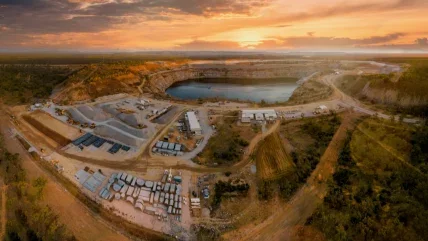
In a packed Godfrey-Mitchell Theatre, at the ICE headquarters in central London, Clare Önal gave details to the gathering on how the Kidston pumped storage hydroelectric (PSH) project, in Australia, was progressing. She also explained how the project is intended by developer Genex Power Ltd to be operated.
PROJECT BACKGROUND
The nearest major town to the Kidston pumped storage scheme is at Townsville, 270km away (about a six-hour drive). The disused surface mine complex is being repurposed as a PSH and clean energy hub accompanied by wind farms and solar farms.
Alluvial gold was officially discovered at the Copperfield River in 1907 (though maybe that is when word leaked out) and the township of Kidston grew from those beginnings.
When the alluvial deposits of gold ran out, excavation started with open pit mining from 1981 till 2001. The ore deposit was eventually reported as being over 40 million tonnes with an average grade of 1.8g/tonne. With the mine now abandoned, the energy vision for the open pit is for it to form the lower reservoir of the PSH project.
Pumped Storage Systems
PSH systems can only operate with very specific topography that requires large water bodies at high and low elevations.
The hydroelectric systems exploit the height – or ‘head’ – difference between the elevations to have water fall from the high level to the low, and on the way passing through turbines attached to generators. When bi-directional turbines are used, these are pumpturbines capable of pumping water from the lower reservoir back to the upper reservoir.
With the flow in each direction, up or down, there are hydraulic friction losses (‘head losses’). When water flows downwards, there is only a net head remaining at the turbines to generate electricity to send out to the power grid.
When the powerplant moves the mass of water back up, energy is taken from the grid, including extra to overcome the friction.
The benefit of having a choice of conveying a mass of water either up or down through the pipelines or tunnels at a pumped storage project site comes from electricity economics rather than physics. Having the water fall to generate electricity is more valuable at times of need in the power network, either to help meet demand or quickly stabilise the transmission grid. When demand is much less, so is the cost of taking electricity from the grid to pump the equivalent mass of water back up, ready for next time.
Usually, the upper and lower bodies of water are natural bodies of water or can be impounded. Rarely, other bodies are examined for possible use to hold water, like disused quarries or surface mines.
It can be that the position of the upper and lower reservoirs only require surface pipelines to run between them, linked to a surface power plant. But, in some locations, they need tunnels to join them to convey water flow, passing through turbines placed in underground powerhouses, in caverns.
The Kidston arrangement
In the case of Kidston, the renewable sources at the energy complex are solar power (50MW existing installed capacity with another 270MW in feasibility stage) and wind power (200MW in development). These will be used to supply electricity to pump water from the lower to the upper reservoir.
The lower reservoir is called Eldridge Pit and the upper reservoir is Wises Pit (see Figure 1). The Wises Pit then effectively acts as the ‘battery’ storing energy that can be released when energy demands peak.
At the detailed design stage, Mott MacDonald was working in a joint venture with GHD. The design JV was working for a construction JV of McConnell Dowell and John Holland, which has a contract with Genex Power. Andritz Hydro designed and supplied the pump turbine and associated hydromechanical equipment.
UNDERGROUND WORKS
Figure 2 shows the planned underground works for the Kidston PSH scheme. The spiral main access tunnel (MAT) drops about 200m at a gradient of 1 in 7 to the underground powerhouse caverns; the two intake shafts are 230m depth and 4m i.d. transferring water to the penstock chambers, which are 30m long reducing in section from 4m wide to 2.5m; the powerhouse cavern housing the turbines is 18m wide, 85m long and 45m high; the project also has a smaller transformer hall cavern; the two tailrace tunnels are 330m long, conveying the water out to the lower reservoir at Eldridge Pit.
For the underground works, Mott MacDonald carried out the permanent lining design of the two intake shafts, the penstocks, the transition, and the tailrace tunnels. Two smaller shafts were chosen rather than one single larger shaft, enabling them to be excavated by raise bore method. Beyond the construction phase, having two shafts also allows some flexibility for maintenance and continuous operation during the long life of the facility.
