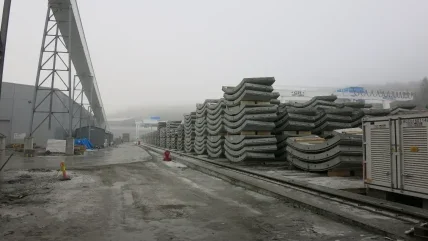
THE NORWEGIAN TUNNELLING MARKET is booming with a lot of upcoming projects for road, rail and tunnels. Two of the main projects are the coastal highway route E39, crossing the Sognefjord with a budget of more than EUR 40bn (USD 44.7bn), and the Follo Line tunnel, which includes four subprojects with a total value of EUR 950M (USD 1.06bn).
Thor Skjeggedal, general secretary at the Norwegian Tunnelling Society (NFF), also mentions other projects: “It has been just completed a joint rail and road project along the lake of Mjøsa. The new four-lane highway is long 17km and the double track railway line is about 15km. The total cost of this project was approximately EUR 1bn (USD 1.12bn).
“Another project to be completed is the Farriseidet – Porsgrunn double track railway line with seven tunnels of total lengths of 15km for a total investment of EUR 750M.
“The biggest on-going project is the 20km-long Follo Line tunnel. The assembly of four 9.96m-diameter double shield TBMs are continuing to excavate and the fi rst will start boring in September this year.
“Other on-going projects are the Ryfast road tunnel system near Stavanger with a total length of 52km for a total investment of EUR 1bn. This project is scheduled to be open for traffi c in 2019 and it will be the deepest subsea road tunnel ever built, reaching 292m below the sea level.
“Outside of Bergen the E16 highway is under rebuilding to include about 32km of new tunnels. There is also the upgrading of the Ulriken railway line with about 7.8km of new tunnel mostly excavated by an open TBM.”
Looking at the tunnelling statistics, Skjeggedal says, tunnels for highway have had the highest volume of excavated material in 2015 with 4,453,780 cbm. “In 2015 tunnel work for hydropower projects was the second largest end-use sector, but this trend is prone to change year by year,” he notes.
Eivind Grøv, a chief scientist at research organisation SINTEF and professor at the University of Science and Technology in Trondheim, adds: “The statistics show that in 2015 the tota construction volume in Norway was 7M cbm of solid rock. It was 6.5M in 2014, 6M in 2012 and 2013. It has been increasing gradually for almost 10 years, starting from 4M cbm in 2003.”
Skjeggedal also explains how the Norwegian tunnelling market is evolving with the arrival of foreign contractors. “Nowadays the major project owners go for bigger and bigger contracts. Earlier a contract of EUR 50 to 100M (USD 55.9 to 111.8M) was a big contract and they were always unit price contracts,” he says. “Now we see EPC contracts of up to nearly EUR 1bn and since the local contractors are relatively small, such big contracts are challenging and risky for them. The result is that many foreign contractors are coming into the Norwegian tunnelling market, pressing the margins and that makes the local contractors less competitive.”
The annual tunnelling statistics show the most active companies, indicating how much different contractors excavated over the last several years. In 2015 the main contractors were Skanska with 1,306,546 cbm, Implenia with 1,048,810 cbm, LNS with 975,132 cbm, AF with 686,255 cbm, NCC with 664,753 cbm, Kruse Smith with 536,940 cbm, Hæhre Entreprenør AS with 509,402 cbm, Marti Bau with 498,000 cbm, Ossa SA with 212,500 cbm and Veidekke 271,233 with cbm.
“Considering these statistics we can see a steady increase in excavated volume since 2001, with over 1M cbm up to 7M cbm in 2015,” Skjeggedal says.
“The Norwegian government is making a national transport plan showing how communication projects are planned over the next 10 years.”
Grøv adds: “In the short term there are a lot of tunnels projects coming up in the next years, particularly in connection with infrastructure projects and the hydropower sector, but it’s diffi cult to predict in the long term how will be the infrastructure development.” TBM’S RETURN
After almost 20 years of drill and blast, TBM technology is coming back to Norway. Skjeggedal explains, “up until the early '90s about 260km of tunnels were excavated by TBMs, mainly on hydropower projects. TBMs were not used due to a strong reduction in the construction of hydropower in Norway that lasted until 2014.
“The Røssåga hydropower project required the TBM method, excavating a 7.2km headrace tunnel by a 6.2m-diameter open machine. Now the Ulriken tunnel is under construction with TBMs and the next project will be the Follo Line. However, the majority of tunnelling is still done by the drill and blast method.”
Grøv adds: “The reason for the recent use of TBM technology in a few railway projects rather than drill and blast is to safely excavate parts of tunnels, side by side in populated areas with a lot of existing infrastructure assets and access constraints.”
