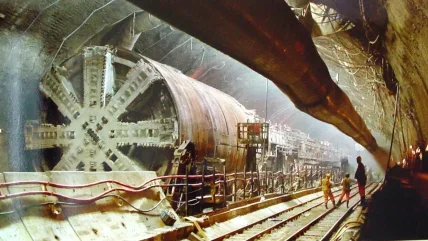
INTRODUCTION
This article is a personal review concerning the development of earth pressure balance (EPB) tunnelling and especially concerning the research and development of soil conditioning additives over the last two decades. It does not claim to be complete and all-embracing, and only highlights some important steps and encourages innovation to drive forward.
Innovation is necessary to bring new solutions to the market – making tunnelling overall cheaper, more efficient, more secure and also more environmentally friendly. This cannot be driven forward only by the chemical suppliers – it needs the joint effort of clients, construction companies, tunnel boring machine (TBM) manufacturers, universities and the chemical suppliers.
TBM TUNNELLING – A HISTORY
The first steps of a shield tunnelling method were made by Sir Marc Brunel in 1825-1842 with the world’s first underwater tunnel (River Thames, London) using a rectangular shield in soft ground. A more modern-like, update was designed by Barlow-Greathead, in 1869, for a Thames crossing again, this time near the Tower of London with circular-shaped shield, a separate air pressure chamber, hydraulic jacking system for metal segments and segment erector.
The first drilling machines were operational in 1846, designed by Henri Joseph Maus, in France, for the Mount Cenis Tunnel and in the US by Charles Wilson, starting in the early 1850s, for the Hoosac Tunnel. The 1880s saw a drilling machine for an exploratory bore at the English Channel.
What we call today a ‘Tunnel Boring Machine’ (TBM) was for the first time assembled in 1931 by Schmidt- Kranz for the German coal mines, followed by the first Robbins hard rock TBM, developed by James S. Robbins, in 1952, to use drag bits and disc cutters for tunnels at Oahe dam in South Dakota. The precursor of all modern pressurised and shielded soft ground TBMs was developed again by Robbins and successfully used in 1964-65 for the Paris RER transport tunnels, in France. (See Figure 2). The compressed air supported TBM was equipped with a cutterhead and soft ground excavation tools, with a cutterhead bearing and bull gear, a protected conveyor to transport the muck out of the excavation chamber, a segment erector for concrete segments and universal seals, and also a proper TBM driver cabin.
As described by Maidl et al (2012), the design of the first Earth Pressure Balance (EPB) TBMs was started in 1963 by Sato Kogyo Co. with a working chamber and screw conveyor system (see Figure 3). The first site use took place in Tokyo, in 1974. These first EPBMs were used in rather cohesive soils with high plasticity, using mineral oil-based foam to reduce the cutterhead torque and achieve better control of the ground support pressure by turning the muck into a compressible medium – which is normally not the case.
FROM JAPAN TO EUROPE – THE BOOST OF GROUND CONDITIONING ADDITIVES
Unlike the very homogeneous silty soils in Japan, tunnelling in Europe takes place in rather nonhomogeneous ground, resulting nearly always in mixed face conditions at the cutterhead level as well as along the longitudinal profile of a tunnel. The mixed face conditions can range from highly cohesive clogging clay soil to highly permeable and cohesionless gravelly soil. Figure 4 (Langmaack 2008) illustrates the soil grading curves of several selected EPB-TBM projects below groundwater level.
The milestones in ground conditioning development with EPBMs in Europe are illustrated by several key projects.
Lyon (1997)
After a fairly challenging first European EPB-TBM use in Milan, in 1994, with unadopted Japanese foam in very coarse soil (Greeman 1994), the first larger diameter EPB project in Europe was BPNL Lyon in France, from 1994-1998. For the works, Bouygues operated an 11.02m-diameter EPB shield manufactured by French company NFM. It was the world’s biggest EPBM at the time. For the project, two tubes were driven through 1,250m of rock in open mode, a 450m-long transition zone of rock/alluvium in EPB closed mode, and then bored through 1,552m of coarse soil. The latter geology is still nowadays considered to be ‘not usable for EPB machines’ even though the TBM drive was realised quite successfully.
