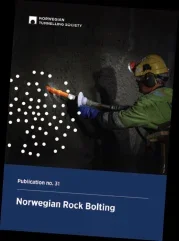
Rock stabilisation choices are largely based on assessments made as excavations proceed in Norwegian tunnelling practice, it is noted at the beginning of the country’s recently published substantial handbook on rock bolting. Therefore, having highly effective practical knowledge of the bolting systems and their practical application are points of particular importance in the field for Norwegian tunnellers.
These areas are discussed in the 90-page guide – ‘Norwegian Rock Bolting’ – from the Norwegian Tunnelling Society (NFF). The handbook is focused on six large chapters (Use; Types; Equipment & Installation; Dimensioning; Control; and, Documentation) plus one page of references. By far the largest chapter is on ‘Bolt Types’, followed by ‘Uses’ and ‘Equipment & Installation’, respectively. Not quite as long a chapter but of importance is Documentation (See box panel).
The report is presented in a highly structured format and is very well illustrated with graphics and tables. It is a most accessible work.
ORIGINS
NFF has been looking after the rock bolting practical handbook information since 2017, the origins of the publication going back to the early 1970s upon which the national roads administration (Statens Vegvesen, or NPRA) based its own related Norwegian-language publications and then made an extensive revision and update.
NPRA, a client organisation that has built many road tunnels by drill & blast throughout Norway over decades, then handed over the process to the national tunnelling society.
The widely experienced membership of NFF (clients, contractors, consultants, manufacturers, suppliers, and more) have contributed to the further development of the handbook. In wanting to share the knowledge with the international tunnelling community, NFF also translated the revised handbook to English and the information is free to download.
KEY POINTS
As noted in the Introduction to the handbook, there are many types of bolts for rock reinforcement but not every bolt directly stabilises excavated rock – such as assembly bolts and others, the function of which and their pinpointed locations are important to the performance of the final constructed tunnel structure (including lining, membranes, technical installations, etc). That difference noted, they are note discussed further for the focus is on using bolts for stabilising rock excavations.
While bolts can be used with other rock stabilisation methods (bands, mesh and shotcrete, and more) they “are the most widely used… under most rock conditions.” Given the variety of geology and rock quality, and tunnel sizes, and the resulting challenges in tunnelling by drill & blast method, “bolts have different designs and behaviours, which are utilised to stabilise rock masses of very different character.”
The handbook noted that bolts are generally easy to install in their pre-drilled holes, that go far enough to reach competent rock at the ends. They can take up relatively high loads, can be end-anchored and pre-tensioned, or embedded ion and act as rock reinforcement. They can also be used in caverns “of almost any geometry.”
The aim is for rock, as far as possible, to be selfsupporting. Bolts and other stabilisation methods are used with that aim in mind, and noting that some project locations may have geologies where there are “substantial stresses present in the rock” and this add to the challenge of stabilisation, and seeking the excavation to be self-supporting – therefore comes the help of the additional measures. In addition to whether there is high or not so much inherent local stress in rock, another challenge is groundwater, presenting challenges for grouting and anchoring bolts, and potential to affect their service life.
“The use of bolts is therefore largely based around choosing bolts that satisfy requirements for a long service life, and such bolts are grouted where there are no rock pressure problems,” says the handbook.
BOLTS – USE
In discussing uses, the handbook begins with notes on two categories – instant and permanent stabilisation, respectively.
For instant stabilisation, two types of fast-acting bolts that provide protection during tunnelling are mainly used: combination bolts with expansion sleeves; endanchored bolts with polyester cartridges. They can be pre-tensioned and provide active pressure in the rock mass, pressing together fractures and causing friction to help strengthen and stabilise the rock.
For permanent stabilisation, there are fully embedded bolts used, either pre-tensioned combination type or not pre-tensioned (activating as rock deforms), based on lifetime considerations. Glued end-anchored bolts can be used where there are high rock stresses.
In terms of uses, there are four categories of rock bolt installation described in the handbook: spot bolting; systematic bolting; spiling; and, bolting in front of the face.
Spot bolting – no fixed pattern of placement, the choice being made of need and location depends on judging local stability needs, if extra support is necessary. The method is often used in coarse-blocked to moderately fractured rock. Use of dowels (embedded rebar) is a form of spot bolting although they primarily act obliquely.
Systematic bolting – bolt installation to specific patterns. This approach is normally used, the handbook says, “in difficult rock conditions and/or heavily to moderately fractured rock.” It is most often used in combination with, and after, application of shotcrete to the excavated rock.
Spiling – aimed to preserve the profile of rock after blasting, and to avoid collapse, this method is employed in particularly poor rock (weakness zones), and also where the ground surface is relatively near, such as where cover is shallow or near portals. The bolts are inserted into the rock in tightly packed arrays over and ahead of the excavation face, and around the profile as may be needed. They are typically embedded rebar with lengths up to twice that of blast rounds. The method should hold profiles until further stabilisation measures are added, such as reinforced sprayed concrete arches, shotcrete, and radial bolts.
The handbook goes on to discuss the installation methods further and also, in detail, the different types of bolts and their recommended applications for different situations. Tables to support choices are provided. As noted at the outside of the report, though – while prepared by professionals appointed by NFF, “It is assumed that the handbook will be used by competent, skilled persons with an understanding of the limitations and assumptions that apply.”
