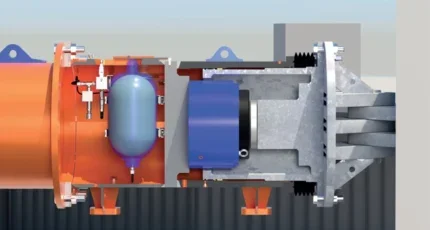
Deep shafts or basements on underground projects do not regularly feature major use of propping, such as was employed on earlier construction works for the new power substation being built at Euston station, in London, as part of the HS2 project.
The substation is needed to switch down high voltage power supplies to the lower voltages, and direct current, required for operations of trains and stations.
In this case, at Euston, a 20m-deep shaft was constructed for the early works. The shaft box was supported by props at three different levels.
Principal contractor is Mace Dragados. The three-level propping for the deep shaft was provided by Altrad RMD Kwikform and installed at the top then at 7m vertical intervals, to 14m below ground level.
The approach taken, though, considered more factors than typically called for in design codes, says Altrad RMD Kwikform. Principally, it was to consider how ambient conditions of temperature variation – with time (day, season, construction duration) and depth (location of props underground). Official UK MET Office data were studied, and a digital twin was employed to predict sunlight to the actual site conditions and urban setting.
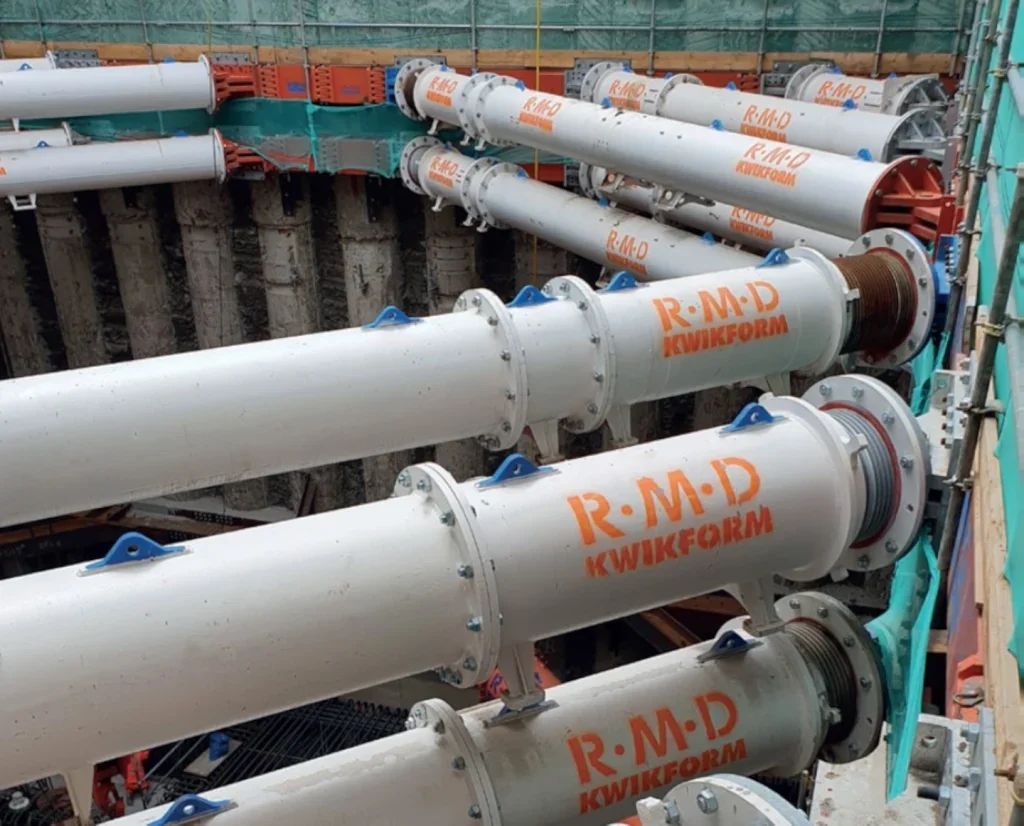
The result of the design analysis then indicated the loading on the props could be about 30% less than called for by codes, the company says. That meant detailing the propping could reduce both quantity and size, which would open up more movement space within the shaft during construction period.
On site, high capacity load cells (‘HD E-Pins’ – developed for the project) were also installed to monitor loading real-time, at all three prop levels. Traditional strain gauges were then not required, it adds.
Building upon from that experience, Altrad RMD Kwikform produced a White Paper, last October, which also followed discussion with contractors and consultants in industry. The paper goes into more detailed aspects of thermal range and loading for ground engineering works and tunnels.
In a statement, then, commercial manager Ajay Nagah, said: “Thermal loading can have a significant impact on ground shoring equipment, and consulting engineers are now interpreting industry standards differently.”
Shortly before the Paper, the company had launched a hybrid hydraulic shoring system, as a Tubeshor patented accessory (Tubeshor Active Thermal Compensator(ATC)). It is part of the prop system for waler or capping beams, and is fitted into standard props. The ATC’s internal equipment has a pressurisation system, comprising a hydraulic cylinder coupled to a bladder accumulator. The pressure is preset before the ATC, fitted in the prop, heads for site. The preset pressure is determined to suit the specific location and depth the prop is to be used on a project.
The shoring solution at HS2 Euston’s substation box also had mechanical screw collars, which isolate hydraulic jacks from load – important in risk management of chance hydraulic failure. The company said the set-up also gives a more robust and stiffer propping arrangement with greater control of deflections.