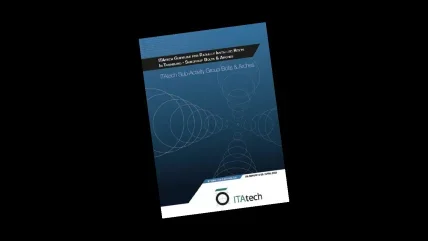
With its goal to provide guidance on selection criteria in design preparation to employ radially installed bolts as part of ground support in convention tunnelling, primarily, the 48-page report for ITAtech is packed with excellent information and covers much in a highly structured and well illustrated way (20 figures, 18 tables). Yet, without being overly compact, it feels a highly effective reference and working document.
The report – the ITAtech Guideline for Radially Installed Bolts in Tunnelling, with a focus on bolts and arches – provides chapters for Definitions and Abbreviations, respectively, as well as useful References among its total of 14 chapters.
Aside from the Introduction, those other chapters cover:
- Bolts as part of ground support
- Classification and selection criteria
- Common bolting systems
- Properties for technical specifications
- Installation
- Bonding agents and grouting
- Corrosion protection
- Quality management and assurance
- Innovation
- Sample clause for technical specification
As noted at the outset, among its objectives, the report says: “This information is intended to assist the designer as well as underground engineer to choose the technically most appropriate bolt type(s) for each expected ground condition and to set minimum requirements for chosen bolt types ensuring a high level of safety during construction.”
The report opens with descriptions of load bearing components and material of bolts, and then the primary focus of the guide is to discuss and guide on selection criteria. Corrosion protection – including the corrosion potential of the environment – are also discussed.
The needs of specification in tender documents for procurement stage of a tunnel project is also discussed.
There is a minimum specification recommended for each of the several components in a bolting system, so as to enable “unambiguous” tender documents, the report notes.
It also vitally provides guidance on installation steps and activation modes of the bolting systems, respectively, while also discussing the advantages, disadvantages and limitations of each bolt type. With quality assurances needs becoming ever more important on projects, the report also looks at system test, and monitoring both during manufacture and installation – and testing after the bolting systems are installed.
The report was issued in April 2023 by ITAtech, and comes as Report No29 in the sequence of ITA reports. Some brief notes follow on a few of the chapters in the highly usable guide.
Bolting in ground support
The report notes that ground support in conventional tunnelling generally comprises various combination of engineered elements to suit the local conditions of the geology and excavation – such as, commonly, bolts, steel arches, lattice girders, and sprayed concrete used with steel mesh or fibres.
With regard to bolts, the report lists and briefly describes their load bearing components, as follows:
- Tendon – the main load bearing element, transmitting tension along the bolt axis. These are typically solid or hollow bars, which can be of different cross sections, and surfaces (smooth, threaded, ribs), or have anchorage points. (Cable bolts are not discussed in the report as they are uncommon in tunnelling.)
- Coupling – these connect tendons to achieve required bolt length
- Bolt head – typically a plate and fastening element, together as an assembly (possibly also including washers), attached to near the end of the tendon. The plate has contact with the ground, shotcrete, etc, and the fastening element transfers load from the plate to the tendon
- Expansion shell – anchorage elements connected to the tendon, and expand typically via and leafand- wedge system. These can help bolts serve as mechanical bolts
- Spacers (centralisers) – for centralising the bolt in the borehole, these are of steel or plastic, and not fixed, to help ensure minimum and uniform surrounding encapsulation by cement or resin grout
- Conical bottom cap – helps insertion of tendons into a borehole (same function as a pointed top at rebar bolts)
- Manchette injection sleeves – for cement or resin injection under pressure for waterproofing and ground improvement
The report discusses base materials for bolts, as briefly noted in the following:
- Steel – most used material, with grades used depending on bolt type and application area. Key criteria for particular applications include loaddeformation behaviour, corrosion performance, and cost effectiveness
- Glass fibre reinforced polymer (GFRP) – the inorganic fibres (commonly glass, aramid – but can use carbon, granite) contained in the polymer matrix are the main stress-bearing constituent, with resin transferring stresses between the fibres as well as protecting them (environment, handling). The report focuses on the GFRP type of FRP bolt, made with thermosetting resins and glass fibre, which “is related to the specific application of the guideline to tunnelling,” it says. The guide adds that polyester matrix is only allowed for use in temporary structures; for permanent bolts the matrix must use epoxy or vinyl ester
Classification and selection criteria
The chapter has five pages, opening with discussion before presenting two helpful large grid tables based on those terms.
The terms are:
- First table: load transfer mechanism; insertion; activation; tendon shape; tendon material; bonding agent; and yielding ability. They each have subcategories.
- Second table: borehole condition; number of basic installation steps; principle ground conditions; working characteristics; and, economy and environment
Each table has those respective list of terms in a grid arrangement against the same type of bolt listings, as follows: mechanically anchored; bonding by bonding agent; friction based; combined systems; deformable/ energy absorbing; GFRP bar and GFRP hollow bar, respectively. These bolt types are then discussed further, in more detail, in Chapter 6: Common Bolting Systems. Bonding agents and grouting are discussed in Chapter 9.
The guide says that the project owner should have the contract classify the excavation sequence and method, and corresponding support measures, and do so with a classification system (international, national, or projectspecific) for different ground conditions.
Installation
The section on installation of the radial bolting systems is relatively brief. Key points covered are:
- Installation steps – seven are listed but the guide observes that not all may be required for each bolt type, and that bolt activation can start with pretensioning but is usually induced by subsequent relative ground movements
- Mode of Installation – these can differentiate the bolting, such as by drilling method, timing of grouting, etc (although the latter depends on ground conditions)
- Borehole stability – stable enables use of all bolting types, whereas unstable requires self-drilling bolt types
- Number of steps – can be associated with installation time)
- Coupled systems – for when space restraints or limitation in feed length require bolts to be extended in length
- Degree of mechanisation or automation – discussed in terms of manual; semi-mechanised; fully mechanised; semi-automated; and, automated And also,
- Bolting in mechanised tunnelling – this notes there can be challenging ground conditions in TBM bored tunnelling where extra ground improvement and/ or temporary support is required, even if segmental lining is used.
Further chapters
The remaining chapters are also filled with useful structured information, arranged in a quickly absorbable way. They brief on corrosion protection (two pages, including two tables), quality management and assurance (five pages, one table and various graphics), innovation (one page), and sample clause for technical specification (one page).
The guidance rounds off with a page of references.