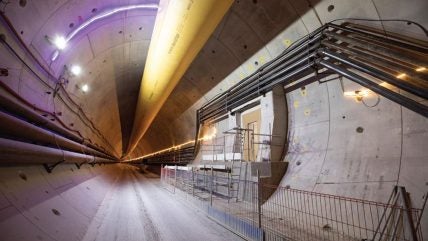
When TBM ‘Cecilia’ broke through on HS2’s 16.1kmlong Chiltern Tunnel on 21 March, smiles on the faces of those involved were irrepressible.
Arriving at the north portal, Cecilia joined TBM ‘Florence’, which had broken through three weeks earlier on 27 February, marking the end of boring on HS2’s longest tunnel.
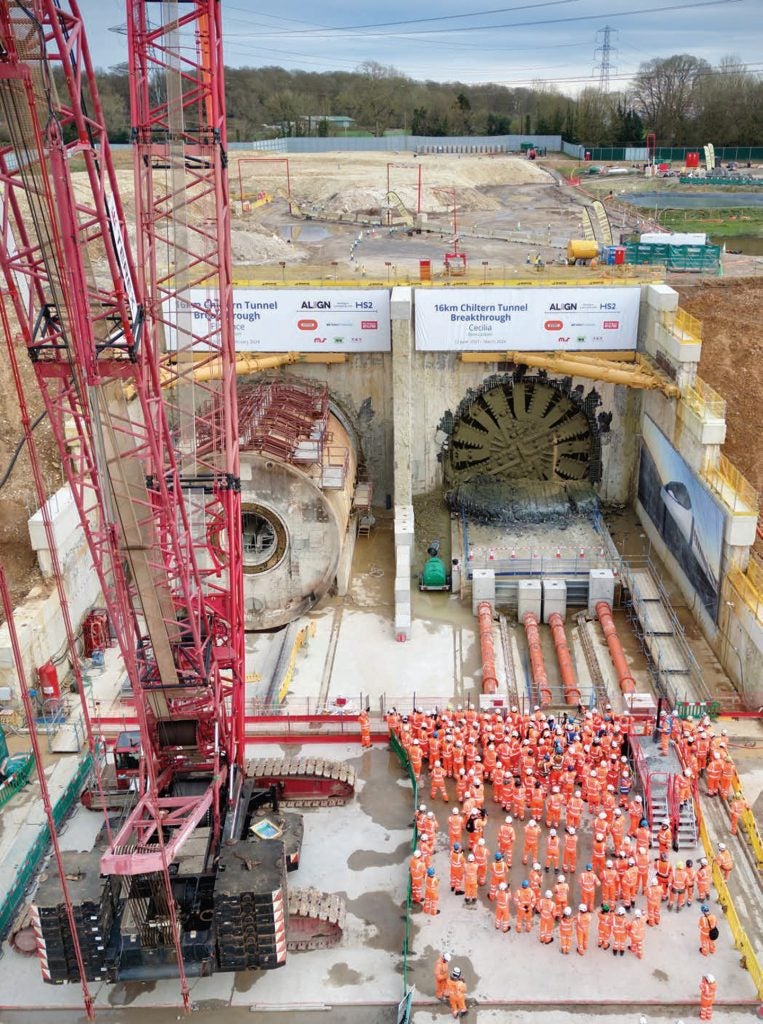
Not only is the twin-bore tunnel on C1 – HS2’s Central Phase 1 section – the longest on the high-speed railway, it is more than three times longer than a typical drive for a TBM.
“We are very proud of what has been achieved – 32km in 33 months. When we broke through, there were many happy faces,” says Align JV’s underground construction director, Didier Jacques.
