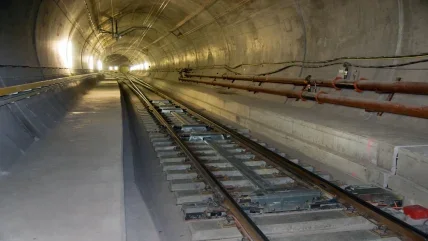
Tunnels are large components of heavy civil engineering infrastructure that bring major societal gain. Like other sectors, the industry’s products have notable carbon footprints now being called upon to shrink due to rising climate concerns. Efforts to pursue carbon reduction fit within ‘sustainability’.
Creating engineered projects needs practical interpretation of principles, in this case of sustainability. To achieve reductions in carbon content would call for compatible choices that are specific and detailed, and measurable. More measurement means increased data, possibly transparency, all to further concentrate minds on alternate technical choices to realise a project.
Presently in tunnelling, prime points of focus for carbon reduction are construction materials, such as mass or reinforced/sprayed concrete, and transport, such as extensive haulage of those products and many more to and from project sites. A further, and growing, part of the project development challenge is to look more to early choices in design and even prior, highlighted Ross Dimmock, vice president for tunnelling at Normet, in a recent talk to the British Tunnelling Society.
Choices already being explored, in materials and projects, include: researching blends of cementitious mixes to reduce the carbon content in sprayed concrete linings (SCL); adding carbon footprint calculations to the procurement competition for the Brussels metro expansion; and plans to reuse tunnel spoil from CERN’s next major underground particle physics project in the Alps. There is also the legacy of sustainability to call upon from past choices, such as those made during construction of the Gotthard Base Tunnel.
With more awareness, discussion and understanding needed around the subject, Day 1 of a training session at the forthcoming ITA World Tunnel Congress in Copenhagen (2-8 September) will focus on sustainability. It will be led by Alun Thomas, of All2Plan Consulting and a leader in SCL, and will include speakers from all parts of the tunnelling industry. He is author of Sprayed Concrete Lined Tunnels (2nd ed).
“There is huge potential to improve the sustainability of tunnelling,” Thomas tells T&T, adding that client leadership is the key – “they must reward green designs and open their projects to innovation.”
WEIGHING CARBON IN SPRAYED CONCRETE
UK experience with SCL “sets us on a good footing” for a low-carbon future, Dimmock recently told the BTS meeting in January. Presenting his thoughts on SCL developments, he took ‘big picture’ international objectives and policies on climate change as context for a practical focus on steps toward a low-carbon approach to tunnelling.
Dimmock pointed to ‘PAS 2080:2016 Carbon Management in Infrastructure’ to provide guidance on upfront choices for possible projects – including whether to build at all, or look to upgrade or extend the life of existing assets before pursuing the new build option. At least, not to automatically assume new build is the route to follow.
As always with projects, observed Dimmock, early decisions make the key differences and in tunnels it is at the design stage where big savings on carbon can be made. Such benefits could be gained, vitally, through client leadership. Gains would be then delivered by incentivising main contractors during procurement as part of engaging the whole supply chain to pursue carbon reduction through both contractual relationships and technical performance.
“Trying to make carbon savings during construction is really about just driving efficiencies,” said Dimmock. But there too, he added, there is much that can be achieved, and progress has been made with SCL in tunnels in recent years.
Dimmock recapped the early use of sprayed concrete, recalling that back during construction of the Channel Tunnel, the strengths achieved were not often more than 18MPa at 28 days, and the works were performed in highly challenging conditions. Today, he observed, that the level of strength gain is achieved in a little under half a day from placing sprayed concrete on tunnel walls. “Things have really changed,” he said.
By the 1990s in the UK, on the Jubilee Line Extension, Heathrow Express and Channel Tunnel Rail Link projects, the wet mix SCL had less dust and less rebound, though the primary lining was placed with a temporary purpose and secondary SCL continued to be needed. Robotic spraying then came along.
Hindhead road tunnel saw permanent primary lining and many technologies established themselves, including sprayed waterproof membranes, less use of mesh and lattice girder support, and improvements in achieving smoothly accurate SCL profiles. In London, the tunnel works on Crossrail and Bank Station projects then benefited from all the progress, enabling permanent SCL (PSCL) linings to be constructed – permanent primary and secondary layers with, in between, a thin regulating layer plus a sprayed waterproof membrane.
Much improvement in SCL has been achieved over the past almost 40 years but, he said, one box has yet to be ticked – decarbonisation.
