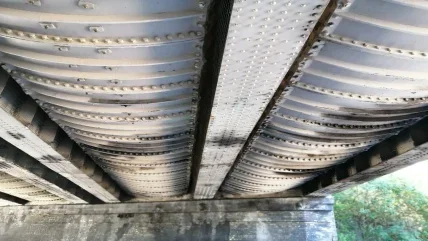
INTRODUCTION
On the 25 May 2023 at the Institution of Civil Engineers, in London, Dominic Barlow, Senior Project Manager, and Adam Evenden, Project Engineer, with J Murphy and Sons Ltd (Murphy) gave a presentation on the North Bristol Relief Sewer (NBRS) Project constructed between 2019- 23 for client Wessex Water (YTL Ltd), and with Aecom as Lead Designer.
PROJECT OVERVIEW AND SCOPE
Wessex Water had identified the need for a new attenuation sewer scheme located in the North Bristol area to alleviate flooding (see Figure 1). The scheme was required to relieve flows and alleviate flooding the existing Frome Valley Sewer and reduce future discharges from CSOs in the area. The new capacity in the network would also contribute to the significant local development of circa 85,000 new properties due to be built over the coming decades. The scheme was designed to future-proof the sewerage system in the area for the next 100 years.
The outline scope of the project was to provide a connection between the existing Frome Valley Sewer in the north and the Bristol Trunk Sewer in the south, as well as six other smaller sewer connections along the route. The new sewer was required to have an attenuation capacity of 38,000m3.
At the tender stage, Murphy investigated 71 different solutions and permeations on how this project could be built. The solution developed was for the following: 5.5km-long DN2.85m segmentally lined tunnel; 1.0kmlong DN1.8m open-cut pipe; 450m of pipe-jacked tunnel; 115m of auger bored pipe; 2No 30m-deep 6m i.d. shafts; and, 14No access chambers.
PROJECT DESIGN DEVELOPMENT
In the Instructions to Tenderers, Wessex Water provided indicative horizontal and vertical alignments of the proposed sewer. At that stage, Murphy sought to optimise and simplify the design by making some significant alterations.
The horizontal alignment that Murphy proposed removed kinks and smoothed curves, maximised straight sections of the tunnel, and reduced the disruption and risk associated with long lengths of pipe jacking under residential properties. Murphy proposed four significant changes to the original horizontal alignment: new location for the TBM drive site to move it farther away from residential properties; removal of two shafts (MH08 and MH11); and, to move the position of one of the remaining 30m-deep shafts to account for the changes in the tunnel alignment. These four changes can be seen in Figure 2.
The vertical alignment was also optimised by Murphy during this stage with the main change being to convert the route into a single TBM drive instead of the 3 drives that the original design would have required. This would reduce the impact on third parties and provide programme and cost benefits to the project.
In addition to the alignment development, there was also a considerable amount of value engineering done around the deep shafts on the project. The minimum acceptable size for the two 30m deep shafts was selected to be 6.0m i.d.. This was due to the expected excavation equipment and the requirements for the TBM to pass through the bottom. Further value engineering was employed by Aecom who developed a bespoke solution for the internal weir walls – to install an overflow weir pipe, replacing the traditional weir walls that would have increased the project cost (see Figure 3).
During refinement of the original design, the tender team removed the need to build two additional deep shafts (MH08 and MH11), which also represented a carbon saving of approximately 118 tCO2e to the project.
A key temporary works area in project design was the TBM Launch pit, the main requirement for which was to be able to fully assemble the shield before the start of excavation. The solution was to construct a 6m-deep, 8m-wide and 65m-long sheet piled pit with surrounding steel waler beams and one level of steel props (see Figure 4). The launch pit was designed to have three main lifting zones, where the prop spacing was increased to allow for the TBM logistics. In addition, the front two props were designed to be removable for a short time to allow for the TBM shields to be lifted into position.
