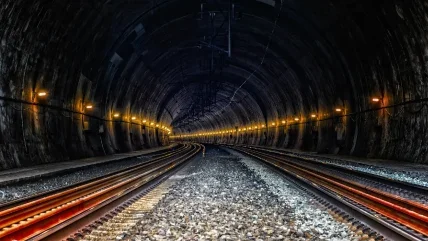
Underground space plays a vital role in sustainable urban planning as it provides a solution to the limited surface area available. In terms of transportation, underground networks enable efficient and rapid mass transit, helping to alleviate congestion and reduce carbon emissions.
Moreover, underground space is essential for the infrastructure required to sustain cities, such as dense networks of pipelines for delivering fresh water and the sewers for collecting wastewater to be taken away for treatment.
Additionally, underground space accommodates the extensive network of cables and service stations necessary for modern communication systems. By utilising underground space, cities can optimise their resource management and minimise their environmental impact, contributing to a more sustainable urban future.
Achieving decarbonisation in tunnel construction is not only possible but crucial from a sustainable perspective. Currently, nearly 70% of embodied carbon in tunnels is attributed to concrete linings. There is a consensus showing that this carbon emission footprint can be reduced by using less Ordinary Portland Cement (OPC) and employing new binders, using carbon cure methods, using high performance fibres instead of steel reinforcement bars (rebar), and reducing concrete thickness and optimising aggregate quantities.
To achieve bringing these down, we need to talk about, first, steel and concrete.
Steel fibres are a more efficient, durable and sustainable means of concrete reinforcement compared to rebar. Using steel fibres can save 50% on the steel and concrete compared to traditional reinforcement, especially in precast lining.
In this holistic approach, the high performance Dramix® steel fibre already plays an important role. Indeed, steel fibre reinforcement can significantly reduce the embodied carbon in segmental linings, compared to steel bar reinforcement. Rebar mass per unit volume of concrete in tunnel segments ranges between 90kg/m3 to 160kg/m3. Considering a CO2 factor of 1.85 for steel, carbon emission is about 166.5kg/m3 to 296kg/m3. In comparison, the mass per unit volume of Dramix 4D 80/60BGP steel fibres in tunnel segments is about 40kg/m3 to meet standard performance Class 5e, according to fib Model Code 2010 for such applications with only fibre reinforcement, and equates to carbon emission of about 35kg/m3. This means a reduction of 4.7 to 8.4 times in CO2 emission.1
MOVING TO PSCL
Permanent sprayed concrete (PSC) is a proven technology that has been used for many applications in underground works throughout the world.
The ITA report N°24, ‘Permanent Sprayed Concrete Lining’, published in October 2020, is to give infrastructure owners and their advisors the confidence to incorporate Permanent Sprayed Concrete Linings (PSCL) into their underground space design.2
The carbon emission during construction by conventional methods as drill & blast is more than by using tunnel boring machines (TBMs).
Results showed that, in the case of such conventional tunneling, materials are responsible for approximately 60% to 80% of the total impacts depending on the impact indicator.3
Changing temporary the shotcrete lining and permanent cast-in-place (CIP) liner to PSCL and improving the mix design could lead to CO2 savings of up to 75%.
Excessive structural design using cast-in-place concrete or other lining structures, where used in the current practice, have a significant impact on excavated volumes, construction time, construction cost, and CO2 emissions.
Many groups are currently conducting research that already shows positive conclusion, such as SUPERCON, in Norway. The final results from the SUPERCON project are yet to come, and hopefully the findings from the project could contribute to more effective tunneling with less carbon emissions.4
Main impact of this research:
In-situ cast concrete lining:
- 8cm + 8cm sprayed concrete
- 40cm in-situ cast
- Results in 130kg CO2e/m2 tunnel (probably much higher)
PSCL
- 8cm + 4cm + 6cm sprayed concrete
- Results in 52kg CO2e/m2 tunnel
START FROM RELEVANT MATERIAL PROPERTIES
A permanent sprayed concrete type of tunnel lining should be considered in the same way as any other permanent concrete structure.
