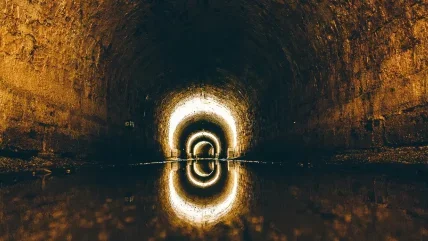
IT IS A SIMPLE FACT that groundwater makes tunnelling and shaft sinking more difficult. Sir Harold Harding, the founding Chairman of the British Tunnelling Society summed it up nicely when he said: “Below ground water is the root of all evil” (Harding and Davey, 2015). However, with careful planning, and the right technology, groundwater can be controlled, and tunnels and shafts successfully constructed, even in ‘bad ground’ (Figure 1).
UNDERSTANDING THE PROBLEM
It is an obvious statement that any groundwater control solution must be matched to the ground conditions – waterlogged silt clearly will present different challenges to water-bearing fractured rock. Like any ground engineering process, groundwater control must be based on a thorough ground investigation, which is then used to develop a conceptual ground model. Where groundwater control is required, it is essential that information is available on: the permeability of the soils or rocks that will be encountered; and the groundwater levels relative to the tunnel or excavation.
DEWATERING AND DEPRESSURISATION
Beyond ground conditions it is important to understand the groundwater problem that must be addressed to allow safe and efficient construction. In most cases there are two potential groundwater problems:
¦ The first and most obvious problem is flooding or inundation by groundwater inflow. This is addressed by dewatering methods.
¦ The second, and perhaps more subtle problem, is instability caused by groundwater seepage. This requires groundwater depressurisation.
Dewatering is the dominant problem in relatively stable ground conditions (such as fractured rock) where high rates of inflow can occur, but do not cause instability of the exposed ground. In this case, groundwater control focusses on pumping away the inflow, and the challenge is to deploy pumps (and associated discharge pipes and power supplies) of sufficient capacity to handle the water, without excessively hindering excavation and lining. If inflows are too large to handle by pumping alone, grouting can be used to reduce the permeability of the material ahead of the face; this can reduce (but not eliminate) inflows. However, some inflow can be good, and in hard rock tunnels the urge to seal every inflow should be resisted, as the inflows may gradually depressurise the ground ahead of the face, and inflows to the tunnel may reduce with time.
The risk of groundwater-induced instability of exposed ground is often the primary concern in soils and weak rocks, and groundwater depressurisation can be used as a solution. In problem soils such as fine-grained sands and silts, even small flow rates of water seeping into a tunnel face or the base of a shaft can cause significant instability and loss of ground. This type of instability caused by groundwater flow is often described as ‘running sand’, an evocative phrase that helps visualise how such material behaves.
When a face is cut or an excavation is made in running sand, the exposed soil will flow or ‘run’ into an excavation, filling it up with fluid sand/silt. These conditions are obviously a problem and would preclude tunnelling by the SEM (sequential excavation method) where short-term face stability is essential. But soil mechanics theory tells us that running sand is not a type of material; it is actually a state in which a granular material can exist, when pore water pressures are high, creating low effective stresses, which causes the soil to lose all its strength and become fluid. Once this is understood, it can be seen that groundwater depressurisation (for example using in-tunnel wells) can reduce pore water pressures and will transform running sand into more stable ground suitable for careful tunnelling.
This depressurisation approach has been widely used in London for cross-passage work and connector tunnels in the Lambeth Group strata, where in-tunnel depressurisation wells were used to reduce pore water pressures in potentially unstable layers of fine sand and silt around the main tunnels.
DIFFERENT CHALLENGES
Tunnelling projects can involve various geometries of underground works, including:
¦ Tunnels, often arranged as twin, parallel tunnels on transportation projects
¦ Shafts and vertical excavations connecting tunnel works to the surface
¦ Cross passages (linking between twin parallel tunnels) and connector tunnels
¦ Recovery works, applied after there has been a tunnel collapse or inundation.
