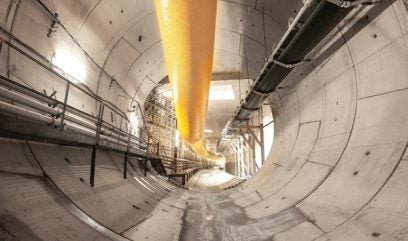
The successful bid made by Paris to host the 2024 Summer Olympic Games was built around an incredible major transport infrastructure project the French capital is developing – the Grand Paris Express. The mass transit project is being built with a double purpose in its transportation reach: to revitalise the core area of the city that the world knows along the banks of the Seine River; and, to upgrade transport links throughout the surrounding Greater Paris area – the constellation of large communities surrounding the core and whose citizens move every day in their millions.1
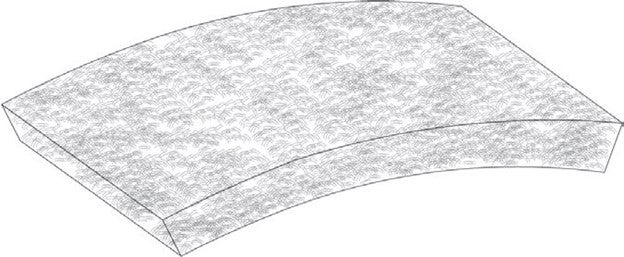
Grand Paris Express involves 200km of automatic subway lines, almost entirely underground, to be completed before 2030 with some key lines for 2024 and the Olympics. With 68 future stations expected to handle two million passengers daily, this new system is going to transform Greater Paris.2
Building the Grand Paris Express presented a host of technical, material, human, and environmental challenges. The owner and developer, Société des grands projets (SGP, which was formerly Sociéte du Grand Paris (SGP)), is solving the challenges by adding innovation at every level of the project, from design to commissioning.
The sheer magnitude of the Grand Paris Express offers an opportunity to test out innovative solutions on a large scale. Innovation is not confined to techniques and construction methods. The intention to build the world’s most digital subway also requires the project to look ahead to tomorrow’s digital practice.
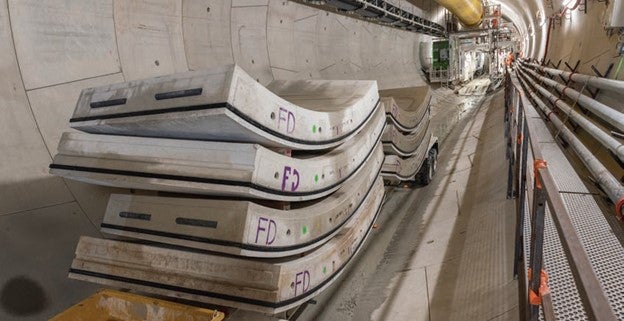
Innovation is what makes the Grand Paris Express project a driver of the ecological transition. SGP is steering a great number of projects towards sustainable design and build practices. This strategy is also paving the way to advancing best practices in the public works sector. But it is, perhaps, in the project’s environmental and energy areas that the innovations – both in methods and in management – will be most significant.
In terms of concrete, there will be ‘before’ and ‘after’ Grand Paris Express. Until now, to design the precast segmental lining we used reinforced concrete, that is to say concrete poured around massive cages of steel reinforcement bars. Since 2020, on the project’s Line 16, Lot 1 (Line 16.1), tens of kilometres of tunnel have been designed with steel fibre reinforced concrete (SFRC) and a much larger deployment is now planned given the latest contracts awarded. This is a rare scale of deployment in the transport infrastructure sector in France.
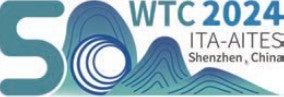
MOVING TO LOW CARBON LINING
The aim of all those involved in the planning, design, construction, operation and renewal of tunnelling infrastructure should be to decarbonise it. This means to reduce the embodied and operational carbon produced. The carbon emission throughout the entire life-cycle of underground infrastructure should be considered.
On tunnelling projects, 60%-80% of the embodied CO2e emissions are in the concrete tunnel lining. Therefore, the easiest way for us to have the biggest positive impact for decarbonising is to reduce the CO2e emissions associated with the concrete tunnel linings.
