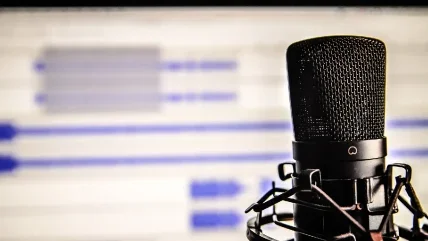
Talk tunnels, and you are usually talking big. Big projects, big money, big diameters. Major tunnelling projects such as Crossrail or, in the end one hopes, HS2 get opened by Prime Ministers and the like with press and publicity in attendance. The current Chair of the British Tunnelling Society may therefore be considered a little unusual. He doesn’t really do big. Microbore and small-bore tunnelling is Rod Young’s speciality, and has been for many years.
“My background is mining” he says.
“I began as a mining engineer. Before I got into tunnels I had a decent period working in the gold mines in South Africa.
“Mining tunnelling is not very different from tunnelling for other purposes. You’d be surprised how many mining engineers are in the tunnelling industry. It’s a lot, although it is getting fewer now that there is so little mining in the UK anymore. But there is still a lot of ex-mining engineers among the older, more senior people.”
It was in mining that Young got his beginning in going underground.
“I grew up in Poynton, Cheshire, not a place you would expect to be related to mining,” he says, “but Poynton nestles in the foothills of the southern Pennines and today it is a thriving large village. Few visitors would realise that at one time Poynton had the largest coalfield in Cheshire, having 74 pits in its heyday. Coalmining ceased in 1935 and all pits were capped but there remain many interesting clues to this former industry, including buildings and tracks and the Anson Engine Museum. So I was aware of mining from an early time.”
He studied Mining Engineering at Newcastle upon Tyne from 1979- 1982, during the summer holidays working for the NCB. “I did my basic training at Orgreave & Treeton Collieries, then worked at Manton Colliery, at the time being one of only a few Million tonne per year pits, dintng roadway and shovelling spillage back onto conveyors – hard, mucky work.”
After that work, South Africa beckoned.
“I went straight overseas and worked for Anglo American on Western Holdings Gold Mine, a mine with 4 deep shafts,” says Young. “I started doing the equivalent to the NCB basic training, was on the graduate training programme, so had periods working as stope & development miner, then shift overseer to mine overseer, obtaining my blasting certificate and mine manager certificate.
Back to the UK was when Young got involved in tunnelling.
“When I first came back I started on a 100”-wedgeblock tunnel, working for Nuttalls, who are now BAM, of course. After moving around a couple of times, all on small-diameter tunnels, I started my career at Barhale. I’ll have been with them 29 years, in June.
Most of the people who have been Chair of the BTS over the years have been involved in larger diameter projects – the likes of Crossrail, London Thames Tideway, HS2 – the prestige projects of the world just now and all the ones that have gone before.
“And the Chairs have tended to alternate between designers and people on the contracting side. I am neither: I am a practical person, and my background is very much in the smaller diameters. I’ve not done anything more than about 4 metres or 4.5 metres.
“So I’m slightly different from my BTS predecessors. But though tunnelling at two metres diameter and below may not be so glamorous it is still important. Cables, water and sewerage, communications – wherever something like that has to go under a road or railway you need it. You could call it bread and butter tunnelling.
“We do a lot for Network Rail, for example, and there is a lot more of it, widespread around the country. They tend to be quick, small projects; I’m involved in quite a few at the moment. £2 million is a typical upper budget, and that would include all the main laying of cable or piping as well as the tunnelling itself and the linking up at either end.
“In one sense microbore is not very different from large-bore tunnelling. It needs the same set of skills and standards. We still use TBMs, though smaller ones, with no onboard operators of course – though pipejacking and now directional drilling are also widely used methods. However, in some microtunnels you cannot actually enter the tunnel yourself, and that does make a big difference.”
Legally, if the diameter is anything below 1200mm you are not allowed inside it. That is the standard; and one thing it does is it imposes limits on the distance that you can drive your tunnel.