The choice of the most appropriate groundwater control method will be influenced by the type of tunnelling works under construction. The various methods can be grouped into three categories (Table 1). The remainder of this article focuses on tunnels and shafts; groundwater control methods for cross-passage construction are discussed in a previous article (Preene, 2020) in the October 2020 issue of Tunnels & Tunnelling International.
IMPACTS AND REGULATION
A key aspect of groundwater control methods is that they can affect groundwater conditions beyond the boundaries of the construction site. For example, pumping for dewatering and depressurisation can lower groundwater levels over a wide area, which can reduce the yield of nearby water supply wells, or draw in contaminated water from neighbouring brownfield sites. If a significant thickness of compressible soils is present, then the increases in effective stress due to groundwater lowering could cause significant ground settlements (which would be in addition to other tunnelling-related settlements). The design of any significant groundwater control exercise should consider the potential impacts.
Because of the potential impacts on groundwater resources, in most countries groundwater control by pumping is subject to regulation, and various permits are required before ground water can be pumped or discharged. Anyone planning groundwater control works in the United Kingdom should consult with the relevant regulatory body: in England, the Environment Agency; in Wales, Natural Resources Wales, In Scotland, the Scottish Environment Protection Agency; and in Northern Ireland, the Environment Agency Northern Ireland.
GROUNDWATER CONTROL METHODS USING FLUID COUNTER PRESSURES
The first group of methods are those that apply a fluid counter pressure to the workings. These methods were developed by tunnellers to effectively pressurise the confined space of a tunnel or shaft to balance the external groundwater head, thereby keeping the water out. The earliest technique to achieve this, developed in the 19th century, was compressed air working where the tunnel is pressurised with air. However, the health risks associated with operatives working in compressed air mean that this technique is now used only rarely, and under close medical controls, for specialist activities, such as face interventions to replace TBM cutterheads.
In the latter half of the 20th century, the alternative method of the closed-face tunnel boring machine (TBM) was developed. These complex machines use either the earth pressure balance (EPB) or slurry method to balance external ground and groundwater pressures (Figure 2). The essence of the method is that a pressure bulkhead in the TBM allows a fluid to be used to balance face pressures and exclude groundwater, while operatives in the TBM, behind the pressure bulkhead, can work in a dry environment, even deep below groundwater level.
The fluid counter-pressure approach can also be used for shaft sinking. One example is the ‘wet’ or ‘flooded’ caisson method (Figure 3). The principle of this method is that the head of water in the caisson (held slightly above groundwater level, by pumping water into the shaft if necessary) applies a small excess pressure to the base of the shaft excavation. In coarse-grained soils (such as sands), this will prevent groundwater inflow, hence avoiding the risk of instability due to ‘boiling’ or ‘running sand’ conditions. In low-permeability clays, the downward water pressure will help counteract the upward pressure from any confined aquifers below dig level. Once the shaft is dug to final depth, a mass concrete base plug, placed by tremie, is used to seal the base of the shaft. When the concrete plug has gained sufficient strength, the water is pumped out, and the inside of the shaft can be accessed.
The water inside the caisson applies a small excess water pressure to the base of the shaft, preventing water inflow and reducing the risk of basal instability. The base of the shaft is excavated underwater as the shaft is jacked downwards. New rings of shaft lining are added periodically at ground level as the caisson sinks.
GROUNDWATER EXCLUSION METHODS
Groundwater exclusion methods have the advantage of avoiding many of the complications of pumping systems – external impacts, water disposal, regulatory permissions, etc. On many projects, shafts are constructed in areas where the risk of impacts from groundwater lowering (e.g. ground settlement or migration of contamination) is a concern. This often makes groundwater exclusion a favoured approach.
Where the shaft design includes a perimeter structural wall (e.g. formed of concrete diaphragm walls or secant pile walls) careful design can allow these walls to act as a groundwater exclusion barrier, provided the depth of the wall is adequate. If the shaft construction method does not include a structural wall, then ground treatment methods (such as permeation grouting or jet grouting) are often used. The objective is to create a zone of low permeability treated ground, within which the shaft can be excavated with only minimal groundwater pumping requirements (Figure 4).