COASTAL HIGHWAY ROUTE E39
The E39 project is part of the European trunk road system and the route runs along the western coast of Norway, from Kristiansand in the south to Trondheim in central Norway with a distance of almost 1,100km. There are seven ferry connections along the route, most of which are wide and deep fjord crossings that will require huge investments and longer spanning structures than previously installed in Norway. The current travel time of some 21-22 hours between Kristiansand and Trondheim is also influenced by the overall road standard of the route.
This project has been commissioned by the Norwegian Ministry of Transport and Communications and administered by the Norwegian Public Roads Administration (NPRA) to develop the route into a more efficient corridor with no ferry connections.
E39 project manager Kjersti Kvalheim Dunham explains, “the aim of the project is to have an efficient road on the west coast of Norway because we have almost 60 per cent of Norway’s traditional export from this part of the country.
“Today the road is very narrow and small and takes too much time to connect Kristiansand and Trondheim. We want to reduce the transport time up to 10.5 hours to have a good social and industrial impact on the country.”
Another objective is sustainability, and how bridge structures might be used for power generation from renewable sources such as solar energy, winds, waves and tidal currents.
Dunham says, “we started doing research and development for the coastal highway E39 program and 49 PhD students are currently working in different topics. They are also studying the environmental and the socio-economic impact of the road.” This project is exploring technical alternatives to mitigate the challenges represented by fjords.
The Sognefjord, which is about 3km wide, was used as a pilot site for developing new concepts for extreme bridges. With its vast depths of up to 1,300m and 200-300m of bottom deposits above the rock, the Sognefjord is considered one of the most difficult and challenging fjords to cross.
“We are evaluating three different bridge designs: a single span suspension bridge, a floating bridge and a submerged floating tunnel,” Dunham says.
A suspension bridge across the Sognefjord would have a main span of 3,700m and this is nearly three times the length of the Golden Gate Bridge in San Francisco and double the length of the current world record. The two bridge towers would reach a height of 450m, which is 150m taller than the Eiffel tower.
Another alternative is a floating bridge, in this case a “triple spanned suspension bridge”. Two of the bridge towers will stand on floating pontoons, which are anchored to the sea floor with anchors and mooring lines. Each tower will reach a height of 200m, while the pontoons are 75m in diameter and will stretch 180m down beneath the surface. This idea is taken from the offshore industry where large platforms are anchored in deep water in the same manner.
“The first study done on a submerged floating tube bridge for crossing the fjords in Norway is from the 1980s (Høgsfjord), but at that moment the technology wasn’t ready to be implemented,” says Arianna Minoretti, senior engineer for the E39 project.
The SFTB consists of two curved concrete tubes that are submerged in the fjord floating approximately 30m below the surface. This "tunnel" enters the bedrock beneath the surface on each side of the fjord and is anchored to floating pontoons on the surface. The tubes are approximately 4km long and are connected with trusses at regular intervals. Drivers would have the same experience driving in a submerged floating tunnel as in any other concrete tunnel. A submerged floating tunnel needs strict safety requirements similar to those that apply in ordinary tunnels. Escape routes are available through the trusses between the tubes.
“The SFTB is under evaluation for the Bjørnafjord, either with floating pontoons or tethers connecting the structure with the seabed, but we are also considering a floating bridge and a multispan suspension bridge with towers on tension-legged platforms,” Minoretti says.
Dunham adds, “we will talk about all the technical solutions at our own conference in Trondheim on 20 September (Teknologidagene), and also at the IABSE- conference in Stockholm on 22 September.”
E39 ROGFAST
The E39 Rogfast is a possible crossing of Boknafjorden and Kvitsøyfjorden, north of Stavanger in the southwestern part of Norway with a sub-sea road-tunnel. The name Rogfast is an abbreviation for the Norwegian name “Rogaland fastforbindelse”, translated in English as the “Rogaland fixed link”. The construction will most likely start in 2017 and the budget cost is EUR 1.5bn (USD 1.68bn).
The tunnel will be approximately 27km long, expected to start in Harestad and end at Arsvågen in Bokn. The tunnel's length will be approximately 25.5km. In addition to the main tunnel there will be an arm up to Kvitsøy with a length of roughly 4km. The E39 Rogfast will be the world’s longest and deepest subsea roadtunnel. Project estimates call for two, 27km reaches the depth of nearly 400m below the sea level.
E39 from Stavanger and further north is the main trunk way in the western part of Norway. E39 Rogfast will be a fast and ferry-less connection between the two cities Stavanger and Haugesund, and it will also shorten the travel time between Stavanger and Bergen.
Dunham says, “most probably this project will be excavated by drill and blast and it will be lined with concrete panel, which is quite common in Norway. She explains the project is focusing on environmental goals as well, such making the Rogfast project carbon neutral, and even an energy producer, which could supply lighting and ventilation in the tunnel. “We aim to make different parts of E39 a Power Road, which can produce more energy than it uses," she says.