The geology at the project site comprises undifferentiated gneiss of the Einasleigh Metamorphics with a UCS of 90MPa. The design is based on Q system with generally good rock conditions with a relatively low permeability (in the order of 2 x 10-8 m/s).
The penstocks are to be constructed by drill and blast method and then the two shafts by raise bore from the end of the penstock tunnel. The shafts will have the primary lining installed and then a slipformed cast insitu concrete for the secondary lining.
Some of the critical checks for hydroelectric schemes include confinement to ensure the minimum in-situ stress in the rock mass is greater than the internal pressure applied to the structure. This was checked during the design, based on the results of the geotechnical investigation and found to be satisfactory.
Another check is the hydraulic gradient, where minimum distance from any point where the internal water pressure is present to the nearest point of atmospheric pressure is determined. This provided the length requirement for the steel liner (see Figure 3).
The primary purpose of the secondary lining is to provide a smooth surface to minimise head losses and therefore to minimise energy, and so economic, loss for the system.
The upper 209m of the intake shafts are reinforced with 250mm thick concrete lining containing macrosynthetic fibres with no steel reinforcement bars. The design takes account of ground, rock wedge and grouting loads plus localised water pressure if any water bearing faults are encountered. Weepholes are placed at 3m maximum staggered spacing.
The steel lining was checked for being both empty with external water pressure, and full with static and transient pressure as well as the shipping and handling loads during placement. The load sharing capability of the rock mass reduces approaching the cavern, and so the thickness of the steel liner ranged from 18.5mm to 26mm depending on the load cases along the penstock. There was also a corrosion allowance included in the thickness calculation.
As the water flows out of the powerhouse, having generated electricity, it exits through a rectangular draft tube which transitions into horseshoe-shaped discharge tunnels.
Due to the upward inclination of the tunnels, there is still a head of water pressure, though not as high as at the intake tunnel but it is still under pressure. The tunnels are inclined upward because the turbines in the powerhouse need to be submerged to prevent cavitation pitting on their steel blades.
This arrangement is more notable than with conventional surface hydroelectric power facilities because of the reversible nature of pumped storage schemes and even more so for Kidston because of the large variation in water levels.
Therefore, being under pressure, the area downstream of the powerhouse cavern at Kidston also has to be steel lined to minimise the hydraulic gradient. The draft tube-to-tailrace transition steel liner (see Figure 4) was designed taking account of the complex change in geometry over a distance of only 10m, where the length was minimised based on the hydraulic gradient requirements.
The steel transition structure was modelled in 3D using STRAND7. The steel plate is 25mm thick with stiffeners and webs and thicker 40mm plate locally for the corner sections. The weight of each transition piece is about 60 tonnes and will have to be transported in three pieces and welded on site. Mass concrete will then be placed between the liner and excavation.
The twin tailrace tunnels are 330m long, on gradients of 1in 8, inclined upwards from the powerhouse to the lower reservoir at Eldridge Pit. The tunnels pass through the same undifferentiated gneiss rock mass as at the intake tunnel, although the tailrace passes through some faults and the rock mass changes into a weaker breccia towards the Eldridge pit. Less favourable rock parameters are used for this section.
The tailrace tunnels will be constructed by drill and blast methods, with a primary lining and then fibre reinforced cast in-situ concrete for the secondary lining, again with no bar reinforcement.
At the time of the presentation the main access tunnel was under construction, having started in 2022 and was approaching the powerhouse location (see Figure 5).
The Wises Pit (upper reservoir) is under preparation, including the area where the intake shafts will be constructed and the Eldridge Pit (lower reservoir) is being pumped out for construction access.
Construction of the Kidston PSH scheme is due to be completed in 2024 with electricity generation scheduled to start in 2025.
In terms of sustainability, the project is re-purposing existing infrastructure, and hydroelectric energy storage schemes of this nature have a long design life compared to battery storage. The project has a design life of 50 years and is believed to be the first that uses off-river solutions by re-using the same water minimising impacts on the local river system.
Using a combination of mixed renewables, the project will produce enough energy to power 143,000 homes for at least six hours through a single cycling of upper reservoir emptying.
Looking ahead, according to the Australia Renewable Energy Agency (Arena) there are about 20,000 potential sites around Australia that could be adapted in a similar way and if only a fraction of these were converted to PSH then Australia would be well on the way to complete renewable energy.