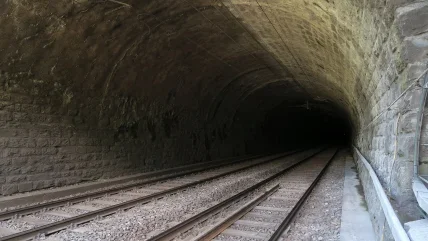
THE OPENING of the Lötschberg tunnel in central Switzerland in 2007 heralded a new kind of project, the very deep and very long transport tunnel. Running 34.6km long through under the Alpine mountain range its characterisation as a "base" tunnel was obvious.
It purpose is to flatten the route of railway tracks, keeping gradients to fractions of a percent and allowing modern high speed trains to pass at up to 250kph. Even more important is easing the wheezing climb for heavy freight, allowing us of 4,000t capacity trains, double the current size, and removing the need for supplementary locomotives. Millions of tonnes of goods currently travelling on lorries can go onto rail.
Few major tunnels had been built this long, the 50.5km Anglo-French Channel Tunnel, and Japan’s almost 54km Seikan undersea tunnel the notable examples. Outside mining there were none so deep, with most of it 1,500m below the surface and two points 2,000m down.
Lötschberg’s sister tunnel the Gotthard, due to open at the end of next year, is even larger at 57km and up to 2,200m deep. Another will follow to complete the same route axis, the Ceneri further south. Opening in 2020 this is a ‘mere’ 15.4km long, and 800m deep.
The focus then moves to Austria with three tunnels now in progress. Just just gearing up for its first major drives after several years of preliminary work, is the cross border Brenner Base tunnel jointly built with Italy. Its 55km length, or 63km if an adjoining upgraded existing bypass is counted in, puts it on a par with Gotthard though at slightly less depth, around 1,800m.
Two more are the Koralm and the Semmering both on the line south of Vienna to Graz and a new line from there to Klagenfurt. These are respectively 33km long and 1,250m deep, and 27.3km, with 800m cover.
Finally there is the Lyon-Turin project, this time at the western end of the Alps between France and Italy, again 55km long. Cover is an average of about 1,000m with a small length up to 2,500m. There are also feasibility studies for links through the Pyrenees and a scheme in planning between Argentina and Chile, the first to go through the Latin American Andes.
For all these tunnels there are special challenges; the sheer size of them as projects, the unknown geology, and special aspects at such depth, notably high temperatures in the rock, and other effects of high overburden including sudden rock fracture in the face, explosive rock bursts, squeezing ground and potentially extremely high water heads in faults. Logistics on such long tunnels are difficult and so too is disposal of the huge volumes of spoil.
"But a first issue perhaps is achieving certainty of the project itself" says Renzo Simoni, chief executive for AlpTransit with funding coming in phases as government approvals and international treaties are made to pay for investigations, and then project construction in sections. Particularly important is winning European finance for the schemes. All of the others are on key route axes for the European Union. Once commitments are made, things can move along. But a detailed period of investigation is crucial says Simoni. On Gotthard a conventional system of separate design and later construction was used, partly because of the need for extended geological probes. As well as drawing on past road tunnel experience across the Gotthard pass a multiplicity of deep boreholes investigations was carried out.
At Swiss consultant Amberg, one of the key firms on Gotthard, Yves Boissonnas elaborates. "One of the major challenges is the scale and complexity of the geology involved and to assess the risks, particularly as it is impossible to get a full picture at such depths.
"Data gathering must be very systematic particularly in identify the major go/no-go areas. For Gotthard these were the Tavetch, Sedrun and Piora Mulder areas. "It is in such valleys and synclines that the greatest issues are likely with difficult ground."
Initial studies guided the need for special investigations, most of all a 5.5km probe tunnel to investigate the notorious Piora Mulder syncline, where water saturated "sugar stone" weathered dolomite could have proved impassable.
At Brenner the decision was made to use a full-length exploratory tunnel he says, to best investigate the rock mass all along the route. Despite additional expense the benefit is a major reduction if the hydrological and geological risks he says. With some 20km of exploratory completed, he estimates "the improvement in geological knowledge and risk reduction is about 35 per cent.
"Also it allows a nearby exploration and perhaps treatment of the rock mass for the main bores running just above." The exploratory tunnel gives additional benefits, serving the main tunnels for as additional service access during operations and reducing needed closure time for maintenance. "And it is the drainage route, which means we can use a simple lidded open channel which is very easy to clean." Cleaning drainage is a significant maintenance task.
For the Semmering tunnel, in an area of very turbulent and mixed geology there has been a three phase approach with initial deep cores to select alignment options and to guide later stage cores up to 720m deep, says Josef Dallen at consultant iC consulenten ZT."I think we might have world record for the total core length relative to the tunnel."
