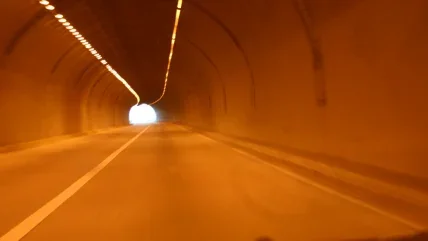
The use of fibre-reinforced concrete (FRC) either as shotcrete or as cast-in-place concrete in temporary or final tunnel linings is constantly increasing. In parallel, the number of fibre types available on the market is growing. Historically, fibres are specified by volume-percentage or weight-per-volume in the mix.
However, it is also widely acknowledged that a performance-based approach is much more constructive and objective, especially for tunnel linings.
The major structural benefit of FRC in tunnel linings is in the improvement of the post-cracking behaviour, specifically elasto-plastic or strain hardening bearing behaviour. Next to the material properties, the post-cracking behaviour is influenced by the combination of moment and thrust force in the lining. A sufficient thrust level can create strain-hardening behaviour, even for FRC that shows strain-softening behaviour under pure bending. A concept which allows a labelling and performance-based classification system for FRC tunnel linings has been developed.19
The typical governing load case of tunnel linings is a combination of bending moment (M) and thrust or normal-force (N). Due to the convexly- curved shapes and bedding by the ground, tunnel linings do not fail by buckling. Therefore, just as for rebar-reinforced concrete (RC) tunnel linings, the design procedure for FRC usually follows the classical approach for short columns, mostly recognised by the use of a moment-normal force-interaction diagram2,3.
The constitutive material law of FRC widely used for the structural design is a stress-strain-relationship (SSR). Compared to RC, the SSR for FRC is expanded on the tension side (see figure 1). Internationally, there are multiple, similar beam tests and test evaluation concepts that are used to develop design values for the SSR.4,5,6,7,8,10,11
In opposition to concrete in unreinforced or rebar reinforced concrete, FRC carries the load in tension in all three phases of material behaviour, un-cracked (elastic), micro-cracked, and macro-cracked. The design assumptions for the calculation of the sectional strength for FRC based on an SSR are presented and further discussed in detail.1,6,7,12,13,14,15,16,18
It is crucial to realise that with this approach, FRC is assumed to be a macroscopically homogeneous and isotropic material.12,13,15 The material properties of a single or discrete fibre in the model become irrelevant. Therefore, the fibres and the concrete are modelled using a single SSR relationship and not two (i.e. as for steel rebar and concrete in RC). Even if the FRC is cracked under tension, the material’s deformation is modelled as strain rather than a discrete crack and is still viewed as homogeneous and isotropic. This, however, is not the case in the area around the crack. This circumstance is very important to appreciate and understand. Fibres influence the bearing behaviour in multiple ways.
Three major benefits of fibres most relevant to tunnels are:
(i) They slightly increase flexural tensile strength under uncracked (elastic) conditions.
(ii) They increase residual flexural tensile strength under cracked conditions in the case of ultimate bearing capacity of tunnel linings.
(iii) They increase the toughness of the concrete12.
Constitutive law of FRC
A generic SSR and nomenclature of the variables are shown in Figure 1, which is similar to SSRs provided for example by RILEM in7 and ACI in5. Strengths are using the Roman lower-case letter “f”, while strains are displayed with the Greek lower-case letter ‘ε’ with specific subscripts at particular locations. The tension side (t) is represented by three sections, which model and control the bearing behaviour in the three different phases, elastic (t1), micro-cracking (t2), and macro-cracking (t3). A more detailed discussion about the three different phases is provided in references.12,15
Loadbearing Capacity Calculation
The loadbearing capacity of a cross-section based on the SSR is calculated by finding the equilibrium between internal stresses and external forces. Figure 2 provides a general idea of how the SSR is used to evaluate the resulting moment and thrust on a tunnel lining.6,7,12,13,14,15,16,17,18 The bearing capacity is driven by the resulting force (‘integrated area’ under the SSR) and the distance from the neutral axis (lever). It also shows that an overly sophisticated approach to model phase II between ft1 and ft2 does often not provide significant benefits or accuracy for the design in actual projects.
Fib Model Code 2010 Classification System
The Fib Model Code 20101 classification system is based on the three-point beam test standardised in EN 146519, which is also referred to as the ‘notched beam test’ (see figure 3). The test uses a square 150 x 150mm beam with a 500mm span. In the centre, the beam is notched 25mm deep, which leaves an effective beam height of 125mm.
During the test, the load (F) and the Crack Mouth Opening Displacement (CMOD) at the notch, which is the crack width, are measured (see figure 4). In contrast to un-notched beam tests, the crack location is predetermined due to the notch. At four specific CMOD’s the load Fj is documented. F1 at CMOD1 = 0.5mm and F3 at CMOD3 = 2.5mm are used to determine the related ‘characteristic residual flexural tensile strength’ of FRC significant for serviceability (fR1k) and ultimate conditions (fR3k).
