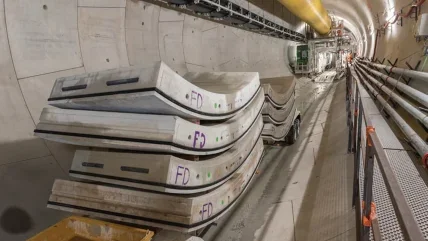
Steel fibre reinforced concrete (SFRC) was introduced in the European market in the second half of the 1970’s. No standards or recommendations were available at that time, which was a major obstacle for the acceptance of this new technology.
Since that time, SFRC has been applied in many different construction applications, such as in tunnel linings, mining, floors on grade, floors on piles, prefabricated elements, and more. In the beginning, steel fibres were used to substitute for secondary steel reinforcement bars or for as bars to provide for serviceability through crack control in less critical construction parts.
Nowadays, steel fibres are widely used as the main and unique reinforcement for tunnel lining . Steel fibres are also considered for structural purposes helping to guarantee the construction’s ability and durability in:
- full replacement of the standard reinforcing cage for concrete tunnel segments
- permanent sprayed concrete lining
This evolution into structural applications was mainly the result of the progress in SFRC technology, as well as the research done at different universities and technical institutes in order to understand and quantify the material properties.
This evolution into structural applications was mainly the result of the progress in SFRC technology, as well as the research done at different universities and technical institutes in order to understand and quantify the material properties.
Recommendations for design rules for steel fibre reinforced concrete started to be developed in the early 1990’s. Since October 2003, the Rilem TC 162-TDF Recommendations have been available for the design rules for SFRC.
However a lack of regulation and standards hampered the spread of the fibre reinforced concrete technology for final tunnel linings. With the publication of international design guideline the fib Model Code for Concrete Structures 2010, this obstacle has been overcome and designers are gaining more confidence in working with steel fibres.
The aim was to have the publication be a source of information for updating existing codes or developing new codes for concrete structures. It specifically addresses non-traditional types of reinforcement, such as steel fibres, that had reached a status of recognition in previous years, with special attention being given to the use of fibre reinforced concrete in structural applications.
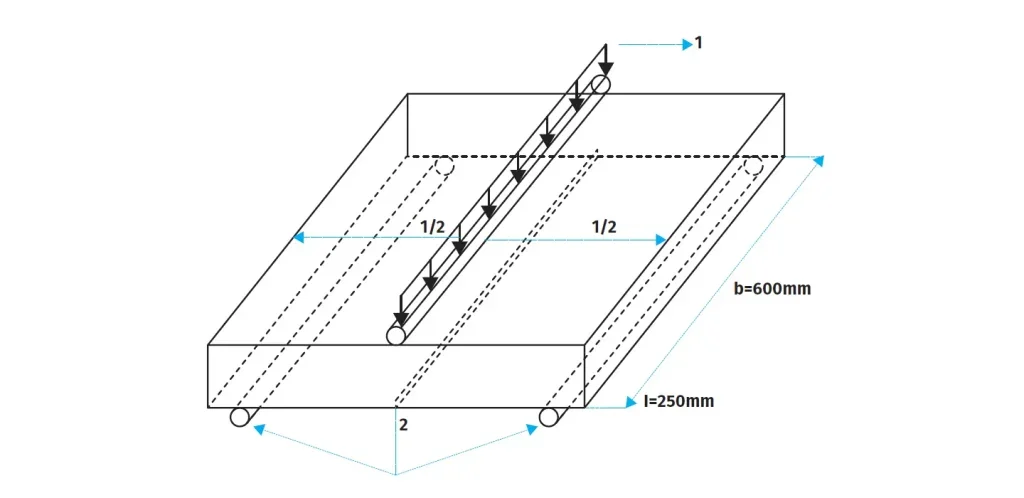
The Model Code (2020) – fib MC (2020) is also intended to be an operational document for normal design situations and structures. It is a single Code dealing with both new and existing concrete structures; that is, both the design of new structures and the various activities associated with the assessment, interventions upon and life-cycle management of existing concrete structures. This ambitious project has built upon the achievements of fib MC2010(2), published in 2013 and which was the previous edition of the fib Model Code for
CONCRETE STRUCTURES.
