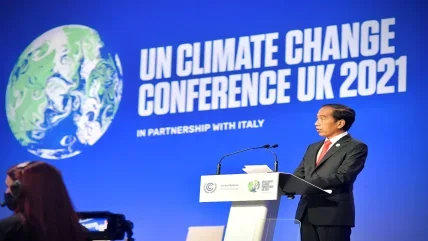
Climate change and the need for humanity to reduce carbon emissions are currently major considerations in all industrial processes and in particular the construction industry.
The COP 26 United Nations Climate Change Conference is scheduled to be held in Glasgow (31 October–12 November 2021) and will provide the opportunity for the showcasing of global efforts to reduce carbon.
Concrete is recognised as the second most widely consumed commodity on the planet after water. It also contributes approximately 8% of global carbon emissions; the main source of these emissions is the manufacture of Ordinary Portland Cement (CEM I). Figures vary from country to country, but it is generally acknowledged that the production of one tonne of CEM I emits approximately one tonne of CO2 into the atmosphere, while 1m³ of C40/50 CEM I concrete in the UK contains approximately 350kg/m³ of embodied carbon; when you add 100kg/m³ of reinforcement, this figure rises to about 405kg/m³.
A consequence of this is that there has been a focus recently on using ‘low-carbon concretes’ and almost all the major ready-mix concrete suppliers now market low-carbon concretes. These generally comprise a range of concretes with CEM I replacements of up to 70% by ground-granulated blast-furnace slag (GGBS). This could be considered as an example of marketing ‘smoke and mirrors’, since GGBS and other cement replacement materials, such as fly ash and limestone fillers, have been used extensively in UK concretes over the past few decades and are specified in BS8500-1 to be used in below-ground concretes with certain exposure conditions, such as groundwater sulphates and chlorides.
These ‘low carbon’ concrete packages are marketed as providing embodied carbon reductions of between 30% and 70% compared to a CEM I only concrete. In a large number of below ground structures, this comparison is not valid, since the exposure conditions and heat of hydration in deep sections could require the concrete to contain more than 66% GGBS replacement and, as such, no reduction in embodied carbon could be achieved by the use of a proprietary ‘low carbon’ concrete.
The major drawbacks of using high GGBS blends occur in the construction of concrete-frame buildings and structures. Concretes containing more than 50% GGBS content will tend to have long setting times and slow strength development when cast in columns, walls and suspended slabs at normal UK ambient temperatures. A consequence of this can be extended working hours for concrete finishers, longer striking times and back-propping of suspended slabs, leading to increased costs and programme.
A final anomaly is that due to the possibility of high GGBS-content concrete not being able to achieve its required characteristic compressive strength at 28 days, concrete suppliers will often increase the binder content of the mix design to compensate for this – thereby increasing the embodied carbon content of a concrete that is being used to reduce carbon.
With high cement replacement concretes, it makes more sense to specify a compliance age of 56 or 90 days. This will enable more rational and economical mix designs to be adopted.
Some major infrastructure and building projects are now beginning to specify a limit on the total value of embodied carbon in a project, rather than a percentage reduction that can easily be achieved by comparing a concrete that contains a moderate level of CEM I replacement with a pure CEM I only concrete of the same strength grade.
With CEM I being the major contributor of embodied carbon in concrete, it makes sense to either:
(i) reduce its content in concrete by as much as possible or
(ii) eliminate its use completely.
The latter option may seem incredible to most engineers but developments in geopolymer concrete and alkali-activated cementitious materials (AACM) in recent years have made it a distinct possibility. These are special concretes that do not contain any CEM but instead comprise replacement materials such as GGBS, fly ash, metakaolin and calcined clay; they are activated with the addition of alkali additives such as hydroxides and silicates.
AACMs are not new. Alkali-activated slag mixes were first developed in the late 1930s but their use did not become commercial until recently. In the UK, the introduction of Cemfree AACM by the David Ball Group has been assisted by the publication by BSI of BS PAS 8820: Construction Materials. Alkali- Activated Cementitious Material and Concrete(1). The development of this standard was sponsored by HS2 Ltd, the David Ball Group and Hanson UK. Commercially available alkali-activated slag concretes generally have characteristic compressive strengths which are typically lower than C25/30.
