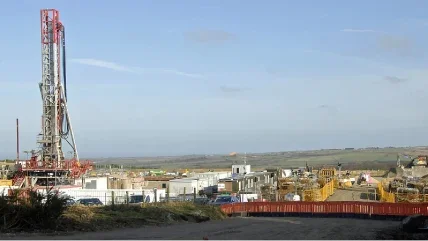
MUCH HAS BEEN WRITTEN OVER recent years about the Anglo American Woodsmith Project which will produce polyhalite to be used as fertiliser. A key element of the project will be the transport system to carry the mined polyhalite to the docks at Wilton.
At the joint British Tunnelling Society (BTS)/Minsouth meeting in February 2021, Craig Sewell (General Construction Manager) and Jason Fawcett (Tunnel Construction Manager) both of Strabag, described the ongoing tunnel construction.
OVERVIEW
Starting construction in 2017, the Woodsmith Project is the world’s largest known and highest grade polyhalite resource located near Whitby and Scarborough in Yorkshire, England, and 37km from the deep harbour facilities at Teesside (Figure 1).
Strabag was awarded the main contract for the Mineral Transport System (MTS) in March 2018 with the addition of the Lockwood Beck shaft sinking in June 2020. The scope of the tunnel project is as follows:
¦ 37.1km TBM tunnel drive
¦ 300m launch ramp and 100m
¦ On site production of the segmental lining
¦ 380m-deep intermediate shaft at Lockwood Beck
¦ TBM launch cavern construction at Woodsmith Mine
¦ Adit construction and SCL cavern enlargement at Lockwood Beck
¦ Tunnel fit out and permanent conveyor system installation.
WILTON SITE
The site contains the launch ramp, batching plant and TBM support, as well as segment production facilities and segment storage.
Goliath gantry cranes are used to supply segments to the tunnel transport system with the muck from the tunnel being transported to off-site facilities. Water is treated in ponds before discharge into the drainage system. Some of the tunnel arisings are being temporarily stored to help landscape the area when it is eventually used as a material handling facility for the polyhalite when it finally arrives at Wilton.
TBM DRIVES
The mineral transport system (MTS) tunnel follows the Redcar Mudstone lithology and crosses several fault zones with a maximum cover of 390m.
For the mine conveyor operation, a relatively straight tunnel drive is required with minimum 6,000m radius curves along the alignment.
TBM 1 – which is currently mining – will tunnel downhill at a maximum gradient of 3.5%, then approximately 15km uphill at 0.2%. Though it was originally planned for this TBM to tunnel to the Lockwood Beck shaft location, the progress has been so good that it will now continue beyond this location.
TBM 2 will be launched from a cavern at 360m depth, which will be constructed at Woodsmith Mine and will tunnel for approximately eight kilometres downhill at a gradient of 0.2%.
The tunnel cross-section has a bore diameter of 6m and internal diameter of 4.9m with a universal large key-type lining (six segments) 350mm-thick and 1500mm long. The lining is high strength with four ring types with varying rebar density up to 125kg/m and exposure class depending on the ground conditions which can be up to 29bar of hydrostatic pressure. The concrete grade is either C50/60 or C60/75. When completed, the tunnel cross-section will contain a high-capacity conveyor belt system with a 66kV power cable for the mine supplied from Teeside and fibre-optic communication cables.
The mine dewatering system will also run through the completed tunnel and a 900mm-gauge maintenance railway system will be installed.
LOCKWOOD BECK SHAFT AND ADIT
This will be 380m-deep with a 3.2m ID constructed by blind bore (Figure 2). A 20m long, 3m x 3m adit connection (currently under design) to the MTS tunnel will be built with a future SCL tunnel enlargement about 130m long to accommodate HV/LV equipment, heavy-duty conveyor equipment, double-track crossing, pumping station, water holding tanks as well as a refuge chamber.
The pre-grouting exercise for the blind-bore method is currently underway to stabilise the ground. A 25m-deep secant pile shaft will support the conductor casing installation and a 450mm pilot hole with Micon directional control to control the steering head for the future reaming operation. A steel casing fabricated off site will then be installed and welded on site in 42 scetions of 9m-long each, with thicknesses ranging from 15 to 30mm. The whole shaft will be drilled and then dewatered. The programme of works will span over a 12-month period and, as it is non-man entry, considered safer than other forms of conventional shaft sinking.