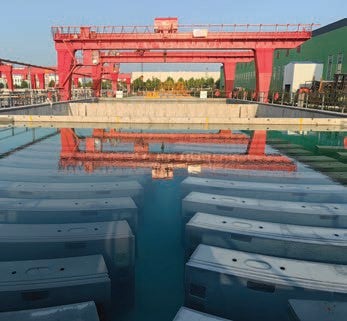
To bring this down, we need to talk about steel and concrete. Steel fibres are a more efficient, durable and sustainable means of concrete reinforcement. It saves (50%) steel in comparison to traditional concrete reinforcement, especially in precast lining. For example, in a typical metro tunnel of 10km length, fibre-reinforced precast segments can save up to 5000 tonnes of steel. To put it in a different perspective, 10,000 tonnes of CO2 are saved on average for 10km of fibre-reinforced tunnels.
Ordinary Portland Cement (OPC), responsible for 8% of global CO2 emissions, is a major component in tunnel construction that we aim to minimise. By partially replacing it with a new generation of binder materials, such as ground granulated blast furnace slag (GBBS) and fly ash, we can already make significant strides in reducing the carbon footprint. What’s more, the combination of these alternative binders with steel fibres in fibre reinforced concrete (FRC) offers even greater potential for carbon reduction.
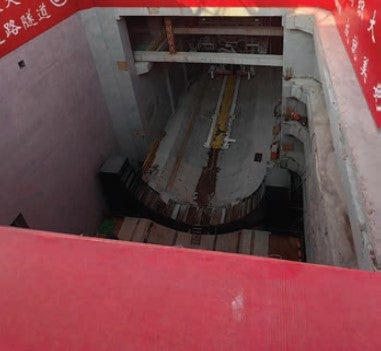
The works on Grand Paris Express 16.1 is a good illustration of what is achievable. The project owner was deeply involved in the innovation process, its innovation policy being above all a lever for making Grand Paris Express a project in the service of ecological transition and developing practices in the world of public works. Already the achievements include:
- Firstly, comparing the 40kg/m3 Dramix® steel fibres against the 85kg/m3 of rebar yielded a potential material saving of more than 50%.
- Secondly, the reduction of steel quantity required also provided a corresponding reduction in transportrelated CO2 emissions. One truckload delivery of fibres to the manufacturing plant allows the production of nearly 185 precast concrete tunnel segments, compared with 60 equivalent segments per truckload of conventional steel bar reinforcement.
- Furthermore, in terms of resources, FRC can reduce the quantities of concrete by 2cm to 3cm in segment thickness.
That’s not all, FRC also makes it possible to improve the technical performance of the structures. Thanks to the presence of fibres, the concrete segments behave better against cracks. Not only are cracks less important than for traditionally reinforced concrete but they also close over time. Likewise, the FRC segments are more resistant to corrosion. Steel, in contact with air and water, corrodes. As the fibres are interspersed through the cementitious matrix, if a fibre is corroded it will not propagate its corrosion to other fibres. Over time, we will therefore be in the presence of a much more durable material.
SOME STRUCTURAL REQUIREMENTS
The objective was clearly defined by the SGP and its prime construction services contractor Egis: to demonstrate that fibres work as well as traditional solutions.
In terms of results, according to the Model Code 2010, a 4D SFRC is required, with the understanding that the minimum characteristic values to be achieved are:
fR1k = 4.4 MPa
fR3k= 5.7 MPa
The fib 83 bulletin4 based on the Model Code 2010 will be used to determine and classify the characteristic values of the residual strengths (fLk, fR1k and fR3k) of SFRC.
The hardening behaviour at section level on the beam test, according to EN 14651, allow immediately.
- Cracking control at Service Limit State (SLS)
- Structural ductility at Ultimate Limit State (ULS)
The fib Bulletin 83 (2017) VP 1.4.1 (4), which complements the fib Bulletin known as the Model Code 20105, sets out the general rules for loads that may occur during the life of a precast concrete segment. For the sake of completeness, there are 10 of these load cases. The fib Bulletin takes into account four load cases that represent different stages in the life of a segment during its manufacture, transport and installation in the tunnel:
- Demoulding
- Storage
- Handling
- Transport
It also takes into account two load cases related to the life stages of the segments in the tunnel:
- Cylinder thrust
- Geology
After all the tests carried out beforehand, the final choice was made to use a Dramix® high performance fibre with high tensile strength > 2200MPa.
A high L/D (Length to Diameter) ratio, in this case 80, was also a determining factor in the choice made. The fibres are long (60mm), which allows the aggregates to be perfectly integrated (maximum diameter 20mm) and they are relatively fine (diameter 0.75mm), creating a net of 11.6km of fibres per m3 of concrete.