BOLTS – TYPES
As noted, much space in the handbook is given over to the discussion of the types of bolts, and also to some degree on the equipment employed for their installation. Two large chapters, totalling 43-pages or effectively half of the report, cover the areas.
On bolt types, the report covers the following:
- End-anchored bolts – with expansion sleeve anchor; polyester anchoring; and, grout anchoring
- Fully embedded bolts – grouted rebar; perfobolts; and, polyester anchored
- Combination bolts – pipe bolts; end-anchored and post-grouted bolts; CT-bolts; NC bolts; and, Fin-bolts
- Others – friction (Split Set, Swellex); fibreglass; and, D bolts
- Cables and anchors – threadbars; self-drilling anchors; multiple wire anchors (prestressed cables); and, wire cables (unpretensioned cable bolts)
- Materials & accessories – plates and hemispheres; expansion sleeves; polyester; and, grout
- Corrosion protection – hot-dip galvanisation (alone, or with epoxy resin); stainless steel; and, fully embedded bolts Each bolt type is presented and discussed in mostly dedicated pages that includes an image graphic, tables, and text covering four topics – Area of Use; Installation; Advantages; and, Disadvantages.
EQUIPMENT AND INSTALLATION
With bolts intended for rock stabilisation during and after construction (during the long operational life of a major underground asset), they protect both tunnellers and users.
In being responsible for the short-term and longterm safety and stability, tunnellers need to have good understanding of the geological conditions and sufficient experience with performing rock support, and that includes installation – which means not only knowing the bolt types but the equipment to place the bolts.
The installation work starts with drilling bore holes and, “Correct fitting and use of bolt drilling equipment improves occupational safety and increases capacity,” says the handbook. It adds, “When inserting and anchoring bolts, it is important that the relevant installation procedures are followed.”
The well-illustrated and structured chapter covers its theme in eight sections, as follows:
- Drilling equipment and bolt hole drilling – handheld drills; rock bolting rigs; jumbos; and, error sources in drilling bolt holes
- Bolt installation equipment – jumbos; wheel loaders with basket or work platform; pneumatic drills with feed column (feed cylinder); grout pumps; impact wrenches; and, hydraulic jacks and torque wrenches
- Installing bolts with expansion sleeve
- Installing bolts with polyester cartridges
- Grout for embedding bolts
- Embedding bolts
- Pre-tensioning bolts
- Water in bolt holes
Under the short sub-section on jumbos (which the publication labels ‘tunnel boring machines’), that handbook notes that it is common for these rigs to be used for drilling holes and also bolt installation. Further, in tight spaces, the rigs can be equipped with a split feed bar (two profiles that slide on each other) to make access easier for bolting.
Additionally, the handbook observes: “For practical reasons, it is common to use 48mm-51mm for drilling both charging holes and bolt holes when driving tunnels.”
GETTING IT ALL DOWN
Not a long chapter at 14-pages, this section of the rock bolting handbook gives some focus to the importance of ‘Documentation’, especially around tools and possibilities for digitisation of data in various ways. The information is important to daily construction and post-build phases, in final documentation.
The handbook observes that, in Norway, efforts are underway to digitise final documentation within Building Information Management (BIM) data environments.
The format is very well illustrated, following the approach elsewhere in the handbook. The chapter sections are: Definition; Recording; Final Presentation; and, Measurement-While-Drilling (MWD).
Definitions – this section discusses ways to hold data in 2D of bolting undertaken in the real-world 3D environment of tunnel. Assumptions are involved and these are discussed under various sub-headings, such as the ‘Fold-out principle’ and ‘Map and tunnel coordinates’.
The importance of this detailing should not be underestimated, for as the handbook notes, “Coordinates in a tunnel are fundamental for tunnelling and rock stabilisation.”
Recording – five main methods for recording rock stabilisation are noted: manual; drilling log; total station survey; camera; and, model-based documentation. Combinations of these methods might be most appropriate, it is observed. After brief introductions, each method is discussed in more detail with many supporting illustrations.
Final Presentation – the handbook recommends that collated data (often using software to record and store information) from the entire project is gathered and submitted as part of this step in the documentation process. The aims is to include data and information on all measures used for stabilisation of excavations, especially rock bolts (with type, number, length, location and direction installed).
It is noted that all major construction clients today require modelbased methods to be used on project to help plan, design and construction tunnels, leading to ‘before’ and ‘after’ – or ‘as-built’ – details in these digital documents.
The handbook adds: “This indicates a transition from drawingbased deliveries to drawing-less model-based projects, where the coordination model is pivotal.”
A result is new opportunities around bolting documentation. With major quantities of data being collected from drill & blast tunnelling projects across Norway, much of it gives “a good basis for the automatic creation of a bolting model” – such as generated based on MWD data. This can then be combined with other data, such as from profile scanning and Q mapping.
Measurement-While-Drilling (MWD) – the handbook notes that most tunnelling rigs used today in transport projects (road, rail) must be fitted with equipment for MWD data logging, resulting in rock quality information via bolt holes, helping interpretation for stabilisation assessment, such as ensuring that the hole has been drilled far enough beyond any poor rock for the bolt to end-anchor into good rock. There can be variation in anchoring of bolts as a result.