During the design period, it was key to estimate the expected ground conditions. From the ground investigation (GI). It was expected that most construction would be undertaken in weak Mercia Mudstone (0.6 MPa – 25MPa), with some evidence of small sections of weathered Mercia Mudstone. Following the contract award, Murphy undertook some additional GI and identified the potential for an approximately 600m-long section of strong basal conglomerate that was located within the tunnel horizon and also one of the remaining deep shafts, MH09. From the GI, the maximum groundwater head was expected to be around 33m (3 bar – 3.5 bar) at various points along the alignment. Figure 5 shows the face of the tunnel excavation during the anticipated ground conditions.
PROJECT CONSTRUCTION Site Establishment
Construction work on the project started in August 2019, following three months of ecological mitigation works. The first stage of works was to establish the main TBM tunnelling compound and three satellite site compounds (two deep shaft sinking sites (MH09 and MH10), and the TBM reception site at MH12. At this stage, heavy earthworks were undertaken at the main compound to alter the topography enough to allow the TBM compound to be constructed, as shown in Figure 6. Several bespoke temporary works designs were required, all undertaken by Murphy’s in-house design team, Murphy Applied Engineering (MAE).
TBM Refurbishment
Whilst the site establishment stage of the project was being undertaken, the refurbishment of the TBM began at Murphy’s Ollerton facility between the summer of 2019 and the of spring 2020. All the refurbishment work for the TBM and ancillary equipment was undertaken by the in-house team of specialists supported by key suppliers.
The TBM that had been selected to complete the tunnel drive was a Murphy-owned Lovat EPB machine (called ‘Fionnuala’), originally manufactured in 2001. All the backup ancillary tunnelling equipment, rolling stock, grout silos, TBM services, etc., were also supplied from Murphy Plant.
One of the primary refurbishment tasks was modification of the TBM cutterhead. The EPBM had the option of two cutterheads – a soft rock option with ripper tools only or a hard rock option with cutting discs or ripper tools (via adaptor boxes). The anticipated ground conditions led to choosing the hard rock cutterhead with ripper tools and to have a contingency set of cutting discs available, if required, when tunnelling through the conglomerate section.
However, with the hard rock cutterhead there were concerns that the original opening ratio would cause clogging in the Mercia Mudstone, where smectite was anticipated. To mitigate this, Murphy developed a concept design to increase the opening ratio. This concept was then sent to Lovsuns in Canada, where a design and finite element analysis was undertaken to confirm that the structural integrity of the cutterhead would not be compromised with these modifications. The existing cutterhead was modified in line with the design applied to this machine (see Figure 7).
Tunnel Construction
Following the completion of the site establishment and TBM refurbishment, tunnelling started on the NBRS project in the summer of 2020. Below are some key facts about the tunnelling.
- The tunnel ring was a 2.85m i.d. trapezoidal ring, consisting of six equal-sized segments, 1m long and 180mm thick. The ring design had a 40mm taper to allow for steering for the tunnel.
- Grouting of the tunnel lining was undertaken using a traditional two-component grout mix that was pumped through the cast-in port in the lining.
- Spoil was removed during tunnelling via rail-bound spoil wagons hauled by a battery-powered Schöma locomotive.
- The TBM launch pit was serviced by two overhead gantry cranes (10t for segments and ancillary equipment/ supplies and 12t for processing the spoil wagons).
- The labour arrangements on the TBM were through a direct delivery model where the key operatives on the TBM were directly employed by Murphy, which was then supplemented using well-known labour suppliers for the backup positions.
- The TBM operated on a 5×2 shift pattern allowing for 10hr of production time and 2hrs planned maintenance at the end of each shift, Monday-Friday. Planned production-stops for maintenance were carried out over the weekends.
- Along the tunnel alignment were multiple third party crossings, including the M5 carriageway, rail lines, a flood attenuation reservoir and a high-pressure fuel main. All of these were successfully crossed without the installed monitoring showing any breach of agreed trigger levels.
