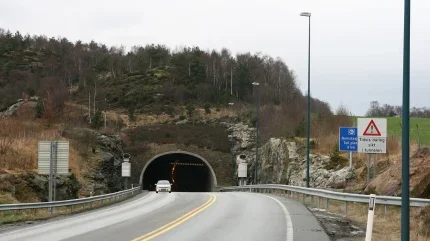
Norway is a remotely populated country with a coastline of some 57 000km, which, including islands and fjords, is greater than the circumference of the earth at the equator. The Norwegian government has made a commitment to the connection of these remote islands to facilitate the development of business. Many projects have been implemented over the past 20 to 30 years to connect islands with populations as small as a few hundred inhabitants. Many options have been considered for connections of islands and crossing of these straits, fjords, etc., including immersed tubes, rock tunnels, bridges, new ferries and submerged floating tunnels. The presentation concentrated solely on tunnels located in rock.
Over the past 30 years there have been 28 subsea road tunnels constructed in Norway through bedrock, representing a total length in excess of 100km. All of these are single-tube tunnels with cross sectional areas varying from 43 to 78m2. Depth below sea level is up to almost 300m. Table 1 provides a summary of some of the key statistics of some of these Norwegian tunnels. The first tunnel was Vardo which was opened in 1983 and is 2.6km in length. In addition eight subsea tunnels have been built for the oil industry as shore approaches and pipeline tunnels and another eight for water supply and sewerage.
All these tunnels are excavated entirely in bedrock by drilling and blasting. Throughout Scandinavia, general rock mass conditions are favourable for such methods. The geological setting is dominated by igneous rock types such as granite, together with metamorphic rocks of various types and origins such as gneiss, shale and in some places basalt. The host rock is intersected by weak zones, which may have an intense tectonic jointing, hydrothermal alteration or be faulted and sheared, constituting significant weaknesses in the rock and making the rock mass far from homogenous. These conditions may require rock strengthening measures.
The host rock in Scandinavia generally varies from poor or very poor to extremely good rock quality, according to the Q-system. The zones of weakness can exhibit great variation in quality, their Q-classification ranging from ‘extremely poor’ rock mass at the lower end of the scale, to ‘good’, with their width extending from only a few centimetres to tens of metres. The stand-up time of many of these zones may be limited to only a few hours. The great challenge in Norway, and in particular subsea tunnels, is dealing with these changing ground conditions and due to the location and depth of the tunnels having limited methods available that allow a detailed investigation of the rock mass to be undertaken prior to tunnelling.
Figure 1 details schematically the major features of subsea tunnels. The tunnels may have an incline and a decline of up to 8 per cent. Additionally there is a saline body of water that is a reservoir for water infiltration in the tunnel that, combined with exhaust fumes in operation, provides a very harsh environment for which all of the rock support needs to be designed for.
One of the most important parameters in the design of subsea tunnels in Norway is the depth of rock cover above the tunnel. The Norwegian public road organisation has specified that the cover should be a minimum of 50m unless you can prove and document that there are very good rock conditions along the route of the tunnel. Many of the tunnels in Norway are between 25 to 40m and the cover is generally detrmined on a risk-based approach relating to water ingress to the tunnel and piping to the sea.
Pre-investigations are undertaken in five stages and the aim is to build a geological model with sufficient confidence on which predictions for aspects such as cost, programme, rock support and grouting can be made. The stages are:
1. Initial stage that includes bathymetric surveys and geological references;
2. Feasibility study including desk study, geological surface mapping, acoustic survey and some refraction lines;
3. Detailed feasibility study that includes comprehensive refraction seismic and core drilling;
4. Detailed design using directional core drilling, detailed refraction lines for a particular route and tomography in particular areas;
5. Tender stage where a geological summary report is prepared on the geological model.
The main aim of the pre-investigations is to establish a geological model with sufficient confidence. The geological model shall form the basis on which predictions for time scheduling, cost assessments, tunnelling prognosis, rock support and grout estimates shall be made. Pre-investigations highlight the following elements:
• Cost effective methods aimed at determining the variability of the rock mass
• Critical areas call for specific investigations
• Probe-drilling ahead of the tunnel face acknowledged as a reliable investigation method while tunnelling.
