
Works of a range of tunnel projects use formwork for cast insitu concrete linings to excavated profiles as well as to help form free-standing large tunnel elements themselves, such as for immersed tube tunnels.

Among projects across Europe recently there have been road and rail tunnel linings that have employed formwork from Peri, or its subsidiary business Kern TunnelTechnik, such as:
- For the A26 road tunnels, in Austria
- Gubrist road tunnel renovation, in Switzerland
- The Divaca-Koper rail tunnel linings, in Slovenia
- linings for parts of HS2, outside London
Other UK projects have included the London Thames Tideway large diameter sewer tunnel, and the Hinkley Point C outfall tunnels.
Formwork is also being employed on the immense casting works for the 17.6km-long immersed tube tunnel being built between Denmark and Germany.
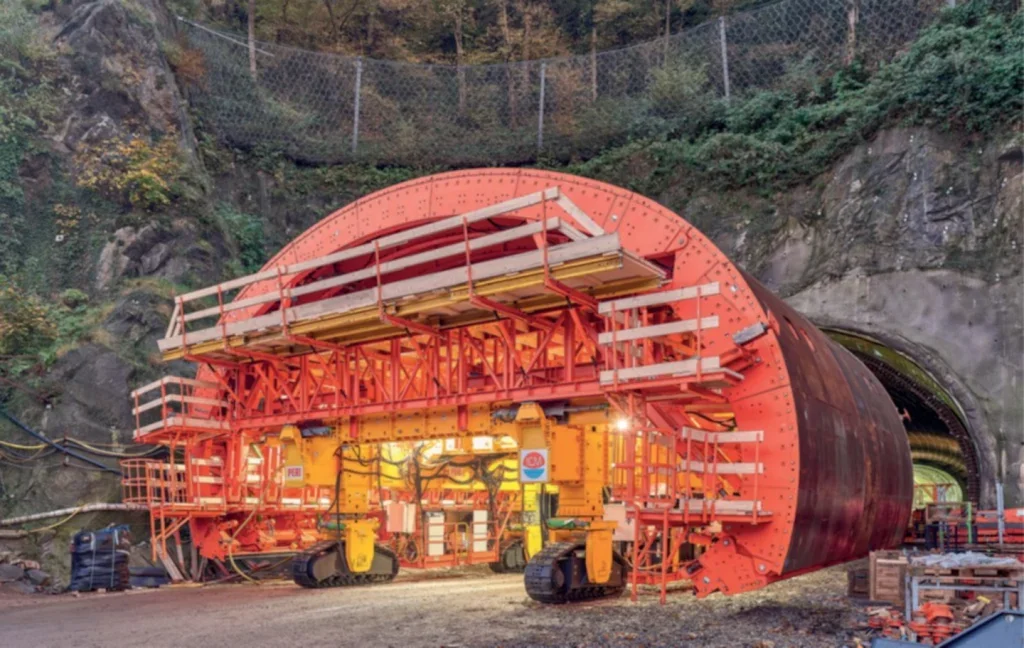
A26 ROAD TUNNELS, AUSTRIA
Approach tunnels to the new A26 suspension bridge over the Danube have been under construction. The excavations are designed with concrete lining and varied types of formwork have been employed for the tasks.
The tunnelling works have involved establishing and lining five different cross-sections, requiring profile transitions, tight radii of between 50m and 750m in the bends, and varying gradients.
For the casting works, Peri developed a customised, fully hydraulic steel formwork carriage, weighing 250 tonnes, with a caterpillar drive – for movement, due to the tight curve radii. It was 8.07m high x 14.50m long, and its width changed from 11.20m (for casting) to10.70m (moving). The formwork system was used for concreting of different cross-sections for 170 parts of the tunnels.
