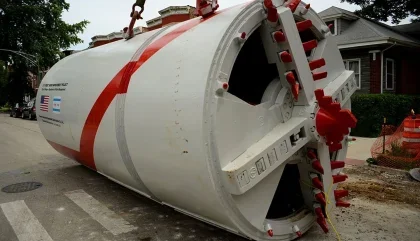
Since disc cutters, and their precursors, are now mature technologies there may be a tendency to consider TBM cutters as generic commodities with a drift to purchase decisions based on price. However, this attitude ignores the cost consequences of unplanned cutter changes and any related face interventions, whether due to cutter unreliability or unexpected ground conditions. The way cutters are employed also directly impacts on tunnelling machine productivity.
Herrenknecht emphasises its experience in the integration of cutters into the whole tunnelling machine system, viewing cutters as part of the whole cutterhead design, including the importance of changing procedures for optimum efficiency.
From the 1980s disc cutters with a V-shape profile were replaced by designs with constant cross-section (CCS) profiles so that a constant cutting edge would be retained longer. This allows cutter maintenance to be more predictable with a less sudden drop-off in performance.
Materials
The main focus of recent rock cutter research and development has been on metallurgy including steel treatment and alloy compositions. TBM cutters not only have to carry out their main tasks of cutting or crushing materials encountered up to 400MPa, and moving them around to removal apertures, they also have to withstand environmental extremes including ground temperatures of up to 50 °C, high groundwater pressures and also intrusive dust.
Sandvik is reportedly investigating the increased of use (up to 80 per cent) of industrial diamonds in cutting edges. This is in addition to the established use of industrial diamonds in core drilling bits to produce clean cuts with as little disturbance of the core as possible.
It is possible to design cutters in materials capable of tackling all types of ground but they would be prohibitively expensive for normal construction. However an attempt to slash costs by buying the cheapest cutters that will fit is unlikely to save money over the whole tunnel project due to early failures and especially the costs involved in unplanned interventions for cutter changes in terms of both extra labour costs and project delays.
The replacement of roadheader picks is much more related to the unit costs since the relatively easy access to the cutterhead in free air makes the indirect cost of replacement labour and downtime proportionally much less. Even so, an incorrect choice of pick types or cutterhead geometry can be very expensive, especially in hard ground. Roadheaders have the advantage of being able to work around hard inclusions, but the solid rock capability is much less than that of hard rock TBMs or drill and blast.
Caterpillar Tunnelling attributes its improved current disc cutters to the use of Caterpillar Tough Steel, which had been developed for and used for years on Caterpillar earthmover plant components such as crawler undercarriage track links and sprockets, achieving hardness and resistance without being brittle. However, according to parts sales and marketing manager, Nick Natale, the Company is also working on new (patents pending) cutter designs to be released in 2013.
For where an ‘impact hammer’ rather than ‘cutting’ action is required for hard rock inclusions, Caterpillar offers its ‘super ripper’ tools with carbide inserts. These have been employed successfully on Beijing Metro tunnelling by the BUCG (Beijing Urban Construction Group) – where the Chinese termed it ‘Diamond’ due to its success, says Natale, and on an EPBM for the Brightwater project (BT3C) in the US. For the latter contract Lovat (now Caterpillar Tunneling Canada) upgraded the existing TBM from contract BT-4, including suitability for an increased hydrostatic head of 7.3bar expected in the complex glacial, boulder-laden ground.
Although this type of cutter design was originally intended for soft ground it has been found that, with the right materials, it also works well in mixed ground. In Beijing the EPBM encountered beds of boulders including some up to 1.2 by 1.5m across, but these were smashed by the super ripper tools in two parallel drives. Approximately four boulders of >800mm diameter were encountered with each ring advance. Echoing Brightwater, the matrix is highly permeable with abrasive cobbles and gravels. Shang Xiaomin, BUCG chief project manager for the Spacing-S Current cut Chip formation Previous cut P1 S/P=10-20 Beijing Metro Line Nine says, "Among all the metro tunnels we have built throughout China, Beijing Metro Line Nine Lot Six is undoubtedly the most difficult." Due to the presence of much water, protected areas, and military compounds on the surface there was little or no chance of intervention from the surface if everything were to go wrong such as the TBM becoming stuck due to premature cutter wear.
