaries; and if you are doing a twin-bore road tunnel you are probably looking at a 15-metre diameter tunnel. Adding one diameter of ground cover gives you a total from invert to ground surface of about 30 metres. If you then have 10 or 20 metres of water above that, you are looking at around about four to five bars of pressure at the invert – and that takes you into the high pressure region for hyperbaric construction. BTS CAWG recommends three-and-a-half bar is the cut-off between intermediate and high pressure.
“From the medical point of view, at a pressure of around 3.5 bar breathing normal air becomes dangerous: the nitrogen in the air becomes toxic – narcotic in fact. It makes you become error prone, and then at higher pressures you become even more error prone until at about 9 or 10 or 12 bar, you die.
“Underwater divers are the only other group who regularly breath air under pressure. That community talks of the Martini rule: breathing air at one bar excess pressure has the same effect as drinking one Martini, two bars equates to two Martinis and so on. If you correlate that to alcohol consumption and national drink driving laws, then breathing air at about 3.5 bar equates to the drink driving limit in the UK.
No contractor who has a drink and drugs policy would allow you to drive a vehicle if your blood alcohol level exceeded the drink driving limit. So why should you be allowed to work in compressed air where you have the same level of narcosis?”
It gets worse: “Furthermore, your lungs have to work harder to shift that greater weight of gas; and they are not really built for that. When our distant ancestors emerged from the sea, about 350 million years ago, they evolved lungs that worked at atmospheric pressure, and it would take millions more years of evolution if we now wanted to change that.
“So when human lungs are faced with air at three-and-a-half times the normal density they rapidly tire and don’t expel so much at each breath. The result is that the air at the bottom of the lungs tends to remain there. So the gas which is changed most frequently is the gas in your nose and your windpipe – but the carbon dioxide that you generate is deeper in your lungs. So the last gas to be expelled is the carbon dioxide in your lungs and it is the first gas to be re-inhaled.
“All of which means that carbon dioxide is retained in your system; and high levels of CO2 lead to reduced levels of oxygen.
“The solution to the problem is to add helium to the breathing mix. Helium is very light gas and if you breathe helium rather than nitrogen then the mass of gas that you’re shifting is very much less, so it is less work for your lungs. Also, helium is not narcotic at the pressures we’re talking about, so you don’t have the narcotic effect either.
“But helium is expensive: You cannot afford to pressurise the cutter head of a TBM with helium. That is why tunnellers working in hyperbaric conditions use breathing apparatus – face masks connected by umbilicals to an oxygen, nitrogen, helium mix of gases.
“Of course, most research on breathing gases under pressure comes from the diving community: in particular from the Second World War, when the Navy wanted to find ways for divers to remain undetected, and later from the offshore oil industry, for whom the billions of dollars of potential revenue made a few millions spent on diving research look like small change. So tunnelling knowledge of breathing under pressure to a large extent is piggybacked on underwater diving experience.
Unfortunately, the two are very different, and the human body reacts differently to high-pressure exposure when it is in water than when it is on dry land (or in a tunnel).
“One reason is that in diving you are buoyant: your leg muscles don’t have much to do because you are floating in the water. In tunnelling you are standing in your legs, therefore the blood flows to the tissues in your legs and the work for the muscles in your legs is very much greater. That changes the balance of the blood in your body, which in turn affects decompression timings: when you are decompressing after tunnelling there is much more gas in your lower limbs than there would be in diving.
“The whole science of the health effects of hyperbaric tunnelling is neglected. Divers and tunnel workers are really the only people who will experience high pressure; diving has had lots of money to do research into the physiological problems involved; for tunnelling there is virtually no research money at all. Even on very large tunnelling project contractors’ profit margins are small and simply can’t provide for it. So there is lots of research still to be done. It will be a long time till the answers are discovered.
“The other big problem pertaining to health is dust. Silica causes silicosis; that is a well-known and studied disease and people have known about it for two or three centuries from masons and people doing stone dressing in dusty conditions. In most industries you are capturing the dust; but in tunnelling when you shotcrete you are actually spraying it out. The techniques and equipment for controlling dust exist but persuading industry to use them is a quite different situation.”
Another of his HSE roles was on the Channel Tunnel.
“I was involved in that as part of the HSE inspection of construction and then, once the tunnel was open, I represented HSE interests with the Channel Tunnel Safety Authority. So I was involved in how the tunnel is operated, and in inspecting the infrastructure, the tunnels, the buildings, the terminal sites – all the civil engineering building infrastructure as well as the ventilation and smoke control.
“Ventilation on the Tunnel is quite challenging because of the length of the tunnel, and because of the number of people at risk. If two passenger trains are in one of the tunnels you could have 750 people enveloped in smoke. The consequence could be potentially disastrous.
“Suppose a heavy goods vehicle shuttle were to go on fire. The philosophy is to blow the smoke back down the train, away from the locomotive and the drivers cab at the front; you’d blow the smoke away from that to allow them to escape. But the train behind, downwind of them will obviously then be in the path of the smoke being blown towards it. In that train the driver or train manager would walk from one end of the train to the other and reverse the train out.
“But at any one time there can be four or five trains in a single tube of the Tunnel and you can only reverse that second train if the one behind it, the third train, also reverses. You can get a situation where a number of trains have to reverse out for the first of them to get out of danger.
“There have been a number of minor fires in the Channel Tunnel, including two big incidents, in 1996 and 2008; all so far have originated in lorries carried on shuttles.
Fortunately, there have been no fatalities but the damage in both cases was quite severe and caused shutdowns for some months.
“In one or two places the concrete lining of the tunnel was completely destroyed, you were actually able to see the ground behind the lining. It was actually quite good ground, reasonably dry and stable. We always said that if we could choose a location to have a fire we would choose spots like those. But there are areas towards the French side where the ground is quite highly fissured and very wet.
“After one of those major fires they found a borehole in the tunnel that ran water. It was not a vast amount: like a 25mm hosepipe, and as you passed it you would taste the water. Over the course of the reconstruction, it became increasingly salty.”
Travellers through the tunnel perhaps happily for their peace of mind remain largely unaware of such things.
In 2010, Lamont left the HSE and set up his own consulting company, Hyperbaric and Tunnel Safety Ltd. It specialises, not surprisingly, in tunnel health and safety. There are, he says, plenty of people wanting advice.
“We have done work in New Zealand, Singapore, India, and Hong Kong; we have been consulted on Crossrail. At the moment, for the past two weeks, I’ve been doing legal work on injury compensation over an incident on an operational tunnel. I still do a lot of work on standards, especially in Europe, and I am active in the International Tunnelling Association.”
Tunnelling by its nature can never be totally free of risk; even so, today its safety record is a good one, of which the profession can be proud. That has been, and must remain, a joint effort and achievement between underground workers, contractors, designers – and people like Dr Donald Lamont who have devoted their careers to working out how to make tunnelling safer.