As described by Langmaack (1997), for the first time different soil conditioning foams were thoroughly tested. In addition, the first liquid biological long chain polymers were developed to give structure to the muck and modify the foam behaviour. The product development around this jobsite was the germ cell for the modern foams, polymers as well as anti-clay additives, whereas the latter still needed some re-design to be efficient for site use, finally, in 2001.
For the BPNL jobsite, a couple of initial tests were driven, tests which are still used for actual projects:
- Different foams for different geologies
- Foam behaviour with and without polymer
- Permeability studies with foam, foam + polymer, foam + polymer + bentonite suspension to modify soil with permeability of k=2.7 x10-3 m/s down to 4.5×10-5 m/s together with the original soil.
Figure 4 illustrates the BPNL soil grading.
The author would like to thank Laurent Frouin and Fabrice Grandhaie in this context for all the inspiration. It was a truly a great time.
Aviles (1999)
Again, a challenging jobsite: a sewer outfall project, tunnelling with a Lovat EPB-TBM first through clay soil and afterwards through gravelly sand with absolutely no silt content (sharp graded sand with 20% gravel, see Figure 4), all below the Atlantic Ocean off the coast of northern Spain.
After having difficulties with clay clogging (the anticlay polymers were not ready at that time) and injecting a lot of water, the soil changed suddenly, and much earlier than had been foreseen, into running sand under 3.5 bar sea-water pressure. The tunnel was almost flooded.
Our first proposal at the time was to inject a bentonite suspension at the cutterhead to increase the soil cohesion. But due to a very long installation time and huge additional investment necessary the contractor asked to use whatever chemical was necessary to solve the problem. Finally, we composed a foam/long chain polymer mix with much higher polymer content than ever used to create a strong and thixotropic foam that was able to replace the water in soil voids. Figures 5 & 6 illustrate well the difference between using a simple foam and using a well adopted polymer/foam mixture, resulting in excavation of an almost dry sand.
The project was finished very successfully (Langmaack 2005, Langmaack 2016).
Madrid MetroSur (2001)
From 2000 onwards Madrid had a complete infrastructure development plan, including a metro system for the south of the city.
Unfortunately, the soil in the south of the capital consists mainly of clay, which results in heavy clogging on a cutterhead and inside the working chamber (Langmaack 2002). Using the foams available at that time, the 9.33m-diameter EPB machines on the MetroSur project achieved only very low advance rates of about 5mm-10mm/min and additional heavy maintenance and cleaning of the cutterhead and the working chamber. This difficulty jeopardised the plan.
However, the problem lead to a new way of using foams and anti-clay polymers together. For the first time they were very successfully applied on-site and since then the approach has been used all over the world, being copied by others. On the MetroSur project, the effect of the new way of using foams and anticlay polymers together was dramatic, as illustrated by Figures 7 & 8 – even making tunnelling records possible, achieving of 936m in 31 days, with the same TBMs at the very same location where the machines had struggled.
This was a big step forward for the EPB use in clay, and we were extremely happy. A special thanks to Rafael Valenzuela and Daniel Montalban who supported me with great enthusiasm on site.
Madrid M30 (2005)
The next incredible step forward in soil conditioning was for the first giant EPB TBMs worldwide: 15m diameter machines. They were to work on the M30 motorway project, in Madrid. We all have been concerned that the necessary cutterhead torque on such machines could be extremely high since diameter influences torque to the cubic power!
Therefore, we did extensive soil conditioning tests in the laboratory and used a second generation of anti-clay foam, allowing to reduce the cutterhead torque significantly even with a completely filled and pressurised working chamber. See Figure 9 and Langmaack (2013). As a result of well applied and adopted soil conditioning, the average real cutterhead torque on the EPBMs on M30 remained half as important as expected and only at 30% of the installed torque.
This jobsite is a perfect example of how well applied soil conditioning – and we saw this on the Herrenknecht TBM as well as on the Mitsubishi TBM on the project – can protect the cutterhead well, reduce clogging and wear very efficiently, avoiding frequent chamber interventions as well as time consuming and more risky cutterhead tool change.
Special thanks to Claus Nielsen and Sören Nörtoft for their great support.
New Kaiser Wilhelm Tunnel (2011)
A 10.54m-diameter dual mode HR/EPB TBM with constant screw conveyor muck-out was used for Deutsche Bahn’s (DB) New Kaiser Wilhelm rail tunnel project, in Germany. DB was doubling up capacity beside the existing, 1879-built, Kaiser Wilhelm railway tunnel.
