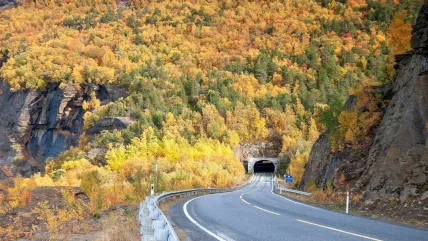
Anne Kathrine Kalager (Follo Line TBM project manager, Bane Nor) and Professor Eivind Grøv (chief scientist, SINTEF) both of the Norwegian Tunnelling Society, gave an insightful presentation at the 16 January 2020 meeting of the British Tunnelling Society (BTS).
Norwegian Tunnelling Society
Anne Kathrine Kalager began the meeting by describing the role of the Norwegian Tunnelling Society which, like the BTS, provides a knowledge-sharing arena based on the know-how, enthusiasm and commitment of its members. Currently, the NFF’s main focus areas are to:
- Strengthen health and safety, and reduce environmental impact;
- Promote sustainable exploitation of the bedrock;
- Contribute to innovation in the industry;
- Recruit, educate and develop professionals, and
- Strengthen knowledge sharing and cooperation nationally and internationally.
Work in progress by the society includes guidance on the use of explosives, rockbolts and shotcrete, as well as digitalisation. Plans for future work include costs and productivity in tunnelling, environmental accounting systems (such as CEEQUAL), reduction of plastic use, tunnel spoil as a resource, and a handbook for clients of drill and blast tunnels.
Under Oslo – The Geological Context
The presentation on upcoming projects in Oslo first described the geological context followed by individual projects. Oslo’s geology is mainly hard rock, consisting of a Precambrian crystalline basement (gneisses, granites and amphibolites), Cambrian and Silurian sedimentary rocks (limestone, sandstone, siltstone, hornfels, shales), and intrusive rocks and dykes (syenites, porphyry, basalt, diabase).
Generally, the rock mass is homogeneous and competent, with little to moderate jointing. it is also impermeable, with single fractures or groups of fractures acting as drainage channels. During glacial periods, the rock was eroded, particularly at fracture groups or zones of weakness. These ‘valleys’ eroded by the glaciers have since been filled with thick layers of marine clay, which may be sensitive to settlement.
A tunnel intercepting a fracture zone can cause the water table to draw-down by a significant distance from the tunnel. This could cause environmental problems or settlement, particularly where buildings are constructed on thick, superficial layers of soft marine clay. It is therefore important to decide whether the tunnel should be drained or undrained. If it is drained, then the designer needs to decide how much leakage can be allowed and how this will affect first, the water table and second, any potential settlement. It may be possible to deploy systematic pre-excavation grouting in a drill-and-blast tunnel to reduce inflows to an acceptable level (see Figure 1) If a TBM is used with a watertight segmental lining, then backfill grouting, along with some pre-excavation grouting from the front of the TBM, may be sufficient .
More Hazards
Another geotechnical hazard in Norway is ‘quick clay’ – marine clay with an open structure held stable by salt. If the salt is washed out of the clay then the clay becomes unstable, like a house of cards. If the clay is then disturbed, its structure can collapse and it can become fluid. These landslides can occur at very shallow slope angles.
Many quick-clay slides have occurred in Norway:
- The largest was at the Verdals-slide in 1893 where 55 million m3 of clay were transformed to a liquid ‘soup’ causing the loss of 116 lives;
- The Bekkelags-slide in 1953 destroyed a section of the Østfold-line and 100m of the Mosseveien. Five people died.
- The Rissa-slide in 1978. Six million m3 of clay within an area of 330,000m2 was liquidised, causing a fatality and the destruction of more than 20 buildings. The slide created a 3m-high tidal wave in the nearby lake.
More information on quick clay slides can be found at https:// www.ngi.no/eng/Services/Technical-expertise/Landslides/Quickclay- slides-in-Norway.
Beneath Oslo – Future Projects
New constructions under Oslo include railway tunnels, a metro line connecting existing metro lines and the Fornebu Line, and water supply and cable tunnels. The Fornebu Line is a new, 8km-long metro line from Majorstuen to Fornebu; 6.6km is tunnelled and it includes a total of six new underground stations.
