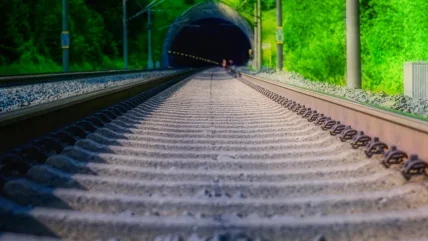
Turkey’s Bahçe-Nurdagi rail project has been under development over the last few years with shield tunnelling through abrasive hard rock.
The Turkish State Railways Directorate (TCDD) has been building the twin rail tunnel project to help develop the economy in the region. That part of south east Turkey is one of the country’s busiest railway corridors and TCDD plans to overhaul the railway connection by providing a shorter, faster route between the towns of Bahçe and Nurdagi.
Earlier this year, though, the region suffered two consecutive major devastating earthquakes, with magnitudes of 7.8 and 7.6. The Bahçe-Nurdagi rail tunnel project site is located and close to the intersection of two large active fault zones – the East Anatolian Fault (EAF) and Dead Sea Fault (DSF). The tunnels were inspected after the events and they were found to have sustained only minor cracking in a few concrete segments of the bored tunnels, which were nearing completion.
The geology in the project area has some of the most extreme hardness and abrasiveness ever measured in Turkey. It includes incredibly hard and abrasive metasandstone with quartz, with an average of 220 MPa (31,900 psi) UCS and a Cerchar abrasion value of 3.87, says Robbins, which provided a 8.0 m diameter single shield to construct the tunnels.
The TBM completed the first tunnel in 2020. In June this year, the TBM completed its second tunnel on the Bahçe-Nurdagi project. A total of 18.6km of TBM tunnelling was completed.
For the two drives, the machine completed lengths of the bored tunnelling of 9.2km and 9.6km, respectively.
After its first bore in the difficult ground, the machine required some inspection and repairs.
“Robbins Field Service was always available when we requested,” said Deniz Sahin, TBM Chief for contractor Intekar Yapi Turizm Elektrik Insaat San. ve Tic. Ltd. Sti. “The biggest repairs we undertook with Robbins Field Service technicians were the main bearing seal change and checking and repairing of the TBM before launching it on the twin tunnel after the completion of the first tunnel. Both operations were completed in a short time due to good planning with Robbins technicians.”
The machine began its second bore for the project in February 2021.
“During tunnelling we performed a normal maintenance programme as given in the TBM manual, and the machine had minimum downtime, which shows the durability of Robbins TBM in very hard and abrasive rock,” said Sahin.
Geology experienced on the second tunnel drive was comparable to the first, says Robbins, achieving a best monthly advance rate of 411m.
“We are very proud to complete this tunnel in difficult rock formations with our excellent team,” utilising the powerful Robbins single shield, said Sahin.
Yunus Alpagut, Robbins representative in Turkey, said: the TBM “has performed extremely well in this project with minimal downtime and good advance rates to complete the longest twin tube railway tunnels in Turkey.”