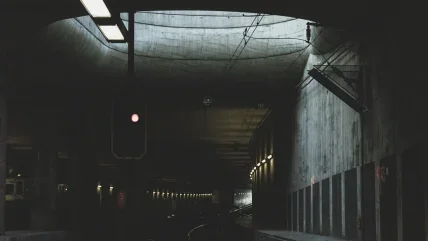
So-called "mega machines" populate today’s headlines and captivate imaginations with their sheer size and complexity. Viewpoints surrounding the concepts of large diameter EPBs and their trends, together with the politics and logistics involved, can be dif_ cult to gage. The changing face of large-scale EPB tunneling is a complex one: "What is a large diameter machine? Ideas about this are evolving.
A 10m machine is a big machine, but it is no longer considered large diameter. Machines in the 12 to 14 m range are now considered large, and machines over 14 m are considered very large," said Brad Grothen, Engineering Manager for Robbins, who has worked on and designed large TBMs worldwide. It is not only industry perception that is evolving, though — new design concepts, logistical considerations, and technologies that push the limits make this one of the most exciting topics in the tunneling industry.
Large scale trends
Most in the industry would agree that we are seeing a trend towards larger diameter machines for all types of ground, from hard rock to soft ground under water pressure.
"There appears to be some competition in the industry to make machines bigger and bigger," observed Steve Skelhorn, Project Sponsor for contractor McNally Corporation, who has worked on dozens of EPBs in his career.
Consultants surveyed for the article agreed that with the current suite of projects under consideration, large diameter machines (over 14m) would remain a trend. They found this particularly true for road tunnels and combination road/railway tunnels. However, the vast majority of new tunnels being proposed were predicted to remain medium sized (9 to 13m range).
"I believe acceptance of these machines as a tunneling tool is increasing, but there has to be sufficient portal area for assembly and support. In my opinion the main market for them is in highway, rail, and water projects," said Paul Zick, Project Director for Obayashi Corporation.
Shinichi Konda, Robbins’ chief EPB engineer, was measuredly optimistic when considering the large diameter trend: "In Japan in particular, they are politically becoming more popular. To manufacture two smaller machines with two shafts is very expensive and can take up a lot of space. In this instance it is beneficial to use one larger machine with one shaft to take up less space." While EPBs over 14m have been used in Japan since the 1990s, they are gaining more traction due to the country’s unique land rights regulations.
Konda made mention of a particular project known as Gaikaku, or the Tokyo Outer Ring Road Project. The tunnel can only be constructed below city streets with 16m width, as residents and businesses own land down to a 50 m depth in the country. As such, three different TBM manufacturers are currently building a total of four 16 m EPB machines for the tunnel project, which measures 16.2 km in total length.
Open space: design considerations for mega TBM’s
The design possibilities that open up with large machines are, like the rest of the machine, bigger. "The larger diameter just provides more overall room — if you have a hybrid machine for example, there is more area to work with in terms of changing out cutting tools in the cutterhead and having multiple mucking options in place, such as both a screw conveyor and belt conveyor," said Grothen. Other advantages of the extra space include the ability to dock with the man lock using a pod, allowing for transport in emergencies and for decompression if saturation diving is needed.
For Grothen, the back-up system is another area that sees dramatic design frontiers open up at large diameters. "There are road elements that can be brought into the design, such as precast concrete inverts for rubber-tired vehicles. Castin- place concrete linings can be used. There are a lot more options for parallel construction."
Other systems are simply sized up — two screw conveyors for example, and double segment erector arms to place segments at a more continuous pace. All of the extra space and technology does require extra crew, more logistical planning, and more action plans in place should equipment malfunction.
"Many of the added features are really about risk mitigation. The risk of operating a large machine increases as the area of the excavation face increases," said Grothen.
Changing cutters
For most consultants surveyed, a distinct advantage of large diameter EPB design is the ability to enter the cutterhead spokes in order to change cutting tools at atmospheric pressure. Some cutter change systems allow for continuous flow through of the muck, but these types of cutterheads are often deep in their design, and the passage canals for cutting tools face the risk of becoming blocked by excavated material.
Another type of system, touted by Robbins as the RACCS (Robbins Atmospheric Cutter Change System), offers a solution to the problem of clogging. The flow-through design is currently in development, and requires cutterhead spokes that are completely sealed off inside and large enough for a worker to crawl inside. Disc cutters are mounted on moving sled structures that are separated from the inner and outer cutterhead structure using two gates. Gates can be lifted to move the cutter forward or retract the cutter backward.