Figure 8 shows an overview of the tunnel drive site during the construction stage.
CHALLENGES ENCOUNTERED DURING TUNNELLING
In the tunnelling phase of the project the TBM encountered some significant challenges, these can be broken down into three areas:
- The extent of conglomerate, sandstone and siltstone bands was larger than anticipated, resulting in higher cutting tool wear and slower advance rates at times.
- Significantly higher than anticipated groundwater flows were encountered between Ch2500 to Ch4000 (Ring1500 – Ring3000), which coincided with mixed ground conditions.
- The COVID-19 Pandemic and associated resource supply issues. To overcome these challenges the project team had to develop a range of technical and innovative solutions.
Challenge 1
To overcome the first challenge ,Murphy commissioned Maxwell Geosystems to prepare a 3D ground model based on the available GI. Due to the extent of the conglomerate, sandstone and siltstone being larger than expected, it was important for the project to gain a better understanding of the upcoming ground conditions to allow for more accurate forecasting of production rates and cutterhead tool wear.
The key aspect of the Maxwell model is that it was a geostatistical model that assigned a probability to each different type of ground condition. This probability was shown through the opacity of the colours on the 2D sections (every 20m) and long sections of the tunnel. The higher the uncertainty in the model the more the opacity would decrease for that colour (fading to white). This is shown in Figures 9-10 where a comparison between two different sections can be made. The top image shows the model with only the tender boreholes, as can be seen there are large sections of it within the tunnel alignment that are showing an increased level of uncertainty. When the additional GI is fed into the model these areas are shown as a much darker shade of brown and yellow as the model is more confident of the geology that will be encountered.
The team used this information to provide a more accurate forecast for tunnel production rates. This allowed better planning of key tunnelling operations, such as third party crossings and planned maintenance.
In addition, Murphy commissioned for the data from the Maxwell model to be used in a study on Machine Learning (ML) that was undertaken, post PhD, by Dr Jake Rankin. The ML study aimed to provide a better forecast of the tunnelling production rates. For more information on the study, please refer to the BTS Harding Prize lecture, and related paper in T&T, where Jake presented how the ML works and the outputs it provided to the site team.
It is important to note, however, that whilst these techniques helped to improve production rate forecasting, it was found that they weren’t perfect. Differences were still encountered between these models and the existing ground conditions that required the production team to react during tunnelling. This also highlights the need to continue developing technology and solutions for improving forecasted tunnel production rates.
The Maxwell model and ML were not the only solutions to the first challenge – the TBM was still required to bore through the larger than anticipated zones of conglomerate, sandstone and siltstone. To optimise advance rates and minimise cutter tool wear, the lacing pattern of the tools on the cutterhead was changed multiple times to suit the varying geology. Generally, tools changes occurred at 700m intervals in the mudstone, 70m in the conglomerate and 15m in the sandstone (40MPa -70MPa).
Challenge 2
The second significant challenge was the higher than anticipated ground water flows experienced between 1,500m and 3,000m into the tunnel drive. In this area, the TBM struggled to advance using EPB pressure to balance ground water with the use of ground conditioning chemicals, and, as such the spoil quality deteriorated into a slurry, creating tough working conditions.
Prior to this zone, spoil conditioning was managed as had been planned, using a range of ground conditioning products.
The slurry was also causing problems on the surface as the spoil was not suitable for disposing off-site via road lorries without additional measures to make the spoil more cohesive. Due to this, a complex water management strategy was required to continue excavation and increase the production rates of the TBM. The strategy can be broken down into measures required at the face, in the tunnel, and on the surface, respectively.