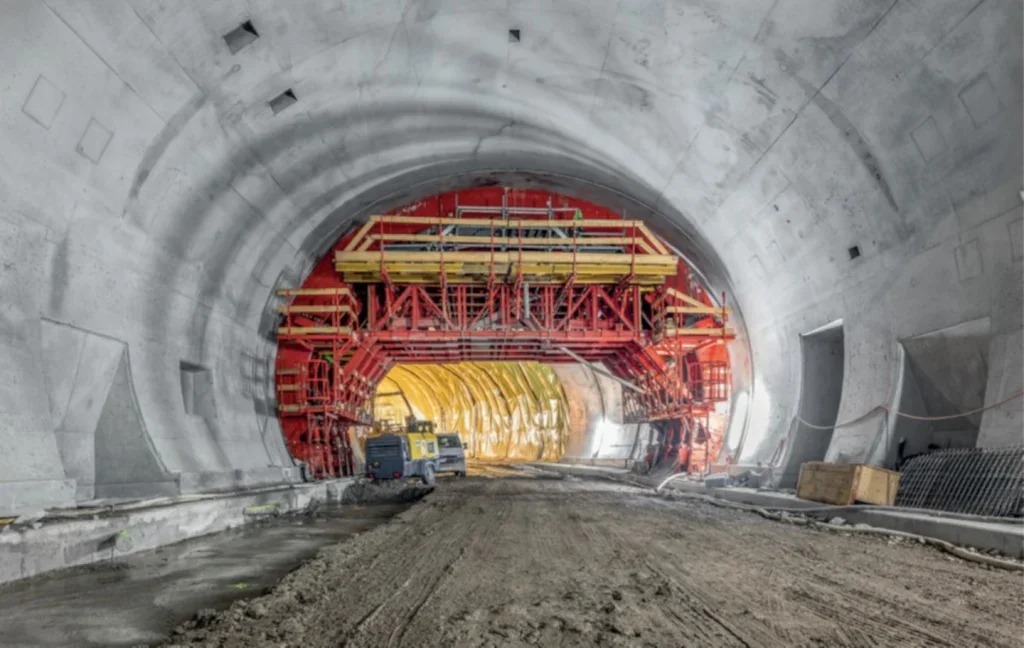
Prior to the casting work, a 6m-long mobile assembly carriage on rubber tyres was used for sealing works, and then a reinforcement carriage passed in working 12m block lengths.
CASTING ELEMENTS FOR FEHMARN LINK
The world’s largest concrete casting factory is in operation, in Denmark, to make the enormous segments for the world’s longest immersed tube tunnel – the Fehmarn fixed link.
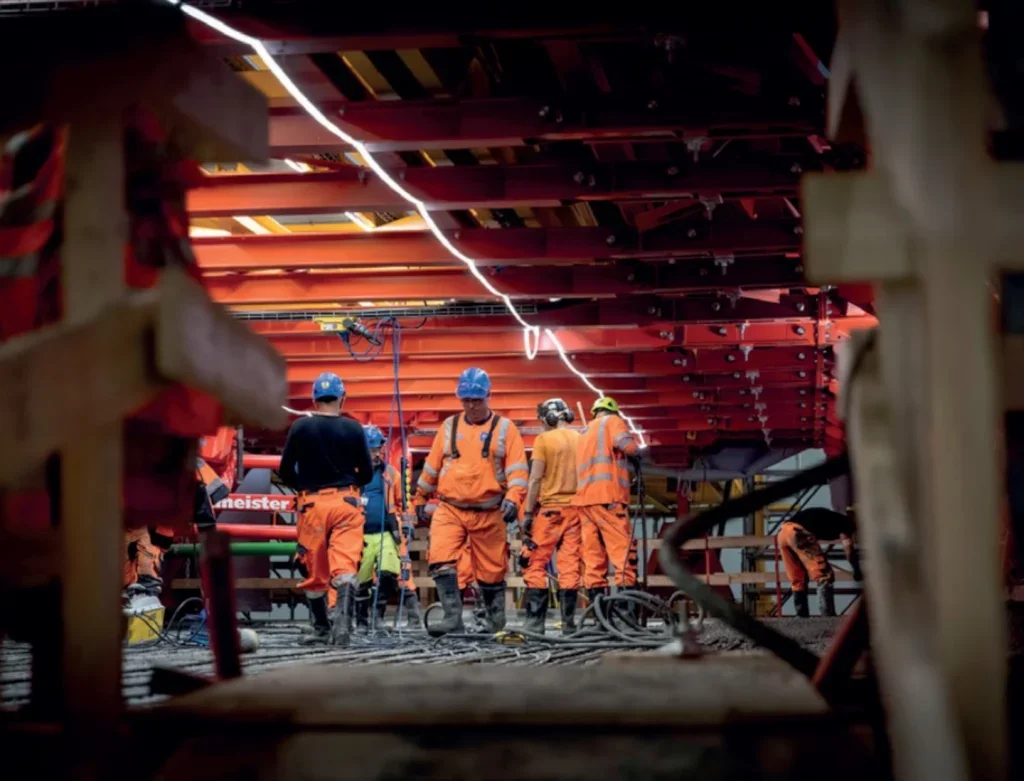
The 17.6km-long combined rail and road link is being constructed between Denmark and Germany, and is part of the EU-backed strategic high-speed rail network for Europe.