While boring, the cutter is in an advanced position with both gates up. When a crew member wants to change a cutter at atmospheric pressure, the front gate is closed and the cutter is retracted into the chamber. The design is unique in its use of two gates. "We want to eliminate or prevent the chance of cutter structures clogging in tough ground conditions. Our design has an open back behind each cutter that allows muck to continually flow through it," said Grothen. Engineers are currently building a large test fixture for this system, which will analyze how RACCS reacts in sand, gravel, boulders, clay, and mud conditions under pressure.
Limitations on large diameter machines
Along with all of the design possibilities on larger machines come some limitations. In some cases these challenges can be mitigated with extra monitoring and equipment, and in other cases they are simply a function of the large-scale excavation taking place."You can go bigger, but at some point you do start to run into logistical problems, such as bigger, heavier pieces, gaining access to the site, larger cranes, and just finding the precision tools that can make very large parts," said Grothen. He added that the operation of the machine itself was not necessarily affected by the large diameter, and that slurry machines were even less subject to size limits. "In slurry machines, power requirements are not as great, the thrust required is not as much, and the machine is lighter overall. These machines could definitely go bigger."
The larger parts can cause another potential issue, though not with the technology: "Cost is certainly a factor. When you have a very large diameter main bearing, you must split the bearing during the manufacturing process. This can wind up being much more costly than a standard main bearing. You are also limited by the number of suppliers that can manufacture such a large item," said Konda.
Another limitation is the pressure differential as size increases — the earth pressure at the bottom of the cutterhead will be different from the pressure at the top. While the differential in itself is not problematic, and can’t really be helped, there are issues with maintaining material flow through the chamber at very large sizes.
The challenge, according to the consultants interviewed, is to eliminate "dead" zones where material comes to halt, which reduce the space available for flowing materials and increase wear inside the excavation chamber and cutterhead. Such additional mechanical measures like independent and actively driven mixing devices may be required.
To further ensure good muck flow, the consistency of the conditioned material has to be closely monitored and controlled. This requires additional monitoring as well, such as temperature and density monitoring in several sections of the excavation chamber.
Other factors also come into play with a large cutterhead, which may require additional monitoring: "With a very large TBM there exists a very large pressure drop from top to bottom of the face, which in turn will have an impact on the bearing sealing systems. Grease and oil injection to the seals presents challenges due to these large differential pressures and intervention work," said Skelhorn.
Maintaining good control of foam additive at the face can also be difficult, as the geology often differs across a large excavation face. "A foam system is a good solution for ground conditioning, however the quality of the foam depends on the pressure," said Konda. "If an operator bases the concentration of the foam on the pressure at the center of the cutterhead, then there will be too much foam at the top and too little foam at the bottom." Solving the problem requires an awareness of the pressure differences and can be helped by independent foam lines.
New wave of Technology
Despite increased need for monitoring, the future of large diameter EPBs is a bright one.
"Designers are realizing that if you increase the diameter of a tunnel by just a small amount, the cross sectional area can multiply to become quite significant. This is particularly attractive for road tunnels. A large diameter machine in this case can be a good solution," said Grothen. The machines also offer a quicker construction solution compared with building two tunnels at smaller diameter. "The speed of excavation and ability to control the quality of the finished product with parallel construction are definite benefits," said Zick.
The technology involved in large diameter EPBs is ever evolving. Japan is again an innovator of new concepts that could help to usher in a robust era of large diameter excavation. Konda mentions new designs being tested out in Japan, which include bolt-less segments that have no bolt pockets on the I.D. of the segment and require no secondary lining — a technology that could potentially make the construction of very large diameter tunnels much quicker.
Also of particular importance in Japan are non-circular machines. In a country where all muck must be sent to a plant to be treated regardless of the type of ground or additive used, eliminating extra muck removal is a plus. In traffic tunnels, which are ultimately rectangular in shape, a method known as the Multi-Micro Shield Tunnel (MMST) has been developed. The method involves excavation by numerous small rectangular shield machines, with adjacent sections being linked together by reinforcing bars. The excavated ground is then filled up with concrete to form the outline of a large rectangular tunnel. Afterwards, the soil within the internal section is excavated. The net result is a large tunnel of rectangular or square shape with no extra muck required for removal.
Whether or not non-circular machines make their way outside of Japan remains to be seen. One thing about the future of large diameter EPBs is for sure, however: They will remain a fixture in the tunneling industry, and an option for large scale projects worldwide. For Zick, and for many in the industry, the trend is a positive one: "I think the future is very promising. In the U.S. alone, there are several very large diameter projects in the planning and design phases. The industry benefits from having large diameter machines available as an option."