Robbins president Lok Home says that the company has been working with the University of Trondheim (NTNU) and the Norwegian government on a programme and laboratory and field tests of improved cutter materials. The company’s cutter department manager, Steve Smading, says it is premature to report on new cutter materials although research is ongoing.
Layout
Successful penetration of the TBM cutterhead has a lot to do with the overall design and geometry of the cutterhead layout as well as the cutters themselves. For example, there has to be a balance between enough area of openings to allow the removal of dense, sticky ground such as clay as well as any unbroken boulders, and the necessary support structure for cutters and to transmit thrust and support to the face.
In general larger disc cutters are better at penetration but also in maintaining rotary action due to their slower speed. The increased amount of material also tends to permit longer drives between cutter changes. Since their introduction, disc cutters have tended to increase in diameter commensurate with the diameter of the whole cutterhead. Now the largest cutters used tend to be of 17 or 19in diameter, although models up to 20in are available.
Robbins employed 20in cutters for two 10m-diameter, double-shield, hard-rock TBMs for a 43.5km tunnel for the AMR project from the Srisailam Reservoir to the Nalgonda District of Andhra Pradesh. The aim was achieve longer cutter life as excavation included quartzite of up to 450MPa UCS, shales, and granite of 160 to 180MPa.
There are some general principles on size that can be followed. Robbins’ Steve Smading comments that the company likes to standardise on cutter sizes for simplicity of operation and economies of scale. However, "for hard rock, the bigger the better." he says, "in softer ground smaller cutters improve the muck flow through the larger cutterhead openings."
For the same rock conditions and TBM thrust, larger diameter cutters reduce penetration as the larger ‘footprint’ reduces face pressure. On the other hand, the larger bearing capacity made possible by the overall cutter design allows greater thrust transmission and therefore higher performance. Other advantages are less heat build-up due to a slower rotation speed, and more material to wear out between necessary cutter changes.
Robbins is reported to be working on completely different approaches to the problems of excavation soft ground in a mixed face, with field trials imminent.
Several manufacturers have trialled the alternative approach of undercutting rock with special disc cutters, but probably none have advanced the technology as far as hard-rock TBM specialist Aker Wirth. This was used in the reaming TBM used for the Uetliberg Tunnel. The undercutting tools as used at Uetliberg were slightly pitched to the rock face (at 10°) rather than the normal perpendicular. This alignment ‘chips off’ relatively large pieces of rock rather than just crushing the rock on the disc edge, and also acts as a wedge, reducing the overall forces required. According to Aker Wirth, the energy required to break the rock is only about half of that required for conventional tunnelling.
In order to cut rock continuously the TBM cutters have to be constantly moved radially as the cutterhead rotates, placing additional demands on the control system. The disc cutters in the Uetliberg machine were mounted on moveable slide assemblies moving outwards with each new 200mmlong impact cut. After each cut the cutter is retracted to its original position. Other, claimed advantages for Aker Wirth undercutting include fewer cutters (and therefore lower costs), any cross-section can be created, and that spoil is available for recycling if required.
Small-bore and microtunnelling cutterheads cannot, of course, accommodate the larger cutters and, as with larger bore machines, there needs to be a delicate balance of transmitting the necessary forces to the face whilst leaving space for spoil removal. Early hard-rock designs employed roller cutters with rows of carbide button inserts, but arrangements of disc cutters are now successfully employed by Robbins on its SBUs and by independent supplier Palmieri.
The latter’s includes double- and triple-disc tools on one roller, with or without hardfacing.