Dimmock said that systems today offer possibilities to potentially achieve 35%-40% reduction in carbon from concrete, which, he believes, correlates well to estimates by Alun Thomas, in 2019, on what might be feasible for SCL tunnelling. The reduction possibility comes from across the spectrum of design, materials and equipment. “So we can do quite a lot,” said Dimmock. “We can take big steps.”
On equipment for SCL placement, he anticipates that benefits can be gained from training; from the use of battery electric-drive sprayers; from more automation for layer profiling; and from a greater application of computing technology for laser scanning, digitalisation and rapid data analyses.
On materials, he recently calculated that a CEM I (standard OPC-based) sprayed concrete mix design would have approximately 560kg of carbon (equivalent CO2) per cubic metre. But where OPC is blended with other cementitious products, to be classed as CEM II – III, for example, the carbon footprint can be much less. As an example, he says a design possibility for a non-tunnel civil excavation project showed that a blend of OPC with ground granulated blast furnace slag (GGBS), on a 75:25 split, and with polymer fibres, could reduce the carbon load by 40%-50%.
The challenge for taking up low-carbon cements in soft ground tunnelling, however, is the slower strength gain even though long-term performance is favourable. Early strength gain is vital for safety and building thick enough layers in SCL operations. He adds that interesting studies with geopolymers show mix designs could help achieve ultra-low carbon concrete while delivering rapid early strength gain, but that progress then tails off after a week, to almost plateau at lower than typically desired strengths (only around 15MPa). Options exist to improve strength, he adds.
A further spin-off benefit of closer monitoring of carbon would be more data available on the use of materials, which would help to focus on cost savings, suggests Dimmock.
THE PROBLEM OF GEOLOGY
Encountered geology naturally leads to variations in the excavated profile achieved versus the plan. When building up SCL layers, there can be an excess use of sprayed concrete, perhaps 50%-100% more than anticipated in the design profile, he said.
PSCL – and moving away from multiple layers when creating SCL tunnels – helps reduce the SCL’s overall thickness, not least because each layer comes with its own envelope of dimensional tolerance, safety and risk. Upon revisiting the original SCL layers design for Crossrail, a study by a consultant, suggests, said Dimmock, that today a thinner lining could be possible for such purposes, and a commensurate reduction in carbon content in tunnel lining. “I think it’s time to really look at full-scale trials with new technologies again”, added Dimmock.
While new underground projects will be needed in future, the opportunities with and needs of existing tunnels are many – perhaps more, in an era of climate concern, he observed. Last year’s extensive flooding in Europe and Asia affected much of the existing infrastructure, including tunnels, and points to the need for better protection of underground assets.
At the BTS meeting, Dimmock emphasised the importance of looking at such asset security: “It is one of those topics that we need to think about going forward.”
DECISION FOR BRUSSELS METRO
Development of the next phase of the underground metro in Brussels is paying marked attention to sustainability, T&T is told by Laurence Delplace, Amberg Engineering’s regional manager for France and Belgium, and responsible for managing the consultancy’s services to the project.
Brussels Metro North project will extend the subway network by 4.5km in a single tube tunnel from the centre to the northeast, replacing surface tram route No.3. The double-track underground link will run from Gare du Nord rail station out to Bordet station, via six intermediate new stations (Liedts, Colignon, Verboeckhoven, Riga, Tilleul and Paix). The metro project is being developed by Beliris, a joint city-federal transport agency, and will have the capacity to carry approximately 60,000 people at rush hour. The budget is approximately US$933m.
The 8.9m i.d. metro tunnel will be excavated through soft ground in the urban setting. Geology along the alignment is mostly sandy clay and clayey sand, the remainder (about 30%) is sand.
Minimising settlement for subsidence control is a high priority under dense infrastructure in the heart of the capital, but the project also seeks to actively and measurably meet a series of sustainability aims. On top of those requirements, the project will connect with existing rail and tram lines, and operate as an automated transport system.
Amberg has been performing a range of services to Beliris for the project’s tunnel – feasibility study, preliminary design, final design, preparing and helping the tender process for construction contracts, and works supervision. The project services also include overall fire protection studies.
Planning stages have been completed and construction is getting underway.
While the first works package is already in construction, taking the route below Gare du Nord railway links, the main works package has yet to reach procurement. The Covid pandemic and other delays hindered the project development schedule. The specification for the main works package is being written and the Request for Proposals (RFP) is due out in the third quarter (Q3) of this year, Delplace tells T&T:
“One of the decisive criteria for the selection of the contractor will be the CO2 Balance,” says Delplace.
