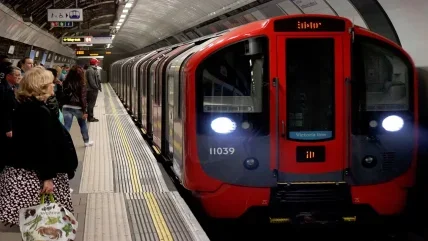
The evaluation of the structural response of grey cast iron (GCI) tunnel linings poses significant challenges due to the presence of bolted joints affecting the stiffness of the structure. Current methods of structural analysis fail to account adequately for the behaviour of the joints and their effect in the overall structural response.
This paper introduces recent advances in the development of new methods for the structural analysis of these tunnels.
First, a new set of bending stiffness reduction factors were derived based on the results of an extensive numerical parametric study; these can be readily applied in routine engineering calculations. Subsequently, the rotational behaviour of a prototype tunnel joint geometry was fully characterised for the first time, enabling the development of a new model for simulating the mechanical response of GCI tunnel joints.
Additionally, the analyses provided new insights into the effects of removing the bolts and tightening the bolts to different extents on the joint response.
INTRODUCTION
There are hundreds of kilometres of deep tunnels belonging to the London Underground (LU) metro network that were constructed with GCI linings. With an increasing number of underground structures being constructed in proximity to these tunnels and the absolute necessity to protect their serviceability, adequate methods of predicting their structural response are needed more than ever.
This paper summarises some of the findings and methods established by the Author for the structural assessment of GCI tunnel linings during his recently completed PhD studies (Ruiz López, 2022).
GCI linings were constructed as a succession of rings to form a tunnel, each ring comprising several segments. Rings and segments were bolted together at circumferential and longitudinal joints, respectively.
The segments have a U-shaped cross-section formed by the skin and the circumferential flanges with the longitudinal flanges closing the segments at both ends. The use of bolts in the longitudinal flanges was possibly aimed at preventing excessive opening of joints (i.e., separation of segments) which can nevertheless occur (Thomas, 1977) and is thought to reduce the stiffness of the structure. Due to uncertainties in the mechanical behaviour of the joints, the stiffness of the tunnel lining is largely unknown which constitutes a fundamental barrier to achieving meaningful structural analyses.
An experimental investigation into the behaviour of a half-scale GCI ring was conducted at Imperial College London (Yu et al., 2017; Afshan et al., 2017) was aimed at overcoming these limitations – see the laboratory set-up shown in Figure 1. The investigation provided valuable insights into the impact of the joints on the structural response. Moreover, the availability of the experimental results motivated the development of a competent 3D finite element (FE) model replicating the laboratory setup (Ruiz López et al., 2022) and which constituted the starting point of the research described here.
The FE model, developed in the program ICFEP (Potts & Zdravkovic, 1999), was employed subsequently to characterise the behaviour of joints and to evaluate systematically the influence of the joints on the structural response. The investigations are described below.
In this paper, a new methodology is introduced – based on bending stiffness reduction factors, to incorporate the influence of joints in preliminary assessments of GCI tunnel linings. The comprehensive characterisation of the rotational behaviour of a prototype joint is described subsequently. Lastly, the effectiveness of removing the bolts and tightening the bolts as mitigation measures for existing tunnels is evaluated.
PRELIMINARY ASSESSMENTS ACCOUNTING FOR THE JOINTS
Segmental GCI tunnel linings are frequently analysed as continuous (non-jointed) structures using analytical models, such as the elastic continuum model (Duddeck & Erdmann, 1985). In those instances, TfL (2017) recommends starting the structural assessment assuming the full circumferential bending stiffness of the tunnel ring (rigid ring) and changing to a reduced bending stiffness (flexible ring) should the initial assessment fail.
Although TfL (2017) does not specify what reduced bending stiffness should be adopted, it is common practice in industry to employ the reduced second moment of area proposed by Muir Wood (1975). The latter does not consider the nonlinear behaviour of tunnel joints with respect to compression stresses and ovalisation levels and, consequently, its applicability to GCI tunnel linings is somewhat tenuous.