The measures at the face consisted of three main options, the first to create a grout block behind the TBM shields. To do this, it was required to stop the TBM advance and back grout the last 20m-30m of tunnel to fill any fissures in the area that the primary grouting had failed to seal. The grout would then be left to cure for approximately 5hrs and then production could resume. Whilst this method initially proved effective at controlling the water flows and improved the quality of the spoil, the benefits were short-lived. When the TBM resumed excavation, it would intersect new fissures and the spoil condition would begin to deteriorate again. The benefits from the grout block would typically last 10m-15m, which was approximately a day’s worth of production. This method was eventually discounted as it did not provide a large enough benefit to counteract the loss in production required to create it.
The second option developed at the face was to alter the primary grout in strength, consistency, and its properties to prevent wash out and maintain refusal pressure. Alternative admixtures, such as limestone fillers and polymers (anti-wash-out additives), were developed into a suitable set of mix designs that could be used with the TBM’s grout system. These alternative mix designs proved effective at maintaining a refusal pressure on the primary grouting. However, to achieve this, at times the grout volume required would be three times higher than the theoretical amount. During these trials, there was little relationship seen between the different grout mixes and the quality of the spoil the TBM was producing.
The third option used at the face was a depressurisation system installed as close to the excavation face as possible. A series of bleeders were drilled through the tunnel lining, using the existing grout port, into the surrounding rock mass. These bleeders were then connected to a pipeline that ran the length of the tunnel and discharged clean water into the water treatment system (WTS). These bleeders would act like well points and passively reduce the water pressure in the surrounding rock mass. This meant that during the excavation and ring-building cycle of the TBM, less ground water would reach the excavation chamber, which remained at atmospheric pressure, and therefore the consistency of the spoil would be improved. Figure 11 shows the depressurisation system developed for the project.
Further to the measures being used at the face, solutions were also implemented in the tunnel, such as using multiple trains per advance to account for the loss of volume in the spoil skips being taken up by water instead of spoil. By not allowing the skips to overflow with slurry it would improve the working conditions on the TBM and also help to minimise any effects to the logistics system. In addition, there was a continuous cleaning regime required to clean the inverts in the tunnel of any slurry that had built up. A specialist vacuum pump and a small conveyor belt were used to minimise manual handling.
The last section of the water management strategy was to apply measures on the surface to handle and process the slurry spoil that was being produced from the TBM. The first part of these measures involved mixing drying agents (cement, polymers, and bentonites) into the slurry spoil that would absorb the free water and make the spoil suitable for disposal from the site. This additional stage proved very effective and enabled the project to continue removing spoil from the site. However, it took time and space to carry out efficiently. To improve this process an additional spoil handling bay was constructed on site to allow this stage of the spoil management plan not to limit the production rate of the TBM.
In addition to the spoil management on the surface, the WTS was frequently overwhelmed by the volume of slurry it was required to process and this would mean the TBM had to stop production until the WTS had been cleaned. The WTS was not sized or designed to be processing the actual volume of slurry being produced. To assist with this problem a small slurry treatment system was established to process the slurry originally entering the WTS. This allowed for the discharge standards to be maintained, meaning that the TBM production rate would not be limited by the WTS capacity.
Challenge 3
The third significant challenge faced by NBRS was that of the global, COVID-19 pandemic. The pandemic struck right at the start of the tunnelling phase and caused the works to be delayed by three months whilst the SSOWs were produced, and the project was able to procure enough PPE/RPE in accordance with the SSOWs to safely commence tunnelling within a small diameter tunnel.
The project’s approach to managing the risk of COVID was to zone the worksite and tunnel (including the TBM).
There were three zones created:
- Green zones, which meant no additional PPE or RPE was required and that the 2m social distancing could always be maintained.
- Amber zones, where operatives were required to always be equipped with additional PPE/ RPE but would only be required to put it on when the 2m social distancing could not be maintained.
- Red zones, where it was not possible to keep the 2m social distancing at any time and therefore additional RPE/PPE had to be worn (for example, in the passenger cart of the rolling stock).