According to NGU’s report (NGU: Rogfast – Norges geologiske undersøkelse, October 2014) the Rogfast tunnel goes through an area of complicated geology in the form of several thrust nappes and faults, where many types of rock are represented. Four thrust nappes, consisting mainly of granitic and dioritic gneisses, have been defined over the bedrock.
The tunnel is expected to go through phyllite and mica schist for the first approximately 6.3km from Randaberg, until it meets an expected fault zone in this area. Depending on the vertical throw of the fault, the tunnel is then expected to enter the Karmøy Ophiolite, which has gabbroic gneisses, hypabyssal rock types, volcanic rock types and sediments, as well as ultramafic rock types (dark and quartz-free). If the vertical throw is greater, the tunnel may enter the Storheia Nappe, which is composed of granitic and dioritic gneisses and lies under the Karmøy Ophiolite, or go right down to the phyllite.
Project manager at the NPRA, Tor Geir Espedal, says that a study has been conducted to address the potential for water leakage in the tunnel, based on experience from tunnels in the same area. There is experience of little leakage in phyllite and mica gneiss, while there has been moderate leakage in the other rock types, depending on the stresses and joint directions. The same study showed there is little need for injection throughout 66 per cent of the tunnel length and little to moderate need for injection over a further 27 per cent of the tunnel length.
FOLLO LINE PROJECT
As part of the largest transport project in Norway, the Follo Line consists of a 22km new double track railway line between Oslo central station and the new station at Ski, a small city south of Oslo. The Acciona Ghella joint venture will build the main part of the 20km-long tunnel, which will be Norway’s longest railway tunnel to date and the longest rail tunnel in the Nordic countries.
The Follo Line will be the core part of InterCity development in the south of Oslo and is commissioned by the Norwegian National Railway Administration (Jernbaneverket).
The project includes five EPC-contracts and the total cost is NOK 25bn (USD 3.03bn), financed by the Norwegian government.
The project includes the necessary realignment of tracks for the existing Østfold Line on the approach to Oslo Central station and between the tunnel and the new Ski station.
“It is important to avoid conflicts with other tracks going in or out of this busy station or with relics from the Middle Age located in that area,” says Anne Katherine Kalager project manager Tunnel TBM. The Follo Line is also designed for speeds up to 250kph to enable a 50 per cent reduction in journey time between Oslo and Ski.
With regard to the geology, the rocks consist predominantly of Precambrian gneisses with banding and lenses of amphibolites and pegmatite. There are also several generations of intrusions, which can be found over distances of up to 15km alongside the Follo Line tunnel. Sedimentary shale occurs in the northern part of the tunnel close to Oslo Central station. Weaker layers of the gneiss have been more exposed to erosion, which has resulted in long, prominent ridges and valleys. Kalager explains, “The rock mass is usually homogenous, showing good quality with moderate jointing as well. Laboratory tests illustrate that it is abrasive and strong. “Many people will define the rock as extreme hard rock compared to what is defined as hard rock many other places in the world.
“Some groups of weakness zones intersect the tunnel alignment. The thicknesses of these zones are normally between 1 and 5m, rarely above 10m."
During several glacial periods these weakness zones have been exposed to erosion and have developed to be valleys on the rock surface. These valleys are filled with thick layers of marine sediments, mostly clay or silty clay.
Leaking into the tunnel through these weakness zones will eventually result in lowering of the pore pressure in the sediments above the tunnel. If the pore pressure is lowered in these sediments, it will cause settlements on buildings founded directly on the sediments above the tunnel. Kalager says, “one of the success criteria for the excavation of the tunnel on the Follo Line tunnel is to avoid leaking into the tunnel and development of settlements on buildings close to the tunnel.
“In order to prevent such problems, grouting will be mandatory from the TBMs in these areas,” she adds. “At the early stages of the project, a huge monitoring system was established to register normal differences of the pore pressure throughout the year. All the buildings within a defined influence area have been and will be registered.
“Settlement bolts are installed at each corner of all the buildings and the buildings will be monitored before and during the construction period. The whole monitoring will give an early warning in case of water leaking, reduction of the pore pressure and development of settlements during the construction of the tunnel. Necessary mitigations, as pre-excavation grouting or infiltration of water may be implemented to prevent damages on buildings.”
Kalager also describes how the tunnel will be excavated and lined. In the northern part of the tunnel section, both the Follo Line and the relocated Østfold Line are located quite close to the other existing tunnels, caverns and different kinds of sensitive installations.