In 2022, EN 14487-1 was amended to include reference to the alternate notched specimen methodologies for residual flexural tensile strength determination; the following year, EN 14488-3 was then updated to include a notched panel test based on the EFNARC proposal.
This was significant, in that it linked the compatible standard conformance flexural test to the limit state design methods necessary to realise the potential for single pass permanent works SCL (PSCL) as had been advocated in preceding ITAtech guidance.
A number of test methods are used around the world to evaluate the behaviour of fibre-reinforced shotcrete (FRS) for permanent sprayed concrete linings (PSCL).
Confusion exists between strategies to characterise material by testing and then how to use information for design. A good understanding of some of the key concepts around the testing of FRS is therefore essential to avoid this kind of confusion and any other potentially controversial discussions.
European standard EN 14487-1 mentions two different ways to specify the ductility of FRS – namely in terms of the energy absorption capacity and the residual strength., respectively. It also states that both ways are not exactly comparable.
- The energy absorption capacity that is measured on a panel can be prescribed when – in the case of rockbolting – emphasis is put on the energy that hasThe method of designing the structure
- to be absorbed during the deformation of the rock.
- The residual strength method can be prescribed when the concrete characteristics are used in a structural design model. This is especially useful for permanent sprayed concrete linings
The design of Fibre Reinforced Concrete (FRC) structures, particularly of FRC tunnels, is usually made adopting the indication of fib Model Code 2010. This code is considered as reference documents in several guidelines for tunnels.
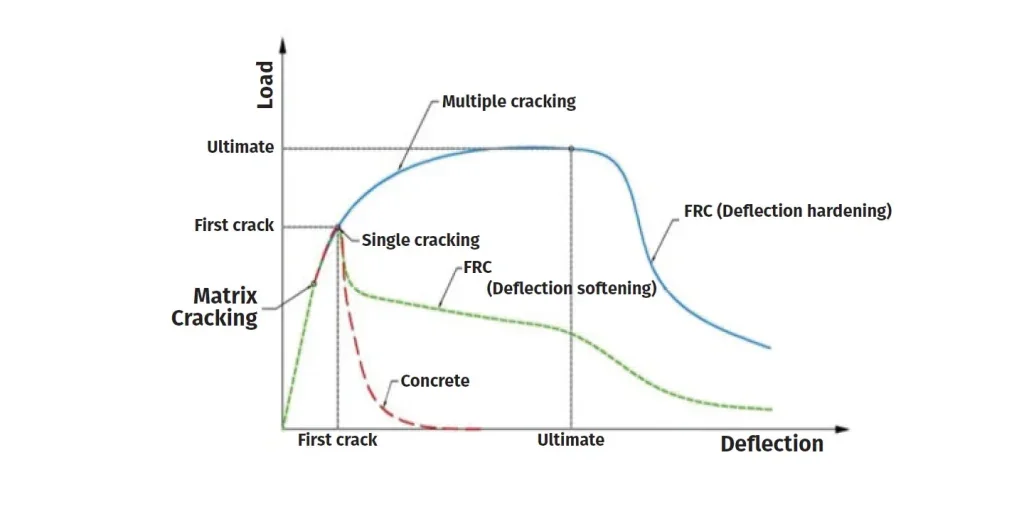
A practical method to determine the tensile behaviour of SFRC for shotcrete applications is a 3-point bending test on square panels (pr EN 14 4886-Method B)
- Ductility: verification is necessary to consider any benefit of steel fibres in the long-term; The design state-of-practice requires for FRC to exhibit Deflection Softening behavior.
- Deflection Hardening: is necessary to ensure the development of multi-cracking so that crack widths are controlled.
Nominal values of the material properties are determined according to pr EN 14-488-3 Method B. The diagram of the applied force (F) versus the deformation should be produced, a typical diagram is shown.
A joint document AFTES-ASQUAPRO group has developed recommendations for the permanent application of wet spray concrete in underground structure. This document (of about one hundred pages) provides general information and outlines the key basis principles. The main objective of the document is to provide assistance for the drafting of the technical specification in procurements contracts.
The document was drawn up with the participation of numerous professionals involved in sprayed concrete and undergrounds works, from both the private and public sectors, thereby heightening its legitimacy and making it a widely consensual reference document.
The different types of fibres are discussed and their field of application is specified. Steel Fibre only for PSCL.