Considering the limitations of existing methods, a new set of bending stiffness reduction factors () were derived, based on an extensive numerical investigation replicating the assumptions of the elastic continuum model. The new reduction factors are presented here in a series of design charts, allowing their straightforward application in routine engineering practice.
Methodology
The segmental GCI ring considered in the analyses was based on those of the Central Line’s 11ft 81/4in (3.562m) running tunnels which can be considered as standard for GCI tunnels in the LU network. Each ring was formed by six segments and a smaller key segment (which was omitted for simplicity). The joint arrangement was the typical adopted in the first few decades of construction of the LU system with the longitudinal joints aligned between rings (i.e. allowing the analysis of a single ring to investigate the whole tunnel response) and one of the longitudinal joints located at the crown (see Figure 2a).
The 3D numerical model followed the methodologies adopted to successfully simulate the experimental tests mentioned above (Ruiz López et al., 2022); Figure 2b presents the FE mesh employed in the analyses. Symmetry conditions were applicable and so it was only necessary to simulate a quarter of the circumference and half the segments’ width, as shown in Figure 2b.
The soil stresses were applied via normal and shear stresses acting on the extrados of the ring. The magnitude of the total vertical stress v was based on the tunnel depth being considered by assuming that the full overburden stress was acting on the tunnel lining. As recommended by Tube Lines (2007), the ratio of the total horizontal stress to vertical stress h/v was taken as 0.7. Adopting a h/v<1 implies that the tunnel ring would deform into squatting (i.e. enlargement of the horizontal diameter along with shortening of the vertical diameter) which is consistent with field observations: Wright (2013) reported that measurements from circularity surveys across the ‘Tube’ indicated that tunnels generally squat between 0.5%-1% of the diameter.
Regarding the interface conditions between the extrados of the lining and the surrounding ground, full bond conditions were simulated with normal and shear springs acting all around the extrados whereas normal springs only were considered for tangential slip conditions. The magnitudes of the spring stiffnesses were adjusted for the numerical model to reproduce the behaviour of the elastic continuum model. Prior to the application of the soil stresses a bolt preload corresponding to 25% of the yield load was applied.
The self-weight of the tunnel ring was neglected, in accordance with the elastic continuum model. The stress-strain behaviour of GCI was simulated with an appropriate elasto-plastic model. The stiffness and strength parameters of the interface between segments and the bolting system were based on those established in the analyses of the experimental results. The value of the springs simulating the soil reaction was varied parametrically for each combination of tunnel conditions to investigate the influence of the joints under a range of ovalisation levels.
Six parametric studies were conducted, each adopting a different combination of tunnel depth (10m, 20m, and 30m), and soil-tunnel interface condition, adopting either full bond or tangential slip. The same analyses conducted on the segmental ring were conducted with an equivalent continuous ring (i.e. without joints) in order to make comparisons between the two sets of analyses.
Derivation of bending stiffness reduction factors
Figure 4 presents the results from the analysis adopting full bond conditions in terms of bending moments (kNm) at the crown and springline (see Figure 2a), with the tunnel squat (% of the internal diameter) for the three tunnel depths considered. The crown and springline are the sections where the maximum positive (tension at intrados) and negative (tension at extrados) bending moments, respectively, occur and therefore are the most critical sections in terms of the assessment of internal forces. Each pair of data points, corresponding to the crown and springline, for each squatting level were obtained from a single analysis.
The figures also include the elastic continuum solution for the full bending stiffness (continuous rigid) and the reduced bending stiffness (continuous flexible) as defined by Muir Wood’s (1975) formula. The latter gives a reduction factor of 0.444 for a tunnel lining with six longitudinal joints.
By comparison with the continuous rigid ring result, it can be observed that the segmental ring exhibits a reduction in bending stiffness that becomes more prominent with the squatting magnitude. This is a result of the increasing opening taking place at the intrados of the crown/invert joints which, being subjected to positive bending, are more prone to opening than the other joints, i.e. the segment’s U cross-section requires a larger bending moment to reach zero stress at the extreme fibre under negative bending.
Although the stiffness reduction affects the global response of the ring, the impact of joint opening is mostly local and more exacerbated around the crown joint where the bending moments start deviating from the continuous rigid solution at tunnel squats of about 0.15%, 0.25% and 0.35% for tunnel depths of 10m, 20m, and 30m, respectively.