Pre-grouting works are ongoing with 29 holes totalling over 3,000m being drilled and grouted. The permanent casing manufacturing has commenced.
WOODSMITH MINE
Strabag will have access to Woodsmith Mine later in 2021 and its scope includes cavern construction at MTS level to support the TBM2 launch. The cavern design methodology is currently being developed with Arup undertaking the design works on behalf of Strabag.
TUNNEL DESIGN
The tunnel designer is Zentrale Technik, Tunnelbau of Stuttgart (Strabag inhouse designer). The lining uses conventional reinforcement due to the high stresses encountered. Bolts and dowels are being used on the radial and circumferential joints respectively.
GEOLOGY AND GEOTECHNICAL CONDITIONS
The investigations consisted of using existing data – which included old mine plans and shaft sections – and geophysical borehole surveys with 40 seismic traverses totalling 88.7km. A total of 24 boreholes were sunk to the MTS depth along the 36.6km drive.
The tunnel is bored almost entirely within the relatively uniform Redcar Mudstone Formation (ReM), however glacial till was encountered at the start of the drive with mixed-face conditions. Nodular ironstone beds with anticipated strengths of 200MPa contrast with the weaker mudstone (5-20MPa).
The TBM has passed beneath extensive old mine workings, where the primary concern was mine water and the presence of fault-driven methane gas ingress, but so far it has avoided any problems and kept a minimum 100m away from known mine workings.
Joint Geotechnical Review Meetings are held during tunnelling to evaluate zones looking forward with higher risks being outlined. Face mapping is undertaken as well as probe drilling ahead of the TBM. When a fault is traversed, it is followed up with dilatometer tests for insitu stress measurements by coring through the lining at axis and invert.
TBM FEATURES
The 6m diameter, 12m-long TBM was supplied by Herrenknecht with full-face rock excavation commencing in June 2019. There is a 225m long backup to support the TBM.
The machine comprises an open-face rock cutterhead with 34 No. 17” (430mm) discs and an eccentric cutterhead and conical shield with a slightly smaller middle section to provide overcut to reduce the risks from squeezing ground.
There is also good access to the cutterhead due to the large 3.6m-diameter main bearing and has a forward probe drilling capability of 150m.
A closable door is present on the muckchute to prevent an inrush of ground which, though not 100% watertight, would allow time to deal with the situation, though none have been encountered so far.
Health and safety features on the TBM include fire prevention and protection, as well as gas detection on the TBM and at 500m intervals in the tunnel. Handheld detectors are also used. A dedicated, fast manrider is available to access and evacuate crew from the TBM. Refuge chambers are also available.
Grout materials are pumped from the surface. As the drive proceeds, a total of five production trains, which can carry three rings-worth of segments, will be used. The locomotives are hybrid and exploit the gradient to recharge the batteries.
TUNNEL PROGRESS TO DATE
By October 2020, the TBM had advanced 10.5km having started its drive in June 2019 at the SCL launch adit; it has since reached the Lockwood Beck shaft location thus completing Drive
1. The best day’s production was 52.65m in 24 hours, and the best month was 1,019m of tunnel. This put the tunnel 138 days and 2.3km ahead of programme at the time of this presentation on 11 February 2021. Every week there is a planned maintenance day which has certainly paid dividends in terms of TBM reliability, with very little unplanned maintenance needed.
A dedicated rescue team is based full-time on site and has been developed in conjunction with a fully-qualified mines rescue officer to nationally-recognised mines rescue training standards. This is planned to remain in place for the mine operation.
SEGMENT PRODUCTION
Production commenced at Wilton in March 2019. A total of 24,221 rings were needed requiring 145,326 segments.
Initially, a single carousel was used to supply TBM1, with a second carousel featuring robotic technology commissioned in September 2020 to increase production ahead of TBM drives two and three.
The robotic technology employed on the segment manufacture includes:
¦ Fully automated ladder and mesh machine fabricating components from 5T coils delivered to site.
¦ Fully automated robots completing 230 spot welds following manual assembly of segment cages into bespoke jigs completed in less than ten minutes. (Figure 3)
¦ Automatic checking and cleaning of segment moulds.
At the time of this presentation (11 February 2021), over 9,500 rings (57,000 segments) were cast. There is storage availability on site for 1,800 rings.
Rapporteur: Andrew Hindmarch