The method of designing the structure by the Model Code 2010 is explained.
They cover both the sprayed concrete for preliminary support and the structural sprayed concrete, this latest being calculated to take up the long-term loads.
The methods for tensile bending tests on notched panel are specified according to EN 14 488-3 Method b as well as principles for their use, which is essential for structural concrete.
During works, it is thus advised to carry out thorough testing on Day 7, to be completed by additional testing at Day 28.
In addition to tensile bending tests, energy absorption capacity and early age hardening tests are discussed.
The programmes for design, suitability and inspection tests are detailed for both preliminary support and structural concrete, taking into account the specificities of each.
The method for calculating characteristic values is explained and the importance of using characteristic values and not average values is highlighted.
And even more recently, during the Word Tunnel Congress 2024 (WTC 2024), in Shenzhen, China, I was proud to present as vice Chair he new ITAtech guideline on ‘Low Carbon Lining’ which had been only just officially published.
The report is an ‘Executive Summary’ of approximately 30 pages. The chairman of this group in Dr Benoit Jones CEO/Managing Director, Inbye Engineering Limited who has accomplished a fantastic to job to allow the achievement and publication of this guideline.
The main aim of this guideline is to promote and encourage the use of low carbon concrete tunnel linings and to enable clients, specifiers, designers, suppliers, constructors, insurers and asset operators to feel comfortable using low carbon concretes in tunnel construction.
A few of the few main conclusions in the report are as follows:
- An urgent response to the climate crisis is needed now. We need to dramatically reduce emissions of carbon dioxide and other greenhouse gases (CO2e emissions).
Sustainability must be used as the decision-making framework, where social, environmental and economic factors are all considered. As part of this framework, CO2 saving must be a criterion in all decision-making.
- All parties – clients, designers, constructors and suppliers – must work together to reduce CO2e emissions and we must do it urgently. Leadership by the client, and incentivisation of CO2e emissions reductions through the design and construction contracts, is essential to achieving this collaboration
- The biggest reductions in CO2e emissions can be achieved during the planning and design stages. It is important, therefore, to try to quantify the CO2e emissions related to different options in a pragmatic way as early as possible to aid decision-making
- For tunnelling projects, by far the largest contribution to CO2e emissions is the Portland cement in concrete tunnel linings and annulus grout
- The second biggest source of CO2e emissions in the lining is the reinforcement. Replacing conventional steel bar reinforcement with fibre reinforcement can reduce this footprint in many cases
- For conventional tunnelling, if the sprayed concrete primary lining is designed to be permanent, i.e. durable for the whole design life, this can result in large savings in overall concrete volume. Either the secondary lining can be deleted (no longer needed), or its thickness and/or reinforcement volume can be reduced as the primary lining shares the load The possibility of using permanent sprayed concrete allows for consideration of this preliminary lining to carry the permanent load. In this case, the three possible solutions are:
- to consider the preliminary sprayed FRC lining collaborating with the cast final lining
- to consider the preliminary sprayed FRC collaborating with a further sprayed in a second stage
- to consider only the preliminary FRC lining as the final Stage
BOOST TO PARIS AND SUSTAINABILITY
With its important contribution to materials technology for construction of the Grand Paris Express tunnel project, Dramix fibre-reinforced concrete has been a boost to Greater Paris as it has prepared to host the 2024 Summer Olympic Games, starting late July.
Indeed, the French capital’s successful bid to host for the Olympic Games was built around this incredible infrastructure investment and development, which has a double purpose: to revitalise the capital along the banks of the Seine river; and, to upgrade transport systems in Greater Paris, that constellation of cities surrounding the capital and whose citizens move every day in their millions.