To obtain information about features that are in the subsea part of the tunnel vertical holes can be drilled on the land sites. Refraction is generally used on the subsea section, however where this identifies concerns it is becoming increasingly common to undertake directional drilling along the proposed alignment. Directional drilling has been undertaken up to about 1000m long for Norwegian subsea tunnels to hit the actual area where more information is required. Notwithstanding this, based on the knowledge during pre-investigation and tunnel excavation, probing ahead of the tunnel face is generally undertaken on a systematic basis with two, three, six, or even more holes (if required) with a length of 30-35m ahead of the tunnel face to gain more information about the conditions ahead of the face.
The established practice of site investigations has proven to be reliable, but exceptions have occurred. In the Oslofjord tunnel, despite an extensive program of seismics, directional core-drilling, hole-to-bottom seismics and seismic tomographic interpretations, the glacial erosion along a known depression along the bottom of the fjord proved to be much deeper than interpreted, and left the tunnel without rock cover over a short section. This was detected by probe drilling during construction; a by-pass tunnel was prepared to allow continued tunnelling under the fjord. The soil filled section was frozen (at 120m water pressure, or 13 bar) and excavated through. Figure 2 demonstrates that if the directional drill hole had been placed above the tunnel alignment, not within the cross section and below, the eroded channel could have been avoided by lowering the alignment of the tunnel.
A similar situation was close to occurring at the Bomlafjord tunnel. A 900m long directional core hole towards a low point in the bedrock (not the deepest) hit moraine where rock was expected. This was checked by further directional core drilling and the tunnel alignment was adjusted (from a 7.0 to an 8.5 per cent Slope) to pass in the bedrock below the moraine deposit. This resulted in the tunnel alignment being lowered by approximately 30m thus saving costly remedial measures in the form of ground freezing and a by-pass tunnel.
Excavation and rock support
All subsea tunnels in Norway have been excavated by drill and blast. This method provides great flexibility and adaptability to varying rock mass conditions and is cost effective. The most difficult rock mass conditions often occur in fault zones along the deepest parts of the fjord where any uncontrolled major water inflow will have severe consequences.
The systematic percussive probe drilling by the drilling jumbo is the single most important element for safety, and a limit of 30 litres per minute per 100m length of tunnel for water inflow is generally set for all subsea tunnels in Norway. The water is collected at the low point and pumped to the surface for discharge. All rock support structures are drained, whether they are made of sprayed concrete (prime support measure), sprayed concrete ribs or in the worst case, cast-in-place concrete (mostly horseshoe) lining. Sprayed concrete is dominantly applied as wet mix and is steel-fibre reinforced. The use of sprayed concrete has been increasing gradually to about 1.5-2m3 of sprayed concrete per metre of tunnel. Traditional methods such as mechanical and hand scaling and rockbolting are still in use and the number of rockbolts is in the range of three to six per metre of tunnel. Various types of inner lining are often used, with the main purpose to prevent water entering the traffic areas (including frost protection), rather than providing structural support for the tunnel.
One of the most significant differences between the design of road tunnels in Norway and the UK is the tunnel classification system. In Norway, the design uses the NPRA Handbook 021 where the tunnel relates to the annual and daily traffic flow in the tunnel irrespective of the tunnel length.
However in the UK, BD78/99 (Design of Tunnels standard) also references the length of the tunnel. This means that for tunnels in excess of 2km in the UK, the volume of traffic is not a consideration in the size of the tunnel. In Norway however, where tunnels are used to connect remote islands producing small traffic density (often with an annual average daily traffic of under1000 vehicles) it is important that the traffic flows are considered when the viability of constructing these tunnels is in question.
Risk and contractual practice
Tunnelling and underground works are inevitably associated with a certain amount of risk taking. No matter the extent of the pre-investigations, a certain level of risk remains. Identification of risk and risk allocation is important. Norwegian tunnelling involves standard unit rate contracts with risk allocation and contractual handling as follows in an ideal risk sharing model:
• The Owner carries the risk for the rock mass conditions as they occur,
• The Contractor carries the risk for the appropriate and efficient handling of the works and focus on improving his technical and organisational performance,
• The Owner is responsible for the collection of information on ground conditions. All information is disclosed to the tendering contractors for their own interpretation.