Starting with open hard rock excavation, the TBM was supposed to reach the transition zone to the soft ground section with only 3.2m distance to building foundations. Therefore, in planning, DB insisted on the machine be switched to EPB mode, with a completely filled and pressurised working chamber, while still in the hard rock section and well before reaching the transition zone – something we had never done before.
As described in Langmaack (2016) and Langmaack (2017), the solution finally applied was to undertake simultaneous injection of a strong foam and a polymer reinforced bentonite suspension at the cutterhead. This combination turned the hard rock chips and the fines created by the cutterhead into a compressible homogeneous paste (see Figure 10).
The switch from hard rock open mode excavation to fully pressurised EPB advance was tried a couple of times and then was successfully, finally, applied close to the predicted transition zone to soft ground. The conditioning system was also continued in the soft ground section with a subsequent reduction of the bentonite suspension injection as the amount of hard rock decreased.
Special thanks to Ulrich Rehm and Armin Strauss for all the challenges as well as for all the support.
Hamburg Elbe Crossing (2023)
The Elbe crossing project for the Hamburg District Heating System passes through clay soil as well as gravelly sands of high permeability. From the lessons learned on earlier projects, the use of bentonite suspension along with polymers seems mandatory for the sandy section. To meet special concerns regarding the high water pressure and taking into account new ideas to increase tunnelling security and also to increase the efficiency of a fine filler injection, we at MC-Bauchemie have created the SolidFoam® technology – which has undergone extensive testing at the RUB University, Bochum (Thewes 2023).
Figure 11 shows the change of the soil permeability coefficient k with different modes of conditioning, illustrating well the efficiency of applying a highly stable SolidFoam®. More detailed research is in progress and will be presented at the STUVA 2023 conference, in Munich, in November. The technology is to be first applied on the Elbe crossing EPB TBM in Hamburg.
Special thanks to Eugen Kleen and Markus Thewes for the initial ideas and belief in the concept.
TBM DEVELOPMENT
The TBM design itself and its key components are of highest importance for the efficient use of soil conditioners as well as for the whole tunnelling project. The TBM design shall give a high degree of flexibility for using the soil conditioning additives, for example using polymers not only in their diluted form but also as concentration or inside the foam. The more possibilities the TBM design offers, the more efficient the soil conditioners will be. High attention should also be paid to the TBM driver. The driver is one of the key persons for successful EPB tunnelling and should be supported well, both with optimisation proposals as well as displaying information rapidly if something is not running as it should be, such as: blockage of foam injection ports; too much compressed air being used; rising muck temperatures; and much more. Here, active soil conditioning guiding systems may take an important role in the future.
Foam Injection Ports
The cutterhead is one of the most important parts of the EPB-TBM. Therefore, we need to have as many foam injection ports as possible at the cutterhead, directly connected to the foam system at the TBM gantry.
Until the year 2000, TBMs were partly using revolver swivels and had split foam lines, coming from the foam generator, to serve two or more injection points on the cutterhead. This arrangement quite often resulted in irregular foam supply due to the pressure gradient in the working chamber, which finally led to blocked foam lines. Modern machines use a rotary union that allows a proper and continuous one-to-one connection from the foam generator to injection point. Unfortunately, the rotary union design becomes more difficult with an increasing number of injection points on the cutterhead, but this investment pays back rather quickly.
It is also important to spread the injection points well over the whole cutterhead area. Unfortunately, still these days, we see machines with sections of more than 30% of the cutterhead not covered.
Foam System
The design of the foam system itself is the other key part of the soil conditioning system.
In the 1990s – and, unfortunately to a certain extent still so nowadays – the TBMs were equipped with foam mixing tanks. The system is quite inflexible when it comes to changing foam recipes, which made the use of polymer a nightmare and were often the reason for numerous hassles, like overflowing foam or being a source of bacterial contamination. The industry shifted to real-time in-line mixing systems, which are both highly efficient in use and quickly adoptable to the soil conditions.
Also, the generator design itself is of great importance. The two main criteria here are the creation of a stable foam with quite uniform foam bubbles as well as a minimum amount of free compressed air.