At the springline, which is the section farthest from the joint undergoing opening, the bending moments are similar to those of the continuous rigid solution up to squatting levels of around 0.4%, 0.7% and 1% for tunnel depths of 10m, 20m, and 30m. It is evident that the segmental ring shows a stiffer response the deeper the tunnel, which is related to smaller joint openings with increasing compression.
The tunnel response is stiffer than that predicted adopting Muir Wood’s (1975) reduction factor for all tunnel depths, even at squatting levels greatly exceeding the range typically observed in the field (0.5%-1%). This suggests that the application of Muir Wood’s reduction factor can result in non-conservative estimates when assessing the internal forces of a segmental GCI lining. Similar conclusions can be obtained for the cases with tangential slip conditions.
As an alternative to the standard methodology of adopting either a rigid ring or a flexible ring following Muir Wood’s formula, a new set of bending stiffness reduction factors were derived from the numerical results. As explained above, the extent of the stiffness degradation varies with the tunnel squatting level and the location around the ring and consequently, three reduction factors varying with squatting magnitude were proposed for each tunnel depth and soil-tunnel interface condition: two of them representative of the stiffness reduction taking place at the crown/invert and the springline, which provide the upper and lower bounds of a ring’s bending stiffness and a global reduction factor which represents an average measure of the bending stiffness all around the ring.
Figure 5 presents the charts displaying the reduction factors for different tunnel depths with full bond and tangential slip conditions. The reduction factor at the crown _c was determined as the ratio between the bending moment given by the segmental ring at the crown and that given by the continuous rigid ring solution
for the same tunnel squat:
1.
Similarly, the reduction factor at the springline s was established as:
2.
where and
denote the bending moments at the springline from the segmental ring and the continuous rigid ring, respectively. The global reduction factor ng was defined as the ratio between the bending stiffness required for a continuous ring to match, for equal soil stiffness, the tunnel squat of the segmental ring and the bending stiffness of the segment cross-section. The abovementioned bending stiffness of the continuous ring was obtained from the expressions of the elastic continuum model provided by Duddeck and Erdmann (1985) for the radial displacement due to non-isotropic loading.
The reduction factors depicted in Figure 5 can be applied in preliminary assessments of potential damage of GCI tunnel linings to consider the influence of the joints on the structural response. In such assessments, the reduction factors c and s can be applied to determine the tunnel’s present-day bending moments, corresponding to an assumed or measured tunnel squat, at the crown/invert and springline sections, respectively. Likewise, these two factors can be used along with the elastic continuum model in assessing the changes of bending moments of an existing tunnel corresponding to given ground movements caused by nearby construction. The global reduction factor can be applied to the bending stiffness of the tunnel lining in numerical analyses focused on assessing the movements of an existing tunnel subjected to new solicitations.
ROTATIONAL BEHAVIOUR OF LONGITUDINAL GCI TUNNEL JOINTS
Even though the advanced 3D numerical model shown in Figure 2b can reproduce the behaviour of segmental GCI rings as observed experimentally (Ruiz López et al., 2022), it is impractical for geotechnical numerical analysis where the tunnel lining is usually simulated as a beam or shell and where 2D plane-strain conditions are often applicable. The need to consider the segmental nature of GCI tunnel linings in geotechnical numerical analysis prompted the development of a new model able to represent the nonlinear rotational stiffness of the joint using 2D beam elements.
In order to develop the new joint model, detailed knowledge of the rotational behaviour of GCI tunnel joints was required. While some insights into the rotational joint behaviour had been previously obtained from experimental (Thomas,1977; Tsiampousi et al., 2017) and numerical investigations (Li et al., 2014; Tsiampousi et al., 2017), these studies only examined the behaviour of the joint under zero compressive axial force and hence did not provide the required information for developing the model.
Ruiz López et al. (2023a), however, conducted a comprehensive characterisation of the behaviour of two joint geometries, those corresponding to the prototype 11ft 81/4in (3.562m) running and the 21ft 21/2 in (6.464m) station tunnels, considering the effect of different compression levels, under positive and negative bending. Only the results from the 11ft 81/4in running tunnel are discussed in the following.
The adopted 3D numerical model was similar to that illustrated in Figure 2b in most respects apart from including only the joint at the crown section.