For structural use, mechanical performance of spray fibre reinforced concrete (SFRC) lining must be verified in accordance with a performance-based approach. Model Code 2010 allows a comprehensive design approach for FRC. This approach can be extended to sprayed FRC if a correct characterisation of the mechanical properties of the material is made, and with particular regard to the residual tensile strength.
Particularly when working with SFRC, it is important to consider and understand the idea behind the testing procedure selected. Testing a material is the same as asking a question.
For example: How does this material react under the specific conditions of this test method? Subsequently, an answer to the question can be retrieved from the results, and this answer can be shared or used for design or performance evaluation. Essentially, it is crucial to understand the test (question) that is being run (asked) and the result (answer) that is collected.
In EN 14487-1, the European Standard for sprayed concrete, Annex A mentions the following:
“The different ways of specifying the ductility of fibre reinforced sprayed concrete in terms of residual strength and energy absorption capacity are not directly comparable.
- The residual strength must be specified when the concrete characteristics are used in a structural design model.
- The energy absorption value measured on a plate with continuous support can be specified when, in the case of rock-bolting, emphasis is laid on energy which has to be absorbed during the deformation on the rock.”
EN 14487-1 prescribes differing ways of specifying the ductility of sprayed concrete. These include an EN 14488-5 energy absorption test, used in empirical design methodologies; and, an EN 14488-3 flexural strength test in which residual strengths are determined using notched beam specimens in accordance with EN 14651, consistent with limit state design to fib Model Code 2010.
In 2011, EFNARC introduced a notched panel test, based on the EN 14488-5 energy absorption test specimen, as a geometrically analogous alternative to the notched beam methodology thereby providing equivalent residual flexural strengths. It was suggested that the notched panel test had several advantages, including using a test specimen that better represents the material in the real structure with reduced variability.
In 2022, EN 14487 was amended to include reference to the alternate methodologies for residual flexural strength determination. In 2020, Chris Peaston included the prEN notched panel test in the SCL specification for the HS2 high-speed rail project’s Si/S2 contract, provided by Arup for SCS. There is provision in the SCL specification for the notched panel test to be used as an alternative to the notched beam.
KEY PERFORMANCE CRITERIA FOR PSCL
By adopting pr EN 14488-3 Method B for the post-peak characterisation of the sprayed FRC, it is so possible to derive the parameters fct,L, fR1, fR3 that are necessary for the design according to Model Code 2010. A performance class type C35/45 3c could be considered.
It is recommended for permanent SCL the minimum performance level to be:
Fr1k/frlk > 0.8 and fr3k/fr1k >0.9
CONCLUSION
Steel still is the most recycled material, and the Bekaert R&D team, together with universities, continue to investigate recyclability. Remelted or reused steel could be directly reused as steel fibres to reinforce tunnels and mines. SFRC delivers a microplastic and pollution free solution, as is increasingly required by government in shotcrete applications for subsea tunnels.
For a sustainable use of structural concrete, environmental and mechanical performances of concrete structures must have the same importance. By means of sufficiently high mechanical performances, the structural safety of a construction is ensured.
This the reason why a great challenge for the coming years will be develop solution for low carbon tunnel lining based mainly on the following approach:
- Lower thickness
- New generation of binder
- Use of FRC, which would eliminate traditional rebar in all types of lining
- Production process improvement
PROJECT EXAMPLE: M4-M5 LINK TUNNELS, SYDNEY
The M4-M5 Link Tunnels in Sydney, Australia, are approximately 7.5km-long and accommodate up to four lanes of traffic in each direction with spans up to 23m in the main lines and 34m in transition caverns. The project connects the new M4 Tunnels with the M8 Tunnels to form the 33km-long WestConnex Motorway, mostly underground.
Like many road tunnels in Sydney, these tunnels are designed as drained structures and adopt PSCL for a 100-year design life.