She adds that CO2 Balances for materials and transport are to be calculated and form part of contractors’ bids. Subsequently, the winning contractor will have their CO2 Balance performance monitored subsequently on site.
“Instead of forcing the contractor to chose specific material or transport modes, a certain freedom is given,” says Delplace. “But the condition is clear – CO2 emissions need to be as small as possible.”
The focus on the carbon footprint of the production and use of materials, and methods of transport, are prime metrics for assessing tangible ways to pursue practical paths to achieve sustainability in tunnelling.
Imposition of the CO2 Balance criteria, she adds, will push contractors to find combinations of solutions and materials with lower CO2 emissions.
Delplace says: “Some options are, for example, the use of low-emission concrete, or the use of fibre-reinforced concrete (FRC),” rather than more standard mix designs. She adds that FRC solutions have been investigated for segmental tunnel lining in the industry, and are currently being implemented on the Grand Paris Express, a megaproject that will significantly expand the French capital’s metro network.
In looking at CO2 Balance from a transport perspective, consideration is given to how materials are brought to and taken away from tunnel jobsites. “The contractor will be able to choose between several options depending on the destination,” says Delplace.
When considering the relative CO2 Balance of alternative transport possibilities, different options, or modes, to weigh might include: using only road haulage; having all movement by rail; or using some river (fluvial) transport in combination with either road or rail, or both.
“Each mode will imply different CO2 emissions and also different prices,” says Delplace. “So, in the end, there is a clear equilibrium to find. We want the contractor to have full ownership of these impactful decisions.”
She continues: “That said, we obviously support fluvial transport,” which while she notes as being more costly, “will create less impact on traffic and be much lower in CO2 emissions.”
For the first construction lot, which is already underway, the contractor was required to use the canal. But the large volumes of excavated materials to be generated for the main lot, soon to go into procurement, makes it “more difficult to impose a unique mode of transport,” says Delplace. “A certain degree of freedom is given,” and to help reduce the impact on inner-city traffic in Brussels, a long-term mobility analysis is being undertaken, she adds.
But materials and transport are not the only areas of focus for pursuing sustainability on the Brussels metro project. Other points of focus include attention to the circular economy and geothermal aspects, respectively.
With reuse of materials and equipment as the main intent of the circular economy, Delplace tells T&T that there were discussions with start-up businesses in this area of recycling. They explored the use of some clayey soil for other purposes, such as making bricks to use cosmetically in stations, and also some excavated tunnel sand for concrete production.
On the geothermal focus, Delplace says that a pre-feasibility study looked at using underground heat related to the segmental tunnel lining and the diaphragm walls. She says such installations could provide energy for the depot and maintenance centre.
Following the RFP this autumn, construction of the main lot is anticipated will start in 2024. The various elements that make up the sustainability plan for the metro extension project are not necessarily something unique in themselves, explains Delplace, but the combination of all criteria and actions is showing potential promise for a green project. The client is definitely the driver in pursuing sustainability for the infrastructure project, she adds.
She observes that in many big European projects, there is a general trend toward an interest in sustainability, although not a lot is always done in reality. “In Brussels, there is a clear choice to do something about it with a real outcome.”
CONCLUSION
Data will be important to choices
“This is very much a data-driven process, in which information – for example, on the embodied carbon in different options – guides the choice of best solution,” Thomas tells T&T. “While some clients still focus on the short-term environmental impact of creating an asset, there is an increasing trend towards considering the whole lifecycle.”
Whichever, from the supply-side, the lowest technical carbon footprint of each physical element of a project may not, automatically, or indeed always, be the answer to a client’s elected approach to reducing the carbon content. The total they see could well be different to the sum of the parts, in terms of carbon content alone.
To help those calculations, for the design and construction stages of a project at least, industry should have technical alternatives at the ready. But, an added complication is that sustainability is at an early stage of development in the infrastructure sector. That has implications for what is on offer, and also for clients running cost-benefit calculations to choose how to take forward a project’s development.
Support for gearing up green change varies by country, government and clients. Their choices affect decisions all through the supply side, including investment, R&D and perceptions of risk. As ever, leadership will be key. For both public and private sector clients, there will be cost implications for either supporting, or otherwise, the development of sustainability in tunnels.
“Better procurement processes are needed, ones that reward green solutions instead of penalising them,” Thomas tells T&T. “A key element in this is good design and too often, good design is undervalued.”
The green road beckons for all in infrastructure but much is uncertain. What is certain is that while heavy civil engineering structures will always create big impressions upon the landscape, their carbon footsteps in future are to be small and light.