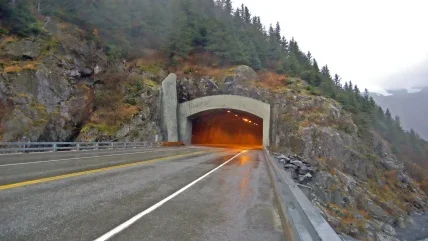
At the Swiss Tunnel Congress this year, in June, delegates heard the latest progress with the ‘plug-in’ safety door for tunnel cross passages of long traffic tunnels. The R&D product, known as the cross-cut wall module, or element, is a prefabricated concrete wall with a pre-fitted door. Using laser scans before leaving the factory, the wall inserts can have made-to-measure fit before being despatch to installation sites, deep underground.
Cross passages provide access between the long parallel tubes of a transport tunnel at regular, and other, intervals. The access routes provide two key benefits: key escape routes between the twin main tunnels to safer, clearer environments in the event or fire or other incidents requiring evacuation; and, space to hold technical equipment.
As important safety and technical support structures, the cross passages need to be protected against the large airflows conveyed with the running tunnels, leading to pressure waves and suction, as well as generating dirt and moisture under normal operating conditions. Consequently, the cross passages need to be sealed off with end walls or bulkheads, the STC conference was informed in a paper by Robert Binder of Biprotec GmbH.
The R&D project is being advanced under the auspices of the Swiss Centre of Applied Underground Technology (SCAUT) with a consortium composed of Elkuch Group and Biprotec, Amberg Group, SwiBox, Müller-Steinag Baustoff, Gifas Electric, Sika and Halfen. Tests have been undertaken in the Hagerbach underground test gallery, in Switzerland, which is also to host a demonstration of the system in November.
Veronika Petschen, managing director of SCAUT, described the challenges of matching the required cross passage sealed doors to underground environments with varying construction tolerances, depending on geology and excavation methods used.
“In natural rock you are doing well to get accuracy down to a couple of centimetres, which means that every cross-cut is slightly different in size and their linings have to be custom made on site. That takes a lot of time,” she has told T&T. Petschen added that laser scans of the cross-cut can be used with an adjustable mould in a factory to “cast the concrete element precisely to size, with the safety door and mechanism already fitted.”
The cross passage wall element is then transported to site and along rail tracks to be inserted into place with a few hours – about ten times faster and with fewer logistical construction challenges than the traditional approach.
SCAUT says that using conventional methods and insitu-concrete walls, the bespoke fit-out of installation and making the necessary electrical connections for each cross passage door can take up to three days for already experienced and effective teams of three workers to achieve, each time, based on data from works in the Gotthard, Ceneri and Lotschberg base tunnels in Switzerland. There are consequent financial and logistical costs from such repeated activities along the long, linear underground environments, and programme effects on other project activities.
The R&D effort started in 2016 with first results (with a full-scale prototype) presented by late 2017, at Hagerbach, and the system has continued to be developed. Studies on Semmering Base Tunnel, in Austria, helped to examine sealing options (hose injection of hydraulic mortar; or adhesive with epoxy resin bound mortar) to achieve shear joint strength where the wall elements fit into cross-passage openings. Research is further underway on sensor technology for remote observation, operation and predictive maintenance of the safety door.
It is seen that possibilities exist to install the wall element system in some new build tunnels, such as in Austria and Sweden, and there is some potential to examine speedy retrofits of existing twin tunnels.