The characteristic residual flexural tensile strength is developed using the classic elastic flexure formula.1 As discussed in detail in12,13,15,16,17,18, the result is only valid for elastic conditions (isotropic and homogeneous material behaviour). However, the beam is already cracked at this state. In MC2010 the ‘residual flexural tensile strength’ fR1 and fR3 are, therefore, not the same as the ‘serviceability residual strength’ (post-cracking strength for serviceability crack opening) (fFts ) and the ‘ultimate residual strength’ (post-cracking strength for ultimate crack opening) (fFtu), respectively, used in the SSR.
Labelling / Performance Classification for FRC tunnel Linings (Pc-Frc)
The performance classification introduced in MC2010 is based on the characteristic residual strength values for serviceability and the ratio between the characteristic residual strength values for serviceability and the ultimate state. In the opinion of the author, this approach provides a good basis to classify the performance of FRC for tunnel linings. However, a major disadvantage of the classification provided by MC2010 is that the classification is independent of the compressive strength.
The absolute bearing capacity of FRC tunnel linings is highly dependent on the compressive strength and this fact is not reflected in the classification. FRC with identical MC2010 residual strength classification can, therefore, perform in a very different way.
Alternatively, the use of dimensionless – normalised – values of the residual strength as a percentage of the compressive strength avoids the issue. The following generic and simple SSR was used by the author16,17,18,19 and is suggested for the introduced Performance Classification for FRC Tunnel Linings (PC-FRC):
The flexural strength (ft1) and residual strength (ft2 and ft3) on the tension side is specified as a percentage of the compressive strength. For simplicity, the elastic behaviour is modelled with a flexural tensile strength of ft1 = 10% of fc at εt1 = 0.1‰. The strain for residual strength ft2 and ft3 is located at εt2 = 0.2‰ and εt3 = 25‰ respectively. The suggested residual strength values ft2 and ft3 are either 0, 1.25, 2.5, 5.0, or 7.5% of the compressive strength, while ft2 is always equal or larger than ft3. On the compression side, the compressive strength (fc) is, per definition, 100%. The intersection between the parabolic and constant section (εc1) is located at -2‰ and the ultimate compressive strain (εc2) is -3.5‰.
Previously the author developed the dimensionless momentstrain- curves displayed in figure 5 and 6 for pure bending conditions, but also under the influence of thrust, using the generic SSR of figure 118. Similar to classic moment-normal force-interaction diagrams, dimensionless values were used for the moment (m) and normal-force (n) (thrust). The figures show examples of dimensionless moment-strain curves that were calculated using the introduced SSR. By the equations provided (see 19) these values can be transferred into actual bearing capacities for a tunnel lining or to evaluate beam tests independent from its geometry. In ref19 specific examples for this approach are shown. The callouts refer to the residual strength ft2 and ft3 used for each curve as a percentage of the compressive strength fc. In particular, figure 6 illustrates an example that typical beam-test load curves can be properly simulated by modelling the post-crack behaviour using the residuals strengths ft2 and ft3 with a constant or trapezoidal curve.
A detailed discussion of the approach, including the influence on the bearing capacity in combination with the thrust is provided in18. Based on this work, a simplified graph was developed for pure bending that provides a generic relationship between the residual strength ft2 and ft3 relative to the compressive strength fc in percent and the bearable, dimensionless moment.
FRC labelling system and performance classification
Before the presentation of the classification system, a labelling system for FRC is introduced that can be used for the specification of FRC. The introduced label adds two values to the classic compressive strength classification label. For example, a FRC with a compressive strength of fc = 35 MN/m2, a residual strength of ft2 = 1.75 MN/m2 (= 5% of fc) and ft3 = 0.875MN/m2 (= 2.5% of fc) would be labelled as a FRC 35 | 5 | 2.5 based on the percentage relative to the compressive strength. Similarly, the labelling can be used for imperial units based on the compressive strength. For example, a compressive strength of fc = 5,000psi, a residual strength of ft2 = 250psi (= 5% of fc) and ft3 = 125psi (= 2.5% of fc) would be labelled as a FRC 5000 | 5 | 2.5. Additionally, it is noted that the residual strength ft3 for typical FRCs used in tunnelling is typically equal or less than ft2 (ft3 ≤ ft2) so that the residual strength ratio is typically less or equal than 1 (ft3 / ft2 ≤ 1).
The introduced performance classification for FRC-tunnel linings (PC-FRC) consists of main class and the sub-class. The main class is labelled with Roman numerals I, II, III, and IV and based on the residual strength ft2 expressed as a percentage of the compressive strength fc (see figure 9).
The sub-class, labelled with letters a, b and c, is based on the ratio of the residual strength ft3 relative to the residual strength ft2 in percent (see figure 10). Based on this classification, for example, a FRC 35 | 4.5 | 1.9 fibre reinforced concrete with compressive strength of 35MN/m2 (appr. 5,000psi) would be classified as II-b (Class II: 2.5 < 4.5 < 5.0; subclass b: 25% < 42% (= 1.9/4.5*100) < 50%).
