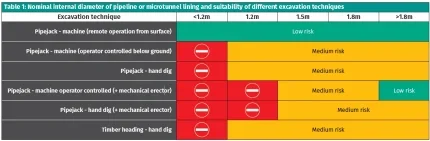
The Pipe Jacking Association (PJA) recently released an update to its guidance documents to the trenchless tunnelling industry – issuing ‘Pipejacking design guidance for CDM Duty Holders’ to replace ‘Tunnelling & pipejacking guidance for designers’.
PJA chairman, Sean Martin, said: “The original guidance was published a number of years ago and has been a key source document to the trenchless industry – predominantly in the UK, but also as a reference document across the world.
“The latest version,” he adds, “reflects changes in UK regulation and equipment capabilities.”
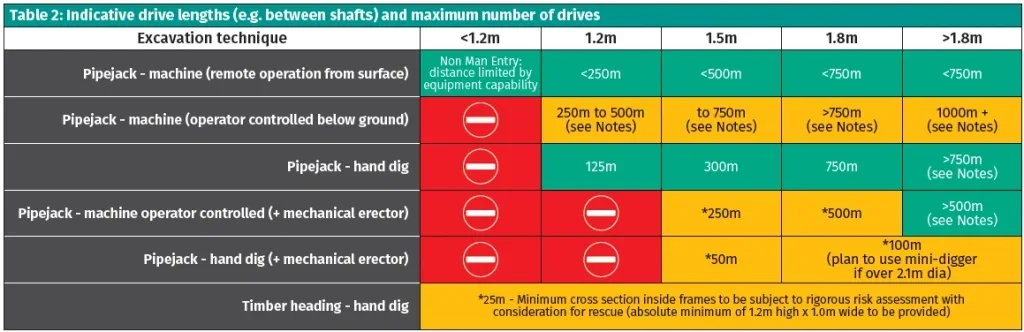
The update also supports the PJA’s “dedication to providing best practice guidance for the cost effective and environmentally sensitive installation of underground utility services.”
UPDATED GUIDANCE
The updated document is issued as guidance for CDM Duty Holders, coming from best practice consensus agreed between the PJA and the British Tunnelling Society (BTS). The guidance needs to be read in conjunction with BS6164 Health & Safety in Tunnelling in the Construction Industry – and should, they emphasise, only be used by those “competent to plan, design and construct pipejacks and microtunnels.”
It is based on experience of the occupational health and safety risks arising from heavy physical activity and handling, including when using vibrating tools; working in confined space; the need to quickly and effectively evacuate or effect rescue in “a range of reasonably foreseeable situations.”
Further duty to consider risks from foreseeable hazards of pipejacking and tunnelling can also include: atmosphere; heat & fire; ground conditions; ground gases, water & contamination; and, ventilation.
The guidance adds that satisfying these requirements may call for a minimum internal diameter of a tunnel to be larger than needed to meet hydraulic or other usage requirement of the pipejack/tunnel.
Being guidance, the updated document does not relieve any CDM Duty Holder of their legal responsibilities.
The guidance can be varied, they add, such as when it might be judged appropriate “where improvements in technology and working practices occur, or through the adoption of measures to mitigate risk.”
TABLES
The document issued includes two tables, as shown, each concerning the internal dimensions and indicative drive lengths for pipejacks and microtunnels.
While noting that pipejacks and microtunnels are now routinely installed at up to 3.4m internal diameter (i.d.), the tables focus on three colour-coded risk levels (low, medium, and ‘not acceptable’) across five bands of diameter: less than 1.2m; 1.2m; 1.5m; 1.8m; and, more than 1.8m.
The first of the tables (Table 1) concerns internal diameter with respect to six excavation methods, and classifies them – per the diameter bands noted above – according to the three colour-coded risk levels.
Only the excavation method of pipejack by machine and being remotely-operated from the ground surface is classed as lowest risk (green) for all the bands of diameter in Table 1. The only other low risk (green) class is for pipejack that is machine operator controlled with use of a mechanical erector.
Low risk (green), in the guidance, is discussed as: designers and contractors should undertake a robust assessment of the risks associated with the pipejacking and tunnelling, in addition to site specific risks and specify the appropriate mitigation measures.
In discussing medium risk (amber/orange), the guidance must justify decisions to deviate from low risk criteria. On the ‘not acceptable’ risk category, the guidance discusses such in relation to methods requiring routing personnel access and diameter is below 1.2m, although some excavation categories include 1.2m.
All hand digging is categorised as either ‘not acceptable’ or medium risk, depending on diameter.
Table 2 provides colour-coded risk guidance for indicative drive lengths (between shafts) and also maximum number of drives. The data in the table matrix are by excavation method and diameter, respectively.
In its Notes, the guidance says the indicative drive lengths, as given in the table, include consideration of access and escape requirements; that drive lengths longer than indicated in the table, and where excavation method/diameter entries show an asterix (*), there are limits to exceeding the length, and such need to be risk assessed and implementation of adequate control and mitigation measures. Doing more than 25%-75% longer drive needs checked and approved by the principal designer; it is considered “not acceptable” to exceed the indicative drive length by more than 75%
Also in discussing drive lengths, the Notes discuss the need for frequent access for managing multiple interjacks and what is then categorised as generally ‘not acceptable’ arrangements – such as where there isn’t an automatic lubrication system and/or where retooling will be required. An exception is where the pipejack/ tunnel can incorporate risk mitigation and/or has large enough cross section for an ‘access envelope’ that meets the guidance. The ‘access envelope’ does not include ventilation ducts, spoil handling systems and ancillaries.
Further, the guidance Notes say that where small diameter machines are able to have tool replacement performed underground the first choice/least risk option should be to use intermediate shafts. They add that, where possible. Drive lengths should avoid in-tunnel tool changes.