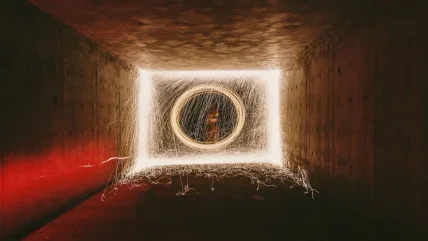
Tom Lennon of BRE GAVE an authoritative talk. He has been responsible for full-scale fire tests on steel, concrete and timber frame buildings at BRE’s Cardington facility. He has also researched the fire performance of concrete and has been involved in fire testing of tunnel linings.
The presentation covered two aspects of tunnel lining fire testing; first, the background to the parameters influencing tunnel lining fire performance, particularly concrete spalling; second, the types of test and assessment procedures that are used for common tests.
Part 1: Background to Research On Fires and Spalling
Why do we need fire testing?
Major fires have occurred in tunnels e.g Channel Tunnel, UK (1996, 2006, 2008, rail); Great Belt Tunnel, Denmark (1994, rail); Mont Blanc, Italy/France (1999, road), and the Tauern Tunnel, Austria (1999, road) to name but a few. Some even leading to significant fatalities and major costs due to structural damage. Following the immense consequences, steps must be taken to mitigate the risk.
Explosive spalling
This is a major issue for tunnel linings and the subject of much research. Explosive spalling leads to the loss of large sections of lining. The literature and experience gained over many years suggests that spalling is more likely where there is high moisture content, high concrete strength, rapid temperature increase or high levels of restraint (or applied load) – or any combination of these factors. In terms of structural design, standard design procedure considers fire to be taken into account by the concrete cover specified and the dimensions of structural elements. However, in other cases, where one or more parameters that influence spalling prevail, designers will need to consider a risk-based approach and take action, which might be testing or protection. One solution to spalling is to include polypropylene fibres in the mix but alternatives include fire barriers, boards, sprays, mix designs which minimise explosive spalling, and controlled environmental conditions.
Initial research on spalling
During the construction of Canary Wharf, Mr Lennon was involved in looking at high-strength concrete columns to create slender sections for the lower floors of buildings. High-strength concrete tends to have low porosity, low permeability and high density, and in a fire, these properties lead to a build-up of stress (a combination of pore pressure and thermal stress) which cannot be relieved. This makes the high-strength concrete susceptible to spalling. When polypropylene fibres were used to prevent spalling in 1997-1998, this was an innovative application of an existing technology which was used to prevent shrinkage cracking in slabs. Research was carried out for the UK government where several columns were subjected to axial loads using a 500t compression machine and standard fire exposure provided by a portable gas furnace.
The first tests were carried out on unreinforced columns (200 x 200mm x 1.5m high) with typical slenderness ratios and two strengths of C95 and C105 micro-silica limestone aggregate, with and without polypropylene fibres and applying either 40% or 60% of the ultimate load capacity. Out of the 30 specimens tested, only four remained intact of which three included polypropylene fibres. Even though polypropylene fibres were found to reduce, delay or eliminate spalling in high-grade concrete, the testing highlighted the importance of load ratio on the testing as none of the unreinforced columns loaded to 60% actually survived, regardless of whether polypropylene fibres were added. This showed that polypropylene fibres are not the ultimate solution to the problem and therefore all factors need to be taken into consideration.
For the reinforced columns, the same-size samples were used with strengths ranging from C45, C65, C85 and C105. Different polypropylene fibre contents were tested (3% and 6%) with a fixed moisture content of 3% and a compression load one third of the ultimate load capacity (ULC). The columns performed better, with no collapsed samples; residual strengths measured between 55% and 75% of ULC, with larger residual strength losses in those columns without fibres and with residual strength loss increasing with higher concrete grades.
The work undertaken for this testing programme was used in 2000 to produce the BRE guidance ‘Effect of polypropylene fibres on the performance in fire of high-grade concrete’. The work also inputted into the European Concrete project based on large-scale fire tests at BRE’s Cardington facility.
A fire test was carried out on the ground floor in a compartment 15 x 15m by 4.25m high which included one completely exposed internal column and eight partially exposed columns at the boundary, all reinforced and containing polypropylene fibres. No spalling occurred in the high-strength concrete, even though there was significant spalling in the normal concrete of the slab without polypropylene fibres, where after the fire exposed rebar could be observed.