With raisebore heads there is usually more opportunity for the spoil to fall away freely, and for the replacement of any failed cutters, as with drilling bits. In this case the use of roller cutters with tungsten carbide inserts is more common.
Compensation
With the increased demand for deeper tunnels, there is the increased need for resistance to increased groundwater pressures. Traditional designs of TBM cutters are susceptible to contamination, including clogging, of the bearing run due to any significant difference in pressure between that on the face and the interior of the bearing. Not only can this result in premature bearing wear but also prevent smooth rotary movement and cause possible flat spots on the cutter. All this can result in early cutter failure and consequent poor operation or failure of the whole cutterhead. The only remedy is time-consuming and expensive intervention to the cutterhead and face, probably under compressed air or by divers before the next opportunity for ‘free air’ maintenance.
Various designs have been developed by manufacturers to compensate for the difference in pressure and so minimise contamination. Good seals can usually deal with a small pressure differential of three bar and are therefore suitable for many EPBMs working at moderate depths. However, there are now frequent demands for TBM projects at greater groundwater pressures.
Herrenknecht says that there are now requirements for tools that can work in ambient pressures of up to 20bar. At pressures above 4bar, some means of compensating for such a large pressure differential is necessary. A Herrenknecht solution is the use of a membrane that allows for the transfer of pressure from the ambient to the lubricating oil in the bearing chamber.
Other developers of pressure compensation designs include Robbins, which is working on a wide programme of cutter improvements for EPB tunnelling in soft and mixed ground, including work under high pressures, currently up to 10bar. The company’s Zachary Box, published the current state of development in pressure-compensated cutters in a recent paper. Early attempts to tackle the problem involved pressurising the inside of the cutter bearing cavity up to three bar so that the seals can work at up to 6bar, although this still limits the use of the cutters. Excess external pressure forces seals together and cause more friction, and therefore wear or seizure.
A testing module at the Robbins Kent facility simulates a pressurised operational environment so that the performance of seals can be assessed. Currently the basic design has reached its fourth generation, with more planned.
Steve Smading says, "Most TBM disc cutters to date have been designed for generally hard rock, but ‘soft-ground’ problems are totally different. One is to try and get the cutter to keep rolling, for which different bearings and seals have been trialled. Robbins has developed a patented design for compensation differential pressure in order to protect the cutter bearing. This is destined for the Robbins hybrid EPBM being used on India’s Sleemanabad water tunnel project. Here boulders are present in the top of the tunnel resulting from decomposed granite. The rest is mainly sand [and a little] clay." According to Box, there is no clear leader in pressure-compensated cutter design at present. "Only after further development of the plumbing design and then further field tests of all designs can we find a definitive direction to move forwards with."
Mixed
One of the major problems facing TBM contractors is mixed ground, especially when there is a wide range of material hardnesses in the face. Varied hardnesses of stratified rocks can be problematical but perhaps the worst is a soft matrix holding hard boulders such as boulder clay or decomposed igneous rock. The latter has caused several delays in Asian tunnelling projects, as much caused by excessive abrasion due to residual minerals (mainly quartz), as due to shock loading from the hard inclusions. In some cases, the cutters, depending on thrust, can bury themselves in the soft parts of the face making it more difficult to remove or cut boulders.
The basic conflict in cutterhead design is that there needs to be a sufficient support area, necessarily closed in, to carry the cutting tools and transit thrust, but on the other hand, there needs to be as much open face area as possible to allow passage of spoil, including soft, sticky material, with clogging.
A few years ago Herrenknecht developed a narrow single-disc cutter that allows for a spacing of 80mm even if the cutters are arranged next to each other.
The cutters can therefore be arranged in rows on ‘arms’ with comparatively large spoil removal apertures between the arms.
Bob Moncrieff, independent tunnelling consultant of Rona Consulting, based in Bangkok, says, "It is difficult to design a cutter for ground with some boulders in it. In some Asian projects the tropically weathered ground, such as granite, leaves quartz intact where the rest of the material has decomposed.