The tunnels on these new projects will be constructed using either drill and blast or hard-rock TBM. Although the use of TBMs has been rare in Norway, four hard-rock Herrenknecht TBMs equipped to allow pre-grouting were recently used successfully on the Follo Line.
Oslo generally has many existing underground structures, such as tunnels and caverns for storage of petroleum products; road, rail and metro tunnels, and many geothermal energy wells.
Underwater Tunnels
During the second half of the meeting, Professor Eivind Grøv discussed tunnels under fjords and under the sea, including some ‘blue-sky’ thinking about future uses of tunnelling for Hyperloop or for connecting to subsea oil fields. Several disclaimers were set down at the start – some of these uses or projects may have no merit, some are initial ideas or theoretical concepts and require much more study, and some ideas may test the limits of application of TBMs beyond what is currently feasible.
The Rogfast Project
Located on the E39 motorway between Stavanger and Haugesund on Norway’s west coast, the 26.7km Rogfast project will be the world’s longest subsea road tunnel. Forming the final link in the west coast motorway, it will have twin bores with two traffic lanes in each and enable road users to bypass the ferry. With the deepest point below sea level at 390m, it has a 4km-long turn-off ramp up to Kvitsøy (an intermediate island) with a 7% gradient. Recent estimates put the cost at around NOK20bn (€1.78bn). A schematic of the turn-off ramp at Kvitsøy is shown in Figure 3
The geological risks include:
- Up to 390m head of water;
- Several weakness zones both south and north of Kvitsøy, up to 60m wide;
- Some zones expected to have Q-values below 0.003;
- Around 40% of tunnel length is in phyllite, greenstone and slate, considered favourable rock types;
- Grouting is expected in (meta)gabbro and gneiss, around 40% of tunnel length;
- Variation in rock-mass quality may occur over short distances;
- 83 zones of poor rock-mass quality (Q < 1), making up 10% of tunnel length;
- Swelling clay expected in weakness zones;
- May have low in-situ stress levels causing a risk of major leakage, and
- Regional faults where the distal part may be water-bearing.
The current plan is to use traditional Norwegian drill-and-blast tunnelling. Rock cover would be a minimum 50m, with probe drilling ahead of the face, pre-excavation grouting, rockbolts and sprayed concrete support, with a freestanding inner lining.
TBMs could be used for the Rogfast tunnel. They would need to be either a mixshield (slurry) TBM or a dual-mode EPB/single- or double-shield TBM. The ability to undertake pre-excavation grouting and probe drilling would be mandatory. The TBMs would need to be capable of switching modes during boring to cope with changes from good, hard rock to a weak and unstable water-bearing rock mass, installing a segmental lining in weakness zones, and using rockbolts and shotcrete in good ground conditions.
Different numbers of TBMs were assessed, as well as using a ‘double deck’ arrangement in a single bore. Using more TBMs is better for flexibility and for the overall programme, but less good for construction logistics. Using fewer TBMs reduces TBM cost and is better for logistics, but not so good for the overall programme.
The conclusions of the study were:
- Using TBMs is feasible for the Rogfast tunnel project;
- Cost per metre is 20-35% higher than drill and blast;
- Construction time is approximately 1.6 years shorter than for drill and blast;
- TBMs involve lower construction risk than drill and blast;
- A dual-mode TBM with double shield and EPB-capacity can provide increased precaution and redundancy in adverse ground conditions;
- TBM technology requires further development to provide robust solutions for the project, such as the 390m water head, and
- The geological conditions are complex and the final choice of machine type may be evaluated following supplementary investigations.
Tunnels to Oilfields
Professor Grøv also presented a novel use of tunnelling – the concept of using TBM-bored tunnels to connect subsea oilfields to the mainland to better meet environmental constraints. A case was selected for investigation near the Lofoten Islands – a prospect 30km offshore at 150m sea depth. Around two thirds to three quarters of the tunnel is to be excavated in “moderate to poorly consolidated shale, mudstone, siltstone and sandstone” mainly of late Cretaceous age.
The challenges for TBM use are:
- Very weak and unstable rock mass including running ground, swelling rocks etc;
- Stress-related problems such as squeezing;
- Large water inflow potential with up to 250m head, requiring pre-excavation grouting;
- Gas pockets/shallow gas, and
- Mixed face conditions.
