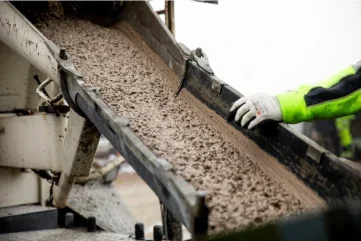
The Fehmarnbelt project is participating in a trial casting of concrete with a reduced carbon footprint.
The contractor consortium, Femern Link Contractors (FLC), is conducting the trial casting using a new type of concrete at a specially allocated area at the tunnel construction site in Rødbyhavn.
The trial is part of a larger collaboration on the concrete, known as Calliste, in which the Fehmarnbelt developer Femern A/S, is involved, together with Aalborg Portland, the Technological Institute, several universities, concrete suppliers and public and private developers.
“We have strict requirements as regards strength and durability for the construction of mega projects, such as the Fehmarnbelt tunnel, and this is of particular relevance when building in the marine environment. We’re also firmly focused on reducing the CO2 footprint from our construction project through new technologies and we want to give additional impetus to the development of concrete of the future,”saidKim Smedegaard Andersen, deputy technical director at the Fehmarnbelt project.
Aalborg Portland, a sub-supplier of cement to the Fehmarnbelt tunnel, has developed a cement known as Futurecem, which can reduce the CO2 footprint from concrete production by 25% compared to traditional concrete. This is achieved by replacing some of the clinker content in the cement with specially treated clay and limestone. The Calliste collaboration is conducting applied research and aims to develop this technology further. The aim of the collaboration is to halve the need for cement in concrete while maintaining high strength and durability.
Pernille Nyegaard, centre project manager at the Technological Institute, said the trial casting was the first time a concrete had been used where approximately 50% of cement clinker had been replaced by a special combination of clay and limestone.
“This significantly reduces the CO2 footprint compared to the types of cement normally used in Denmark,” he said.
“This is the first time for us to cast with the new type of concrete on this scale, which means that we can investigate the concrete’s durability. The trial is important to demonstrate how the concrete performs in a real traffic environment with frost and salting.”
If the Calliste project achieves the expected results, it will open the possibility for it to be used in future construction projects, where concrete production carries a heavy CO2 burden.
Reducing concrete’s environmental impact is becoming a key focus for infrastructure and underground construction projects.
Last year, the Cross Yarra Partnership working Sydney’s Metro Tunnel trialled a crushed glass concrete mix in the construction of temporary suspended concrete slabs, producing a concrete mix of equal strength and quality to traditional concrete. The trial demonstrated that 25% of virgin sand used in concrete mix coud be replaced with recycled crushed glass, reducing reliance on virgin sand and diverting waste glass from landfill.
In July 2022, John F Hunt, working for HS2’s station construction partner, Mace Dragados Joint Venture, completed the UK’s largest pour of Earth Friendly Concrete (EFC). EFC is made from a combination of ground granulated blast furnace slag, pulverised fly ash and a high-alkaline chemical, rather than Portland cement. Its geopolymer binder system reduces embodied carbon by around 70%, saving 250kg of CO2 per cubic metre poured.