Part 2: Fires in Tunnels and Explosive Spalling Tests
Explosive spalling is a major concern for tunnels where all contributing factors are present. Hydrocarbon fires can develop due to petrol tankers, which means the fuel load can be very high, with rapid temperature increase. Also, a tunnel is often constructed with high-strength concrete and there will be restraint against thermal expansion.
Given the nature of tunnel fires and the form of construction used, it is essential to ensure that the proposed design is capable of resisting a hydrocarbon fire. There is currently no standardised approach for the testing and approval of tunnel lining segments in relation to fire performance due to the wide range of circumstances present in tunnels, making each case vary. Some attempts have been made to produce standardised procedures which allow a certain flexibility in terms of the fire curve to be used. In 2006, EFNARC produced guidance titled ‘Specification and Guidelines for Testing of Passive Fire Protection for Concrete Tunnel Linings’.
Fire exposure is an important aspect to observe in tunnel fire performance. There are various fire curves (Figure 1) ranging from the normal standard curve to the other extreme – the RWS curve with temperatures of up to 1,360°C degrees. The most commonly used is the EUREKA curve with temperatures of up to 1,200°C degrees after five minutes and which holds for about 60 minutes, then decreases in the cooling phase. This is severe fire exposure but fairly representative of a real hydrocarbon fire.
Fire Testing Tunnel Linings
BRE has provided fire-testing services for a number of high-profile tunnel projects, including CTRL, Heathrow Terminal 5 and Hindhead Tunnel. This expertise provided input to Crossrail’s fire-test specification for sprayed concrete linings. Two different fire specifications were produced, one for pre-cast linings, the other for sprayed concrete linings; both required the use of the Eureka time curve. The specifications produced depend on the experience of the consultants who are employed to develop them. For testing Crossrail’s segmental lining, the specification was much more complex and more difficult to carry out and BRE could not undertake the test as specified.
The sprayed-concrete lining specification required an applied load of 5MPa and both small-scale test samples (250mm-diameter cylinders, Figure 2a) and large-scale test samples (1,700 x 800 x 450mm, Figure 2b). The small scale informed the concrete mix design to assess whether spalling was likely or not, before large-scale tests were performed. The performance criteria was based on the depth of spalling.
The temperature rise within and through the slab was measured to assess the impact on the waterproofing material and its melting point, and also the residual strength of the heated concrete. This was achieved by placing thermocouples at specific distances from the surface of the specimen (Figure 3).
Every specimen tested was at the same conditions and moisture content. Once the test was carried out, cores could be taken, a core log could be recorded and the strength profile through the depth was determined.
A good example of a test with and without the inclusion of polypropylene fibres can be seen in Figure 4.
Commercial testing uses loaded panels (1,500 high x 750 wide x 350mm thick) in a 500t compression machine exposed on one face to the hydrocarbon fire (EUREKA curve). Applying the EUREKA curve to the samples creates challenges for the furnace as it must reach 1,200°C degrees in five minutes and then lower the temperature to ambient after 170 minutes. This has proved impossible so the test recreates the closest possible to Eureka but cannot accurately achieve it, even though this is irrelevant in terms of the behaviour of the panel and the performance criteria.
When explosive spalling exposes reinforcement it has a massive impact on the tunnel’s structural performance. Some European companies offer an alternative to lab testing in which they bring the furnace inside the tunnel and carry out an in-situ fire test. Lessons learnt from Crossrail are being applied to the fire-testing specifications for tunnel linings on HS2, whether precast or sprayed insitu.
There is a need for standardisation which allows for flexibility depending on the specific circumstances of the project. The Crossrail SCL specification and current HS2 specification could provide a useful starting point to specifying a fire test and assessment methodology which is robust and does not impose an unreasonable financial burden on contractors.
Questions from the floor
Asil Zaidi, student, Warwick University: How does fire affect the gaskets in segmental linings?
It depends on the design. We measure temperatures through the depth and the extent of spalling. The actual impact depends on the lining thickness, the thickness of the pre-cast unit, the position of the waterproofed membrane and the different melting points of the constituent materials. We can make decisions only as far as we know the temperature distribution.
Rosa Diez, Mott MacDonald: As designers, we find it difficult to design to the Eureka curve, particularly considering that fire engineers regard Eureka as not representing fires that may occur in railway tunnels where you no longer have hydrocarbons. What are your views on using something different, or is there any other fire exposure that could be used?
