To say the A86 motorway completion in western Paris has faced obstacles would be an understatement. The project has been jumping hurdles of all kinds since the early 1990s; financial, environmental, political, legal, safety, and technical and logistical problems. Mixed ground, from limestone to running sand, with three distinct water tables, are minor technical issues compared to the efforts required to get the project underway at all, says Pierre Boutigny, the project’s technical director for tunnelling “With a well designed TBM we can handle these things today.”
But high-powered planning challenges, European Court proceedings, and finally, the impact of the Mont Blanc tunnel fire, which has imposed major safety upgrades on the design, have all taken their toll. A fire inside the tunnel works early this year did not help.
The motorway was always contentious. Its 10km length will complete the outer ring motorway for Paris, which was mainly constructed in the 1980s, to complement the more famous inner Périférique. But western Paris is a special area. Once the preserve of aristocrats and kings, its small towns by the river Seine and rolling woodland are today favoured by film stars, politicians and financiers. Many historical buildings, including Versailles Palace, also sit close by. The answer to local and national road resistance was to create a tunnel said Cofiroute, a consortium of contractors and motorway operators (see panel). They proposed a privately funded scheme, not unusual in a country where the autoroute network is predominantly private and tolled. The scheme involves two tunnels, separating light from heavy traffic. It also proposes the first ever double deck tunnel for lighter vehicles.
A single large bore could handle the majority of the traffic volume, carrying northbound and southbound carriageways at different levels. This would reduce excavation costs but also raised numerous safety and psychological issues (see scheme box). Cofiroute argued the design was safe and eventually persuaded the French Government that it would solve the problems. In 1996 the scheme was given the go ahead and work began in 1997 on the portal area at Rueil Malmaison, on the portal itself and on muck handling systems. A conveyor loader for barges, using the river Seine was erected and a Herrenknecht TBM ordered.
However, the local towns and environmental groups were still not happy and challenged the scheme in the European Court at Brussels, alleging that it had been rushed through and did not fulfil competition regulations for open tendering. Work was stopped in early 1998 and hearings were held, with the court finally confirming the concession award. Rival contract giant Bouygues, which has its headquarters near by in the Versailles area, had also shouted “foul” but its appeal was dismissed by the Council of French State in 1999.
Work was able to restart finally in November 1999 and the TBM began the main drive in December 2000. However, by then the appalling fire disaster at the Mont Blanc tunnel had shocked the world, and most particularly the French government. The A86, as the most high profile road project in France, has inevitably been the target for safety concerns. Cofiroute has taken part in long negotiations with the government over the safety of its project, maintaining that its provisions already exceed those deemed necessary for the Mont Blanc renovation (see scheme box). Even so, it has had to make changes, most of these focussing on provision of side chambers and refuges; these will be doubled from the initial design, so that there is an escape point every 200m in the tunnel.
At present the main bore is under way for the first 4.5km long tunnel section, first of two phases for the light traffic tunnel which is the main A86 connector. This bore, the East Tunnel, will take the tunnel from Rueil Malmaison to a new interchange with the A13 Paris radial motorway, and then later a second 5.5km bore, driven from the south, will complete the full connection. The heavy vehicles tunnel, the West Tunnel, which at 10.9m internal diameter is slightly larger than the 10.4m id two-level tunnel, has been suspended currently. The Government is concerned more with this one because it has two way traffic and, obviously, because the heavy vehicles using it are more likely to be fire hazards. This tunnel was to go ahead more or less simultaneously, with a single 7.5km drive taking it south west to a junction with the A12.
Tunnelling on the East bore began in December 2000 using an 11.6m diameter, shielded Herenknecht TBM, originally ordered in 1996, says the project director Bertrand Vielliard, for contractor Vinci, part of the overall construction consortium. The machine is dual operation with both earth pressure balance and compressed air-tuned bentonite slurry modes, adds Boutigny, the latter intended to deal with the very fine Fontainbleu sands which will be met later in the drive. These are partly stable but in the presence of water “simply run” he says.