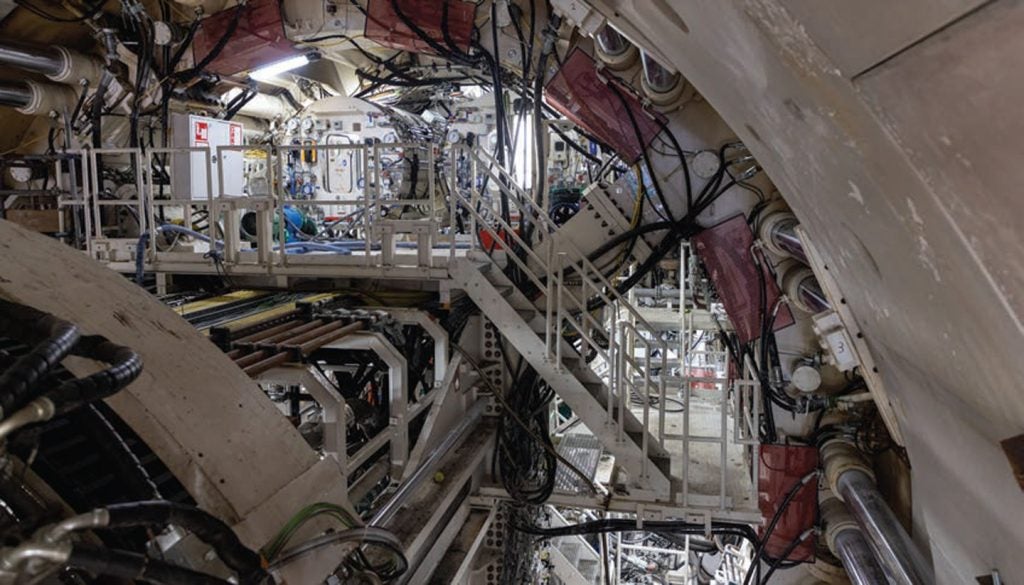
HS2’s head of delivery, Mark Clapp, says that pride was well deserved.
“It was a real case of the team delivering,” he says, adding that everyone, from the surveyors, to the TBM crew, to the team managing the spoil works, was proud of the achievement.
“It hasn’t all been plain sailing, we’ve had our challenges but what has been notable is at each of those potential stumbling points, we’ve closed ranks, identified the best for the programme, and the team have found the right solution to deliver the works without major incident. What more can you ask of a construction project?”
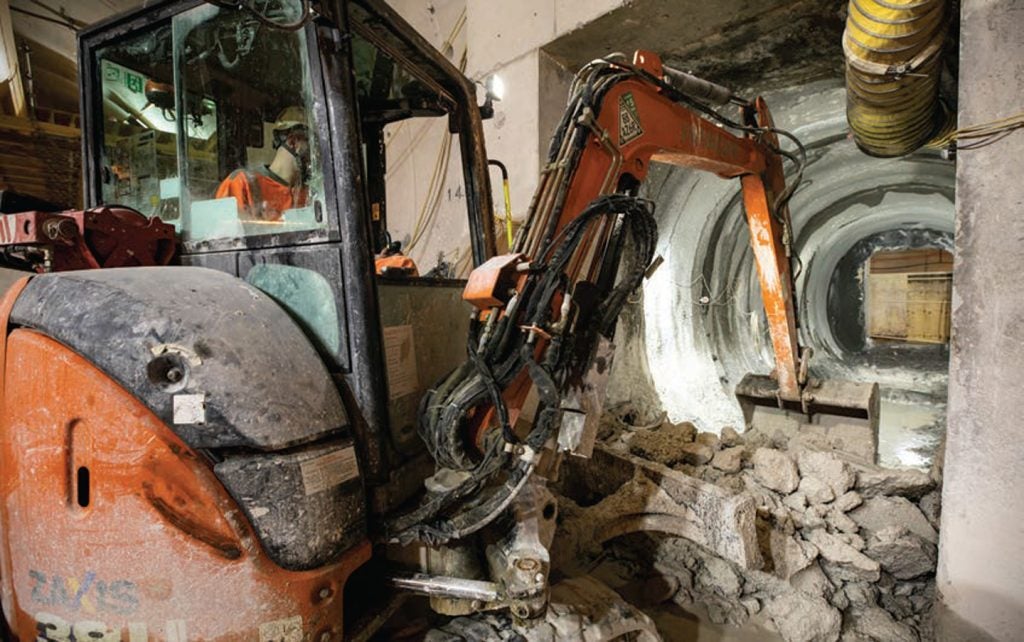
Align – a joint venture of Bouygues Travaux Publics, Sir Robert McAlpine, and VolkerFitzpatrick – operates as an integrated project team (IPT), a collaborative approach that was established between all parties at the outset and it has been working well.