"As a result the cutters become quickly worn by the abrasive quartz, making them thinner and more fragile. If a harder lump is then encountered they can easily break."
"Thicker cutter discs have drawbacks too," says Moncrieff. "The thicker disc may resist wear better, but will not be so effective in its ability to cut rock in the first place."
Abrasion studies
The nature of abrasive wear on cutters is not as simple as may first be thought, and is proving a fruitful area for study at various academic and other research establishments including the Norwegian SINTEF and NTNU in Trondheim, and The Pennsylvania State University and Colorado School of Mines in the US. Factors such as moisture content and EPBM soil conditioning agents can have a substantial influence.
Various studies have already shown that the presence of water in the soil being excavated can increase soil abrasivity, and higher pressure water also increases wear slightly.
Perhaps more intuitive is the confirmation by Gharahbagh and Rostami (Pennsylvania State University) that compacted soil shows a notable increase in tool wear. The Pennsylvania State work is continuing both in the laboratory and from field studies to collect data on different soft ground types, moisture content, hardness and dynamic conditions.
Picks, rippers and scrapers
The advanced Caterpillar ‘super ripper’ tools are just the latest in a long history of fixed cutters that still have valuable contributions to make on TBM cutterheads in soft or mixed ground conditions. With most EPBMs, ripper tools are the most commonly used, with designs such as scrapers for softer, probably clayey, ground.
These have carbide inserts at strategic points located on the tool according to the expected ground conditions, orientation on the cutterhead, and direction of movement.
In the case of variable ground conditions within a drive, adaptor housings are available so that rippers can be interchanged with disc cutters. Changes are possible within the safety of the cuttinghead chamber rather than at the face.
In addition, point attack picks are used in rock cutting methods such as roadheaders. As with TBMs the relative location of these picks, whether transverse or axial, is important to their operational efficiency so that the picks can work together rather than having them attempting to remove rock by individual blows.
Databases
It is clear that the knowledge of which cutting tools work best, and which do not, under certain sets of conditions, can be very valuable.
In conjunction to current research into such issues as abrasion, field tests are often carried out to test or demonstrate hypotheses, but the data collected is relatively small compared to the vast amount of data that could be available from all tunnelling projects. Some leading tunnelling institutions and manufacturers have made efforts to assemble and codify their available data.
Herrenknecht’s Cutter Database has frequently been used by customers, says the manufacturer. It is based on the experience of wear and cutter exchange strategies that are gained from a number of projects.
It allows users to develop economic project strategies for cutter disc exchange and refurbishment, and includes the time, place and reason for each exchange.
So this provides a complete history of each cutter including the relevant costs, allowing forecast to be made for use on future projects.
To facilitate wide use, the database is available in four languages, and gathered data can be transferred to cutter refurbishment shops.
Monitoring
Various methods have been used to find out what is going on with the cutting tools at the face. Even experienced operators will know of problems whether from machine operation or an acoustic link.
However, there has been a trend to more scientific and quantified monitoring to allow better prediction of when tools will need changing in future under certain sets of ground conditions. A more immediate effect on TBM efficiency is reduced interventions, whether free-air or hyperbaric, to check on the cutters.
In the BT-3C Brightwater drive the Caterpillar EPBM was fitted with a CCTV camera and feed frame to allow visual inspections of the tools in situ.
Instrumentation of TBM knife and drag bit tools, such as by wear detectors and pressure pipes in strategic positions, should give early warning of any excess wear so that replacements can be better planned.
Robbins’ Shane Draney also lists the following precautions to protect EPBM cutterheads:
- Inspection and replacement of the primary cutting tools at the recommended intervals,
- Wear detectors and wear pipes should be required on all EPBM cutterheads where interventions would be difficult and drives long,
- When selecting wear plate for cutterheads it will be worth the added cost for high grade wear plates when tough ground conditions or long drives are required.
It is very important that recommendations of additive suppliers are followed, including the proper number and size of injection ports