Geopolymer concretes are a subset of AACMs and were developed in the 1980s by Joseph Davidovits. Geopolymer binders can use a variety of waste products including fly ash, GGBS and mining wastes. These inactive wastes, which are high in aluminosilicates, must be activated by the addition of a strong alkali solution to produce an aluminosilicate gel similar to the material produced by the chemical reactions caused by CEM I.
Over the past 12 years, the Australian construction materials company, Wagners, has developed a geopolymer concrete it has named Earth Friendly Concrete (EFC) that can achieve characteristic compressive strengths up to C50/60 and has been used structurally in permanent works’ applications both in Australia and the UK. It comprises approximately 75% GGBS and 25% fly ash with alkali activators and special super-plasticising admixtures.
Figure 1 shows the embodied carbon values of cementitious blends per tonne of binder.
The use of low-carbon concretes to reduce a project’s embodied carbon should also be complemented by innovative design solutions that will probably involve the design assisted by testing and can reduce the thickness of elements and hence the volume of concrete in a structure. The replacement of conventional reinforcement with steel or synthetic fibres should also be adopted wherever possible.
TUNNELS AND EMBODIED CARBON
In a tunnelling project, it is generally considered that 60% to 70% of embodied carbon is contained in the concrete linings of the shafts and tunnels. It is paramount, therefore that the tunnelling industry does its utmost to significantly reduce or eliminate its use of cement in all applications – segmental linings, in-situ linings, sprayed concrete and annulus grouts.
In-situ shaft linings generally use high volumes of fly ash or GGBS. Piles and diaphragm walls often contain high volumes of GGBS in order to achieve the required resistance to any deleterious materials in the ground and groundwater, and also to reduce peak heat of hydration temperatures in thick sections. Similarly, high replacement levels are used in the casting of in-situ base slabs in shafts not only for exposure conditions but to reduce or eliminate the possibility of early-age thermal cracking in the slab. Replacement levels of up to 95% GGBS with only a 5% CEM I content are allowed in the latest version of EN206, but such mixes require careful design and construction planning due to slow setting and strength development characteristics. Therefore, the only option to further reduce the embodied carbon content of shaft linings and base slabs from their current levels might be to adopt the use of a geopolymer concrete.
The five shafts of the Lea Tunnel project several years ago were the deepest ever built in London. They were constructed by diaphragm walls using 70% GGBS content and then fully lined with a steel fibre-reinforced concrete containing 50% GGBS and 30kg/m³ of steel fibres that was slipformed. It is estimated that approximately 1,800 tonnes of reinforcement steel were eliminated from the shaft linings, reducing their embodied CO2 by more than 740t – achieved by innovative design and extensive pre-construction testing(2).
However, the use of high volumes of replacement materials is difficult in concrete used for precast segments and sprayed concrete, both of which require a very rapid strength development.
Sprayed concrete (or shotcrete) use in shafts and tunnels has been rapidly increasing since the widespread introduction of wet-mix steel fibre-reinforced shotcrete and robotic spraying in Europe in the 1980s and early 1990s. The development of alkali-free set accelerators that are added at the spraying nozzle has mostly replaced the highly alkaline aluminate and silicate accelerators in major projects, so that the in-place early strength requirements of the order of 1MPa at two hours of age may be achieved with a very small reduction of ultimate strength compared to the previous types of accelerators available.
Sprayed concrete mixes also tend to incorporate very high CEM I contents. In a recent UK project, the CEM I content used by the supplier was in excess of 500kg/ m³. This would give an embodied carbon content of the CEM I alone that is more than 430kg/m³. Varying levels of success have been experienced with replacements of CEM I with fly ash or GGBS – or both together – but CEM I contents are still generally more than 350kg/m³ and often in the region of 440kg/m³. If rebound, wastage and overspray of shotcrete are taken into account, then a further 10%–15% would have to be added to the total embodied carbon per cubic metre in place.
It would therefore appear that the largest reductions in embodied carbon per cubic metre of concrete in shaft and tunnel linings are available in the shotcrete sector. But it will be very difficult to achieve with current practice and technology, and the development of AACMs and geopolymer concretes for sprayed applications needs to be looked at rapidly. Similarly, the replacement of CEM I with a geopolymer binder in two-component annulus grouts has significant potential, and this type of grout is currently being developed in Germany.
