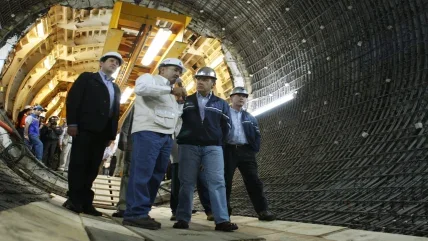
It has been called the most complex geology on earth. Constructing an 8.93m diameter tunnel 62km long is not helped when the city you are building under is itself sinking at a rate of 120mm/year.
Modern Mexico City was founded in 1521 on the site of the ancient pre-colonial city on five large lake beds; its first recorded flooding came 34 years later in 1555 and flooding is now severe and frequent.
A Brief History
Extraction of groundwater has depleted aquifers so much that the city has sunk by 12m in the past 100 years. The so called Grand Canal, 50km-long, was dug in the 1860s to take rainwater and effluent under gravity out of the Mexico valley basin but the city has sunk so much since then that the canal now has a reverse slope, towards the city instead of away from it. Pumps have had to be installed and its capacity has been drastically reduced. Even in 1975 it could convey 80m3/s; today it conveys only 42m3/sec.
Despite the challenging terrain a wastewater tunnel called the Emisor Central was hand-mined in the 1960s approximately 100m below ground. But that too has subsided by around 7m since 1975, and maintenance is problematic because it is in permanent use. The population, which doubled between 1970 and 2000, now stands at around 19 million and produces 40m3/ sec of wastewater; the capacity to remove it is only 10m3/ sec. Since the drainage system also has to handle rainwater, every rainy season brings flooding, particularly to the historic downtown and the airport region. The threat to public health was becoming critical.
A New Solution
In 2007, the then president Felipe Calderon declared the situation a National Emergency. Mexico’s national water authority, Conagua, commissioned the country’s largest infrastructure project in response. The 6m-diameter Tunel Emisor Central, the main sewage system of the city, was to be repaired after decades of overuse and corrosion, and its slope recovered. To enable this, a new tunnel, Tunel Emisor Oriente (TEO) would be constructed to convey the city’s waste to a new, major treatment plant 62km away. The design, construction and delivery were awarded to Comissa, a consortium of Mexican heavy civil contractors ICA, Carso, Lombardo, Estrella and Cotrisa, with Sweden-based Poyry among onsite advisors. Eleven years later, the tunnel was completed. Altogether six TBMs have been used to build it. It has been called one of the most challenging TBM projects in the world.
Funding came mainly from the federal government. The initial investment was MXN9.6bn (US$433m) Today, after 11 years’ work, the project is nearing completion. “Tunnelling work finished in November 2019,” says Roberto Gonzalez, general manager for Robbins in Mexico. The achievement is not to be underestimated. “On parts of the southern plain we were tunnelling through very old clays with lacustrine deposits and a water content that made it like a jelly.” Another description is ‘abrasive basalt sections mixed with sections of watery clay that have been compared to soup.’
During the decade of work, strategies had to be re-thought several times thanks to the difficult and unforeseen ground conditions. These ranged from very soft clays to highly abrasive hard rock and volcanic boulders, with high water pressures that reached six bar.
The project was divided into six lots, each with its own TBM; some of the lots required multiple modifications of the TBMs and frequent hyperbaric interventions, with operatives entering through air locks to work at the face under conditions of several atmospheres of pressure.
The entry shafts for the lots were equidistant at 10km apart. This was to prove an unwise decision, says Gonzalez. Each section contained several different geologies, to be tackled by the single TBM assigned to that section. Better, he says, would have been to divide the lots by geology rather than distance, so that TBMs adapted to each geology could be used without modifications mid-way.
A few geotechnical Problems
The TBMs were EPBs, three from Robbins, three from Herrenknecht. Unusually, the early decision was made that the TBMs should be purchased directly by project owner Conagua, which delivered them to the contractor Comissa. The reasoning was that this was an emergency project and the decision was intended to speed the start of construction. But it brought disadvantages: there were grey areas, such as responsibility for replacement parts and maintenance. “In my opinion, a shared risk can work when the right geotechnical information and tunnel design is in place from the beginning, but in this case it [shared risk] created many delays while agreements were negotiated over important economic decisions,” says Gonzalez.
And one of the key features of the Emisor Oriente tunnel and its problems is that the right geotechnical information was not there at the beginning. A total of 64 borehole tests were conducted along the tunnel route, but a baseline geological report was not finished until 2010, two years after tunnelling began. This again was a consequence of the emergency nature which characterised the project.
The six starting and receiving shafts for the TBMs ranged in depth from 23 to 150m. Almost as soon as it was installed, one of the Herrenknecht machines, that assigned to Lot 1, ran into trouble – through no fault of its own. Flooding burst into its tunnel and all but submerged the machine. Fortunately the waters did not reach the electricity supply, mounted high in the TBM; but the incident cost six months’ delay.
Lot One was a high-priority section that was being fast-tracked in order to relieve chronic seasonal flooding; so, early in 2011 the Robbins machine originally slated for Lot 5 was instead set to bore a 3.9km-long section on Lot 1. “The EPB proved itself and its conveyors in the sticky clays of Mexico City with very high percentages of water content, up to 400%,” explains Gonzalez. It achieved rates of up to 592.5m in one month — considered a record among the six EPB TBMs on the project.