I think that a different curve could be used where there is justification. In some cases it could be a standard fire curve, which is less severe than the Eureka curve, or it could be the Eureka but instead of going for 60 minutes you go for 30 minutes. But in any case, you need justification.
Is research or testing being undertaken to provide a more realistic fire curve?
I think most of it is done in terms of modelling because it’s very expensive to research large-scale tunnel fires. For hydrocarbon fires, which are fairly representative, most of the work is undertaken in terms of FDS modelling.
Neil Moss, GZ Consultants: At London Underground we specified 1kg/m3 of polypropylene fibres based on past testing. Is there any opportunity to reduce that or is it the appropriate number?
That is a difficult question. Eurocode 2, the concrete code, specifies that there should be at least 3kg/m3. I always thought that was a mistake because you want the minimum content that will give the performance you require and that will vary from condition to condition, depending on your mix design and on the fire exposure. So, in some ways, the optimum can probably only be decided by testing.
How did they arrive at 3kg/m3? Was that the number used for the tests?
In part, yes. That was written in Eurocode 2, published 2005, but the work that went into it was done before we did the Cardington tests. I would say, in general, that 3kg is too high, however I’m not sure there is much scope to reduce it much below 1kg/m3. If you are looking to optimise the dosage, you don’t need to go through the full loading test nor test actual-size panels. You could probably do some very good work on quite small panels – just expose them to the same fire curve. That might be cheaper and easier. We’ve done that for several clients in the past.
Charles Allen, independent consultant: I have issues with Eurocode 2 and the fire spalling part of it. On the Channel Tunnel we used 1kg of less than 32 micron (μm) fibres. Now you can get polypropylene fibres down to 12μm diameter and you are much better off with one kilo of that because you end up with more surface area than with two kilos of 32μm fibres.
I am part of the project team in charge of updating the fire part of Eurocode 2 which will be completely revised. It was first written when the concrete industry in general did not really deal too much with fire.
As far as I’m concerned, you picked a cover, you chose a dimension and that was all the fire engineering involved. Since then, after much work, we are better placed to offer more logical guidance than exists in the current Eurocode. There will be a new section on spalling.
One issue relates to the low strength achieved by concrete with 2kg of polypropylene fibres. A lot of air was entrained due to the surfactant on the fibres, and also because the volume and mesh of fibres within the concrete did not allow vibrating out the air, so we ended up with lower strength.
Steve Parke, consultant LTC: While at C300 Crossrail, we ended up with 1kg or just over but there was considerable testing of 2kg and 3kg, and they complained onsite because they could not mix the concrete.
Yes, above certain values it becomes impractical.
Asil Zaidi, student, Warwick University: Are the fibres there to provide air with an outlet to escape out of the concrete and so prevent spalling?
Yes
Would you suggest a volumetric system of dosing? Would the size of the fibre and orientation have an influence?
Yes, it does. The dispersal of fibres is important as is the ratio of surface area to volume. You can get different performances from the same dosage. It is a very complex issue.
John Greenhalgh, Bekaert: You could have 2kg or 3kg of the 32μm (or above) polypropylene fibre or you could have 1kg of a fibre which is only 18μm and the difference in volume is actually millions per kilo. Have you done any work to compare the performance under fire of the blend of steeland polypropylene-fibres in concrete, and polypropylene fibres with traditional steel cages?
All the work we have done in this area has been commercial work. We have tested both conventionally-reinforced linings and steelfibre linings. Steel fibres, to my knowledge, do not really give you any performance in terms of fire. What we normally test is steel fibre-reinforced concrete with polypropylene fibres.
Steel fibres control cracking with greater effect than traditional bar cages. In the first Channel Tunnel fire I believe the explosive spalling was due to the thermal conduit provided by the steel reinforcement cages. The loss of micro polypropylene was around 10-11cms and under the microscope you could see the micro voids. That is why I am curious about the traditional rebar cages.
John Murphy, retired: There are other things in tunnels that get hot, notably the road surface. Can you please comment on what happens to the tarmac road surface or to the fire doors when it gets really hot?
I don’t tend to get involved with issues such as means of escape, early warnings, toxicity and so on. I deal with structural fire engineering issues only.
Ivor Thomas, The British Tunnelling Society: Why do contractors cast segments then transport them to Holland or Germany for testing in fancy ovens when we can use firms in the UK and do the same with smaller panels? By specifying these tests in Europe we are exposing clients to quite considerable time risk.