“If you are pipejacking, everything is being pushed from the pit bottom, so you’re limited to what the rams there can do; if something gets stuck, or hits an obstruction, you cannot send someone to crawl in and fix it: you have to find a way of digging down in the front of the TBM if you have any form of obstruction. And even if you are digging at 1500mm diameter, the TBMs of that size do not have access to the front face as on larger machines, so again even though you are allowed to crawl into the tunnel you will still have to dig down from the surface if you need to gain access to the cutters.”
Most microbore tunnels are quite short – road or river or rail crossings are typically only 50 metres or 100 metres long. Most of his work is within the Anglian Water company’s region, around Eastern England.
“We are doing numerous crossings for various types of water mains, and these are within that range, 50 metres to 100 metres. But still they take a lot of effort: a lot of time is spent preparing the shafts and putting the props in on either side of a rail track. You can be looking at a 15- to 20- week project by the time you put the access points in, one each side and set up the pipe jacks and associated works. But the actual microtunnelling itself might take you four or five, maybe six shifts – and that’s it.
“So small-bore needs a much greater ratio of preparation time to tunnelling time; but these tunnels are needed, and they are needed everywhere.
For example, just now Anglian Water is working on a project called the Strategic Pipeline Alliance or SPA. East Anglia is the driest part of the UK, and they want to be able to move water from the wetter part of their region, in the north, to the drier south and east. So they are putting in a line from Elsham, which is up near Grimsby in Lincolnshire, all the way down to Colchester in Essex. It is nearly 400 kilometres of pipeline that are going in, in various diameters, which makes it one of the largest infrastructure projects in Europe, and there are lots of road and rail crossings.
“Some of them are being done by microtunnelling by Barhale, the company I work for. On the lower section, where the diameters are coming down, they are being done by directional drilling – which again is another technique that the BTS should be interested in.”
Directional drilling does have its own society – the UK Society for Trenchless Tunnelling, (UKSTT). If you take them together with the BTS and the Pipe Jack Association (PJA).
“That group just about covers all the nodig methods there are, so getting the three societies together more has been one of my ambitions as BTS Chair.”
The technology of microtunnelling is not changing much, but the tunnels are definitely getting longer.
“People are doing kilometre-long pipejacks now. That’s not so much because of new machines: its more the design of the pipes. They are stronger, you can put more load on them now. We are putting interjacks in, which helps of course, and detailed design of the temporary works that you need to be able to push that far. But, at the end of the day, the machine is still digging away at the front, and there’s not too much you can do to change that.
“You can do curves of course – they have steering rams, so you can change direction – but you don’t do a lot of that because the pressures go up considerably as you go round even a gentle curve.
“The big improvement that has come – slowly, over the past two or three decades – has been in the processing of the spoil. These are slurry machines, so we pump a slurry additive up to the face and it returns with the cut material. Thirty years ago you would be trucking that waste away daily. Certainly you had a process plant for it, but the quality and the amount of material it removed was limited. The technology for that has improved incredibly. Now you can go a whole drive, recycling your waste, and at the end the water at the bottom of the tank can be nearly clear.
“I don’t think there will be any great changes in the near future; I think there will be lots of little changes. The big step-changes that are happening now on the large diameters have happened already in microtunnelling. We already have remote control. We already drive the machines remotely from the surface, not from underground. Our TBMs never have had drivers in them; and that is what will be coming to the big machines in the years ahead. And even now all the data that’s coming off the machines is going straight to an office somewhere that could be miles away from where the TBM is driving.
“I wouldn’t like you to think that I am totally wedded to microtunnelling for the rest of my career. I would definitely like to get back onto a larger project, and Barhale are tendering for some.
“We are doing works on Thames Tideway: all the big sewers need the smaller-diameter outflows to join onto them, and we are involved in that. And, on any big project there is the relocation of all the services and utilities that are in their way; we are doing a lot of the utility diversions for HS2. It is always interesting to be involved different things.
“And that is a theme I want to carry through to the BTS. I’ve been involved in the Society now for 12 odd years.”
Young says the BTS is there to develop the tunnelling industry, taking several forms. The Society encourages people to join the industry, through interaction with schools and colleges, and through the BTS Young Members. It also work on the development of new standards and guidance, keeping them updated. As new developments occur within the industry, it looks to developing new qualifications and standards and imparting these changes to the industry. There is much effort to impart knowledge to current and new members of the industry through courses, technical evenings, and conferences.
