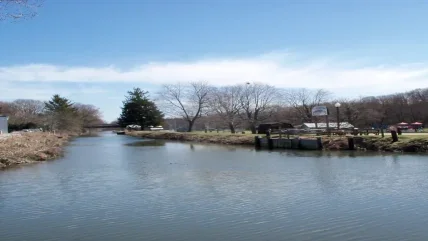
It was not an easy start for Rosie with a very short reach of 200ft (60m) in soft ground, and then mixed face for 600ft (180m).
“It took everybody we had in the industry, everybody from Robbins, to fight through that first 800ft (240m),” says David Chastka, project manager, Kenny/Obayashi JV (prime contractor). But the massive Robbins Crossover was strong enough to flex her muscles at the Ohio Canal Interceptor Tunnel (OCIT) in Akron, Ohio.
The OCIT will be able to hold 26.7M gallons (1,010,705M litres) of stormwater and sewage during heavy rain events and control nine of the overflows into the Ohio & Erie Canal and Little Cuyahoga River. It will also carry raw sewage during non-rain event days.
A joint venture between Illinois-based Kenny Construction and Tokyo-based Obayashi bored the tunnel, which is 27ft (8.2m) in diameter, and 6,212ft long. The consent decree required a volume of 25.6M gallons, but due to value engineering during the initial phase of the detailed design, the alignment was changed to obtain more rock tunnelling and this increased the length of the tunnel. The USD 184.1M bid by the Kenny/Obayashi JV came in below the engineer’s estimate of USD 252.2M.
The client is the City of Akron; the lead designer is DLZEngineering, Architectural and Construction Services; the tunnel designer is McMillen Jacobs Associates (sub to DLZ); the shaft designer is COWI (sub to DLZ); the prime contractor is Kenny/Obayashi, JV; the TBM supplier is the Robbins Company; the segment supplier is CSI Tunnel Systems – Forterra, JV.
The tunnel drive was completed in August 2018.
Challenging Launch
The layout of the city made the TBM launch challenging. The JV launched the TBM in October 2017 from inside the temporary excavation support at OCIT 1 on Hickory street within walking distance of downtown, the Northside entertainment area and the Towpath Trail.
Senior project engineer, McMillen Jacobs Associates, Chris Caruso explains that they decided to launch the machine there due to the configuration of pick up points. “We can’t drop the alignment,” says Caruso. “We were receiving the machine in the middle of downtown so it would have been really difficult to run tunnelling operations over there and to bring segments among traffic and congested areas for example.
“We were launching from a pre-covered zone and incorporated the ground improvement (jet grout) block outside the portal to give the contractors some space to learn how to operate the machine before going to the soft ground operations.
“The other essential thing was to operate a multimode machine—as we wouldn’t be able to complete this drive through rock in close mode and in soft ground in open mode. It was an essential component for the whole job.”
“As with any site in an urban area, the site access is always an important consideration,” says project manager, City of Akron, Mike Wytrzyszczewzski. “This was especially true at the portal launch site or OCIT-1 since all work here had a direct impact on the critical path in the baseline schedule.
“The sequencing and timing of the work before and after tunnelling operations made site management even more crucial.”
Chastka explains that there is a combination of soft ground and rock.
“We launched the machine in soft ground, which was like silky sand, and alluvial material,” Chastka says. “We didn’t have a lot of water pressure when we started the drive at the spring line.
The water table gradually grew as we advanced at the beginning of the drive.
“The first reach was 300ft [91.44m] in soft ground (purely silky sand). Then we moved into the second reach, which was a mixed face for about 700ft [213m]. At the beginning of this reach, we had shale, which gradually grew when we entered into the full face of the rock. This was the beginning of the third reach. The face of the rock was mainly shale or a mix of shale and sandstone.”
Geary Visca, design project manager, DLZ Engineering explains that a series of bores have been done. “We had an investigation programme done during design and also some preliminary bores have been done,” says Visca. “We developed a geotechnical baseline report [GBR] during the design phase.
“On top of the GBR we also prepared a risk register as part of the design. We wanted to develop this register to evaluate and resolve risks as we moved along during the design.
“One thing of this tunnel is that it is storing 26.7M gallons [121M litres] combining sewer gallons overflow and it is also conveying dry weather flow, which is not typical for a storage tunnel.”