In wet sections of the tunnel, a sprayed waterproofing membrane was adopted where the primary lining is still designed to resist all ground loads and the applicable residual water pressure in the longterm. The secondary lining design is designed without relying on longterm shear transfer by the membrane to resist operational loads and, as a redundancy, also the residual ground water loads.
Sprayed concrete strength.
- Primary & secondary lining: 40MPa, flexural tensile strength, fR1k= 3.5MPa, and fR4k = 3.0MPa
- Lining thickness: primary lining is 110mm with 35kg/m3 of steel fibres; secondary lining is 125mm with 35kg/m3 of steel fibres and 1kg/m³ of polypropylene (PP) fibres for fire resistance
The use of high-performance end-hooked steel fibres Dramix 4D 65/35BG was effective in achieving the desired high-level performance ground support characteristic design fr4 = 3.0MPa. Production testing confirmed performance with only minor and, as expected, outliers. The high-performance fibre combined with the consideration of compressive membrane action (CMA) allowed for the design of very thin FRPSCL (t = 90mm) with an assumed unbonded condition with high capacity demonstrated by both numerical modelling and large-scale field tests. The consideration of CMA effects were confirmed by load-bearing capacities that were some 3-6 times greater than those estimated by conventional design methods based on pure flexural/bending resistance.
The outcomes were very positive:
- Reductions in the amount of sprayed concrete used on the project by 27,000m3 (15% in thickness) and reinforced steel fibres by 830 tonnes (10%)
- Reduction of more than 33,000 tonnes of embodied carbon (CO2e) from sprayed concrete
- The removal of 9,000 heavy vehicle movements of Sydney’s local and main roads
- Cost savings to the project by minimising materials
PROJECT EXAMPLE: REM METRO, MONTREAL
Advantages from the development of SFRC as a permanent lining are many, including for the REM Metro Project under construction in Montreal, in Canada. The advantages include:
- Environmental Impact: reduction of CO2 by reducing the mass of steel by using steel fibres rather than rebar
- Reduction of CO2 by having thinner tunnel lining, equating to less concrete used; also, more durable lining means a longer service life
- Cost Reduction/ Cost Performance: reduction in mass of steel required as well as there being no in-situ installation cost
- No formwork required, leading to savings in labour and build time
- Quality and safety can be achieved using the right product for the right use, specifying clear performance requirements and appropriate testing methods
The REM project is being built by a joint venture of SNC Lavalin, Aecom, Dragados, EBC, and Pomerleau. The final design is being performed by a joint venture of SNC Lavalin and Aecom. Once completed – scheduled for the end of 2024 – the REM project will be the 4th largest automated transportation system in the world.
The project includes three underground stations in downtown Montreal, one of which – Edouard Montpetit (EMP) Station – will be the deepest station in Canada upon completion.
The EMP Station is built within the existing double-track Mont Royal Tunnel (MRT) with the side platforms constructed by enlarging the existing tunnel. Using the NATM method of excavation, the station utilises permanent rock bolts and shotcrete reinforced with steel fibres for both the initial and final linings of the station structures (tunnels, shafts, caverns etc.). First, a 5cm layer of steel fibre reinforced shotcrete is applied as initial support, then bolts are installed, and then a sprayed waterproofing membrane is applied. The lining work is finished with another 5cm of steel fibre reinforced shotcrete. The liner is designed for a 125-year service life.
This configuration was first used in North America for a pump station cavern in Indianapolis, but it is the first time this approach is used for a major transit station in North America.
The advantages of this configuration are numerous both in terms of design and constructability in comparison to the typical approach, which would consist of an initial temporary support, a sheet membrane and a permanent final liner. Effectively, the initial liner, which would typically be considered only as temporary support, now serves in both temporary and permanent functions, as this configuration allows load transfer from the initial lining to the final lining. As a result, the overall lining thickness is reduced when compared to the typical design.5