• The Owner’s engineers provide their interpretation of the situation in terms of presenting their estimate on quantities on rock support, rock mass grouting etc and all expected measures are quantified in the tenders and contracts.
• The contracts include regulations for extension of construction time based on actually performed quantities.
If these unforeseen or unexpected conditions occur it would be the owner who is the risk holder, no matter the type of contract used.
Operational aspects
Operation and maintenance of the tunnels is a very topical issue in Norway. Based on a review of information from some Norwegian subsea tunnels at 2010 costs, it is estimated that maintenance of the tunnels is approximately an average of EUR100 (USD140) per metre.
Typically lightweight installations such as lights and fire extinguishers have, in such corrosive environments, a design life of 10-15 years. Experience of the tunnels has also shown that over time the water inflow reduces indicating there is a tendency towards the rock mass self tightening itself.
A study of the accidents that occurred in road tunnels was undertaken in 1997. We have started to divide these tunnels into different zones. What we see is that we have most of the accidents just outside of the portal. We then have accidents following in the next 50m, while in the mid part of the tunnels we have the lowest number of accidents. This could be the fact that, because you are driving in daylight, for example, you are entering a very dark area or you are coming from a dark area and entering daylight.
Questions from the floor
Richard Brown
Q: Are there any provisions for cyclists or pedestrians for the typical tunnels in Norway?
A: No allowance is made for pedestrians or cyclists and they are generally banned from the tunnels. It could be done but would require separation from the traffic area and a lot more ventilation and illumination.
ColinMcKenzie – Retired
Q: Coming from a remote Island community in the Outer Hebrides of Scotland, what is the smallest population that you have connected with a tunnel? Secondly, when deciding the size of the tunnel is there a standard cross section?
A: The tunnel with the lowest annual average daily traffic is 300 vehicles. I think the population then would be probably less than 1000. There are standard cross sections and normally the smallest one has a width of 8.5m, which is quite typical for remote tunnels. To reduce the cross section further there has been some discussion on a single lane tunnel of say 5m width however this would require sophisticated control systems.
Neville Harrison – Retired
Q: How are these tunnels financed?
A: The majority of these projects are funded by the Government and toll payment.
Martin Knights – Halcrow
Q: There is an 8 per cent gradient in the tunnels. Are there psychological problems in dealing with such a steep gradient in tunnels like that for the public and does this increases the accident statistics?
A: In Norway people are more accustomed to driving in road tunnels but of course accidents where vehicles drive into the rear of others are frequent. However, when it comes to the overall picture as far as accidents are concerned, the tunnel accident statistics are similar to open roads.
Tony Rock –MacMcDonald
Q: My question follows on from Martin’s and it’s to do with the gradient. Now the length of your tunnels and the steepness of the gradient must pose a very big challenge for ventilation in the case of a fire, do you have any comment please?
A: The main dimensional criteria of the ventilation fans is related to smoke and pushing smoke out of the tunnel up against a steep gradient. There is a preferred ventilation direction because all emergency cars/vehicles would preferably arrive the scene from one side. The ventilation system requires a minimum speed of air flow which is 2m per second. In the EU regulations there is a leeway on the gradient as 5 per cent is the maximum, unless geographical or topographical conditions restrict this, which is why in Norway the gradients are increased for subsea tunnels.
Rapporteur DamianMcGirr
Typical Norway road tunnel in rock Table 1: Subsea road tunnels Figure 1: Major challenges facing a typical fjord crossing tunnel construction project Figure 2: In construction of the Oslojord tunnel, the filled erosion channel was much deeper than expected as detected by probe drilling, necessitating a bypass tunnel Figures 3 and 4: A similar situaton in the Bomlafordtunnel project was detected and avoided by lowering the alignment by 30m Face instability of the Atlanterhavstunnelen (2006-2009) at the deepest point delayed the project by a year and necessitated a concrete plug, extensive pregrouting and other major support measures; Figure 5: The eroded channel at the deepest point of the Oslofjord tunnel showing position of borehole surveys through fault zone