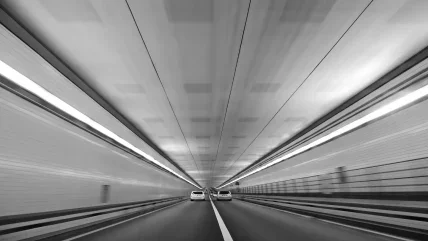
In March, Sika held a workshop led by, Sarah Langley, Head of Infrastructure, to instruct the British Tunnelling Society’s young members on the basics of tunnel waterproofing. In the room full of young engineers, supplies of enough tea, coffee and biscuits – and Sarah’s energetic and engaging presentation – provided the perfect start to the afternoon workshop.
The first half of the workshop focused on why waterproofing is needed, the requirements of water tightness, types of waterproofing solutions in tunnels, durability, and then concluded with the topic of innovations.
At its essence, waterproofing within tunnels is required to prevent water inflow and to protect the tunnel lining from degradation due to mechanical failure of the reinforced concrete lining. An early investment in a reliable waterproofing system can prevent huge maintenance and repairs costs possibly incurred later in the asset lifetime due to damages from water ingress. Here, Sarah presented some dramatic examples of significant water damage to tunnels which drove the point home.
One of the cornerstones of designing waterproof systems is understanding the different design influences on product selection. These include the depth of the system below ground in conjunction with the water table level, the soil conditions, presence of ground contaminants, temperature, construction methods, and standards, to list a few.
The other cornerstone is understanding the level of watertightness that is needed by the client for the infrastructure asset. The Swiss standard SIA 272/197 covers material and waterproofing requirements for geomembranes used in tunnels, and it provides classes for watertightness and the types of tunnels they commonly apply to. This is further, numerically elaborated in performance terms by the STUVA Report which provides the permitted rate of water infiltration, in litres/m2 for a duration of 24 hours.
Following the first steps of the design process, Sarah proceeded to explain the different waterproofing solutions available, depending on the type of tunnel and the watertightness required.
For mined tunnels, the waterproofing options are: synthetic sheet membrane systems; watertight segmental lining; sprayed tunnelling membrane; and, watertight concrete (white box concept).
Similarly, for a cut-and-cover tunnels, the options consist of: synthetic sheet membrane systems; fully bonded polymeric sheet membrane; liquid applied reactive membrane; waterproofing mortars; bituminous membranes; or, the watertight concrete (white box).
It is important to understand the consequences of the options you chose, she explained – for example, watertight concrete creates a buoyancy effect resulting from water pressure acting on the underground structure as groundwater is unable to drain away
Another important parameter of the design consists of the durability of the waterproof system. In some ways, a functional waterproof system within the tunnel is what enables the tunnel to meet its long design life requirements as it prevents defects and damages incurring within the tunnel as a result of active water ingress.
To demonstrate how Sika meets this requirement, Sarah explained the testing Sika carried out on the new Alpine Railway Transversal (NEAT) – a strategic ‘flat’ rail corridor passing through the Swiss Alps and comprising two giant rail tunnel projects: the Lötschberg, Gotthard and Ceneri base tunnels.
The client, AlpTransit, specified a 100-year design life with minimal maintenance on the concrete, in accordance with the sealing used in the Gotthard Base Tunnel. Taking into consideration the unique conditions for this tunnel, such as the high mountain cover and the increased ambient temperature, both the individual components and the way the combined system works had to meet the difficult requirements. The developed aging process for the components was extremely tough with all system components being stored for 24 months under various conditions before being tested. On NEAT, a durability research programme was undertaken (2.5-yr & 10-yr, in rock temperatures up to 45°C-50°C). Through targeted developments, Sika was able to meet the challenging requirements of the Gotthard and Ceneri tunnels. In situ tests were also carried out on the application and fixings, and checks carried out on the vertical folds.