Muck removal was via the TBM’s screw conveyor then onto a belt conveyor through the tunnel. The vertical conveyors in the shaft took the muck to the surface for removal to landfill by truck. Primary linings were cast in place, using telescopic formwork and 350mm of concrete; secondary linings were concrete segments, giving a finished internal diameter of 7m.
After completing the bore in just 15 months, the Robbins machine was dismantled, removed, and sent to its original Lot 5 site, where modifications were made to it for the challenging mix of geologies of that section. “That particular machine worked in two very different worlds,” says Gonzalez. Modifications were also applied to the TBMs for Lots 3 and 4. A seven-bar air lock with a decompression chamber was fitted, to allow two teams to work under pressure at the same time. Chromium carbide plates reinforced the screw conveyor, and removable wear plates were added to each of its turns to withstand the abrasive hard rock. The conveyor casing was redesigned to open lengthwise (‘coffin-wise’, as the engineers refer to it) so that the condition of the screw could be monitored and worn plates replaced. An air compression system controlled water inflows in the chamber. The rotary union joint was redesigned to reduce the time needed to change the centre disc cutters; and the scrapers were redesigned the better to resist load impact.
The entry shaft for Lot 5, at 150m, was the deepest civil works’ shaft in Mexico. Its construction method was unique. A hydro-roadheader excavated sections of diaphragm walls up to 100m deep. After the complete circumference of the shaft had been constructed the rest of the excavation was continued by traditional shaft sinking and by cut-and-cover. At the bottom of the shaft a 28m starter tunnel was excavated to give space to assemble the TBM.
Mucky Problems
After only 250m of excavation, the Lot 5 TBM encountered new geology. Sticky greenish clay with very little water made it difficult to properly extract the material through the conveyor system. It clogged the muck discharge chutes and dropped from the vertical conveyor which was intended to take it to the surface. Much of it ended up at the bottom of the shaft. The contractor had to make stops for cleaning. The cutterhead clogged, which was tackled by using more additives to reduce wear.
The ground changed radically again, to hard clay, silty sand and isolated gravel with high water pressure. After shaft 19 yet another condition was met, of hard basalt, again with high water flow of 200L/sec. Wear on the cutting discs called for regular inspection and changing which the complex geology had not allowed to be foreseen. “Normally interventions are mostly done for inspection purposes” says Gonzalez, “but in this case the presence of cutting tools in the muck required many interventions over a period of more than 20 days for tool changes when high water flow was at its peak.”
Ground conditions improved after that but pumice fragments, sand with gravel, lava deposits, alluvial fans with boulders, sand matrix and high waterflows all contributed to the challenges and uncertainties of the Lot 5 TBM. Even so, breakthrough finally occurred in February 2019.
Meanwhile in neighbouring Lot 3, operated by contractor Carso, the TBM was encountering similar, and worsening, conditions. Partial rock and soil at the face caused impact loading on the cutters and cutter mounting system, and severe wear on the cutterhead. Fines in the excavation face caused clogging and required significant quantities of foam to be used.
When the TBM reached shaft 11, 3.2km into its 9.2km drive, modifications were made to it. A new screw conveyor was fitted with Trimay wear plates, the better to handle abrasive rock chips; a redesigned cutterhead with adjusted cutter spacings and more wear plating was fitted, and these successfully carried the machine to breakthrough.
The Lot 4 machine, with a 10.2km bore, encountered perhaps the most testing conditions of all. Around 405m into its drive, scrapers, parts of the mixing bars and other wear materials appeared along with rocks in the excavated muck. A cutterhead inspection was necessary; with high pressures, up to 3.5 bars, it would have to be hyperbaric. In June 2013, engineers entered the airlock for the first hyperbaric intervention through a TBM ever performed in Mexico. It was the first of many: more than 50 hyperbaric interventions took place to change cutting tools in a very complicated and harsh environment.
Later interventions were undertaken at atmospheric pressure. Despite the challenges of pumping out up to 180L/sec of water, and cleaning fines from the tunnel each time, these interventions were still quicker and lower in cost than those done hyperbarically. In all of these interventions, a double pumping system, at both the TBM and the shaft, was required. By the time of breakthrough in May 2019, the machine had achieved a project record of 30m in one day, and 528m in one month.
Yet the project did not give up on its surprises. A sting in the tail, almost at the end of the project, was where a Robbins machine encountered a blockage to the shield in a geology of rock over soil and became stuck. “To move it forward we had to use the exceptional pressure hydraulic system to give extraordinary thrusts” says Gonzalez. “We reached a pressure of 596 bar on 28 thrust cylinders.” The huge push released the machine, which achieved breakthrough shortly after.
The project was originally scheduled to be completed in mid- 2012. The tunnel was finally inaugurated on December 23, 2019. The final construction cost was MXN33.8bn (US$1.5bn), three and a half times the initial estimate.
Many factors contributed to the delays. “With hindsight, more accurate geological knowledge before the project started would have helped considerably,” says Gonzalez. “Contractual disputes, the high wear on cutters and screw conveyors and the hyperbaric interventions all contributed to delays; not enough money was invested in spare parts, which also resulted in lost time.”
Nevertheless, the tunnel is now complete and functioning. “Not only is it carrying its own flows; we can now divert wastewater to it from the Emisor Central during the dry season, so we can service that older tunnel when we need to.” The treatment plant at its outlet, the largest in Latin America, is functioning and treats 36m3/sec. A project which was going to be exceptionally challenging in the best of circumstances has been successfully brought to fruition.