The loading sequence comprised three steps: the bolt preload; the confinement load; and, the bending load. The magnitude of the bolt preload was taken as 25% of the bolt load at yield; the influence of varying this magnitude was also investigated, as explained in the next Section (Influence of removing bolts and bolt preload on joint response). The confinement load consisted of a uniform normal stress acting all around the extrados of the ring and subjected the joint to a compressive axial force. Stress magnitudes corresponding to the full overburden acting at tunnel depths of 6m, 12m, 24m, and 48m, respectively, were considered in different analyses and kept constant throughout each of them. Lastly, the bending moment/ rotation at the joint was imposed via a vertical load, acting downwards for positive bending and upwards for negative bending, applied across the width of the segment at a certain distance from the joint.
Figure 6 presents the bending moment-rotation (M- ) curves for positive and negative bending, rotation being defined as the relative rotation between two tunnel segments, as shown in Figure 3.
Firstly, the rotational stiffness, i.e., slope of the M- curve, of the joint gradually degrades with rotation from the onset of opening up until the curves reach a plateau which can be considered the end of the joint capacity. The rotational behaviour of the joint exhibits an obvious dependency on the compression level, the bending moment causing opening and ultimate bending moments both increasing with tunnel depth. Due to the asymmetry of the cross-section around the centroid, the joint behaves very differently under positive and negative bending.
Consistent with the observations made in the latter part (Derivation of bending stiffness reduction factors) of the previous Section, the bending moments causing opening are larger under negative bending for all tunnel depths. In relation to the ultimate bending moments, they are larger under positive bending for tunnel depths of 6m and 12m whereas the opposite is found for the
deeper tunnels. This trend is explained by the greater contribution of the bolts to the ultimate bending moment under positive bending prevailing in the lower range of tunnel depths, whereas the larger contribution from the axial compressive force under negative bending becomes dominant for the deeper tunnels.
The M-θ curves converge to the plateau more rapidly under negative bending due to the three bolts becoming active concurrently under this bending mode, while under positive bending the middle bolt develops tension only after yielding of the two outer bolts. The latter feature was also observed in the laboratory tests conducted by Afshan et al. (2017).
The horizontal lines included in the two plots of Figure 6 refer to the maximum capacity of the joint, for each tunnel depth, assuming that the three bolts reach their ultimate tensile load and that failure in compression, due to the contact force between segments, does not occur. It can be observed that the ultimate bending moments are generally close, particularly for negative bending, to the magnitude predicted by the maximum capacity.
The slight drop of bending moments observed in the M-θ curves for positive bending (see Figure 6a) as they approach their plateau is related to the propagation of tensile failure of GCI across the circumferential flange and skin, adjacent to the longitudinal flange. The darker coloured areas in Figure 7 indicate plastic tensile strains larger than the plastic strain at peak strength (0.55%) and therefore undergoing softening. Even though extensive areas of the longitudinal joint experience softening, as shown in the contour plots of Figure 7, complete breakage of the flanges did not occur and the bolts did not fully soften. Lastly, failure of GCI in compression did not generally occur in either of the two bending modes.
The characterisation of the joint rotational response informed the development of a new joint model to be adopted in geotechnical numerical analysis (Ruiz López et al., 2023b). Details of the formulation of the joint model are not provided here but it is worth mentioning that the new model incorporates the dependency, shown in Figure 6, of the joint response on the axial force and the gradual stiffness decay from opening to ultimate conditions. The new development enables the nonlinear behaviour of segmental GCI tunnel linings to be incorporated in geotechnical analysis.
INFLUENCE OF REMOVING BOLTS AND BOLT PRELOAD ON JOINT RESPONSE
Undoing or tightening the bolts of GCI tunnel joints are commonly adopted measures (Kimmance et al., 1996; Moss & Bowers, 2005) to protect existing tunnels from developing excessive internal forces or deformations when subjected to new solicitations. While the adoption of such measures is based on several decades of experience in constructing close to LU infrastructure, their effectiveness is yet to be clearly demonstrated. A series of analyses, following the same set-up discussed in the previous Section (Rotational behaviour of longitudinal GCI tunnel joints), were conducted with an aim of gaining further insights into the effect of removing the bolts and applying different bolt preloads on the joint rotational response.
