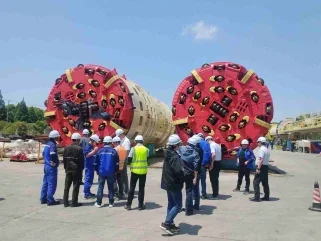
The 38km-long Polihali to Katse transfer tunnel is one of the main works components of Phase II.
The factory acceptance test, which took place at a CCCC Tianhe plant in Changshu City, Jiangsu Province, China was conducted by LHDA senior engineers, tunnel designer Metsi a Senqu Khubelu Consultants, Kopano Ke Matla joint venture, which is constructing the tunnel, and TBM designer Robbins.
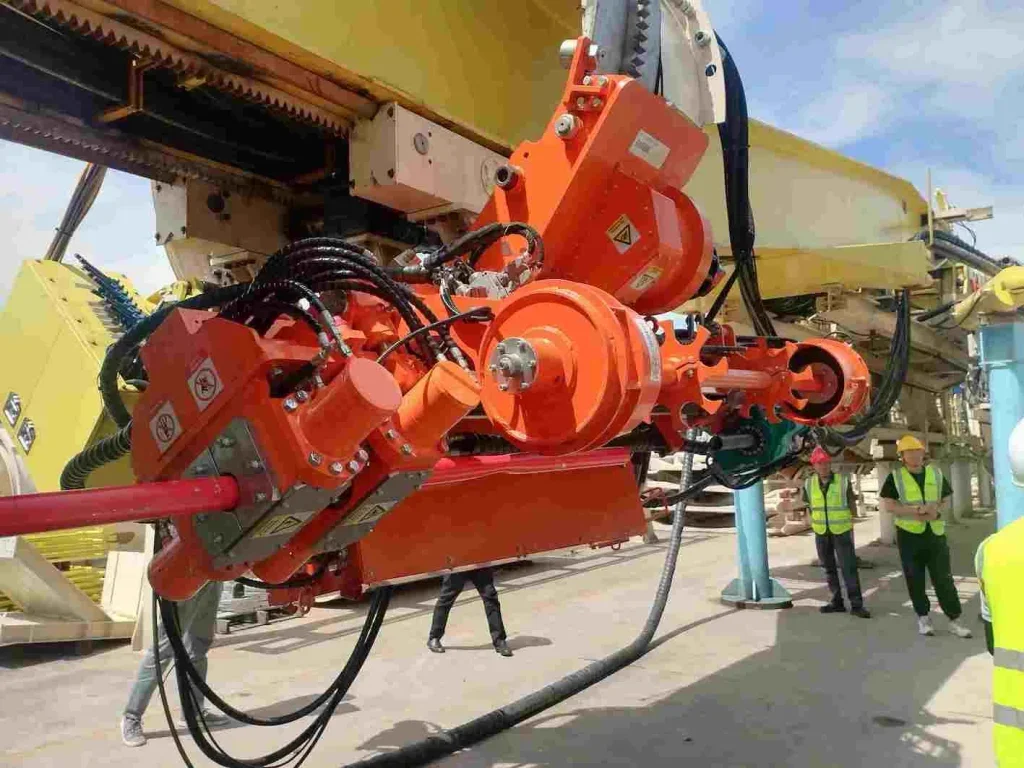
“We verified the design of the TBMs, their functionality and adherence to safety standards,” said Phase II senior projects engineer Neo Thinyane. “This included examining the cutterheads, back-up systems and segment erection mechanisms.”
The team also assessed the muck removal system, conveyor belts, power supply, ventilation, water supply and dewatering systems.