The Fehmarn tunnel is designed with two separate cells for transport mode (rail, road), for separated travel.
The tunnel cross section with its hollowed sections are formed by casting the floor, then the separating walls, and then the ceiling. This initial casting is to create a ‘segment’ of the overall tunnel but with the tunnel being so long these (while being 24m-long) are like slivers to be joined together to form a tunnel ‘element’.
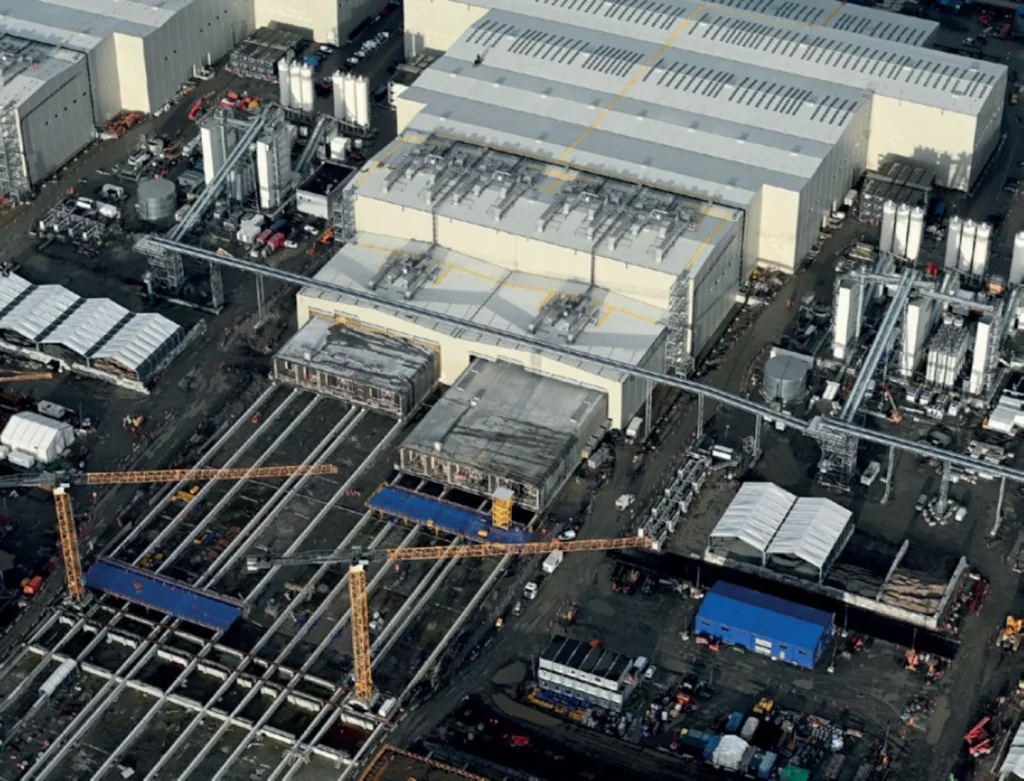
These elements have bulkhead doors attached into their ends – and out the casting factory they go. Eventually.
For these casting tasks are so enormous they take a while. It is almost like they are being gradually extruded from the factory, out of the huge doorway onto the slip ramp, leading toward the dry dock.
With 79 of the standard elements (each 217m-long, and weighing 73,000 tonnes) plus some special-sized elements required for the immersed tube tunnel, one production line is not enough. The factory complex has a few lines, and for each much formwork is employed for the casting works. Peri has supplied significant quantities of steel formwork for the task.
The factory started casting in early 2024 and the Fehmarn project is to be completed by the end of this decade.