Conclusion
MC2010 provides a widely-used concept for testing and developing a constitutive law for FRC. Also, the model code provides a classification system based on the residual strength of FRC. The paper18 analysed the approach provided in MC2010 in detail and simplifies the approach for FRCs typically used in tunnelling to make it more efficient, where increased effort due to the MC2010 concept does not provide major benefits for the design of tunnel linings.19
The biggest weakness of the MC2010 classification for tunnel-lining design appears to be that it is not linked to the compressive strength of the material, which is a major factor influencing the bearing capacity of FRC tunnel linings.
Using the general approach of MC2010, a modified labelling and classification system for FRC is introduced, which bases the residual strength classification primarily on the ratio based on the compressive strength.19 Typical application examples of the labelling and classification system are given to present the application to practitioners.
The presented labelling/classification system provides an effective, easy way to specify FRC for tunnelling applications.
References
1 FIB Model Code 2010, Volume I, Final Draft, fib bulletin 65, March 2012.
2 American Concrete Institute Committee 318: Building Code Requirements for Structural Concrete (ACI 318-14). 2015.
3 American Concrete Institute: The Reinforced Concrete Design Handbook. Volume 1: Member Design SP-17(14). Building Code Requirements for Structural Concrete (ACI 318-14). 2015.
4 American Concrete Institute: Report on Indirect Methods to Obtain Stress-Strain Response of Fibre-Reinforced Concrete (FRC) (ACI 544.8R-16). 2016.
5 American Concrete Institute: Guide to Design with Fibre Reinforced Concrete (ACI 544.4R-18). 2018.
6 American Concrete Institute: Report on Design and Construction of Fibre Reinforced Precast Concrete Tunnel Segments (ACI 544.7R- 16). 2016.
7 RILEM TC 162-TDF: Test and Design Methods of Steel Fibre Reinforced Concrete. ??-??-design method – final recommendation. Materials and Structures, Vol. 36, October 2003, pp. 560-567.
8 RILEM TC 162-TDF: Test and Design Methods of Steel Fibre Reinforced Concrete. Bending Test, Recommendations. Materials and Structures, Vol. 33, January-February 2000, pp. 3-5.
9 EN 14651: Test method for metallic fibre concrete – Measuring the flexural tensile strength, 2007.
10 German Society for Concrete and Construction Technology (DBV): Guide to Good Practice – Steel Fibre Concrete. 2001.
11 Deutscher Ausschuss fuer Stahlbeton (German Committee for Reinforced Concrete) (DAfStb): DAfStb Richtlinie fuer Stahfaserbeton (DAfStb Guideline for Steel Fibre Reinforced Concrete). 2010.
12 Nitschke, A.: Tragverhalten von Stahlfaserbeton für den Tunnelbau. Dissertation. (in German. Load Bearing Behaviour of Steel Fibre Reinforced Concrete for Tunneling. Doctoral Thesis.) Technischwissenschaftliche Mitteilungen des Instituts für konstruktiven Ingenieurbau der Ruhr-Universität Bochum, TWM 98-5, 1998.
13 Ruhr-Universität Bochum, Lehrstuhl Prof. Maidl, Nitschke, A., Ortu, M.: Bemessung von Stahlfaserbeton im Tunnelbau. Abschlußbericht. (in German: Design of Steel Fibre Reinforced Concrete for Tunnelling. Final Report) Research Project funded by the Deutscher Beton-Verein E.V. (DBV-Nr. 211) and the Arbeitsgemeinschaft industrieller Forschungsvereinigungen (AiF-Nr. 11427 N). Fraunhofer IRB Verlag, 1999. ISBN 3-8167-5455-4.
14 Nitschke, A., Winterberg, R.: Performance of Macro Synthetic Fibre Reinforced Tunnel Linings, World Tunnel Congress (WTC) 2016 Proceedings, 22nd – 28th April 2016 in San Francisco, CA. 2016.
15 Nitschke, A.; Bernard, E.: Load-Bearing Capacity of Fibre-Reinforced Concrete Tunnel Linings. 23rd Rapid Excavation & Tunnelling Conference (RETC 2017) & Exhibit Proceedings, 4-7th June 2017, San Diego, CA, 2017.
16 Nitschke, A.: Modelling of Load Bearing Behaviour of Fibre Reinforced Concrete Tunnel Linings. Shotcrete Magazine, Volume 19, Number 2. 2017.
17 Nitschke, A.: Elasto-Plastic Design of Fibre Reinforced Concrete Tunnel Linings. North American Tunnelling Conference (NAT 2018), June 24-27, 2018 in Washington DC. 2018.
18 Nitschke, A.: Design Diagrams for Fibre Reinforced Concrete Tunnel Linings. Rapid Excavation & Tunnelling Conference (RETC 2019) & Exhibit Proceedings, 16-19th June 2019, Chicago, IL.
19 Nitschke, A.: Performance-Based Classification of Fibre Reinforced Concrete for Tunnel Linings Based on Model Code 2010 (NAT 2020), 7-10th June 2020, Nashville, TN.