A further project example the workshop attendees heard about was waterproofing for a road tunnel, also in Switzerland, that was much shorter – the 600m-long, twin tube, three lane Reussport tunnel. PVC membranes were originally installed in the tunnel in 1971. Recently, the tunnel was recognised as needing upgrades as per EU safety and security regulations. The remedial works to the tunnel provided Sika with the opportunity to inspect and test the membrane. Lab tests were conducted on 41 samples and the data plotted (see figure). Continuing the curve from the performance rate collected for 41 years, it can be seen that the PVC membrane would take far longer than 100-year durability to reach the designated 50% performance which indicated the end of its service life.
The first half of the workshop concluded with a list of standards used for material and waterproofing requirements for geomembranes across Europe, with BS EN 13491:2018 (Geosynthetic barriers – Characteristics required for use in the construction of tunnels and associated underground structures) providing a harmonisation of these standards as well as providing guidance on testing. Reference was also made to the Austrian guideline (Tunnel Waterproofing, from ÖBV), published in 2015, covering closed tunnels (NATM and TBM excavations) and cutandcover tunnels. Specific to the UK, the BS8102:2009 (Code of Practice for Protection of Below Ground Structures Against Water from the Ground) provides excellent guidelines via its Design Flowchart and additionally it also provides crucial guidance in considering both the buildability and repairability of the proposed waterproofing system.
CONSTRUCTION
While designing is key in ensuring you have chosen the right system for your project, installation is just as crucial in ensuring that the system functions successfully. By showcasing some excellent photography, while passing around samples of materials she was speaking about, Sarah provided the young engineers with a stepbystep overview of how waterproofing is installed. This would provide engineers overseeing the works with an understanding of what to keep an eye out for.
The installation of the tunnel lining commences with substrate preparation with the section elasticity modulus of the membrane being specified based on the evenness of the shotcrete. This is followed by installation of the drainage layer using disc fixations.
Here, it is important to note that a thin geotextile serves as a membrane protection and should not be used as a drainage layer. Depending on the quality and amount of groundwater, sintering or clogging may occur behind the geotextile which would impede the design life of the product.
The membrane is then mounted, and the seams welded. Similar to a joint, the weld may act as a weak point if it is incorrectly sealed or there is insufficient overlap. The number of joints can be reduced by using bigger sheets and it is crucial to carry out a quality check of the weld by either seam testing with compressed air or by using a vacuum bell. This then allows them to become the strongest part.
The second line of defense in waterproofing is achieved through different ways. The system can either be compartmentalised with sections being split into 150m2 zones, using control sockets or injectable waterbars at joints. In addition to explaining the basic concepts behind waterproofing, Sarah also presented a slide pack which went through the detailing of different joint sections, covering waterproofing at crosspassages, penetration sealing systems, Dwall connections, pile head solutions, and waterbars as well.
The most important component of successful construction is a trained and confident workforce. Training of the workforce or provision of waterproofing specialists is an option provided by Sika. As engineers, to ensure quality control of the waterproofing, it is important to carefully plan the installation procedure for waterproofing systems while keeping in mind the site conditions and weather conditions. It is important to define the daily work phases. Make sure that the completed daily work phases are watertight with special focus on the seams. If the site is exposed to wind then ensure there is no wind uplift and, in general, the sheets should be protected against works being carried out on site as well as foot traffic.
The workshop concluded with the topic of innovation and here Sarah presented: SikaProof A+, which is a hybrid bonding layers that forms a dual bond with concrete, through polymermodified cementitious bonding, thereby providing a watertight basement structure; and, SikaProof T, which is a twolayer composite membrane combined with existing single EBA sheet layer and a cement filled material layer.
Site photos were then available once again to study, showing the young engineers some truly fantastic images of works in tunnels from different countries, such as Switzerland, Italy, the United Arab Emirates, and Qatar. Overall, the workshop was an excellent start to the workshops provided by BTSYM for the 202223 period. The young engineers were exposed to both the design and construction, providing less experienced engineers with a good understanding of the basic concepts and more experienced engineers with resources to further explore waterproofing and understand all the different options that are available.