ACQUIRING MAJORITY IN KERN TUNNELTECHNIK
In late 2023, Peri Group acquired a majority stake in Kern TunnelTechnik.
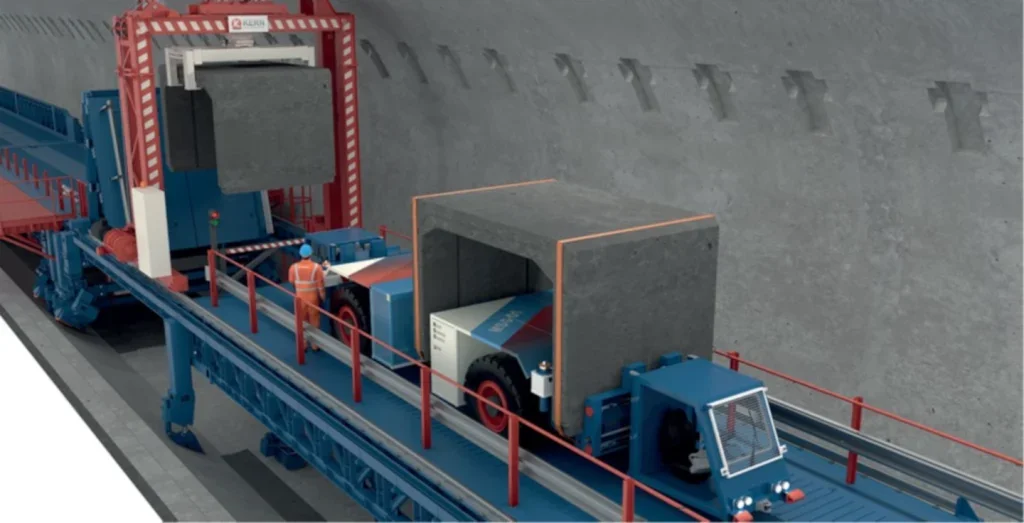
Kern TunnelTechnik has supplied lining formwork and logistics systems for a variety of projects in Europe and North America – such as the London Thames Tideway sewer tunnel, in UK, the Gubrist road tunnel renovation, in Switzerland, and the Hampton Road Bridge Tunnel, in the US.
Following the purchase, Kern has continued to operate as an independent business unit within the group. The majority stake in Kern was a key step to enable Peri to be “broadening our engineering expertise in infrastructure construction,” then noted CEO Christian Schworer.
Peri bought the shares in Kern Group from Walo Group, which had been a strategic investor since 2017 and the companies would continue co-operation. Kern, a Swiss-based company, was founded in 2010.
On the Gubrist tunnel, last October Kern announced a milestone point with completion of renovation of the second of the 40-year old tubes. The contractor is a JV of Implenia, Walo Bertschinger, and Anliker.
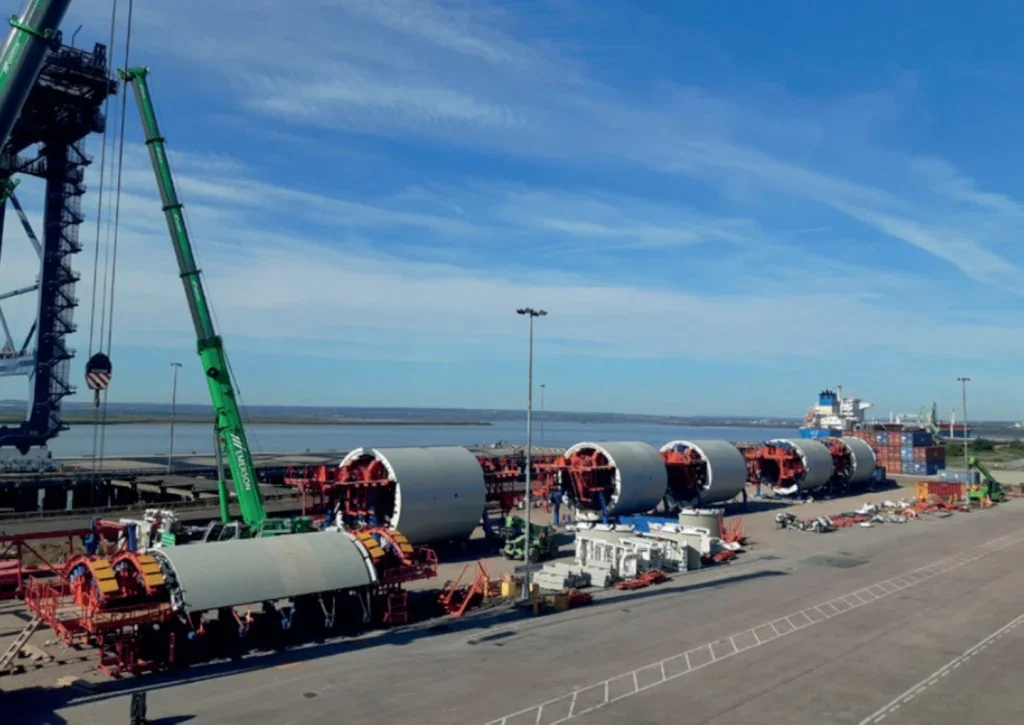
Kern has formwork that passed its Factory Acceptance Test (FAT) last autumn for use on cross passages of HS2’s Northolt Tunnel East package. The contractor JV comprises Skanska, Costain and Strabag (SCS JV).