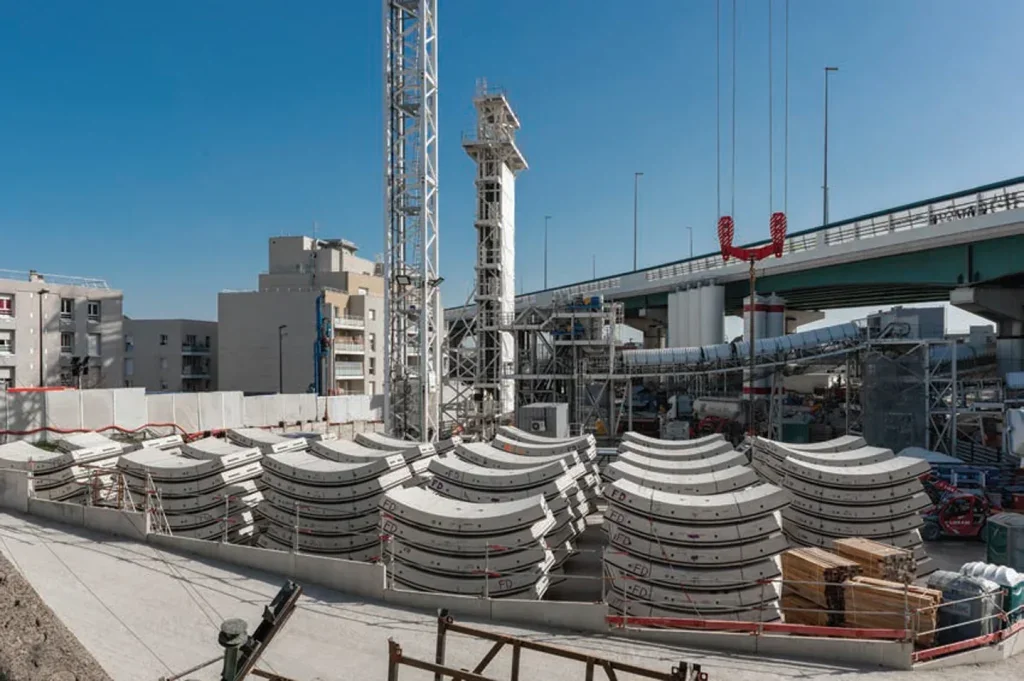
Project
The Grand Paris Express project envisions 200 km of automatic trains on subway lines, running almost entirely underground. It will extend an existing metro line (Line 14) and also construct four new lines (Lines 15, 16, 17 & 18).
The project has been under construction over recent years and is anticipated to be completed before 2030 with some key lines much earlier – in 2024. With 68 future stations and being expected to handle two million passengers daily, this new metro system will be transformative for transport across Greater Paris.
Technical
Building the Grand Paris Express has presented a host of technical, material, human, and environmental challenges. The project developer, Société des Grands Projets (SGP), has been solving them by adding innovation at every level, from design to commissioning.
Sustainability must be used as the decision-making framework, where social, environmental and economic factors are all considered. As part of this framework, CO2 saving must be a criterion in all decision-making.
All parties – clients, designers, constructors and suppliers – must work together to reduce CO2e emissions and we must do it urgently. Leadership by the client, and incentivisation of CO2e emissions reductions through the design and construction contracts, is essential to achieving this collaboration.
Grand Paris Express project is good example of this collaboration with major role of the client SGP (originally named Société du Grand Paris, created in 2010 to build the project but from that foundation and ongoing work now also has a nationwide remit to support other organisations with development of their express transport services).
This impetus for technical developments in support of greater performance for sustainability owes a lot to the early vision and work of Société du Grand Paris, which invited candidates to propose solutions, including through alternative offers. Thanks to the bond of trust between the actors, forged through the first results obtained, the candidates now offer fibre-reinforced concrete segments in their basic offers.