First, analyses for a tunnel depth of 48m under each bending mode were carried out having removed the bolts from the 11ft 81/4in tunnel joint geometry. Figure 8 shows the M-θ curves obtained in those analyses along those derived from the analyses with bolts for the same tunnel depth (already shown in Figure 6). It can be observed that the early part of the M-θ curves is very similar regardless of whether the joint has bolts or not, which can be explained by the bolts being mobilised only after certain joint rotation. The effect of removing the bolts becomes evident thereafter.
The magnitude of the ultimate bending moments is significantly reduced when the bolts are removed; the differences are most significant under positive bending as the action of the bolts is more relevant in this mode. It is also evident that the joint reaches its ultimate bending moment more rapidly when the bolts are removed.
In relation to the potential for tensile failure of GCI, analysis gives the distribution of the maximum principal plastic strain at the end of the analysis under positive bending. The extent of the region where plastic strains occur (coloured area) and the magnitude of these are considerably less than those observed in the analogous analysis with bolts (see Figure 7). The magnitude of the tensile plastic strains (<0.083%) is far from that required to cause failure of the material (0.55% as defined in the numerical model). These results suggest that the possibility of tensile failure around the longitudinal flange can be safely neglected when the bolts are removed and so that this can be an effective measure to protect the structural integrity of the tunnel.
As explained above, tightening the bolts of GCI tunnel joints is a common practice to minimise the potential tunnel deformations resulting from new construction adjacent to the tunnel. It is therefore instructive to consider the effect of bolt preload magnitudes different than that considered so far (25% of the load at yield).
The rotational response of the joint is assessed below for a tunnel depth of 12m with bolt preloads of 12.5%, 25%, and 50%, respectively, of the tensile load at yield. Figure 9 presents the M-θ curves given by the analyses with different bolt preloads. First, it can be observed that the effect of the bolt preload is apparent only after certain joint rotation has taken place, which is similar to the observations made above in relation to the effect of removing the bolts. The bending moment causing opening is therefore not affected by the bolt preload which is consistent with the experimental findings of Yu et al. (2017). Once the bolts are mobilised, the M-θ curves exhibit a stiffer response with larger bolt preloads.
While modest differences are found between the three analyses under positive bending they are more prominent under negative bending. The primary reason for the different impact of the bolt preload is that, under negative bending, the three bolts of the joint are engaged concurrently, whereas under positive bending the middle bolt is only engaged once the two outer bolts have failed in tension. In short, the numerical results indicate that tightening the bolts might be an effective measure for stiffening a tunnel ring only when the latter is to be subjected to loading conditions where the joints open under negative bending.
CONCLUSIONS
This paper summarises recent developments in the structural assessment of GCI tunnel linings.
A new methodology, based on bending stiffness reduction factors, allowing the influence of longitudinal joints to be incorporated in simple structural assessments was introduced first. Upper and lower bound reduction factors were proposed along with a global factor representative of the average stiffness reduction taking place around the ring. These factors varied with the tunnel ovalisation, tunnel depth and the adopted soil-tunnel interface condition. They were presented in the form of design charts allowing their application in engineering practice.
The rotational behaviour of longitudinal tunnel joints was extensively investigated subsequently. The main outcome of the investigation was the derivation of a set of M-θ curves corresponding to different compression levels for each bending mode. The novel characterisation of the M-θ response informed the development of a new joint model allowing the nonlinear behaviour of segmental GCI linings to be simulated in numerical geotechnical analysis.
Additional studies revealed that removing the bolts from the joint can prevent tensile failure of GCI under positive bending and that a larger bolt preload only increases the joint stiffness significantly under negative bending.
These insights can be considered when deciding about potential protective measures of existing tunnels subjected to new solicitations.
ACKNOWLEDGEMENTS
I would like to thank my PhD supervisors Dr. Katerina Tsiampousi and Prof. Jamie Standing for their guidance and support in conducting the research discussed here. I would also like to thank Prof. David Potts for his help with some of the computational aspects of the project.
The PhD project was funded by EPSRC through a Doctoral Training Grant (EP/R512540/1), and their support is greatly acknowledged.