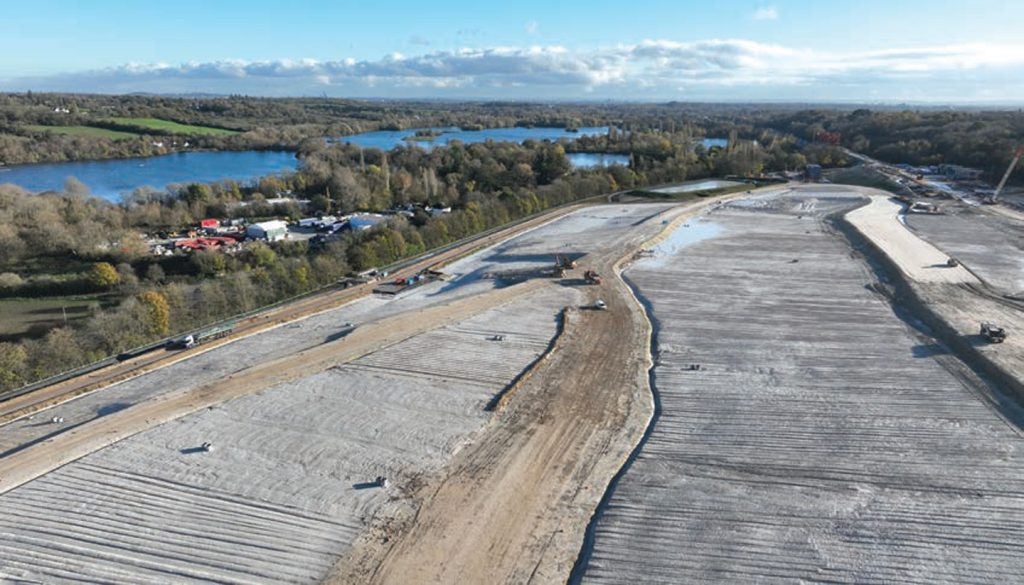
“Align worked really hard to understand the challenges and also to optimise the delivery vehicle,” says Clapp.
An early example of this was Align’s three-year collaboration with Herrenknecht on the TBM specification.
“It would not be unfair to say these two TBMs are Didier’s babies,” says Clapp. “He is an absolute mine of information on TBMs and every aspect of these TBMs has been thought about.”
The result was two variable density 10.26m-diameter TBMs – the first to be used in the UK and the largest TBMs to be used on a rail project – designed for the chalk and flint geology of the Chiltern Hills.
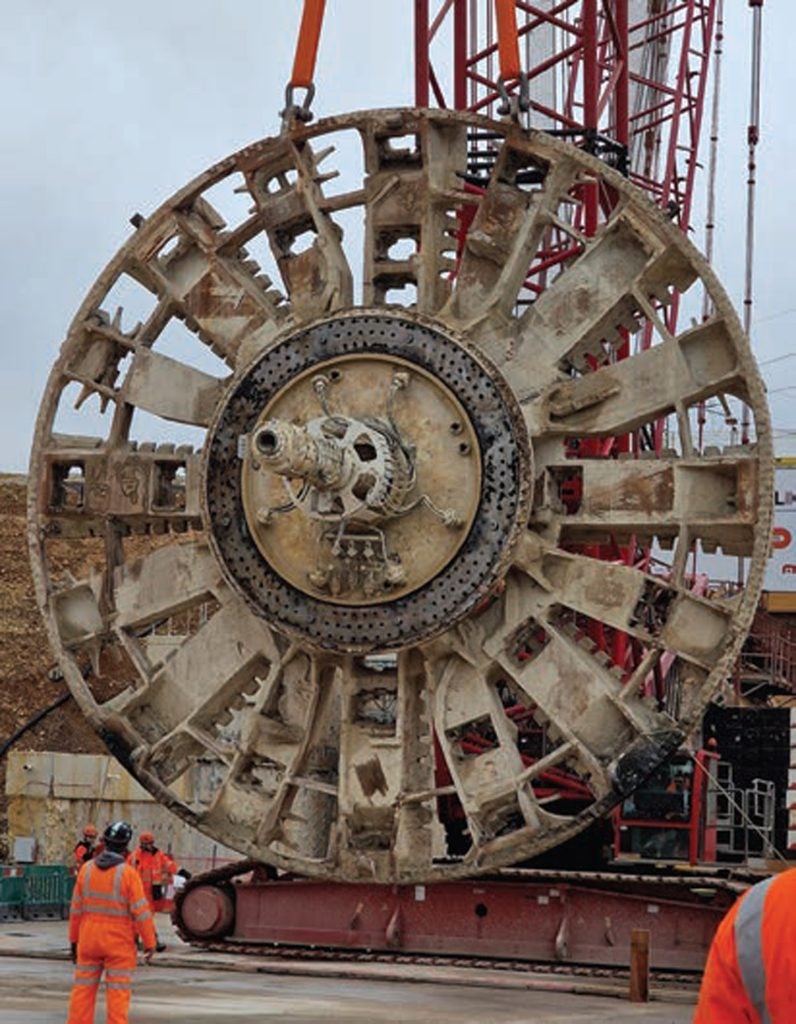
The partnership between Align and Herrenknecht produced TBMs with an impressive amount of innovation – enabled by the space in the tunnel and motivated largely by the length of the tunnel and the desire to improve safety.
