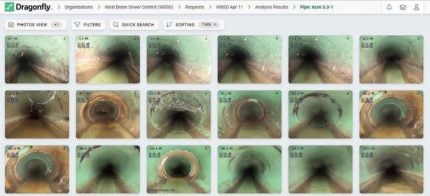
Many challenges and technological developments are underway in the trenchless, no-dig and microtunnelling space across the US, and farther. In this article, T&T has outline briefings from Jacobs and AECOM on key activities involving their respective participation.
Jacobs briefs on comparative experience with artificial intelligence (AI) and human monitoring of CCTV visual checks of utility pipe conditions. Two case studies are considered, below, from West Boise Sewer District and a large northeastern US water/wastewater utility, respectively
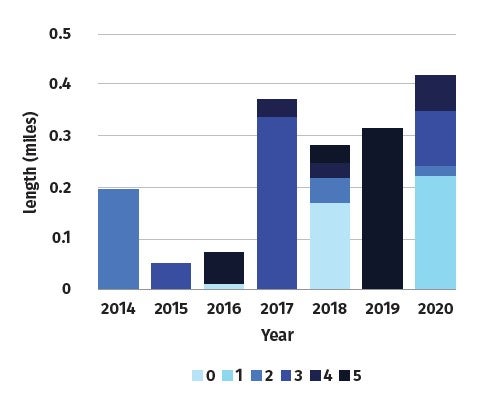
AECOM briefs on the microtunnelling works under the runway of Harrisburg International Airport, in Pennsylvania, where it led the design team (see box panel). The tunnelling works were recently successfully completed.
EFFECTIVE ASSET MANAGEMENT USING AI
Nationwide, utilities are dealing with aging and deteriorating wastewater collection infrastructure and increased sewer flows due to urbanisation and climate change. Financial, resource, and regulatory constraints necessitate focused collection system management, with utilities turning to artificial intelligence (AI) to proactively assess their buried assets, prioritise operational and capital budgets, and efficiently manage collection systems.
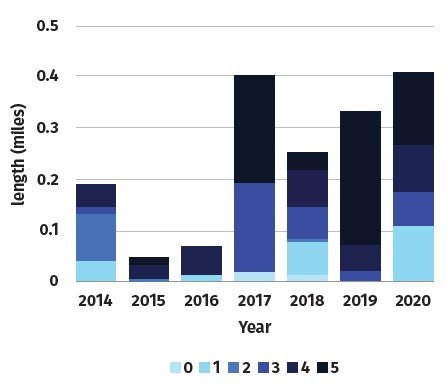
Utilities use closed-circuit television (CCTV) to capture pipe condition details. Defects are recorded in real-time, visually observed, and coded by trained inspectors. This is a time-consuming, monotonous task, and results can be somewhat subjective. AI provides objective data, enabling utilities to make informed data-driven decisions. AI consistently scores the defects, codes defects faster, does not blink or fatigue, and automates the monotonous coding task, improving CCTV sewer inspection crew efficiency.
Jacobs has built a cloud-based, AI defect coding solution, DragonflySM in partnership with Hitachi using next-generation machine learning and computer vision that includes a pipe insights module powered by Jacobs’ Argon platform. Argon provides prescriptive asset management insights, including recommended reinspection and maintenance schedules and prioritised cost-scheduled rehabilitation. Dragonfly’s AI technology helps utilities analyse their CCTV inspection videos (current and historic), providing reliable and accurate data and prescriptive asset management guidance for effective collection system management.
West Boise Sewer District Case Study
West Boise Sewer District (WBSD) faces challenges improving the accuracy and efficiency of its sewer inspection operations with limited resources, aggressive schedules, and significant sewer inspection backlog.
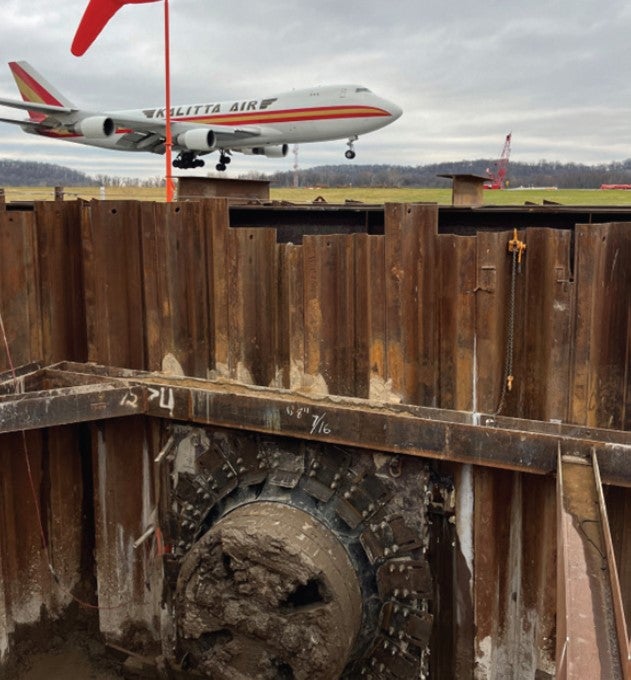
Jacobs introduced WBSD to Dragonfly as an AI solution to expedite sewer defect coding and provide highly accurate inspections at low cost. Prescriptive analytics provide focused asset management insights and pipe repair, rehabilitation, and replacement guidance. While maintenance and office supervisors were keen to use Dragonfly, others were cautious of the new AI technology.