In segmental lining production, heat curing is often applied to the freshly-cast segments in order to achieve a demoulding strength of approximately 15MPa within 6–8 hours from casting. In a major project, this can mean operating a curing chamber temperature of around 50ºC on a 24/7 basis for months or even years. This will also add to the carbon footprint of the segmental lining and is dependent on many factors, such as type of fuel, heat losses from the chamber and size of chamber.
Most segmental lining production in the UK incorporates a percentage of CEM I replacement materials, such as GGBS in the concrete mix, but normally not more than 40%. Should higher GGBS quantities, such as 70% or 80%, be included in the concrete then, due to the slower strength development of the mix, the heating regime may need to be increased by raising the temperature or length of time in the curing chamber (or both), thereby significantly increasing the cost and carbon footprint of segment manufacture.
A combination of cement replacements with fly ash and/or GGBS combined with the use of steel fibres can give dramatic reductions in the embodied carbon of tunnel lining segments when compared with traditional segments used in major projects. This was highlighted by Edvardsen et al(3) and is shown graphically in figure 3. It can be seen that even further reductions in embodied CO2 could be achieved with the adoption of the use of a geopolymer concrete.
It has been estimated(4) that if EFC geopolymer concrete replaced a normal concrete containing 30% GGBS in the 400mm-thick steel fibre-reinforced segmental lining of a 7.5m ID rail tunnel, then the embodied carbon of the tunnel would be reduced by approximately 1,840t per kilometre of tunnel. In a major rail project comprising 100km of tunnel, embodied carbon could be reduced by 184,000t.
The results of tests conducted by Wagners in Germany and Australia on steel fibre-reinforced EFC geopolymer concrete in recent years indicate exceptional performance in terms of strength and durability. The concrete has excellent physical properties in terms of compressive, flexural and tensile strengths, all of which are of the same or greater magnitudes as those of normal concretes. Water permeability, chloride penetrability and sulphate resistance are better than normal concretes. It also has three other extremely good properties that are very applicable to tunnels and shafts:
(i) a very low heat of reaction
(ii) good resistance to hydrocarbon fires and
(iii) excellent resistance to biogenic corrosion in sewer tunnels.
Geopolymer concrete has a very low heat of reaction and several ‘hot box’ trials have been conducted on the material on UK project sites in order to determine the peak temperature of reaction generated in a 1m² block of concrete. It was found that a maximum temperature rise of 15–16ºC was consistent in all grades of the concrete, regardless of binder content. Since normal structural concretes have peak temperature rises of 35–50ºC, the use of geopolymer concrete in deep foundations such as shaft base-slabs could reduce or eliminate the amount of anti-crack reinforcement required to mitigate early-age thermal cracking.
In Australia, Wagners recently fire-tested geopolymer concrete containing steel fibres and polypropylene fibres at the CSIRO laboratories(5). Concrete panels were placed in the furnace and were then subjected to the RABT-ZTV (Eureka) fire curve for hydrocarbon fires in rail tunnels. The results of the tests indicated a spalling resistance that was equal to the CEM I and 25% fly-ash concrete that is currently being used by Wagners in the production of segmental linings for the Cross River Rail project in Brisbane.
A few years ago in New Zealand, Watercare, the water provider responsible for the construction of the Auckland Central Interceptor sewer tunnel, realised that biogenic corrosion from the conversion of hydrogen sulphide into sulphuric acid in sewer tunnels was a huge problem and so decided to run a test program at the AWMC, University of Queensland(6). After one year in the biogenic corrosion chamber, the concrete samples were removed and their respective rates of corrosion were determined. The results showed that the geopolymer concrete had an even lower corrosion rate than calcium aluminate cement concrete – a material frequently specified and used in the repair of corroded sewer tunnels and manholes.
The very low rate of corrosion of geopolymer concrete could enable low corrosion, single-pass linings to be used in the construction of large-diameter sewer tunnels and possibly eliminate the need for HDPE liners and secondary in-situ linings, and significantly reduce a project’s carbon footprint.
THE CHALLENGE
The challenge to reduce carbon emissions arising from construction activities is enormous and will require innovative design and materials solutions – plus a degree of risk acceptance (something for the underwriters to consider, perhaps). But remember …. if we always do what we always did then we will always get what we always got.