“We wanted staff to have the safest TBM to work on,” says Jacques.
In a world-first for boring technology, the TBMs feature the Krokodyl and Dobydo robots reducing the need for operatives to work in confined spaces, at height and near plant and machinery, when handling the tunnel segments. The Krokodyl system removes the timbers that separate the segments when they are delivered on to the TBMs and drops them into a dedicated storage area, while the Dobydo robot installs the dowels on the segments, required before installation.
Stepped access everywhere, rather than ladders, was another safety feature on the TBMs.
The technological innovations made on the Chiltern Tunnel project are a change from established practices and, after some initial scepticism, the team embraced the changes.
“The first time they saw the robot they were sceptical, but they saw it made life easier and safer. They took ownership,” says Jacques.
The logistics of building such a long tunnel also shaped operations – not least the slurry management.
Slurry processing is usually carried out in tunnels of 3km-4km lengths, says Jacques, but in this case Align was applying it to a tunnel four times as long, and with the added challenge of a 110m difference in height between the South Portal, where the TBMs were launched, and the North Portal.
In the slurry box on the TBM, recycled water is added to the excavated material and the resulting slurry is pumped to the slurry treatment plant – the largest in the world – on the South Portal construction site. There, a total of 24 filter presses processed the resulting 3 million m3 of chalk from the tunnel excavations.
After water was extracted from the slurry, the resulting chalk cake is retained on site, removing the need for hundreds of lorry movements on local roads. The chalk is to be used to landscape the area once the construction site is decommissioned.
The 16km tunnel length also led to a grout batching plant being incorporated onto the TBMs, which was essential to support TBM production.
“We need just-in-time preparation of grout so having the plant on the TBMs meant the grout was not travelling the length of the tunnel,” says Jacques.
Another innovation was the invert slab concrete bridge that worked about 200m behind the TBM. This concreted the invert – again with very limited human intervention being required – which provided increased width to allow two lanes, rather than the usual one, for support vehicles. The result was greater flexibility and efficiency, and it allowed construction of the 38 cross passages and five adits while TBM excavation progressed.
Efficiency was also gained through continuous boring, made possible by Align and Herrenknecht developing a ‘Centre of Thrust ‘principle, rather than having potentiometers to divide the thrust between hydraulic rams. The system allows the TBM pilot to choose a position of centre of thrust and then hydraulic cylinders calculate the pressure required for the direction.
This was done through a touch screen and removed some of the headaches for the pilots, says Jacques. The continuous boring removed the stop-start of installing the rings, helping Align to achieve some record-breaking advances. TBM Florence exceeded expectations, achieving an advance of 42m in a day; 226m in a week; and 842m in a month.
Jacques says the approach required adjustment by the TBM crews until they became familiar and confident with the new automated processes.
Project developer HS2 Ltd’s carbon reduction target was a driver for further innovation on the contract. Align cut the volume of concrete needed for four of the tunnel’s five shafts by optimising the design so that the D-walls – which normally would have been temporary works with permanent walls constructed inside them – were designed and constructed as permanent works.
This reduced the diameter from 31m to 17m. Caisson construction was used for the Chesham Road intervention shaft.
The design of the tunnel walkways was also reviewed to cut the amount of material required.
To reduce carbon emissions on energy and fuel, Align agreed a deal with National Grid that the power for the TBM would be generated by nuclear and renewables in equal measure, and vehicles on site were fuelled by HVO (hydrogenated vegetable oil) rather than diesel where possible.
Align introduced a polymer to replace the use of lime to process the slurry at the slurry treatment plant. Introducing the polymer was a big step, says Jacques, and it had the bonus of being safer, as well as more environmentally friendly.
The tunnel cuts across groundwater source protection zone 1 (SPZ1) and passes under the M25 motorway, the River Misbourne and the Chiltern railway. All but the last 200m of the drives were in chalk, with flint present, and 30% in dry chalk where the tunnel sits above the water table.