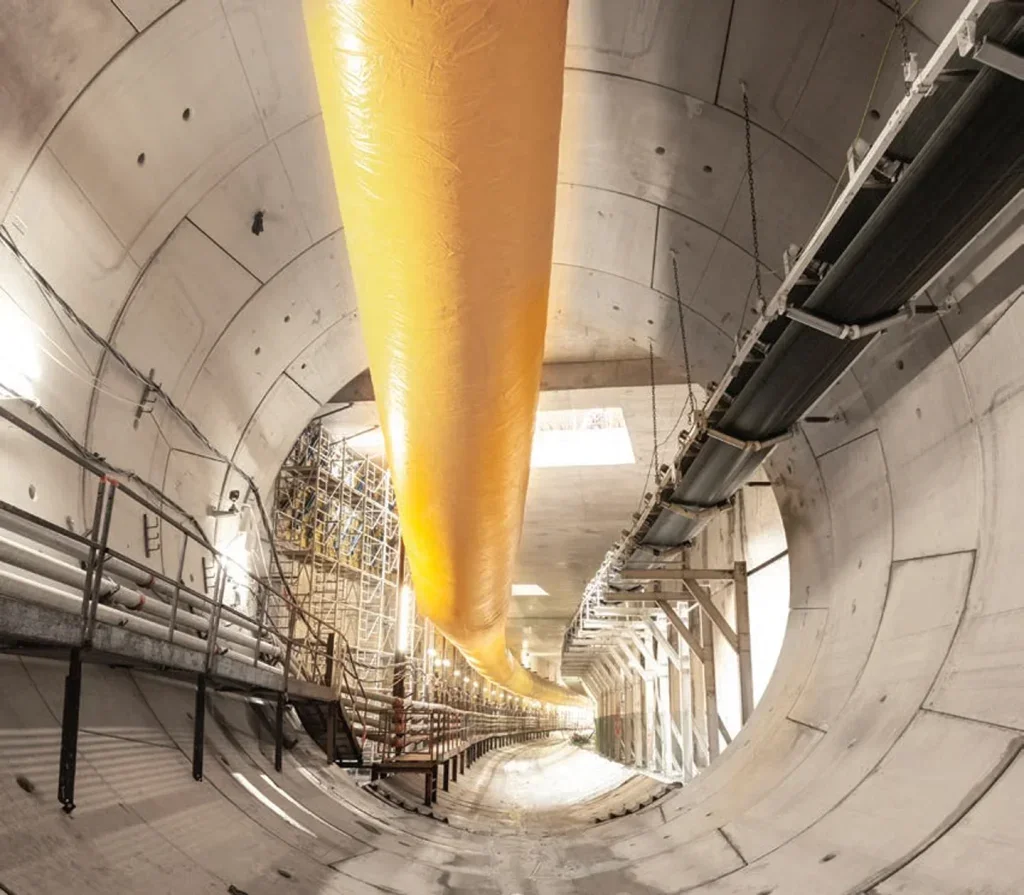
Sustainability
Innovation is what makes the Grand Paris Express project a driver of the ecological transition.
Building the Grand Paris Express will generate around 4.4 million tonnes of CO2, and more than 70% of those emissions come from using concrete and steel. The project has committed to a 25% reduction of the greenhouse gas (GHG) emissions caused by its construction by innovating and adapting the building methods being employed.
Approximately 90% of the new metro network being added through the Grand Paris Express investment is being built with concrete labelled low-carbon. The project is effectively asking construction companies to use concrete with a 40% smaller carbon footprint than conventional concrete.
Fibre-reinforced concrete is also being used to build the precast concrete segments on part of Line 16. This type of concrete only consumes half the resources as traditional steel bar reinforced concrete and cuts also CO2 emissions at concrete production plants and steel mills. The approach saves an average of 10,000 tonnes of CO2e for every 10km length of new tunnel constructed.
FRC was tested on project during early work on the extension of Line 14, which has opened for the 2024 Summer Olympic Games. The work was performed in 2016, during phase T2 of Line 14’s work at Saint-Ouen, north of Paris. In the works, contractor Bouygues Travaux Publics replaced the standard rebar with steel fibre for the reinforced concrete segments on two specific sections: the crossing area of the station ‘Mairie de Saint-Ouen’ over a distance of approx 120m (the new tunnel would only be temporary, to be removed during later construction work for the metro station); and, a tunnel reserved for maintenance.
There had already been experiments with fibrereinforced concrete in the past, also on Line 14 for example. But none of those tests were sustainable. The Grand Paris Express was the first infrastructure project of this magnitude where fibre-reinforced concrete (FRC) is used on a massive scale, considering use of Dramix 4D 80/60BG fibres. The resulting solution from the more recent work has been implemented on several sections of the new metro, the first being on Line 16.1 works, with contractor Eiffage Génie civil consortium, between Saint- Denis Pleyel and the Aulnay operations centre. This has also been a first in France for underground construction.
Benefits
While steel rebar in concrete has about 100kg of steel for each cubic metre of concrete, according to Alex Moubé, head of the low-carbon mission at SGP, the FRC version consumes half as much steel – 50kg – for the same performance. With steel consumption halved, there can be a saving of 5,000 tonnes of steel for 10km of new tunnel constructed. At the same time, it will make it possible to achieve substantial cost savings.