With 4,584 fibre units/kg, the concrete will be guaranteed to have fibres throughout the matrix and especially in the traditionally weak points of the precast concrete segment, such as corners and edges.
Finally, the fact that the fibres are glued was also an important element of choice in order to avoid the formation of balls in the industrial production phase. These balls represent a risk of creating nests of pebbles and segregations, as well as differences in fibre ratios in the precast segment, which would be detrimental to the homogeneity of the matrix and therefore to the intrinsic strength of the whole. The fibres of competitors, all free, did not satisfy Eiffage Génie Civil and Bonna Sabla.
SOME LEARNING POINTS
For the tunnel professions, some points seem important to understand: Like industry, the tunnel trades are primarily interested in mechanics and geotechnics.
In this respect, the importance of the segment has long been neglected, trivialised by reinforced concrete techniques that are tried and tested, but which have their drawbacks.
FRC segments have put the segment back in the spotlight, because of its contribution in terms of durability and low carbon, for a definitive final object in place, compared to the excavation methods, such as the tunnel boring machine (TBM), which are temporary tools to manage the geotechnical conditions.
What is often forgotten is that the segment, for its part, will permanently manage the geotechnical conditions, ensuring the safety of passengers in the context of public rail or road transport.
Reinforced concrete compensates for installation that is not carried out according to the rules of the art, whereas FRC imposes rules of the art that tunnel operators neglect in order to improve production – to the detriment of durability. The result is poor, thinking that FRC segments are ‘fragile’ and crack, whereas these same FRC segments ‘repair themselves’ more easily than reinforced concrete segments. The micro cracking guarantees durability, contrasts with the more extensive cracking of reinforced concrete, causing more serious damage.
The TBM is the master, even though it is only a temporary object, which neglects indeed the segments, even though these same segments are the perennial objects of the structure, guaranteeing the safety of passengers.
CONCLUSION
Underground space plays a vital role in sustainable urban planning as it provides a solution to the limited surface area available.
In terms of transportation, underground networks enable efficient and rapid mass transit, helping alleviate congestion and reduce carbon emissions. Moreover, underground space is essential for the infrastructure required to sustain cities, such as dense networks of pipelines for delivering fresh water and the sewerage systems for wastewater collection for treatment.
Additionally, underground space accommodates the extensive network of cables and service stations necessary for modern communication systems.
By utilising underground space, cities can optimise their resource management and minimise their environmental impact, contributing to a more sustainable urban future.
We believe tunnels should use smart and sustainable construction materials considering innovative design, with steel fibres and alternatives to OPC. The future of tunnelling is choosing these materials today. Dramix® could play an important role in the sustainable journey of the final tunnel lining.
FIBRES FOR SUBSEA DURABILITY BOOST
With China hosting the next World Tunnel Congress (WTC 2024), in Shenzhen in April, it is interesting to briefly note how Dramix® high performance fibres have been used to help meet enhanced durability requirements on a challenging subsea road tunnel project in the country.
The Qingdao Second Tunnel Project is a subsea road tunnel that connects the Qingdao and Huangdao through Jiaozhou Bay. The main tunnels have an operational road design speed of 80km/h. Together with the first tunnel of Jiaozhou Bay, once completed, the second tunnel will further facilitate the development of the west coast and transportation between Qingdao and Huangdao.
The new project includes two main tunnels and a service tunnel in the middle. The diameter of the main shield tunnel is 15m and the service tunnel is 7.7m. Structural linings employed for the tunnels on the project are varied: cast-in place concrete lining; sprayed concrete lining; and, segmental lining reinforced by steel fibres and mesh.
Traditionally, segmental lining of tunnel building has been reinforced by rebar mesh. With added steel fibre inside, the performance of segmental lining can be significantly improved, including for load bearing, crack control, impact resistance and durability. This project adopted rebar mesh plus steel fibre as the reinforcement solution for the segmental lining to enhance its structural and concrete performance in the complicated and challenging conditions below the seabed.
Dramix® steel fibres have been applied in the precast concrete segmental lining for both main tunnels and the service tunnel. At present, this tunnel of shield tunnel construction is still in its initial stage. The use of steel fibre further ensured the quality of segments, greatly improved procedures of segments production and installation, and made a model example for the use of steel fibre in a large diameter segmentally lined subsea tunnel.
Project Name: Qingdao Second Tunnel of Jiaozhou Bay
Client Name: Qingdao Guoxin Group
Contractors: CCCC, CRCC, CREC
Designers: The 4th Railway DI
Project Type: Road tunnel
Type of final lining: Precast segment