As already indicated, the foam system should be easy to use for the TBM driver. Most modern systems, instead, are rather difficult to operate and to be adaptable to the actual encountered soil and the necessary driving requirements of the TBM. Therefore, we developed a versatile foam system for Robbins some 10 years ago, which has in-line foaming solution regulation, including polymer mixing, and also has operations supported by an easy and quick to use touchscreen user surface as shown in Figure 12 (Langmaack 2016). It has water/ (polymerised) foam selectors for each cutterhead injection port and a quick rider system for easy general foam injection rate (FIR) adoption of all foam ports.
Special thanks to Lok Home giving me the opportunity to create that system.
WAYS INTO THE FUTURE Soil Conditioning Testing Equipment
During 2012 and 2013 we developed, together with the Norwegian Technical University, in Trondheim (NTNU), a quite simple, laboratory-scale boring machine capable of drilling through compacted soil samples (Langmaack 2013). Soil conditioners can be added at the simplified cutterhead and torque as well as thrust values can be recorded online, and the cutterhead tool wear recorded after finishing the test.
We call this machine ‘Soft Ground Abrasion Tester’ (SGAT) and it represents, in fact, the missing link between standard laboratory mixing tests and the soil conditioner application on site. The SGAT tester enables us to better identify the best product alternatives as well as the best injection ratio, even considering the resulting wear. Figure 13 shows easily interpretable results of using the same compacted soil and same advance parameters with two different FIRs. This system deserves further development and consideration – for the chemical industry, for the construction companies as well as for the consultants and their clients.
Special thanks to Pål Drevland and Filip Dahl for realising all the good ideas we had.
Preserving the Environment
Our all overall task is to preserve the environment, doing so in tunnelling with soil conditioning to minimise the impact of the chemicals and agents on ground surrounding the excavation and on landfill from disposed spoil. Special risk assessments, like those already in place for Copenhagen metro development for example, are a great step forward. Preserving nature is about more than just looking at biodegradation values (Langmaack 2023).
It is important to indicate here that more environmentally-friendly soil conditioning products are available these days on the market but not always used due to their slightly higher costs – which touches upon the next very important point – a strategic perspective, taken together by key parties developing a project – the client, contractor and consumables producer.
Triangle: Client, Contractor, Consumables Producer
Looking back to projects like BPNL Lyon in the late 1990s being the germ cell of many modern soil conditioners, it may now be time for the next significant step forward. In order to make this happen, construction companies as well as clients might act slightly less conservatively, be more open towards new possibilities, less price/kg but more solution driven which will surely lead to an overall benefit. This includes the acknowledgement of a good technical on-site service.
Furthermore, big projects should include funded research, part-linked to university and industry to help drive innovation forward and also enable well-founded and independent back-analyses.
Future Products and Systems
Here are just some ideas:
- The use of foam on hard rock TBMs definitely needs further research and development, and university support. Foam reduces dust much more efficiently than just sprinkling water and, in addition, also wear can be reduced much more efficiently using the right anti wear polymers. We have seen these encouraging advantages already on a few selected jobsites but the real breakthrough is still missing.
- The SolidFoam® technology will ensure a higher level of soil conditioning efficiency as well as tunnelling security when driving through fault zones or sections of increased soil permeability in either mixed or full face conditions.
- The DrainGrout®, MC-Bauchemie technology opens new horizons and brings a 2-component annulus grout to the market with permeabilities of 10-5 m/s to 10-4 m/s for water draining purposes.
- The Automatic Foam System, which will ease the work for the TBM driver, will deliver more uniform TBM drives and hopefully limit the incorrect application of soil conditioners. Special thanks to Tim Babendererde for believing in this system and being a great sparring partner.
SUMMARY
Soil conditioning has seen enormous development over the past decades – allowing faster and more secure EPB-TBM drives in clay soils, in areas of high soil permeability as well as enabling all kinds of mixed face conditions and huge TBM diameters. The application range of EPB TBMs has never been so vast as nowadays – the possibilities of limiting surface settlements to an absolute minimum have never been so extensive.
Nevertheless, the wide-spread mentality of just looking on the price/kg of the soil conditioners impedes their real efficient use in the day-to-day business – it also impedes further R&D of soil conditioners. The real benefit of well-developed and applied soil conditioners must be calculated correctly, finally, and dedicated research budgets associated to big tunnelling projects would help significantly in driving innovation forward.
New Automated Foam Systems will hopefully simplify the tasks for the TBM driver by early alert of improper soil conditioning use and proposing counteractions – optimising the soil conditioning in general.