In the first 2.5km of the tunnel driven so far, the machine has mainly operated in EPB mode driving through a variety of grounds, starting with the Seine riverside chalk and climbing up through clay, limestone and limestone-marl with more clay to come and then the Fontainbleu sand (see Figure 2). None of this is especially surprising says Boutigny, pointing out that the Paris metro and railway tunnels mean that the Paris basin is very well understood. There was also an initial ground investigation and of course there has been time to contemplate. Boutigny is very happy with the TBM “It incorporates some features from the lessons we learned on the Cairo metro.” The only comment he makes is that the machine cutterhead’s 4000kW generates a lot of heat. “We need 200m³/hour of cooling water pumped through. It also uses 30,000 litres of hyraulic oil.”
As well as EPB, the machine is also used in an open mode where possible and sometimes pressurised foam is injected to condition the ground. Water is variable, coming from three different water tables, which are separated by the clays. For environmental reasons it is important that these do not communicate. Extra cement is used in the annular grouting mix behind the segments when passing through a transition, with the intention of maintaining the seal. Otherwise a fly-ash rich mixture is used behind the 2m wide seven segment and one key lining ring. Each segment has a two level seal, with an inner neoprene gasket and an outer Hydrotite seal. Segments are made at a works in Lyon where contractor Vinci, or rather its former component companies, worked on the tunnels for the city ring road project. They are transported by rail to the north of Paris and then brought to site by barge along the Seine. The operation is part of a carefully thought out logistical operation, designed to minimise the construction impact on the surrounding area by taking advantage of the riverside location. Mucking out goes the same way, by an REI supplied tunnel conveyor to a spoil handling area close to the river used to dry out the muck. It is loaded via a shorter conveyor gantry onto barges. A subcontractor handles disposal.
Work supplies come in below the bottom slab in rubber tyred supply trains. Logistics will become a lot more important later when the tunnel is fitted out. “We almost have two different jobs here” says Boutigny, “the bore itself and then the tunnel fitting and side passages.” Some of the fit-out is done behind the machine with a wheeled gantry, from which brackets and concrete stubs for the tunnel decks are installed. Just behind that, the lower road deck is fitted, using 2.6m long precast concrete panels, stretching the full 8.5m width of the tunnel. The units, made in the site yard, are lowered into position on bearings with a beam crane. “The lower deck is 300mm thick, more than ultimately needed for the car loadings” says Boutigny. “But we need it for the construction operations, to allow trucks and other equipment along the tunnel.”
Two more slabs have yet to go into the tunnel, and ventilation duct dividers, but before that the side passages must be created for top and bottom refuge points and the interconnecting stairways. “We will do those by NATM” he says. But the need to deal with groundwater and the fine sand, means that a range of stabilisation methods may be called for, including ground freezing. As well as technical difficulties there will be logistical problems. “There could be as many as ten side passages at various stages of investigation, excavation and fitting-out, at any one time.” During the Mont Blanc renovation, traffic jamed inside the tunnel as multiple work points were accessed, this meant that it could take a ready-mix concrete truck up to an hour to reach its delivery point.
Despite the recent fire, he is relatively pleased with the progress of the machine, which has made 14 rings a day on its best performance so far. While all this work is underway below ground four access shafts are being formed above ground, dropping a maximum 84m to tunnel level from small forest clearings in the parkland above the route. Ten shafts will be created for the whole 10km length, seven for emergency access and ventilation and three purely for ventilation. “These are quite conventional” says a young civil engineer, Philip Martin, who has been finishing his engineering training on the project. “The first one, now virtually complete, used a timber and lagging support with a conventional excavator for mucking out and the other two are being done with concrete diaphragm walls.”
Significant diaphragm wall construction is also underway at the end of the first drive for the TBM reception pit. The work here will be part of the new interchange, which has to be complete by 2005 when the first section is due to come into service. By that time the TBM will be underway on the second drive, working from the south after being disassembled and transported from the interchange point. Hopefully with purely tunnelling problems to contend with.
Related Files
Figure 2 – Longitudinal cross-section of the, 10km long, A86 East Tunnel, running from Rueil-Malmaison to Pont Colbert
Figure 1 – Map showing the location of the A86 East and West Tunnel alignments
Figure 3 – Cross section the tunnel showing the ventilation system and typical shaft, which also acts as an escape route in the event of an emergency
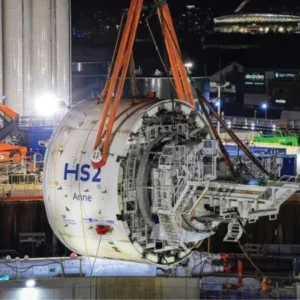