In addition to the zoning control, the project were early adopters of a testing regime when the testing kits first became available. Initially, testing was completed daily to identify any cases early and then isolate those associated individuals/teams. As the guidance began to relax testing was reduced to 3 times/week, where it stayed in place for the duration of the tunnel drive.
Production rates
The table summarises the tunnel production rates and the impact of the challenging ground conditions.
CIVILS CONSTRUCTION MH01 and MH12
To construct the upstream (MH12) and downstream (MH01) connections into the existing sewer, two large reinforced concrete chambers were built. These were constructed within large temporary sheet piled pits established around the existing live sewers. The reinforced concrete chamber was then fully built around the connection points, which required a series of bespoke temporary works that were provided by MAE.
One of the key temporary works undertaken on the project was to support the existing Frome Valley Sewer, so that it could be undermined to create the new MH12 connection point and still remain live. This was achieved by using a bespoke solution consisting of flat slings, universal beams, and tie bars, as shown in the right-hand side picture in Figure 12. Once the chambers had been constructed the final connection into the existing sewer was made, this was then closely followed by placing the cover slabs to isolate the sewer. This sequence and method of construction minimised the risk as far as practicable of working in a confined space live sewer environment. Figure 12 below shows a series of the bespoke temporary works and lifting arrangements that were required for these two manholes.
MH10 and MH09
The two deep shafts on the project were constructed using traditional underpinning techniques to full depth. During the construction of MH09 shaft sinking was paused to install a portal frame that would later allow the recption of a 1.2m i.d. pipe jacking machine. Shaft sinking was also paused in MH10 to complete a 116m-long 0.45m i.d. auger bore drive that would eventually connect to another section of the existing sewer network. Figure 13 shows the shafts during various stages of construction.
SOCIAL AND COMMUNITY ENGAGEMENT
Throughout the project, the Murphy team developed and maintained strong, efficient, and collaborative relationships with the client, 3rd party stakeholders, supply chain and end users. It was anticipated early in the conception of this project that a key element for success was going to be community engagement so Murphy employed a dedicated stakeholder manager who helped the client to identify and manage key stakeholders, such as Ambition LW, The Lawrence Weston Community Farm, and various schools within the area. In recognition of the approach to community engagement, the project was awarded an Excellent Rating for the Considerate Constructors Scheme.
The project also:
- Considered key sensitivities during the design of the project such as the use of electric plant where possible and situated key construction elements such as the TBM drive site and the two intermediate shafts as far away from residential properties as possible.
- Had a close working relationship with the emergency services including the Hazardous Area Response Team (HART) and the Urban Search And Rescue team (USAR) and allowed them to use areas of the site to undertake various mock exercises.
- Engaged in various STEM activities in both the local schools and University of Bristol
LESSONS LEARNED
During the design and construction of this challenging project, many lessons were learnt that Murphy will take forward into future tunnelling projects. Below are the five key lessons learned:
- Early design engagement with the client was effective in optimising the design solution (alignment modifications and deletion of shafts).
- The use of a geostatistical 3D ground model and the award-winning ML programme that was developed on this project proved effective at estimating production rates through unproven ground conditions. Murphy is continuing to undertake R&D in this field and looks to take this further into future projects.
- Early engagement with the supply chain worked effectively through COVID-19 at minimising the impact.
- Murphy’s in-house capabilities all proved effective at supporting the project as and when the various needs arose and demonstrates the full breadth of Murphy’s capability.
- Murphy Applied Engineering,
- Murphy Plant Ltd,
- Murphy Ground Engineering,
- Murphy Electrical Services,
- Murphy Welding Services
- Murphy Pipeline Services,
- Whilst no single type of TBM would have been suited to all the ground conditions encountered, some spoil handling and grouting variations would have been beneficial when dealing with the challenging ground conditions. For example, a TBM that had the screw in the invert of the cutting chamber, and tailskin grouting may have improved the working conditions within certain elements of the tunnel drive length.