Simultaneous boring of three parallel headings is needed to reach high performance. Two tunnels are needed for rail transport of personnel and equipment, and one tunnel for hydrocarbon pipelines. At the end is an exploration cavern, from where drilling for oil can be undertaken.
The TBM would be a 6.6m-diameter double-shield hard rock machine and custom designed to tackle the challenges listed above. The study concluded that, in terms of time and cost, a tunnel solution is a realistic alternative to conventional methods in coastal areas located around 50km from the shore. The risk level for personnel is acceptable and probably lower than conventional solutions. However, the key cost and schedule uncertainties are essentially rock quality, the length of the tunnel and TBM performance.
The Stad Ship Tunnel
The Stadhavet is the most exposed, most dangerous area along the coast of Norway. Construction of the Stad Ship Tunnel will give ships a short cut to avoid going around the Stad Peninsula. Since the first studies began around 15 years ago, the Norwegian Parliament’s 2022-2033 National Transport Plan has earmarked NOK 2.7bn (€240m) for this project.
Much media coverage globally was generated by the project when announced. However, a ship tunnel is not a new idea: in the 17th century, the 160m Malpas Tunnel was built in France.
The Stad, at 47m high, includes a 12m depth of water, is 36m wide (Figure 5) and larger than most canal tunnels. When it is finally completed, it will be the world’s first full-scale ship tunnel of this size.
Constructed using drill and blast, the 1,700m-long tunnel and 1,661m2 cross-sectional area will give an excavation volume of around three million cubic metres or eight million tonnes of blasted rock. It will take three to four years to build.
Currently, horizontal directional core drilling has been undertaken from both portals, covering about 50% of the tunnel length. The rock is banded gneiss with augen gneiss and mica gneiss with a schistosity dipping at 45°. Around 40- 50% of the rock is expected to have a Q > 40 (Very good), 50-60% expected 10 < Q < 40 (Good) and a marginal amount where Q < 10. The major horizontal stress is 7.3MPa perpendicular to the tunnel axis and 4.5MPa parallel to it.
Although the tunnel is not necessarily a complicated undertaking, the contractor who can best master the logistics will be the winner.
Subsea Tunnel for Hyperloop
A plan for a Hyperloop between Stockholm and Helsinki could reduce travel time to 28 minutes. This would require a subsea tunnel 170km long from coast to coast. The biggest challenge is how to deal with emergency situations and evacuation. Allan Sharp and Gareth Mainwaring came up with an idea to use oil platforms as intermediate shafts to aid construction.
Questions from the floor
David Fawcett, independent consultant: Was the type of contract used on the Follo Line satisfactory?
Anne Kathrine Kalager: EPC contract for excavation was used instead of traditional unit price. They are also using EPC for two new tunnel contracts. This is the TK type of EPC contract, often used in oil and gas. Claims must be resolved in a limited time, e.g. six months, rather than waiting until the end of the job. This works well, solving problems when they occur. Unexpected (e.g. ground) conditions are paid for by the client. For complex projects, unit price may be better.
Alun Thomas, All2Plan Consulting: With EPC contracts, do contractors have the opportunity to suggest alternative designs?
Anne Kathrine Kalager: On two new EPC contracts, the negotiation period has allowed contractors to propose alternative methods. On the Follo Line, the contractor proposed changes after signing the contract, so variation orders were used.
Kristina Smith, tunnel journalist: If drill and blast is so perfect for Norwegian rock, why are you so keen on TBMs?
Professor Eivind Grøv: We have a toolbox and a TBM provides us with another tool. In some cases, it might be the best tool. All projects are unique.
Anne Kathrine Kalager: In the early stages of the Follo Line we studied excavation methods. To complete all the excavation in 3-4 years we would have need 6-7 access points in urban areas for drill and blast. With TBMs we could have one site and one access point where there was space and fewer residents.
Andy Flowerday, Barhale: Do you have many tunnels in quick clay? How are they approached?
Anne Kathrine Kalager: In Oslo, yes, we have tunnels in and near quick clay, but we use cut and cover, not TBMs yet. We think in future we will be able to use TBMs, perhaps with ground improvement from the surface beforehand.