“The excavation of the Follo Line tubes and the inbound Østfold Line tunnel has to be done really careful in some areas,” she says. “The tunnels are crossing right under one of the main road tunnels. The distance between the top of the future railway tunnels and the bottom of the existing road tunnels is in one area at 3.5m. A river tunnel is currently located in the “spare area” between these tunnels, so this (river tunnel) has to be relocated and filled with concrete before the excavation of the railway tunnels can start in this area.”
Kalager says: “In this northern part of the tunnel both the relocated inbound Østfold Line tunnel and the two new Follo Line tubes will also pass close to caverns and installations for storage and distribution of oil and petrol.
“There are strong requirements regarding the limits of vibrations for passing the main road tunnels as well as the caverns and installations for oil and petrol.
“Due to limited space for start-up of a TBM in this area, it was decided that the tunnel for the inbound Østfold Line should be excavated partly by very careful drill and blast methodology and by the use of a drill and split methodology.”
Kalager explains, “TBM excavation for the two Follo Line tubes in this complex area could have been chosen as a part of using TBMs for the excavation of the rest of the tunnel, but this would have been the last part of a total TBM excavation length of more than 9km for each of the tubes and on critical path for the project. For this reason it was decided to start the excavation of all the three tunnels within this complex 1.5km-long section, early as a separate contract and to do the excavation by a combination of drill and blast and drill and blast methodology."
As the tunnel needs to be excavated within three years, it was decided to excavate the remaining 18.5km-long tunnel section with four TBMs operating from one central access point. Drill and blast excavation was also considered, but this would have required the excavation of seven access tunnels, many of them in densely populated areas.
Two machines will start operating north toward Oslo Central station and two others will be working south, headed toward Ski. These machines will be connected to a future cut-and-cover section south of the rock tunnel.
Designed for extreme hard rock conditions, these double shield machines have a diameter of 9.96m.
Two 1km-long access tunnels have been excavated from the main rig area and down to the location for the future railway tunnels.
Additional tunnels and two large assembly chambers have been constructed using conventional drill and blast techniques.
“The cross passages between the two tubes, a total number of 44, will be also by drill and blast,” Kalager says. “Precast watertight concrete elements will be installed in a closed ring to ensure rock support in addition to the prevention of water leaking into the tunnel.
“ The production of these elements, roughly 141,000 segments, takes place in the main rig area at Åsland. Approximately 10 per cent of the TBM spoil will be used in the production of the concrete elements.”
An EPC contract for the engineering, procurement and construction of the 18.5km-long TBM excavated tunnel section was awarded in March 2015.
The start-up of the four machines will take place during the period between September and December, and excavation should finish before the end of 2018, while the entire Follo Line is scheduled for completion in December 2021.
THE NEW ULRIKEN TUNNEL
“The section between Arna and Bergen is heavily trafficked. The current single track has insufficient capacity, and track doubling of this section will improve the situation for goods and passenger services,” says Hans-Egil Larsen, head project manager. “The biggest part of the section passes through a tunnel under Mount Ulriken. Jernbaneverket is now constructing a new, parallel tunnel in order to increase capacity.
“The double track will also permit faster speeds and improve traffic management flexibility.”
Starting from the Arna side of Ulriken, the tunnel construction is excavated using both conventional blasting and a TBM. This is the first time a TBM is being used for a railway tunnel in Norway.
The first 765m of the 7.8kmlong tunnel have been blasted in the conventional manner to be wide enough to accommodate extra passing tracks. That means, the cross section needs to be significantly large from 144 to 300 sqm, while it is 68 sqm in the rest of the tunnel.
Two diagonal tunnels have been blasted between the old and new tunnel, allowing trains to cross between tunnels. Another 16 smaller cross-passages will also be blasted between the tunnels for evacuation routes and technical installations. The remaining 7km of the new tunnel will be excavated by TBM. “There are many benefits to using a TBM rather than blasting,” says Larsen.
“By using this technology the project’s progress can be much faster, averaging an estimated 15m per day. We can also obtain an accurate excavation profile, reducing overbreak to a minimum. We can ensure less damage to surrounding rock, reducing the need for rock support. What’s more, bored tunnels generally have a longer lifespan than blasted tunnels.”
This type of machine is well suited because the rock in Ulriken is mostly hard and stable. As a consequence of this, it is not necessary to stabilise the rock prior to boring, merely to stabilise with bolts, steel arches and sprayed concrete as the tunnel progresses.
The TBM is 155m-long with a total weight of 1.8t and a 9.33m diameter. Larsen explains that the biggest challenge in the project is building close to the existing track where 120 passengers and freight trains pass every day. “Sometimes we need to stop the traffic to get the work done,” he adds.
For this project the contractor is JV Skanska Strabag, which started working in August 2014, while Norsk Jernbanedrift started operating for preparatory railway’s work in March. There will be a tender conference in October for the contract, which includes the Arna station and other technical works.