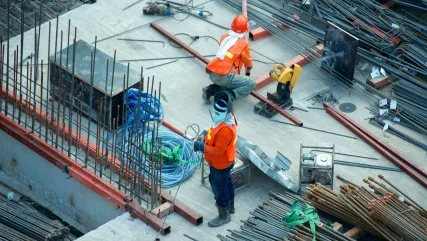
Health and safety is becoming more a fact of modern life. The construction industry in particular is under increasing scrutiny; the pressure to conform to regulations is strong. But there are some aspects of health and safety that cannot be improved purely through legislation and directive. One of the main such areas is behavioural safety.
Speaking to Tunnels and Tunnelling earlier this year (see Tunnels and Tunnelling International, March 2016, pp. 20-24) Bob Ibell of London Bridge Associates said that one of the areas in which the industry has taken a backwards step in his career is that there is less of a voice speaking out for the labour force compared with earlier days. The responsibility for thinking about and looking after the workforce has moved downwards, and with main contractors not particularly interested (as a rule), the less-powerful subcontractors have to step in. In British subcontractor Joseph Gallagher’s (JGL) case, as far as behavioural health and safety is concerned, they have.
NEED FOR CHANGE
In early 2014 a machine driver performed an operation he was not asked to do, without a method statement detailing how to do it. As a result of the decision, another worker was badly injured and the company decided it needed to do things differently.
Up until this point, according to JGL group managing director Steve Harvey, the company had been led by whichever main contractor it was working for. JGL would get involved in everyone else’s health and safety as well as the accepted behavioural safety programmes. However, the decision was made to develop its own programme rather than using a main contractor’s.
The principle is training the workforce to have ‘leaders’ in among the labour, carrying out the work while taking responsibility for their own health and safety, and also to develop a culture of looking after each other.
GATHERING DATA
The fi rst step was to identify the needs of the company. JGL hired a behavioural safety specialist called Alkoomi. Alkoomi started the process by performing a cultural survey of all employees. This is an anonymous process that involves paper-based questionnaires to individual interviews. A report is produced that demonstrates what people think of the business.
“Coming from the mining industry, which is culturally quite an aggressive environment, this came out probably slightly better than we thought,” muses Harvey.
Some 17 key points came out of this cultural survey, which included comments such as “method statements were being prepared by engineers or managers who don’t really understand the key points of the work”. According to Harvey, the comments were pretty much what might be expected from a construction subcontractor’s workforce, but having gotten everything out in the open through anonymous comments, the company could move forward with plans.
DEVELOPING A PROGRAMME
Firstly a leadership team was put together from JGL employees across the business, from site workers to directors, and set aside to be independent from the fi nancial and day- to-day control of the business. It exists solely to focus on the culture and approach to health and safety.
A bespoke programme was then developed with the help of Alkoomi to educate the people, it is built around them and what Harvey calls ”exceptional leadership”. The chosen employees also go through a course to teach them how to train others. These people then train the wider company in behavioural workshops that all employees then have to go through.
“The workshops are led by individuals who have shown an aptitude for leadership,” says Harvey. “It is quite a powerful thing to see senior managers in a business taken through a training course by a concrete pump operator, a labourer, or a machine driver just because he was seen to have this aptitude. It relies a lot on mutual respect.
“When we fi rst put the programme in, I went out with Joseph Gallagher himself and we went to see every person in the business. This meant going up and down the country, seeing 100 people at Bond Street or two people at a site at a motorway service area. But we still leave the direction of the safety side of the business to the LIFE leadership team. A lot of businesses have behavioural safety, but what is important is being relentless with it according to Harvey.
As a construction company, there is not much difference in what JGL would require compared to any other programme. But as a subcontractor – a hands-on company with a relatively large number of direct employees – it has a lot of impact on site if the company has its own programme. The company has its own policy rather than leaving it to the main contractor to try to control the way they work.
“They are our people doing the work, and the company’s reputation lives or dies on the back of what they do,” says Harvey.
IMPLEMENTATION
There is a workforce engagement halfday course which has a maximum of ten people, given by JGL workers. At the end of the workforce engagement course, employees are asked to commit to a pledge, and they write down their own personal safety commitment.
Some are not interested in doing this, but according to Harvey in those cases the workers are asked to leave the business. New employees are also told, prior to any other discussions, about this requirement and if they are not prepared, the interview stops there.
There are also monthly LIFE meetings that involve the leadership team going through everything that happened in the previous month. It starts with a chance for everyone to give a general feel for how the last month went, before looking at any data, numbers or incidents. Each worksite has representation at this leadership meeting.
“You need to be relentless in pursuing this and staying on top of it. And people have seen it as a very positive thing. Certainly our performance from a health and safety point of view is improving. What we were keen to do was not set any unrealistic targets. We just say our aim is to send everyone home safely at the end of the day, and hopefully we can achieve this.
“We have setbacks, we have had a few incidents since we started, but hopefully this gets fewer and fewer. The important thing is not to throw up our hands when something goes wrong – we say ‘tomorrow is another day’ and not spend too long on mistakes.”
INDUSTRY REACTION
Regarding main contractor response, Harvey says it has been positive; that they’re pleased to see a subcontractor taking the initiative.
“It makes their lives a bit easier if they know a subcontractor has the same drive they have. I’ve not come across anyone who sees it as a negative of course. And I’ve always been able to sell JGL as a technically competent business, now I want to sell it as the safest.
“Things are changing. Recently we secured the Bank Station contract in London for Dragados. We were not even talking about price with them at the beginning of negotiations; it was all about how to keep the men safe. It is that significant a factor. There are incentives within the contract around retention of people, safety performance, safe delivery. But to be frank it’s about having a consistent workforce, it’s about having the right leaders on the project, and it’s about working collaboratively as a team to make sure the primary goal on a given day is going to be safe. And that’s essentially what we do with it.
FINAL THOUGHTS
“Dragados appears to be a main contractor that wants to be different and are looking for the right way to go. But a lot of contractors are still looking for the cheapest price. But the way to a safe industry is to ensure you have the right people doing the work. And it does come with a price.
“Having said that, if you’re not working safely it ends up costing a lot more, but it’s too late by that point in time. I’d like to think we have the right strategy.