“I became involved in the courses Subcommittee on joining the BTS Committee,” he says, “and then in my second year on the Committee I became the Subcommittee Chair.”
He ran two of the BTS’s key courses – ‘Underground Health & Safety’, a two-day course at the Institution of Civil Engineers (ICE) and held each year in November (apart from the Covid pandemic shutdown period); and, the 5-day residential ‘Underground Design and Construction’ (D&C) course, at the University of Warwick, in July each year (again, halted by the pandemic).
Why those two courses?
“They were the two courses that the BTS had already been running for quite a few years past. They weren’t something I developed and started, they were up and running already. I just took over the organising of it.
For the D&C course, he says, there were about 30 or 40 people attending, “but after some years we got it up at its peak to nearly 90.
“We invite experts from the industry to come along over the five days, to talk for an hour or so on a variety of subjects: it can be pipe jacking, tunnelling, timber headings, drill and blast, temporary works, various types of design, segments, sprayed concrete lining , project management… It is a technical overview for young engineers just starting out and more senior people joining the industry. The delegates have attended from all over the world not just the UK, such as from Norway, India, Spain, etc.”
Warwick was also the host-university for the BTS-backed MSc in Tunnelling – also impacted by covid shutdowns. The D&C course had been held at several locations in the early years but moved to Warwick when the BTS worked with the university to develop and run the MSc course to be based there.
In mid-2022, Young became Chair of the BTS.
“I am enjoying my time very much, being already a year through my two-year tenure.”
Key events have included presenting the David Wallis Lecture at the BTS conference, in October 2022, speaking at the BTS dinners, opening the courses but this time as Chair.
“My predecessor, Kate Cooksey, was the one who was mainly involved in setting up the Warwick MSC course; and, she was also the one who saw the BTS through the Covid pandemic. Of course that involved setting up Zoom and YouTube meetings because people could no longer meet face to face at the ICE on the third Thursdays of the month as we used to.
“The virtual meetings were very successful; people got used to having lectures and conferences that way, and we had some very large attendances, which have been maintained. But Covid has left its legacies: people have become accustomed to meeting that way. And that has impacted the social side of the Society, which has always been very important: the ‘Meeting people and talking shop over the Famous Sausage and Chips’ side of things, where you meet people and talk shop and swap experiences and help solve each other’s problems face to face.
It helped that, in the past, most of the big projects were London-oriented; people lived or worked near London and it was easy to get to the lectures at the ICE.
“But now that’s not so easy; the projects have moved, and so many of those people have moved out of London also. Even so, we are still attracting good audiences – we have had nearly 200 people at recent meetings.
“It is not a problem that is unique to the BTS: many other professional bodies have seen membership, and attendances, fall off since Covid.
“Our membership figures have actually held up very well, and the YouTube lectures are available online so can be downloaded at any time, and again the numbers who click on them and watch them at some time that is convenient to them, say after supper at home with their feet up, are quite large.
“But I do want to get the in-person social side working for as many people as possible.
“One way is to have meetings all around the UK. We have had a few in the past. Now it is something that I would very much like to focus on. The idea is to go out and have meetings out of London and to do it in conjunction with other organisations.”
He mentioned the PJA and UKSTT. Recently, the BTS held its annual Joint Meeting with MinSouth, which is the south of England group of the mining community. It is looking at working with the Concrete Society – “there is lots of shared interest there.”
Also, he adds, “We are looking at working with the Mining Institute up at Newcastle to have a meeting there. We have already had a couple of meetings with the York Railway Museum. There’s a twofold reason for that: railways and tunnels obviously go together, and we are working with them on their revamp. The Museum is also a perfect venue for lectures as well. The plan is to go there for some meetings in the near future.
“So that is my hope for the BTS. Its great strength is that anyone can join it, whatever your level or involvement in tunnelling. That in turn means that mining people, concreting people, railway people, pipe-jack people, drilling people – all of those can be involved.
And we still do have the sausage and chips at our Thursday meetings. Please come and sample them.”