Ground treatment can also be used for tunnels. However, in many cases, the depth of the tunnel and/or lack of surface access precludes treatment from the surface. As an alternative measure, ground treatment can be deployed sub-horizontally from the tunnel to pre-treat the soil or rock ahead of the advancing tunnel face – permeation grouting or rock grouting being most commonly used.
A key limitation of this approach is that pre-treatment can only be carried out to a maximum distance (typically 20-30m) ahead of the current position of the face. Once the tunnel has advanced towards the far extent of the zone of treated ground, tunnelling must stop (with the face still in treated ground). There must then be a pause in tunnel advance while a further phase of ground treatment ahead of the face is carried out from the new position, after which the tunnel can advance again (Figure 5). This means that the tunnelling must progress in a repeated stop/start cycle of ground treatment, tunnel advance, ground treatment and so on. Optimising the speed and effectiveness of the ground treatment phase is key to making this approach effective on long tunnel drives; in practice this approach is most commonly used to drive a tunnel through short lengths of ‘bad ground’.
GROUNDWATER PUMPING METHODS
In suitable ground conditions (e.g. permeable sands and gravels or fractured rock) groundwater pumping can be a highly effective method of dewatering and depressurisation. If surface access is adequate, and if a suitable route for water disposal is available, then the technique can be straightforward to deploy, using pumping from an array of vertical wells to lower groundwater levels. This approach is often used for shaft construction, where space in the site compound can be used for wells and dewatering equipment. However, for tunnels and cross passages, surface access is rarely available, and in-tunnel pumping methods are required.
The simplest approach is direct pumping from within the tunnel. Every tunnel below groundwater level requires an appropriately designed pumping system. Even a tunnel driven by a closed-face TBM, where the TBM operator and miners work in a notionally dry environment, can experience water inflows. Such inflows can occur due to TBM problems (e.g. excessive water loss through the screw conveyor on EPB TBMs) or during face interventions. Open-face TBMs will experience water ingress through the face at a rate dependent on the soil or rock permeability and any ground treatment or groundwater control measures that have been deployed.
In general, the primary groundwater problem during tunnel construction is instability of soil and rock in the face, as in many cases this will occur before inflows become very large. The exception to this is when tunnelling in fractured hard rocks. In this case, even significant inflow rates may not destabilise the face, and tunnelling can proceed while allowing inflows at the face and using high-capacity pumps to remove the water. However, at very high inflows, direct pumping from the tunnel can become unworkable due to the quantity of pumps and pipework required; a better solution may be to use rock grouting to reduce inflows to more manageable levels.
Where rates of water inflow could cause instability, one option is the use of in-tunnel wells. This involves drilling outwards from the tunnel, either from the face or through the tunnel primary lining in the area behind the face. In general, in-tunnel dewatering can only have a local depressurisation effect, so new wells must be continually installed to keep pace with the progress of an advancing tunnel. For this reason, this approach is not applied widely on tunnel drives but is more commonly applied for the construction of cross passages and connector tunnels.
A key challenge is to drill out from a tunnel below groundwater level, especially in soils and weak rocks. There is a risk that the drill hole will allow inflow of water and soil/rock particles, leading to loss of ground and collapse of the drill hole before any liner can be installed. To avoid these problems, in many cases the drill hole must be made through a ‘blow out preventer’ (BOP) connected to a steel standpipe attached and sealed into the tunnel lining. When each well is completed it must then be sealed into the tunnel lining and capped with a valve.
When the in-tunnel wells are completed, the external groundwater pressure is above tunnel level; when the valves are opened each well will naturally flow into the tunnel. This will achieve some depressurisation effect, but further pressure reductions can be achieved by pumping. Pumping is often achieved by electrically-driven duty and standby wellpoint pumps in the running tunnels to apply a suction to the wells (Figure 6). Ejector wells have also been used as a pumping method. VWP pressure sensors installed in probe holes drilled out from the tunnel can be used to monitor pore water pressures.
CONCLUSION
The presence of groundwater undoubtedly makes tunnel projects more difficult, but these problems are not insurmountable. With good ground investigation information to give some foresight to the likely problems, a ‘toolkit’ of pumping and groundwater exclusion techniques can be deployed to deal with a wide range of ground conditions and tunnel geometries.