WBSD completed a pilot to verify results before applying at scale.
- Processed 7620 linear metres of CCTV videos
- Identified significant pipe deformity defect missed by human inspection
- WBSD manually reviewed defect images to confirm AI findings (see Figure 1)
- Accurate defect identification increased WBSD’s confidence in AI
- Dragonfly pipe insights module (powered by Argon) recognised by WBSD as a significant value-addition
- Pilot expanded to entire sewer network
- Significant cost savings compared to WBSD manual coding budget
Northeastern US Utility Case Study
A large northeastern US water/wastewater utility owns a system that includes approximately 2424km of sewers.
Sanitary sewers are inspected using CCTV and coded by inspectors, with video, coded defects and pipe conditions reviewed by engineering staff (a time- consuming, repetitive, and subjective process). A Dragonfly pilot compared AI results to (human) inspectors and showed how the AI solution with optimised quality control can improve accuracy and efficiency of sewer inspection operations.
- Processed 2743 linear metres of historical CCTV videos
- Varied pipe materials (PVC, VCP, RCP)
- Compared structural and maintenance defects
- AI identified significant differences in structural defects (see Figures 2, 3) and subtle and difficult to detect defects overlooked by (human) inspectors
- Continuous monitoring by AI captured all defect occurrences
- Defects not previously identified help to manage and prioritise pipes requiring intervention
MICROTUNNELLING AT HARRISBURG AIRPORT RUNWAY
Microtunnelling was recently completed that passes under the runway of Harrisburg International Airport, PA. The works were undertaken for the owner, Susquehanna Area Regional Airport Authority (SARAA), as part of its Cargo Expansion II project.
The expansion works were designed to create the infrastructure for three new cargo aircraft parking positions. To create the additional parking space called for a range of construction works, including hangar floor demolition and pavement expansion, plus installation of new 780m-long storm drainage.
There were already 1.07m-dia. storm drains under the existing active Runway 13-31 and Taxiway A. But enhancing these lines presented construction risk and so to improve the storm drainage would involve constructing a 165m-long stretch of the new line under the runway – without interrupting or shutting down its use.
Microtunnelling was the focus as other methods were precluded for various rationale: using pipe-bursting to upsize the existing storm drains would cause surface heave to the runway; horizontal direct drilling (HDD) has poor grade control and that brough some risk of heave to the runway; and, jack and bore methods were incompatible with groundwater and have less controlled overcut, presenting settlement risk.
Value engineering was used to help decide between three design alternatives (1-, 2-, and 3-pipelines) on the basis of permitting, schedule, constructability, construction risk, view on probable construction costs, and future maintenance costs. While the twin-pipe option was not the lowest, or highest, it was the owner’s preference for reasons including operating and maintenance benefits, and no siphon to avoid grit build up.
The design solution involved twin drives of 1.52m i.d., 1.83m o.d. reinforced concrete pipes (RCP), installed using a microtunnel boring machine (MTBM) to avoid disruption to airport operations. The machine worked between open cut box culverts on either side, connecting from the apron and discharging into the river.
Prior to the tunnelling works, the MTBM selection was determined from data collected from geotechnical investigations, including test borings, laboratory and insitu testing, and a geophysical investigation. As a result, the interpretive profile of the geology to be bored through under the active runway was determined to consist of unstable fills and hard native material under the water table.
An MTBM was a specified pressurised face for fully sealed microtunnelling was selected for installation of two 1.52m i.d. storm drains, along with pre-excavation ground improvements. Working hours were restricted. Extensive monitoring was performed during all the preparatory and microtunnelling works. The MTBM drives were recently successfully completed.
- Client: Susquehanna Area Regional Airport Authority (SARAA)
- Design Team: AECOM
- General Contractor (GC): Kinsley Construction
- Third-Party Construction Manager: Urban Engineers
- Instrumentation and Monitoring Subcontractor: Kilduff Underground Engineering
- Shaft/Pit Subcontractor: Self-Performed by GC
- Horizontal Directional Drilling Subcontractor: JMF Underground
- Pre-Microtunnelling Grouting Subcontractor: Nicholson
- Microtunnelling Subcontractor: Michels
- Project Permanent Works Supplier: Vianini Pipe, Inc. for both the RCP casings (single pass – carrier pipe too)