In Slovenia, the company is contributing formwork and a reinforcement gantry to sections (tunnels T2, T4) of the rail modernisation project between Divaca and Koper.
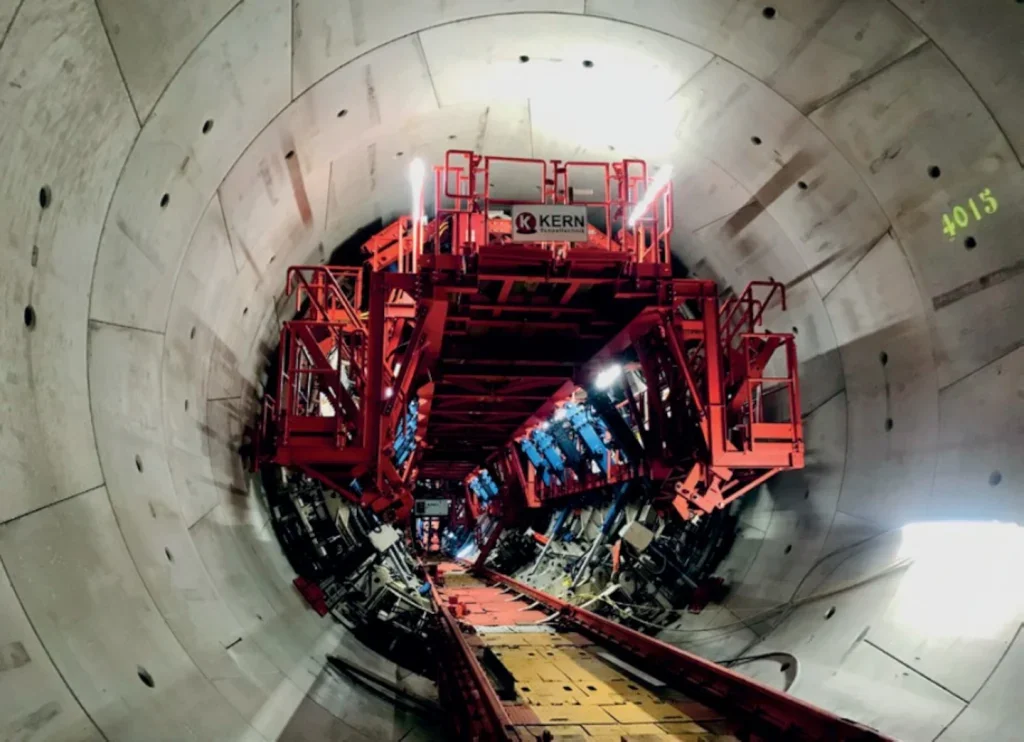
Kern has also had formwork systems involved in many other projects in Europe – such as Hinkley Point C outfall tunnels, in UK; Bad Bergzabern road tunnel, in Germany; Pekel road tunnel, in Slovenia – and a number beyond, including Polihali diversion tunnels for Lesotho Highlands Water Project, Ph2.