Visca adds: “Most storage tunnels only store excess wet weather flow from the collection system and do not convey dry weather flow. The dry weather flow is typically kept in the collection system.
“The OCIT is serving two purposes, storing excess wet weather flow and replacing an existing trunk sewer, and that is why it is conveying the dry weather flow.”
Caruso talks about the geological investigation programme, explaining that they had a standard mandatory for drilling. “We did the standard technical boring; we took rock out as well along the alignment,” says Caruso. “We also had additional boring at the shaft locations and a couple of deep wells were we put in place to monitor ground conditions during construction.”
Caruso explains that a crossover machine was chosen due to ground conditions although they didn’t specify the crossover machine at the beginning of the contract.
“We allowed the contractors to choose for either slurry or EPB depending on the capability to work in opening or close mode and then the contractor worked with Robbins to see whether it was possible to use a crossover type machine,” says Caruso. “It is a multimode machine capable to work in both open and close modes. It is single shield EPB with an articulation joint on that; joint single screw.”
Hyperbaric interventions were not expected but all provisions were made for them as a contingency.
Pre-cast concrete segments 14 inches (355mm) thick and 5ft (1.52m) long with EPDM single gaskets have been used. The configuration is 7 plus 1. The lining was the same for the entire drive. Segments were mainly stored on site but not all of them. They were produced 45 minutes away from in Macedonia, Ohio.
Chastka says that the muck was transferred from the tunnel through conveyors and brought to yard storage across the Little Cuyahoga River.
“Segment supply was mostly convenient since the pre-cast plant was located approximately 30 minutes away and they were delivered on an ‘as-needed’ basis with about 15-20 rings always on site,” says Chastka. “Muck delivery was challenging initially due to the conditioners needed in the soft soils and winter weather.
“However, once the spoils shifted from conditioned soils to rock, it was hauled less than a quarter of mile from the site and almost completely off the public roads.”
Talking about ground treatments, Caruso explains that the contractor was running in open mode for most of the drive in rock. “We knew that there was a potential for water bearing joints based on the investigation programme,” Caruso says. “In order to mitigate the high water level and to avoid slowing down the project, we specified a probe drilling through the face of the TBM in an attempt to anticipate possible water or gaseous conditions ahead. This would allow the contractor and designer to solve small problems before they became much larger. It’s really a risk mitigation strategy.
“It was established that the contractors had to work with a minimum of 50ft [15.24m] looking at front of the machine. And then they can, in theory, be able to pre-excavate and grout. But any pre-excavation grouting was not needed because of the local ground conditions, type of tunnelling and TBM chosen for the project, minimal ground improvements were necessary.”
One exception was the installation of a 50 x 50 x 50ft jet grout block just outside the sheet pile wall for the TBM. Different monitoring techniques were used throughout the project depending on need and location. These included: surface monitoring points, multiple point borehole extensometers, inclinometers, rod extensometers, shallow settlement indicators, and observation wells.
Vibration and noise monitoring is required throughout the duration of the project.
Wytrzyszczewzski says that overall the monitoring was extremely helpful in the areas of the soft soils and mixed face tunnelling reaches. The observation wells became an important component during some of the near-surface work as the water table posed potential risk.
Due to the location of the portal entrance site near a residential area, the only night work allowed was during mining operations. However, muck removal/trucking was only allowed between the hours of 7am and 7pm for all operations. The contact documents established noise and vibration monitoring limits at all three sites on the project. Baseline readings were taken before work began, and remote monitors provide weekly reports for compliance.
Other Challenges
Wytrzyszczewzski explains that from the city’s perspective the schedule and the public engagement programme were quite challenging. “At a high management level it was challenging because of the hard deadline to have an operational tunnel imposed by the regulatory agencies. Various design changes and considerations were made after numerous meetings with residents and community and business stakeholders. Examples of these included noise and vibration monitoring, blasting requirements near a Federal Courthouse, tunnel alignment, haul roads, time restrictions on when materials near residential properties could occur and land acquisition along the alignment.”
From a design perspective Visca says that during the design phase the schedule (both design and construction) was compressed during on-going negotiations with federal and Ohio Environmental Protection Agency. “In addition to this we were dealing with large diameter system,”says Visca. “All the typical issues designs are related to the large diameter and to the complex geology.”