Prior to tunnelling, all the features along the alignment were mapped and safe stopping zones identified. That did not, however, prevent some surface depressions, or dissolution features, forming along the route.
We’re in chalk and these are naturally occurring phenomenon across the Chiltern Hills, so it’s not unusual to have indentations,” says Clapp.
Jacques adds that the tunnelling operations activated existing dissolution features; it did not create them. Looking at the TBMs’ output and the material in the slurry treatment plant, Align and HS2 developed a ground movement risk assessment that was carried out each day, and it helped to remove any surprises.
“The accuracy of that enabled us to identify each of those movement locations prior to anybody else, so we were out on site and in two cases witnessed the ground movements starting,” says Clapp.
Tunnelling through flint was abrasive on the cutterhead, but working in a SPZ 1 also presented challenges for maintenance, whether planned otherwise. Safe areas for tool changes were established around each of the shaft locations but outside those areas it had to be assessed whether water could be kept out of the head for long enough to carry out the work.
“There were some locations where, ideally, we could have changed tools sooner, but the machines were being well looked after and they delivered what they needed to,” says Clapp.
The C1 contract brought many new aspects to tunnelling in the UK – a variable density TBM, continuous boring, the TBM technology, and, the length of the Chiltern Tunnel to name a few, so there is a lot to learn from this project.
Jacques believes the TBM innovations will become established on future projects.
“We are the first site on HS2 to have an IPT, constantly sharing with the HS2 tunnelling working group. Through this group, our legacy will be not just to HS2, but to the wider industry,” he says.
For Clapp, one of the legacies will be the apprentices and graduates employed who are now skilled in their disciplines.
“We’ve seen people who started with us with no construction experience, leaving as fully competent and experienced individuals to join projects elsewhere. That’s a really positive legacy,” says Clapp.
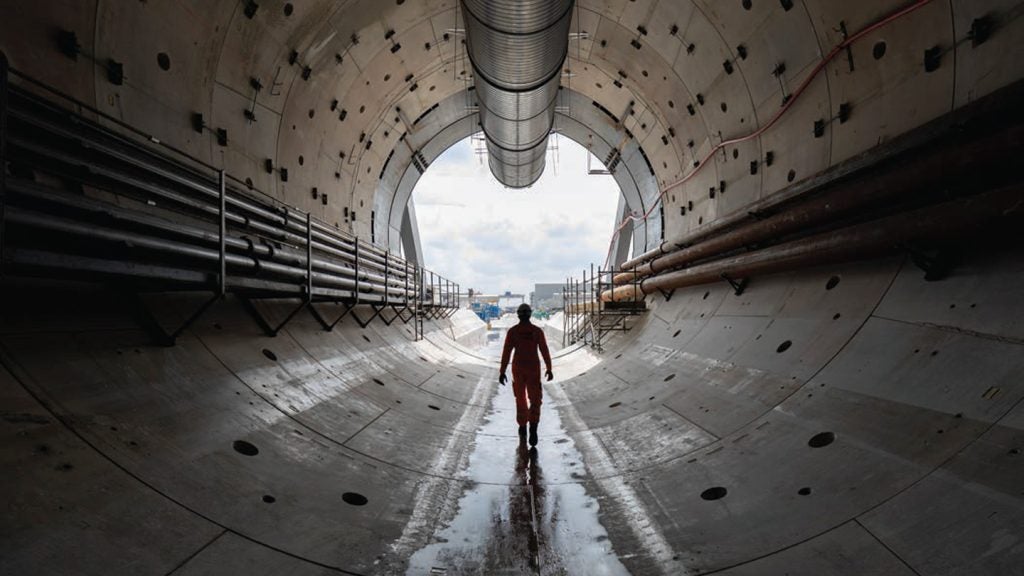
Jacques adds that many operatives now have enhanced skills through using the robots on the TBMs, and new skills and expertise gained from the automatic slurry process.
Align still has plenty of work to do, including completing the 38 cross passages and five adits, which are currently 75% complete, and fitting-out the five shafts, but the team and HS2 are still taking time to acknowledge what Clapp describes as a “fantastic milestone” in completing tunnel boring.
The two 16.1km-long drives were challenging but, completing them “safely and on plan”, was a great achievement.
“The result speaks for itself – and that’s not by luck. It’s come from hard work and team effort, and we all have massive pride in that achievement,” says Clapp.
“The scale of what we have here is unusual and the challenges we’ve overcome are unusual so why would you not be proud?”