An important source of exploration data is the creation of future access tunnels adds Alain Chabert, joint directorgeneral at Tunnel Euralpin Lyon Turin (TELT)the newly project company for the scheme now it has an international goahead. The Maddalena at the southern Italian portal and the Saint Martin la Porte at the north end are both important data sources, the latter identifying squeezing ground risks for further investigation via a 9km test bore just going ahead. The intermediate accesses are also crucial for construction logistics, breaking the tunnels into manageable sections he says "because from the portals alone construction would take 40 years".
CONTRACTS
Most projects keep tunnel sections at around 10-20km long which makes a "Goldilocks" size of construction contract possible says Simoni, neither too big and risk laden but not too small that it discourages international interest. "Our Swiss firms learned a lot from the big international firms." Around EUR 1bn (USD 1.1bn) was the right level Simoni says. He says too that it was important work on a unit price basis, and that risk is too high to try for lump sum arrangements. On Gotthard the contractors had to deposit a bond sum, forfeitable if they left the job uncompleted and covering cost of restarting. Contractors were also give flexibility to decide methods, most choosing TBM; only on the Sedrun section with heavily squeezing ground was it necessary to impose a conventional methodology, allowing for special support measures.
The TBM choice reflects a steady movement towards mechanised drives, from around 20 per cent on the earlier Lötschberg to 80 per cent or so on later projects, and with a shift towards segmental linings. Semmering will be an exception says. As well as intensive investigation detailed planning and preparation before the main project begins is vital says Simoni. "That particularly applies to how the spoil is disposed of, and locations for the many millions of tonnes brought out.
"We wanted to re-use as much as possible and instigated a special research programme to work out specific rock crushing and processing to allow it to be used for the aggregate in the concrete lining."
The Brenner base tunnel has also made rock re-use and rock disposal a high priority, particularly in locating small valley sites for disposal. A strong emphasis has been on avoiding motorways and valley roads through towns with the use of conveyors and extra spoil disposal tunnels.
For the Lyon-Turin a similar environmental focus is present but achieved in different ways. In Italy, with a strong railway network, a short extension to the line will allow train transport of spoil to disposal sites. At the French portal end there is some nearby disposal but possibly using trucks.
MANAGING EXPECTATIONS
One reason for success on Gotthard, due to run trains slightly earlier than planned at the end of next year, was a strong supervision and control at all levels with client staff integrated with the contractors on site.
"Monthly reports from site and detailed quarterly assessments were produced and these fed into a twice yearly report to government."
There was also a special parliamentary delegation of 12 members which concentrated on the project, and which AlpTransit has to report to six times a year on quality, risks, timetable and other factors.
"It was quite strict but also gave us legitimacy – they could not say ‘we did not know’ about something."
Keeping good client control is important at Brenner too says Bergmeister. For that reason BBT has kept a directly employed team of geologists to assess both the overall input to design and to constantly monitor the access tunnels and exploratory tunnel as they go.
"If you use outside consultants the information must be passed on, and every interface is a potential loss of data" he says. As a cross border project the Brenner faces an additional problem he says of disparate design and construction cultures. To counter that BBT has produced a strong set of design guides and templates he says for use throughout. The Lyon-Turin tunnel will face similar challenges.
A key aspect as construction gets underway is to be able to make some changes to the detailed design says Boissonnas at Amberg, particularly to take account of evolving technology in rail, signalling and power engineering. "The civil engineering is important but they have to remember that the hole they are making is just an envelope for the railway and trains. Questions can arise for example if a new kind of track switch might require some tens of millimetres of extra width." He says alterations are not always possible but there needs to be a possibility for change management.
Fast evolving technology is one of the key challenges facing the track, signal and mechanical and electrical contracts. Over a ten year or greater excavation period computerised and electrical equipment can go through one or more generations of design, and perhaps another during a four year long fit out. "The contract specifies that we hand over new equipment and that means we had to replace some computers for example three or four times," says Peter Huber project director for the Transtec joint venture.
"For Gotthard we let this work as one single contract," says Simoni "and here a lump sum is a better method". By including everything in one package the client can avoid extremely fraught interface issues, allowing the contractor to choose his equipment and integrate it, he says.
The logistics for the fitout are even more difficult than excavation says Huber. "We could only work from the portals." Some work required a 40km journey each shift for the workers.
A cascade of work ran along the tunnels, from lighting and axillary power to the complex and highly accurate high speed track laying using a purpose built concreting train. Then was signalling and power and ventilation. "But we did not do the mechanisms for the cross passage rooms and doors" he says.
A major challenge now is assembling the accurate documentation of what has been fitted, proofing tests and operation, all requiring many thousands of detailed files to be handed on says Huber. Train running trials for Gotthard begin this October