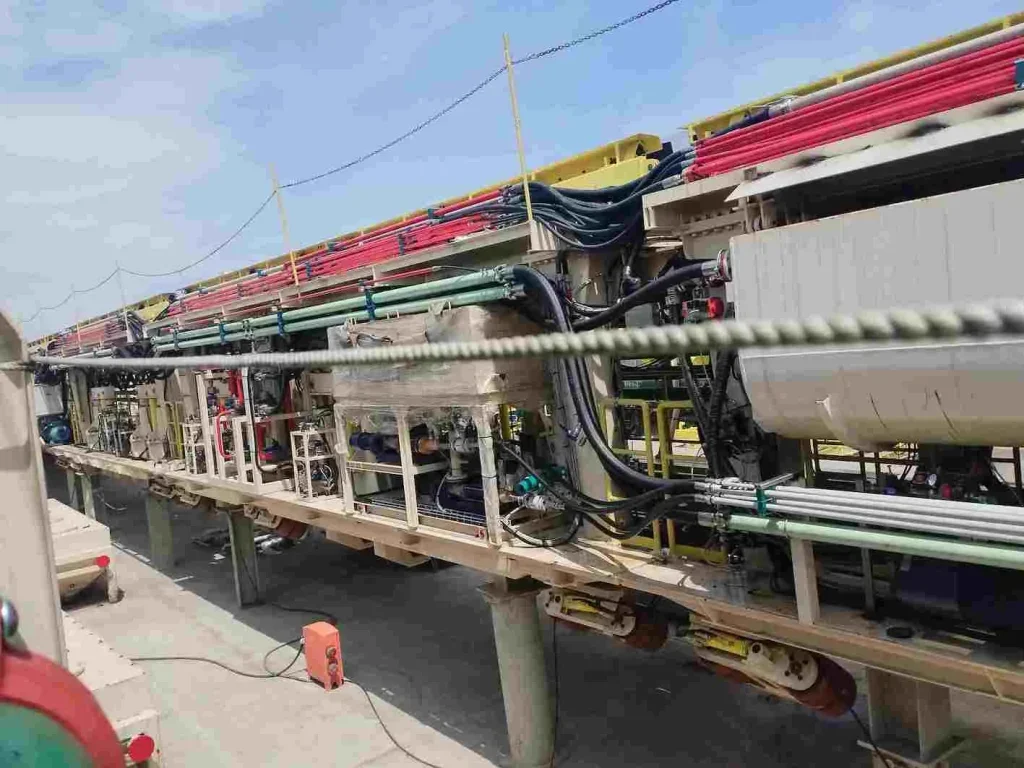
The inspection also focused on safety features, including walkways, head clearance, gas detection systems, and fire detection and suppression. The TBMs are equipped with refuge bays containing life-support systems, including first-aid kits, oxygen tanks, respirators and air filtration systems. There are also back-up power and cooling systems to ensure uninterrupted operation in the case of power outages.
The 5.39m diameter TBMs, which have been designed to handle the challenging basalt rock formations in the Mokhotlong and Leribe districts, are expected to arrive in Lesotho later this year.
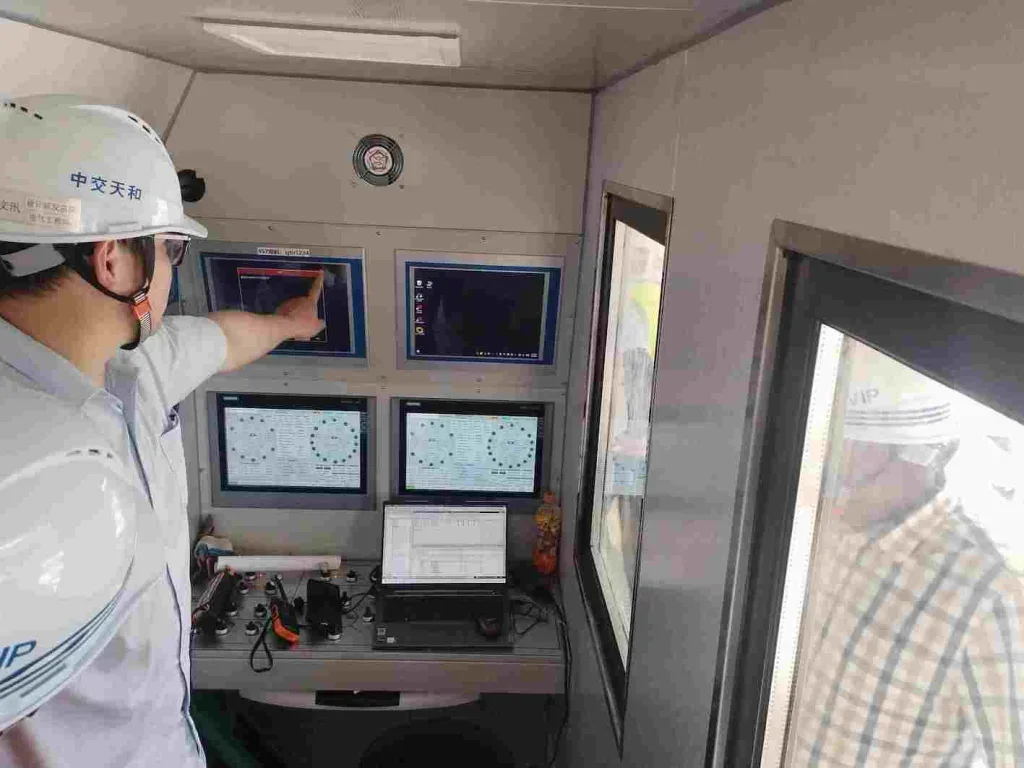
The Polihali Transfer Tunnel will transfer water by gravity from the Polihali reservoir to the Katse reservoir. Both boring and drill and blast will be used. The tunnel works include intake and outlet works, a gate shaft at the existing Katse reservoir with an underwater connection to the lake, and access adits to the waterway and construction infrastructure.